Paper:
Development of Artificial Rubber Muscle Capable of Human-Like Pulling Motion
Jun Kadowaki*1, Daisuke Sasaki*2, Hayato Yase*3, Kaisei Harada*4, and Shinichiro Shobako*1
*1Department of Electro-Mechanical Systems Engineering, National Institute of Technology, Kagawa College
355 Chokushicho, Takamatsu, Kagawa 761-8058, Japan
*2Faculty of Engineering and Design, Kagawa University
2217-20 Hayashicho, Takamatsu, Kagawa 761-0396, Japan
*3Faculty of Science and Engineering, Kindai University
3-4-1 Kowake, Higashiosaka, Osaka 577-8502, Japan
*4Graduate School of Engineering, Kagawa University
2217-20 Hayashicho, Takamatsu, Kagawa 761-0396, Japan
Wearable power-assisted robots driven by artificial rubber muscles should be designed with a wide range of assistance capabilities to support various tasks while minimizing the sense of restraint when worn. Ideally, to realize a compact and lightweight power-assisted robot, the size of the artificial rubber muscle should be maintained while increasing the amount of movement. This study aims to develop an artificial rubber muscle that can achieve a wide range of assistance through rope-based force transmission. An artificial rubber muscle is proposed that can transmit force through a human-like pulling motion using a rope. This McKibben-type artificial rubber muscle is enhanced with a power transmission mechanism. The proposed artificial muscle has two layers: an inner layer that is deformed by air pressure to grasp the rope and an outer layer that pulls the rope by contraction. Each layer moves stepwise by supplying compressed air to realize the pulling motion of the rope. In this study, a prototype of the proposed artificial muscle was fabricated, and its operational principle was confirmed experimentally. Additionally, the force transmission performance was verified by comparing the contraction force of the artificial muscle with the tensile force of the rope.
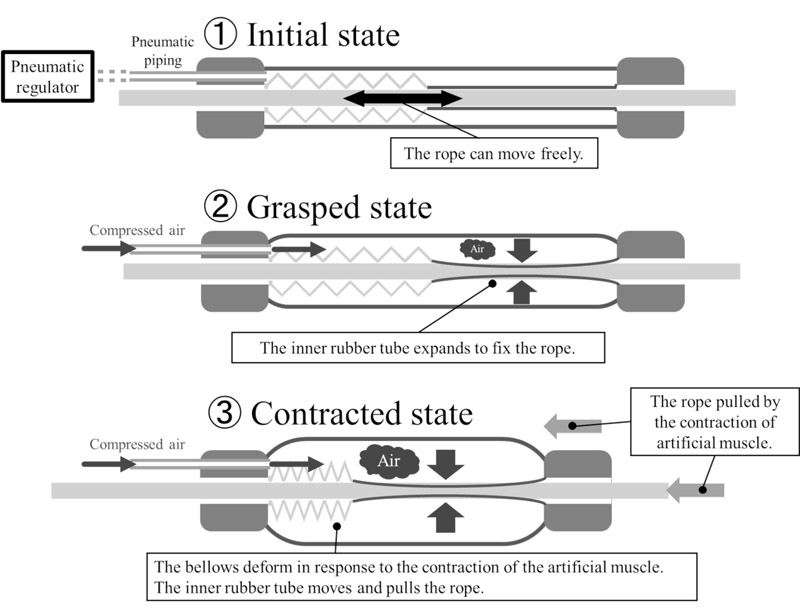
Operating principle of the human-like pulling motion
- [1] H. Kobayashi, T. Aida, and T. Hashimoto, “Muscle suit development and factory application,” Int. J. Automation Technol., Vol.3, No.6, pp. 709-715, 2009. https://doi.org/10.20965/ijat.2009.p0709
- [2] Y. Muramatsu, H. Umehara, and H. Kobayashi, “Improvement and quantitative performance estimation of the back support muscle suit,” Proc. of the 35th Int. Conf. on the IEEE Engineering Medicine and Biology Society (EMBC 2013), pp. 2844-2849, 2013. https://doi.org/10.1109/EMBC.2013.6610133
- [3] M. Ide, T. Hashimoto, K. Matsumoto, and H. Kobayashi, “Evaluation of the Power Assist Effect of Muscle Suit for Lower Back Support,” IEEE Access, Vol.9, pp. 3249-3260, 2020. https://doi.org/10.1109/ACCESS.2020.3047637
- [4] T. Noritsugu, M. Takaiwa, and D. Sasaki, “Development of Power Assist Wear Using Pneumatic Rubber Artificial Muscles,” J. Robot. Mechatron., Vol.21, No.5, pp. 607-613, 2009. https://doi.org/10.20965/jrm.2009.p0607
- [5] Y. Kadowaki, T. Noritsugu, M. Takaiwa, D. Sasaki, and M. Kato, “Development of Soft Power-Assist Glove and Control Based on Human Intent,” J. Robot. Mechatron., Vol.23, No.2, pp. 281-291, 2011. http://doi.org/10.20965/jrm.2011.p0281
- [6] K. Uchiyama, T. Ito, and H. Tomori, “Development of Endoskeleton Type Knee Joint Assist Orthosis Using McKibben Type Artificial Muscle,” J. Robot. Mechatron., Vol.34, No.2, pp. 390-401, 2022. https://doi.org/10.20965/jrm.2022.p0390
- [7] D. Sasaki, T, Noritsugu, and M. Takaiwa, “Development of pneumatic lower limb power assist wear without exoskeleton,” 2012 IEEE/RSJ Int. Conf. on Intelligent Robots and Systems (IROS2012), pp. 1239-1244, 2012. https://doi.org/10.1109/IROS.2012.6385571
- [8] T. Noritsugu, D. Sasaki, M. Kameda, A. Fukunaga, and M. Takaiwa, “Wearable Power Assist Device for Standing Up Motion Using Pneumatic Rubber Artificial Muscles,” J. Robot. Mechatron., Vol.19, No.6, pp. 619-628, 2007. https://doi.org/10.20965/jrm.2007.p0619
- [9] J. L. McKibben, “Artificial muscle,” Life, pp. 87-88, 1960.
- [10] V. L. Nickel, J. Perry, and A. L. Garrett, “Development of Useful Function in the Severely Paralyzed Hand,” The J. of Bone and Joint Surgery, Vol.45, No.5, pp. 933-952, 1963.
- [11] C. Ferraresi, W. Franco, and A. M. Bertetto, “Flexible Pneumatic Actuators: A Comparison between The McKibben and the Straight Fibres Muscle,” J. Robot. Mechatron., Vol.13, No.1, pp. 56-63, 2001. https://doi.org/10.20965/jrm.2001.p0056
- [12] N. Saito, T. Satoh, and N. Saga, “Effects on knee joint force from a body weight load reduction system driven by rubber-less artificial muscle,” Industrial Robot, Vol.46, No.5, pp. 642-649, 2019. https://doi.org/10.1108/IR-11-2018-0224
- [13] N. Saga, K. Shimada, D. Inamori, N. Saito, T. Satoh, and J. Nagase, “Smart Pneumatic Artificial Muscle Using a Bend Sensor like a Human Muscle with a Muscle Spindle,” Sensors, Vol.22, No.22, Article No.8975, 2022. https://doi.org/10.3390/s22228975
- [14] A. Ohno, H. Nabae, and K. Suzumori, “Static analysis of powered low-back orthosis driven by thin pneumatic artificial muscles considering body surface deformation,” Proc. of 2015 IEEE/SICE Int. Symp. on System Integration (SII), pp. 39-44, 2015. https://doi.org/10.1109/SII.2015.7404892
- [15] T, Doi, S, Wakimoto, K. Suzumori, and K. Mori, “Proposal of flexible robotic arm with thin McKibben actuators mimicking octopus arm structure,” 2016 IEEE/RSJ Int. Conf. on Intelligent Robots and Systems (IROS), pp. 5503-5508, 2016. https://doi.org/10.1109/IROS.2016.7759809
- [16] F. Daerden and D. Lefeber, “The Concept and Design of Pleated Pneumatic Artificial Muscles,” Int. J. of Fluid Power, Vol.2, No.3, pp. 76-83, 2001.
- [17] H. Takemura, D. Sasaki, K, Yokoyama, and I. Kikutani, “Development of Wearable Power Assist Robot for Shoulder Using Disk Brake Mechanism Driven with Pneumatic Soft Actuator,” Trans. of the Society of Instrument and Control Engineers, Vol.54, No.1, pp. 76-83, 2018 (in Japanese). https://doi.org/10.9746/sicetr.54.76
- [18] Y. Yamada, A. Kojima, M. Okui, and T. Nakamura, “Improvement for Compatibility of High Durability and High Efficiency of Straight-fiber-type Pneumatic Artificial Muscle,” Trans. of the Society of Instrument and Control Engineers, Vol.54, No.6, pp. 557-563, 2018 (in Japanese). https://doi.org/10.9746/sicetr.54.557
- [19] T. Nakamura, “Peristaltic Mixing Pump Based on Bowel Peristalsis Using Pneumatic Artificial Rubber Muscles and Prospects for Practical Applications,” J. Robot. Mechatron., Vol.34, No.2, pp. 276-278, 2022. https://doi.org/10.20965/jrm.2022.p0276
- [20] N. Saga, T. Nakamura, and K. Yaegashi, “Mathematical Model of Pneumatic Artificial Muscle Reinforced by Straight Fibers,” J. of Intelligent Material Systems and Structures, Vol.18, No.2, pp. 175-180, 2007. http://doi.org/10.1177/1045389X06063462
This article is published under a Creative Commons Attribution-NoDerivatives 4.0 Internationa License.