Paper:
Development of a Robot Combining a Hyper-Extension Unit and an Earthworm-Type Robot Enhancing Propulsion and Traction
Ryusei Okuma*
, Sogo Matsuo**, Fumio Ito*
, and Taro Nakamura*

*Department of Precision Mechanics, Faculty of Science and Engineering, Chuo University
1-13-27 Kasuga, Bunkyo-ku, Tokyo 112-8551, Japan
**Department of System Design, Faculty of Engineering and Design, Hosei University
2-15-2 Ichigayatamachi, Shinjuku-ku, Tokyo 162-0843, Japan
This paper proposes a robot that combines a hyper-extension unit at the front with an earthworm-type robot at the rear, designed to inspect long, narrow, and complex pipelines. In conventional in-pipe inspection robots with simple designs, there was no mechanism for the robot to effectively exert traction and propulsion while optimizing speed according to the required force. Therefore, this paper describes the development of a robot that combines a hyper-extension unit at the front, which achieves an elongation rate of approximately 300% even at low expansion rates, with an earthworm-type robot at the rear. The developed robot can operate in two patterns: pattern 1 combines the movements of an earthworm and an inchworm, while pattern 2 resembles that of an inchworm. It can switch between speed and force modes by changing its motion pattern. Experimental comparison of the horizontal straight pipe movement speeds of pattern 1 and pattern 2 without and with load showed that pattern 2 was 3.32 times faster than pattern 1 without load and that pattern 1 was 1.51 times faster than pattern 2 with load, clarifying the importance of changing robot’s motion pattern according to the load. The vertical pipe movement speed without load was 3.04 times faster in pattern 2 than in pattern 1. The proposed robot traveled 1.43 times faster than the conventional robot equipped with a conventional spring mechanism when passing through the elbow pipe using pattern 1. However, it could not pass through the elbow pipe using pattern 2, showing the importance of changing the robot’s motion pattern when passing through bent pipes. These results indicate that the proposed robot has the potential to achieve more efficient inspection in long-distance, small-diameter, complex pipes by changing its motion pattern according to the situation in the inspection pipe.
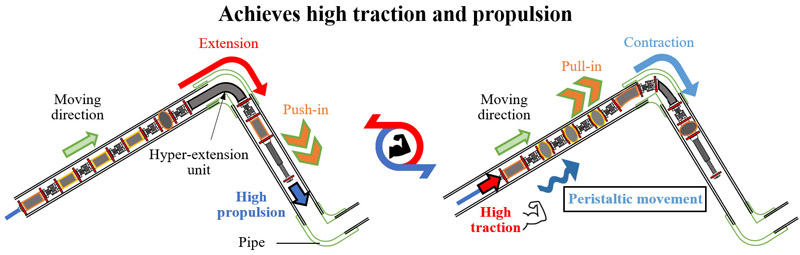
Concept of earthworm-type in-pipe inspection robot with a hyper-extension unit in front part
- [1] H. Masuta, H. Watanabe, K. Sato, and H. Lim, “Recognition of branch pipe for pipe inspection robot using fiber grating vision sensor,” Proc. of the 2013 Int. Conf. on Ubiquitous Robots and Ambient Intell. (URAI2013), pp. 633-638, 2013. https://doi.org/10.1109/URAI.2013.6677411
- [2] G. H. Mill, A. E. Jackson, and R. C. Richardson, “Advances in the inspection of unpiggable pipelines,” Robotics, Vol.6, Issue 4, Article No.36, 2017. https://doi.org/10.3390/robotics6040036
- [3] S. Yoda, Y. Wakibe, and Y. Imagawa, “Inspection methods of piping,” Bull. Soc. Sea Water Sci., Vol.68, pp. 57-62, 2014 (in Japanese).
- [4] Q. Ma, G. Tian, Y. Zeng, R. Li, H. Song, Z. Wang, B. Gao, and K. Zeng, “Pipeline in-line inspection method, instrumentation and data management,” Sensors, Vol.21, Issue 11, Article No.3862, 2021. https://doi.org/10.3390/s21113862
- [5] M. A. A. Wahed and M. R. Arshad, “Wall-press type pipe inspection robot,” Proc. of 2017 IEEE 2nd Int. Conf. on Automatic Control and Intell. Syst. (I2CACIS), pp. 185-190, 2017. https://doi.org/10.1109/I2CACIS.2017.8239055
- [6] B. Zhang, M. Abdulaziz, K. Mikoshi, and H. Lim, “Development of an in-pipe mobile robot for inspecting clefts of pipes,” Proc. of 2019 IEEE Int. Conf. Cybernetics Intell. Syst. (CIS) and IEEE Conf. Robotics, Automation and Mechatronics (RAM), pp. 204-208, 2019. https://doi.org/10.1109/CIS-RAM47153.2019.9095803
- [7] H. M. Kim, Y. S. Choi, Y. G. Lee, and H. R. Choi, “Novel mechanism for in-pipe robot based on a multiaxial differential gear mechanism,” IEEE/ASME Trans. on Mechatronics, Vol.22, Issue 1, pp. 227-235, 2016. https://doi.org/10.1109/TMECH.2016.2621978
- [8] A. Kakogawa and S. Ma, “A multi-link in-pipe inspection robot composed of active and passive compliant joints,” Proc. of 2020 IEEE/RSJ Int. Conf. on Intell. Robots Syst. (IROS), pp. 6472-6478, 2020. https://doi.org/10.1109/IROS45743.2020.9341478
- [9] J. A. I. Diaz, M. I. Ligeralde Jr., M. A. B. Antonio, P. A. R. Mascardo, J. M. Z. Maningo, A. H. Fernando, R. R. P. Vicerra, E. P. Dadios, and A. A. Bandala, “Development of an adaptive in-pipe inspection robot with rust detection and localization,” Proc. of 2018 IEEE Region 10 Conf. (TENCON 2018), pp. 2504-2509, 2018. https://doi.org/10.1109/TENCON.2018.8650073
- [10] A. Kakogawa and S. Ma, “Design of an underactuated parallelogram crawler module for an in-pipe robot,” Proc. of 2013 IEEE Int. Conf. on Robotics and Biomimetics (ROBIO), pp. 1324-1329, 2013. https://doi.org/10.1109/ROBIO.2013.6739648
- [11] S. Xiao, Z. Bing, K. Huang, and Y. Huang, “Snake-like robot climbs inside different pipes,” Proc. of 2017 IEEE Int. Conf. on Robotics and Biomimetics (ROBIO), pp. 1232-1239, 2017. https://doi.org/10.1109/ROBIO.2017.8324586
- [12] A. Selvarajan, A. Kumar, D. Sethu, and M. A. Bin Ramlan, “Design and development of a snake-robot for pipeline inspection,” Proc. of 2019 IEEE Student Conf. on Research and Development (SCOReD), pp. 237-242, 2019. https://doi.org/10.1109/SCORED.2019.8896254
- [13] A. Zagler and F. Pfeiffer, ““MORITZ” a pipe crawler for tube junctions,” Proc. of 2003 IEEE Int. Conf. on Robotics and Automation, Vol.3, pp. 2954-2959, 2003. https://doi.org/10.1109/ROBOT.2003.1242044
- [14] X. Yu, Y. Chen, M. Z. Q. Chen, and J. Lam, “Development of a novel in-pipe walking robot,” Proc. of 2015 IEEE Int. Conf. on Information and Automation (ICIA), pp. 264-268, 2015. https://doi.org/10.1109/ICInfA.2015.7279314
- [15] K. Isaki, A. Niitsuma, M. Konyo, F. Takemura, and S. Tadokoro, “Development of an active flexible cable by ciliary vibration drive for scope camera,” Proc. of 2006 IEEE/RSJ Int. Conf. on Intell. Robots Syst. (IROS), pp. 3946-3951, 2006. https://doi.org/10.1109/IROS.2006.281829
- [16] J. Lim, H. Park, S. Moon, and B. Kim, “Pneumatic robot based on inchworm motion for small diameter pipe inspection,” Proc. of 2007 IEEE Int. Conf. on Robotics and Biomimetics (ROBIO), pp. 330-335, 2007. https://doi.org/10.1109/ROBIO.2007.4522183
- [17] T. Yamamoto, S. Sakama, and A. Kamimura, “Pneumatic duplex-cambered inchworm mechanism for narrow pipes driven by only two air supply lines,” IEEE Robot. Autom. Lett., Vol.5, Issue 4, pp. 5034-5042, 2020.
- [18] F. Ito, T. Kawaguchi, M. Kamata, Y. Yamada, and T. Nakamura, “Proposal of a peristaltic motion type duct cleaning robot for traveling in a flexible pipe,” Proc. of 2019 IEEE/RSJ Int. Conf. on Intell. Robots Syst. (IROS), pp. 6614-6621, 2019. https://doi.org/10.1109/IROS40897.2019.8967648
- [19] Y. Mano, R. Ishikawa, Y. Yamada, and T. Nakamura, “Development of high-speed type peristaltic crawling robot for long-distance and complex-line sewer pipe inspection,” Proc. of 2018 IEEE/RSJ Int. Conf. on Intell. Robots Syst. (IROS), pp. 8177-8183, 2018. https://doi.org/10.1109/IROS.2018.8593436
- [20] X. Zhou, Y. Teng, and X. Li, “Development of a new pneumatic-driven earthworm-like soft robot,” Proc. of 2016 23rd Int. Conf. on Mechatronics and Machine Vision in Practice (M2VIP), 2016. https://doi.org/10.1109/M2VIP.2016.7827269
- [21] F. Ito, Y. Naruse, K. Takaya, J. Watanabe, and T. Nakamura, “Traction amplified actuation system for inspecting narrow and complex pipes using enhanced linear antagonistic mechanism – Bend pipe passage model and force comparison,” IEEE Access, Vol.11, pp. 76156-76165, 2023. https://doi.org/10.1109/ACCESS.2023.3297147
- [22] R. Okuma, Y. Naruse, F. Ito, and T. Nakamura, “Proposal of a moving speed enhancing method for peristaltic motion type in-pipe inspection robot with linear antagonistic mechanism using endoskeletal type artificial muscles,” 2023 IEEE Int. Conf. on Robotics and Biomimetics (ROBIO), 2023. https://doi.org/10.1109/ROBIO58561.2023.10354779
- [23] R. Okuma, Y. Naruse, F. Ito, and T. Nakamura, “Peristaltic soft robot for long-distance pipe inspection with an endoskeletal structure for propulsion and traction amplification,” Proc. of 2024 IEEE/RSJ Int. Conf. on Intell. Robots Syst. (IROS), 2024.
- [24] F. Ito, T. Itsuno, and T. Nakamura, “MD-LUFFY: Massively deformed linearly-elongation-actuator using flexible fiber and yarn – fundamental characteristics on elongation/contraction and expansion rate,” Proc. of 2024 IEEE Int. Conf. on Advanced Intelligent Mechatronics (AIM), pp. 148-153, 2024. https://doi.org/10.1109/AIM55361.2024.10637060
- [25] T. Nakamura, “Experimental comparisons between McKibben type artificial muscles and straight fibers type artificial muscles,” Proc. of SPIE Int. Conf. on Smart Structures, Devices and Systems III, Vol.6414, Article No.641426, 2007. https://doi.org/10.1117/12.698845
- [26] H. Tomori and T. Nakamura, “Theoretical comparison of McKibben-type artificial muscle and novel straight-fiber-type artificial muscle,” Int. J. Automation Technol., Vol.5, No.4, pp. 544-550, 2011. https://doi.org/10.20965/ijat.2011.p0544
- [27] A. Kojima, M. Okui, I. Hisamichi, T. Tsuji, and T. Nakamura, “Straight-fiber-type artificial muscle deformation under pressurization,” IEEE Robot. Autom. Lett., Vol.4, Issue 3, pp. 2592-2598, 2019. https://doi.org/10.1109/LRA.2019.2902016
- [28] F. Ito, I. Horiuchi, K. Tsuru, and T. Nakamura, “Development of an earthworm-type electrical wire installation assistance robot using artificial muscles,” IEEE Robot. Autom. Lett., Vol.8, Issue 5, pp. 2999-3006, 2023. https://doi.org/10.1109/LRA.2023.3264725
- [29] K. Uchiyama, H. Sato, F. Ito, and T. Nakamura, “Antislip anchoring mechanism for peristaltic pipe inspection robots traveling in low-friction environments,” Proc. of 48th Annu. Conf. IEEE Ind. Electron. Soc., 2022. https://doi.org/10.1109/IECON49645.2022.9968391
- [30] T. Tomita, T. Tanaka, and T. Nakamura, “Development of a peristaltic crawling robot for long-distance sewer pipe inspection with consideration of complex pipe line,” Proc. of 2015 IEEE/RSJ Int. Conf. on Intell. Robots Syst. (IROS), pp. 2742-2747, 2015. https://doi.org/10.1109/IROS.2015.7353753
This article is published under a Creative Commons Attribution-NoDerivatives 4.0 Internationa License.