Paper:
Rail Structure Supporting Mechanism Using Foamable Resin for Pillar Expansion, Anchoring, and Fixation
Rui Fukui*, Kenta Kawae**, Yuta Kato*, and Masayuki Nakao*
*Department of Mechanical Engineering, School of Engineering, The University of Tokyo
7-3-1 Hongo, Bunkyo-ku, Tokyo 113-8656, Japan
**Department of Human and Engineered Environmental Studies, School of Frontier Sciences, The University of Tokyo
5-1-5 Kashiwanoha, Kashiwa-shi, Chiba 277-8563, Japan
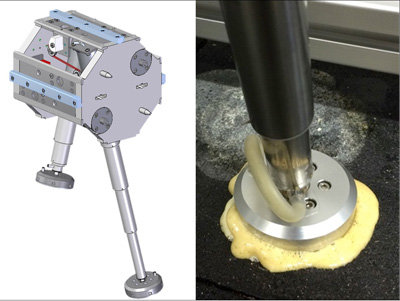
Rail structure supporting mechanism
- [1] M. Rosen, “Robots to the rescue: DARPA's robotics challenge inspires new disaster-relief technology,” Science News, Vol.186, No.12, pp. 16-20, 2014.
- [2] K. Chayama, A. Fujioka, K. Kawashima, H. Yamamoto, Y. Nitta, C. Ueki, A. Yamashita, and H. Asama, “Technology of Unmanned Construction System in Japan,” J. of Robotics and Mechatronics, Vol.26, No.4, pp. 403-417, 2014.
- [3] T. Furuta, T. Yoshida, T. Nishimura, and H. Yamato, “Development of the Exploring Robot toward Future Indoor Surveillance Mission in the Fukushima Daiichi Nuclear Power Plant,” J. of the Robotics Society of Japan, Vol.32, No.2, pp. 92-97, 2014.
- [4] T. Uehara and N. Suganuma, “Change of Environment Leading to Development of the Quadruped Robot,” J. of the Robotics Society of Japan, Vol.32, No.2, pp. 139-140, 2014.
- [5] T. Trainer, “Development of Unmanned Systems after March 2011 Incident,” J. of the Robotics Society of Japan, Vol.32, No.2, pp. 133-136, 2014.
- [6] K. Nagatani, S. Kiribayashi, Y. Okada, K. Otake, K. Yoshida, S. Tadokoro, T. Nishimura, T. Yoshida, E. Koyanagi, M. Fukushima, and S. Kawatsuma, “Emergency Response to the Nuclear Accident at the Fukushima Daiichi Nuclear Power Plants using Mobile Rescue Robots,” J. of Field Robotics, Vol.30, No.1, pp. 44-63, 2013.
- [7] K. Kon, H. Igarashi, N. Sato, and T. Kamegawa, “Development of a Practical Mobile Robot Platform for NBC Disasters and Its Field Test,” Proc. of IEEE Int. Symp. on Safety, Security, and Rescue Robotics (SSRR), pp. 1-6, 2012.
- [8] R. Hodoshima, K. Ueda, H. Ishida, M. Guarnieri, E. F. Fukushima, and S. Hirose, “Telerobotic Control System to Enhance Rescue Operations for Arm-Equipped Tracked Vehicle HELIOS IX,” J. of Robotics and Mechatronics, Vol.26, No.1, pp. 17-33, 2013.
- [9] R. Fukui, Y. Kato, R. Takahashi, W. Wan, and M. Nakao, “Automated Construction System of Robot Locomotion and Operation Platform for Hazardous Environments – Basic System Design and Feasibility Study of Module Transferring and Connecting Motions,” J. of Field Robotics, 2016 (in press).
- [10] J. W. Romanishin, K. Gilpin, and D. Rus, “M-blocks: Momentum-driven, magnetic modular robots,” Proc. of IEEE/RSJ Int. Conf. on Intelligent Robots and Systems, pp. 4288-4295, 2013.
- [11] A. Bowyer, “Automated Construction using Co-operating Biomimetic Robots,” University of Bath Department of Mechanical Engineering Technical Report, November 2000.
- [12] A. A. Yusof, T. Kawamura, and H. Yamada, “Evaluation of Constructor robot telegrasping Force Perception Using Visual, Auditory and Force Feedback Integration,” J. of Robotics and Mechatronics, Vol.24, No.6, pp. 949-957, 2012.
- [13] H. Yamada, T. Kawamura, and K. Ootsubo, “Development of a Teleoperation System for a Constructor robot,” J. of Robotics and Mechatronics, Vol.26, No.1, pp. 110-111, 2014.
- [14] R. Guzman, R. Navarro, J. Ferre, and M. Moreno, “RESCUER: Development of a Modular Chemical, Biological, Radiological, and Nuclear Robot for Intervention, Sampling, and Situation Awareness,” J. of Field Robotics, 2016 (in press).
- [15] M. Hashimoto, C. Yokogawa, and T. Sadoyama, “Development and Control of a Face Robot Imitating Human Muscular Structures,” Proc. of IEEE/RSJ Int. Conf. on Intelligent Robots and Systems, pp. 1855-1860, 2006.
- [16] I. Kumagai, K. Kobayashi, S. Nozawa, Y. Kakiuchi, T. Yoshikai, K. Okada, and M. Inaba, “Development of a Full Body Multi-Axis Soft Tactile Sensor Suit for Life Sized Humanoid Robot and an Algorithm to Detect Contact States,” Proc. of IEEE-RAS Int. Conf. on Humanoid Robots, pp. 526-531, 2012.
- [17] L. Q. Tan, S. Q. Xie, I. C. Lin, and T. Lin, “Development of a multifingered Robotic Hand,” Proc. of IEEE Int. Conf. on Information and Automation, pp. 1541-1545, 2009.
- [18] W. Wang, S. Shams, D. Shin, C. Han, and H. Choi, “Soft Biomimetic Leg Design and Fabrication Process of Cockroach-Inspired Robot,” Proc. of IEEE Int. Conf. on Mechatronics and Automation, pp. 1405-1409, 2010.
- [19] J. G. Broughton and A. R. Hutchinson, “Adhesive systems for structural connections in timber,” Int. J. of Adhesion and Adhesives, Vol.21, No.3, pp. 177-186, 2001.
- [20] R. Fujisawa, N. Naohisa, S. Okazaki, R. Sato, Y. Ikemoto, and S. Dobata, “Active modification of the environment by a robot with construction abilities,” ROBOMECH J., Vol.2, No.9, 2015.
- [21] S. Revzen, M. Bhoite, A. Macasieb, and M. Yim, “Structure synthesis on-the-fly in a modular robot,” Proc. of IEEE/RSJ Int. Conf. on Intelligent Robots and Systems, pp. 4797-4802, 2011.
This article is published under a Creative Commons Attribution-NoDerivatives 4.0 Internationa License.