Paper:
Realization of MDOF Soft Actuator Capable of Bending in Arbitrary Directions
Taiki Tsuji*1, Daisuke Sasaki*2, Jun Kadowaki*3, Hayato Yase*4, and Kaisei Harada*5
*1Graduate School of Science for Creative Emergence, Kagawa University
2217-20 Hayashicho, Takamatsu, Kagawa 761-0396, Japan
*2Faculty of Engineering and Design, Kagawa University
2217-20 Hayashicho, Takamatsu, Kagawa 761-0396, Japan
*3Department of Electro-Mechanical Systems Engineering, National Institute of Technology, Kagawa College (NIT, Kagawa)
355 Chokushicho, Takamatsu, Kagawa 761-8058, Japan
*4Faculty of Science and Engineering, Kindai University
3-4-1 Kowakae, Higashiosaka, Osaka 577-8502, Japan
*5Graduate School of Engineering, Kagawa University
2217-20 Hayashicho, Takamatsu, Kagawa 761-0396, Japan
In recent years, soft machine systems that employ soft actuators with high affinity and safety toward humans have attracted attention. The soft actuators developed thus far include those that can extend or bend by only supplying compressed air, or those that switch their motions by modifying their structures. However, the type of motion is limited and structural modifications are required to switch between different movements. In this study, we developed a soft actuator with multiple degrees of freedom that allowed switching between extension and bending without structural changes. This actuator comprised a structure in which flexible linear brakes (FLBs), which are negative-pressure-driven linear braking mechanisms, were arranged alongside a bellows-structured silicone rubber tube (bellows tube). The bellows tube extended when compressed air was supplied. When engaged, the FLBs provided fiber reinforcement against the bellows tube and bent the actuator. Thus, the actuator switched between extension and bending by engaging or disengaging the FLBs without structural changes. In this paper, we describe the structure of the actuator and the mechanical model used to arbitrarily change its bending direction using braking mechanisms.
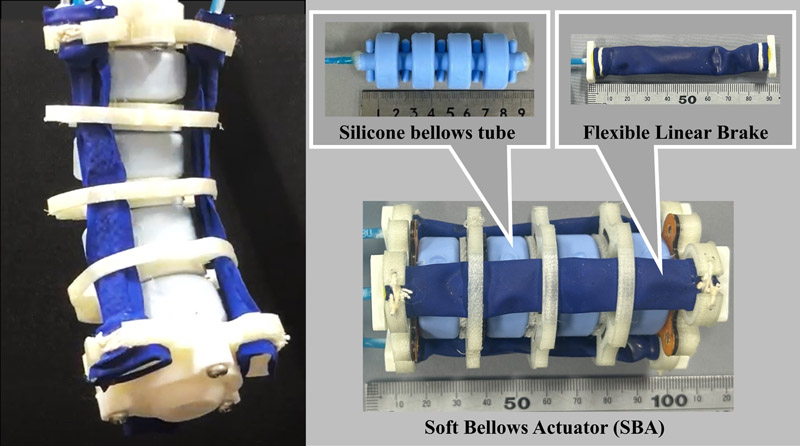
Actual motion and structure of SBA
- [1] Cabinet Office, “Situation of the Ageing Population,” Annual Report on the Ageing Society [Summary] FY2021, p. 4, 2021.
- [2] H. Kobayashi, T. Shiban, and Y. Ishida, “Realization of All 7 Motions for the Upper Limb by a Muscle Suit,” J. Robot. Mechatron., Vol.16, No.5, pp. 504-512, 2004. https://doi.org/10.20965/jrm.2004.p0504
- [3] K. Suzumori, “Overview of the Kakenhi Grant-in-Aid for Scientific Research on Innovative Areas: Science of Soft Robots,” J. Robot. Mechatron., Vol.32, No.2, pp. 195-201, 2022. https://doi.org/10.20965/jrm.2022.p0195
- [4] P. Yuan, G. Kawano, and H. Tsukagoshi, “Design and Modeling of Soft Pneumatic Helical Actuator with High Contraction Ratio,” J. Robot. Mechatron., Vol.32, No.5, pp. 1061-1070, 2020. https://doi.org/10.20965/jrm.2020.p1061
- [5] T. Umedachi and M. Shimizu, “Toward Self-Modifying Bio-Soft Robots,” J. Robot. Mechatron., Vol.34, No.2, pp. 219-222, 2022. https://doi.org/10.20965/jrm.2022.p0219
- [6] K. Nishikawa, K. Hirata, and M. Takaiwa, “Development of Self-Powered 5-Finger Pneumatically Driven Hand Prosthesis Using Supination of Forearm,” J. Robot. Mechatron., Vol.34, No.2, pp. 454-465, 2022. https://doi.org/10.20965/jrm.2022.p0454
- [7] L. Fracczak, M. Nowak, and K. Koter, “Flexible push pneumatic actuator with high elongation,” Sens. Actuators A Phys., Vol.321, Article No.112578, 2021. https://doi.org/10.1016/j.sna.2021.112578
- [8] A. A. Caldron, J. C. Ugalde, L. Chang, J. C. Zagal, and N. O. Perez-Arancibia, “An Earthworm-Inspired Soft Robot With Perceptive Artificial Skin,” Bioinspir. Biomim., Vol.14, Article No.056012, 2019. https://doi.org/10.1088/1748-3190/ab1440
- [9] S. Kikuchi, Y. Yamada, R. Higashi, and T. Morita, “Super Multi-Joint Manipulator by Using Creased Plate and Pneumatic Actuators Arranged Antagonistically,” J. Robot. Mechatron., Vol.27, No.3, pp. 276-285, 2015. https://doi.org/10.20965/jrm.2015.p0276
- [10] Z. Xie, A. G. Domel, N. An, C. Green, Z. Gong, T. Wrang et al., “Octopus Arm-Inspired Tapered Soft Actuators with Suckers for Improved Grasping,” Soft Rob., Vol.7, No.5, pp. 639-648, 2020. https://doi.org/10.1089/soro.2019.0082
- [11] Z. Guoliang, H. Yangdong, and D. Weiqiang, “A soft pneumatic dexterous gripper with convertible grasping modes,” Int. J. Mech. Sci., Vol.153, pp. 445-456, 2019. https://doi.org/10.1016/j.ijmecsci.2019.02.028
- [12] M. Fatahillah, N. Oh, and H. Rodrigue, “A Novel Soft Bending Actuator Using Combined Positive and Negative Pressures,” Front. Bioeng. Biotechnol., Sec. Bionics and Biomimetics, Vol.8, Article No.472, 2020. https://doi.org/10.3389/fbioe.2020.00472
- [13] M. L. Dezaki, M. Bodaghi, A. Serjouei, and S. Afazov, “Soft Pneumatic Actuators with Controllable Stiffness by Bio-Inspired Lattice Chambers and Fused Deposition Modeling 3D Printing,” Adv. Eng. Mater., Vol.25, No.6, Article No.2200797, 2022. https://doi.org/10.1002/adem.202200797
- [14] H. Li, D. Xie, and Y. Xie, “A Soft Pneumatic Gripper with Endoskeletons Resisting Out-of-Plane Bending,” Actuators, Vol.11, No.9, Article No.246, 2022. https://doi.org/10.3390/act11090246
- [15] H. Li, J. Yao, P. Zhou, X. Chen, Y. Xu, and Y. Zhao, “High-force soft pneumatic actuators based on novel casting method for robotic applications,” Sens. Actuators A Phys., Vol.306, Article No.111957, 2020. https://doi.org/10.1016/j.sna.2020.111957
- [16] A. Bhat, J. W. Ambrose, and R. C. Yeow, “Composite Soft Pneumatic Actuators Using 3D Printed Skins,” IEEE Rob. Autom. Lett., Vol.8, No.4, pp. 2086-2093, 2023. https://doi.org/10.1109/lra.2023.3246841
- [17] J. Zhang, H. Wei, Y. Shan, P. Li, Y. Zhao, and L. Qi et al., “Modeling and Experimental Study of a Novel Multi-DOF Parallel Soft Robot,” IEEE Access, Vol.8, pp. 62932-62942, 2020. https://doi.org/10.1109/access.2020.2983260
- [18] T. Kalisky, Y. Wang, B. Shih, D. Drotman, S. Jadhav, and E. Aronoff-Spencer et al., “Differential Pressure Control of 3D Printed Soft Fluidic Actuators,” Proc. of 2017 IEEE/RSJ Int. Conf. on Intelligent Robots and Systems, pp. 6207-6213, 2017. https://doi.org/10.1109/iros.2017.8206523
- [19] T. Watanabe, D. Sasaki, J. Kadowaki, H. Yase, and K. Harada, “Modeling and Application of a Pneumatic Flexible Linear Brake for Power Asist Devices,” J. Robot. Mechatron., Vol.36, No.4, pp. 836-846, 2024. https://doi.org/10.20965/jrm.2024.p0836
This article is published under a Creative Commons Attribution-NoDerivatives 4.0 Internationa License.