Paper:
Driving Conditions for Miniaturization of Micro Flow Control Valves Using Particle Excitation
Daisuke Hirooka
, Naomichi Furushiro
, and Tomomi Yamaguchi
Department of Mechanical Engineering, Kansai University
3-3-35 Yamate-cho, Suita, Osaka 564-8680, Japan
In this study, we introduce research aimed at developing a compact particle-excitation flow control valve that enables continuous control of air flow rate. We have been developing a compact control valve with continuous flow control for application to soft actuators. The control valve that we are developing uses particles as a valve plug, which does not require a valve plug positioning function and allows the control valve to be miniaturized. Furthermore, by controlling the movements of the particles on the orifice, the control flow rate can be made finer and the response can be improved. On the other hand, the past driving principle used the resonant mode of an oscillator utilizing a piezoelectric element (PZT) to control the motion of the particles. In this vibration mode, the size of the oscillator limits the miniaturization. Therefore, we propose a drive method that uses simple plate deflection vibration mode. This drive method eliminates the need for a large oscillator, and thus reduces the size of the control valve. To confirm the feasibility of the proposed drive method, we fabricated a prototype and evaluated its characteristics during flow control.
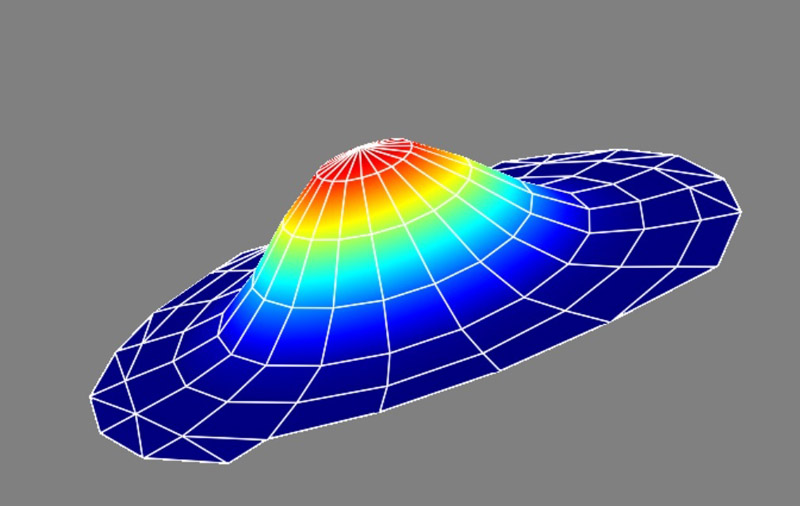
Image of simple plate deflection vibration mode
- [1] K. Suzumori, “New robotics pioneered by fluid power,” J. Robot. Mechatron., Vol.32, No.5, pp. 854-862, 2020. https://doi.org/10.20965/jrm.2020.p0854
- [2] T. Nakamura, “Fluid-driven soft actuators for soft robots,” J. Robot. Mechatron., Vol.36, No.2, pp. 251-259, 2024. https://doi.org/10.20965/jrm.2024.p0251
- [3] S. C. Mawah and Y. J. Park, “Tendon-driven variable-stiffness pneumatic soft gripper robot,” Robotics, Vol.12, Issue 5, Article No.128, 2023. https://doi.org/10.3390/robotics12050128
- [4] K. Nishikawa, K. Hirata, and M. Takaiwa, “Development of pneumatically driven hand capable of grasping flexible objects,” J. Robot. Mechatron., Vol.32, No.5, pp. 923-930, 2020. https://doi.org/10.20965/jrm.2020.p0923
- [5] S. Koizumi, T.-H. Chang, H. Nabae, G. Endo, K. Suzumori, M. Mita, K. Saitoh, K. Hatakeyama, S. Chida, and Y. Shimada, “Soft robotic gloves with thin McKibben muscles for hand assist and rehabilitation,” Proc. of the 2020 IEEE/SICE Int. Symp. on System Integration, 2020. https://doi.org/10.1109/SII46433.2020.9025832
- [6] S. Shimooka, R. Suzuki, T. Uehara, T. Hirayama, and A. Gofuku, “Development of ankle-joint rehabilitation device for bedridden patient using fan-shaped pneumatic soft actuator driven at low pressure,” J. Robot. Mechatron., Vol.34, No.2, pp. 565-576, 2023. https://doi.org/10.20965/jrm.2023.p0565
- [7] K. Nishikawa, K. Hirata, and M. Takaiwa, “Development of self-powered 5-finger pneumatically driven hand prosthesis using supination of forearm,” J. Robot. Mechatron., Vol.34, No.2, pp. 454-465, 2022. https://doi.org/10.20965/jrm.2022.p0454
- [8] S. Hirai and K. Kato, “Micro pneumatic valves for wearable robotic systems,” 24th IEEE Int. Symp. on Robot and Human Interactive Communication, pp. 652-657, 2015. https://doi.org/10.1109/ROMAN.2015.7333584
- [9] T. Kobayashi, T. Akagi, S. Dohta, F. Cho, T. Shinohara, and M. Yokota, “Slide-gate type multi-port switching valve,” J. Robot. Mechatron., Vol.35, No.3, pp. 633-640, 2023. https://doi.org/10.20965/jrm.2023.p0633
- [10] T. Kanno, T. Hasegawa, T. Miyazaki, N. Yamamoto, D. Haraguchi, and K. Kawashima, “Development of a poppet-type pneumatic servo valve,” Appl. Sci., Vol.8, Issue 11, Article No.2094, 2018. https://doi.org/10.3390/app8112094
- [11] K. Tadano, Y. Ishida, and H. Takeishi, “Development of a four-way pinch-type servo valve for pneumatic actuator,” Applied Sciences, Vol.10, Issue 3, Article No.1066, 2020. https://doi.org/10.3390/app10031066
- [12] S. Dohta, T. Akagi, W. Kobayashi, S. Shimooka, and Y. Masago, “Improvement of a pneumatic control valve with self-holding function,” Materials Science and Engineering, Vol.249, Article No.012002, 2017. https://doi.org/10.1088/1757-899X/249/1/012002
- [13] P. Rothemund, A. Ainla, L. Belding, D. J. Preston, S. Kurihara, Z. Suo, and G. M. Whitesides, “A soft, bistable valve for autonomous control of soft actuators,” Science Robotics, Vol.3, No.16, Article No.eaar7986, 2018. https://doi.org/10.1126/scirobotics.aar7986
- [14] F. Zhao, S. Dohta, and T. Akagi, “Development and analysis of small-sized quasi-servo valve for flexible bending actuator,” Trans. of JSME, Series C, Vol.76, No.772, pp. 3665-3671, 2010. https://doi.org/10.1299/kikaic.76.3665
- [15] Y. Sugimoto, K. Naniwa, D. Nakanishi, and K. Osuka, “Tension control of a McKibben pneumatic actuator using a dynamic quantizer,” J. Robot. Mechatron., Vol.35, No.4, pp. 1038-1046, 2023. https://doi.org/10.20965/jrm.2023.p1038
- [16] T. Shin, T. Ibayashi, and K. Kogiso, “Detailed dynamic model of antagonistic PAM system and its experimental validation: Sensorless angle and torque control with UKF,” IEEE/ASME Trans. on Mechatronics, Vol.27, Issue 3, pp. 1715-1726, 2005. https://doi.org/10.1109/TMECH.2021.3086218
- [17] D. Hirooka, K. Suzumori, and T. Kanda, “Flow control valve for pneumatic actuators using particle excitation by PZT vibrator,” Sensors and Actuators A: Physical, Vol.155, Issue 2, pp. 285-289, 2009. https://doi.org/10.1016/j.sna.2009.07.005
- [18] D. Hirooka, T. Yamaguchi, N. Furushiro, K. Suzumori, and T. Kanda, “Development of novel particle excitation flow control valve for stable flow characteristics,” Int. J. Automation Technol., Vol.10, No.4, pp. 540-548, 2016. https://doi.org/10.20965/ijat.2016.p0540
- [19] D. Hirooka, N. Furushiro, and T. Yamaguchi, “Micro flow control valve with stable condition using particle-excitation,” J. Robot. Mechatron., Vol.34, No.2, pp. 422-429, 2022. https://doi.org/10.20965/jrm.2022.p0422
- [20] D. Hirooka, T. Yamaguchi, N. Furushiro, K. Suzumori, and T. Kanda, “Particle-excitation flow-control valve using piezo vibration-improvement for a high flow rate and research on controllability,” IEEJ Trans. on Sensors and Micromachines, Vol.137, No.1, pp. 32-37, 2017. https://doi.org/10.1541/ieejsmas.137.32
This article is published under a Creative Commons Attribution-NoDerivatives 4.0 Internationa License.