Paper:
Development of a Peristaltic-Movement Duct-Cleaning Robot for Application to Actual Environment - Examination of Brush Type and Installation Method to Improve Cleaning Efficiency –
Fumio Ito*, Takahiko Kawaguchi*, Yasuyuki Yamada**, and Taro Nakamura***
*Graduate School of Science and Engineering, Chuo University
1-13-27 Kasuga, Bunkyo-ku, Tokyo 112-8551, Japan
**Faculty of Engineering and Design, Hosei University
2-33 Ichigayatamachi, Shinjuku-ku, Tokyo 162-0843, Japan
***Faclty of Science and Engineering, Chuo University
1-13-27 Kasuga, Bunkyo-ku, Tokyo 112-8551, Japan
This paper describes a method to increase both the cleaning performance and speed of a peristaltic duct-cleaning robot, besides the cleaning of a real house duct. Duct piping ventilation is an important component for safeguarding indoor human health. However, dust accumulates inside such ducts during long-term use of ventilation systems. This dust leads to the generation of bacteria, dispersal of which can cause serious human health problems. Therefore, it is necessary to clean such ducts. The ducts used in factories, for example, have a large cross-sectional area and so are easy to clean by conventional duct-cleaning methods. However, as housing ducts have a small cross-sectional area and many curves, they are difficult to clean via the passive method of inserting a cleaning tool through the duct ports. For this reason, the authors attempted to develop a method of duct cleaning using a robot that imitates the peristaltic movement of earthworms. Herein, the authors examine the type and mounting position of the cleaning brush that produces the optimum cleaning efficiency. From this, we confirmed the duct cleanability of the peristaltic robot.
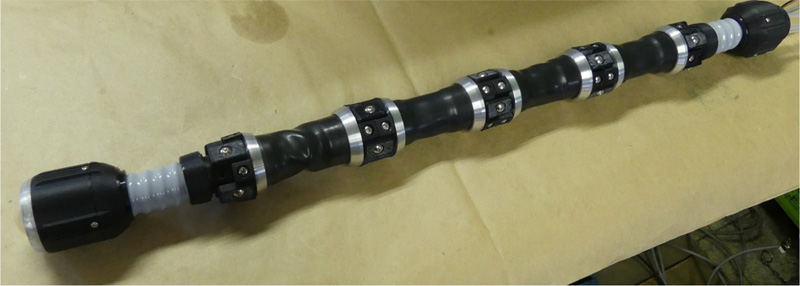
Peristaltic-movement duct-cleaning robot
- [1] B. Zhou, B. Zhao, and Z. Ta, “How Particle Resuspension from Inner Surfaces of Ventilation Ducts Affects Indoor Air Quality – A Modeling Analysis,” Aerosol Science and Technology, Vol.45, No.8, pp. 996-1009, 2011.
- [2] H. Yoshino, K. Amano, M. Matsumoto, K. Netsu, K. Ikeda, A. Nozaki, K. Kakuta, S. Hojo, and S. Ishikawa, “Long-termed Field Survey of Indoor Air Quality and Health Hazards in Sick House,” J. of Asian Architecture and Building Engineering, Vol.3, No.2, pp. 297-303, 2004.
- [3] H. M. Kim, Y. S. Choi, Y. G. Lee, and H. R. Choi, “Novel Mechanism for In-Pipe Robot Based on a Multiaxial Differential Gear Mechanism,” IEEE/ASME Trans. on Mechatronics, Vol.22, Issue 1, pp. 227-235, 2017.
- [4] A. Kakogawa, Y. Oka, and S. Ma, “Multi-link Articulated Wheeled In-pipe Robot with Underactuated Twisting Joints,” Proc. of 2018 IEEE Int. Conf. on Mechatronics and Automation, August 5-8, Changchun, China, pp. 942-947, 2018.
- [5] T. Nishimura, A. Kakogawa, and S. Ma, “Improvement of a Screw Drive In-Pipe Robot with Pathway Selection Mechanism to Pass through T-Branches,” J. Robot. Mechatron., Vol.25, No.2, pp. 340-346, 2013.
- [6] H. Amir, M. Heidari, R. Mehrandezh et al., “Dynamic analysis and human analogous control of a pipe crawling robot,” Proc. of IEEE/RSJ Int. Conf. on Intelligent Robots and Systems 2009, October 10-15, Missouri (TX), St. Louis, pp. 733-740, 2009.
- [7] Y.-S. Kwon, B. Lee, I.-C. Whang, W.-K. Kim, and B.-J. Yi, “A Flat Pipeline Inspection Robot with Two Wheel Chains,” 2011 IEEE Int. Conf. on Robotics and Automation, pp. 5141-5146, 2011.
- [8] H.-O. Lim and T. Ohki, “Development of Pipe Inspection robot,” Proc. of ICROS-SICE Int. Joint Conf., pp. 5717-5721, 2009.
- [9] S. U. Yang, H. M. Kim, J. S. Suh, Y. S. Choi, H. M. Mun, C. M. Park, H. Moon, and H. R. Choi, “Novel Robot Mechanism Capable of 3D Differential Driving Inside Pipelines,” 2014 IEEE/RSJ Int. Conf. on Intelligent Robots and Systems (IROS 2014), September 14-18, Chicago, IL, USA, pp. 1944-1949, 2014.
- [10] H. M. Kim, Y. S. Choi, Y. G. Lee, and H. R. Choi, “Novel Mechanism for In-Pipe Robot Based on a Multiaxial Differential Gear Mechanism,” IEEE/ASME Trans. on Mechatronics, Vol.22, No.1, pp. 227-235, 2017.
- [11] M. Konyo, K. Hatazaki, K. Isaki, and S. Tadokoro, “Development of an active scope camera driven by ciliary vibration mechanism,” Proc. of the 12th ROBOTICS Symposia, March 15-16, Nagaoka, pp. 460-465, 2007.
- [12] M. Konyo, K. Isaki, K. Hatazaki, S. Tadokoro, and F. Takemura, “Ciliary Vibration Drive mechanism for Active Scope Cameras,” J. Robot. Mechatron., Vol.20, No.3, pp. 490-499, 2008.
- [13] S. Xiao, Z. Bing, K. Huang, and Y. Huang, “Snake-like Robot Climbs Inside Different Pipes,” Proc. of 2017 IEEE Int. Conf. on Robotics and Biomimetics (ROBIO), pp. 1232-1239, 2017.
- [14] E. Prada, M. Valášek, I. Virgala, A. Gmiterko, M. Kelemen, M. Hagara, and T. Lipták, “New Approach of Fixation Possibilities Investigation for Snake Robot in the Pipe,” Proc. of 2015 IEEE Int. Conf. on Mechatronics and Automation (ICMA), pp. 1204-1210, 2015.
- [15] F. Trebuňa, I. Virgala, M. Pástor, T. Lipták, and L. Miková, “An inspection of pipe by snake robot,” Int. J. of Advanced Robotic Systems, Vol.13, pp. 1-12, 2016.
- [16] H. Shin, K.-M. Jeong, and J.-J. Kwon, “Development of a Snake Robot Moving in a Small Diameter Pipe,” Proc. of Int. Conf. on Control, Automation and Systems, October 27-30, 2010 in KINTEX, Gyeonggi-do, Korea, pp. 1826-1829, 2010.
- [17] Y. Tanise, K. Taniguchi, S. Yamazaki, M. Kamata, Y. Yamada, and T. Nakamura, “Development of an air duct cleaning robot for housing based on peristaltic crawling motion,” Proc. of 2017 IEEE Int. Conf. on Advanced Intelligent Mechatronics (AIM), pp. 1267-1272, 2017.
- [18] T. Tomita, T. Tanaka, and T. Nakamura, “Development of a peristaltic crawling robot for long-distance complex line sewer pipe inspections,” 2015 IEEE/RSJ Int. Conf. on Intelligent Robots and Systems (IROS), pp. 2742-2747, 2015.
- [19] M. Kamata, S. Yamazaki, Y. Tanise, Y. Yamada, and T. Nakamura, “Morphological change in peristaltic crawling motion of a narrow pipe inspection robot inspired by earthworm’s locomotion,” Advanced Robotics, Vol.32, No.7, pp. 386-397, 2018.
- [20] A. Kojima, M. Okui, Y. Yamada, and T. Nakamura, “Prolonging the lifetime of straight-fiber-type pneumatic rubber artificial muscle by shape consideration and material development,” Proc. of 2018 IEEE Int. Conf. on Soft Robotics (RoboSoft) Livorno, Italy, pp. 24-28, 2018.
- [21] N. Saga, J. Nagase, and T. Saikawa, “Pneumatic artificial muscles based on biomechanical characteristics of human muscles,” Applied Bionics and Biomechanics, Vol.3, No.3, pp. 191-197, 2006.
This article is published under a Creative Commons Attribution-NoDerivatives 4.0 Internationa License.