Paper:
Development of 2-DOF Manipulator Using Straight-Fiber-Type Pneumatic Artificial Muscle for Agriculture
Kosei Seno, Teppei Abe, and Hiroki Tomori

Department of Mechanical Systems Engineering, Graduate School of Science and Engineering, Yamagata University
4-3-16 Jonan, Yonezawa Yamagata 992-8510, Japan
Recently, Japan has been witnessing an increase in the average age of agricultural workers and a decrease in the number of new entrants into farming, both of which are progressing year by year due to the country’s declining birthrate and aging population. As a result, expectations for substitution by robots and human-robot collaboration are rising. Therefore, we propose a robot arm built using straight-fiber-type pneumatic artificial muscle (SF-PAM) and a noncircular pulley. SF-PAM is sealed and has no sliding parts; thus, it has excellent dustproof and waterproof properties and is suitable for work on farms. However, due to its structure, the SF-PAM has a nonlinear relationship between the contraction force and the amount of contraction, and the output torque is insufficient near the limit of its range of motion. As a solution to this problem, a noncircular pulley is introduced to compensate for the output torque and expand the range of motion. Based on this, this study aims to realize fruit harvesting operation using a robot arm. In this paper, a two-degree-of-freedom robot arm was developed, and position control experiments were conducted to verify the tracking with the target value. As a result, the mechanical equilibrium model of the wire-pulley mechanism was found to be valid for this robot arm. However, issues were found due to the arrangement of the SF-PAM and the shape of the noncircular pulley.
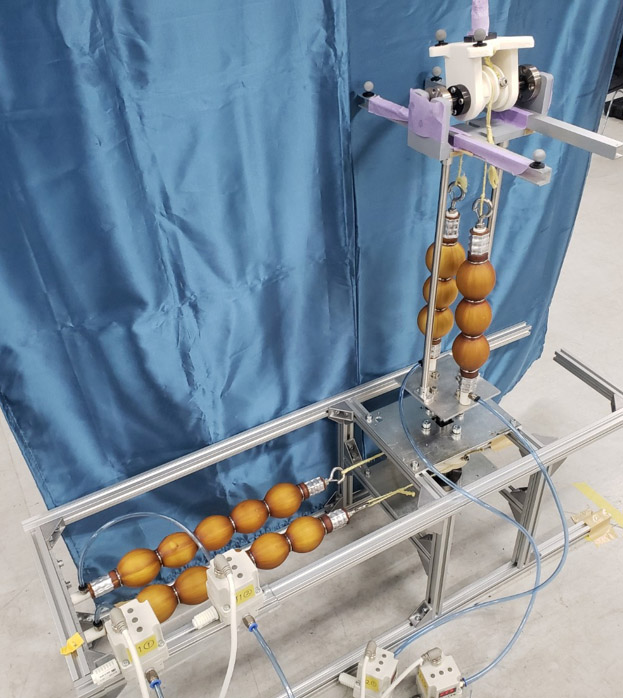
PAM manipulator with noncircular pulley
- [1] F.-H. Tseng, H.-H. Cho, and H.-T. Wu, “Applying big data for intelligent agriculture-based crop selection analysis,” IEEE Access, Vol.7, pp. 116965-116974, 2019. https://doi.org/10.1109/ACCESS.2019.2935564
- [2] M. Sekine, R. Kokubun, and W. Yu, “Investigating the effect of a mechanism combined with a speed-increasing gear and a pneumatic artificial muscle,” Actuators, Vol.7, Issue 2, Article No.22, 2018. https://doi.org/10.3390/act7020022
- [3] Y. Yang, Y. Wu, C. Li, X. Yang, and W. Chen, “Flexible actuators for soft robotics,” Advanced Intelligent Systems, Vol.2, Issue 1, 2019. https://doi.org/10.1002/aisy.201900077
- [4] D.-A. Zhao, J. Lv, W. Ji, Y. Zhang, and Y. Chen, “Design and control of an apple harvesting robot,” Biosystems Engineering, Vol.110, Issue 2, pp. 112-122, 2011. https://doi.org/10.1016/j.biosystemseng.2011.07.005
- [5] Y. Xiong, Y. Ge, L. Grimstad, and P. J. From, “An autonomous strawberry-harvesting robot: Design, development, integration, and field evaluation,” J. of Field Robotics, Vol.37, Issue 2, pp. 202-224, 2020. https://doi.org/10.1002/rob.21889
- [6] C. Ferraresi, W. Franco, and A. M. Bertetto, “Flexible pneumatic actuators: A comparison between the McKibben and the straight fibres muscles,” J. Robot. Mechatron., Vol.13, No.1, pp. 56-63, 2001. https://doi.org/10.20965/jrm.2001.p0056
- [7] B. Tondu, “Modelling of the McKibben artificial muscle: A review,” J. of Intelligent Material Systems and Structures, Vol.23, Issue 3, 2012. https://doi.org/10.1177/1045389X11435435
- [8] T. V. Minh, T. Tjahjowidodo, H. Ramon, and H. van Brussel, “Cascade position control of a single pneumatic artificial muscle-mass system with hysteresis compensation,” Mechatronics, Vol.20, Issue 3. pp. 402-414, 2010. https://doi.org/10.1016/j.mechatronics.2010.03.001
- [9] B. Ugurlu, P. Forni, C. Doppmann, E. Sariyildiz, and J. Morimoto, “Stable control of force, position, and stiffness for robot joints powered via pneumatic muscles,” IEEE Trans. on Industrial Informatics, Vol.15, Issue 12, pp. 6270-6279, 2019. https://doi.org/10.1109/TII.2019.2916228
- [10] S. Hirose, K. Ikuta, and K. Sato, “Development of a shape memory alloy actuator. Improvement of output performance by the introduction of a σ-mechanism,” Advanced Rovotics, Vol.3, Issue 2, pp. 89-108, 1988. https://doi.org/10.1163/156855389X00019
- [11] G. Endo, H. Yamada, A. Yajima, M. Ogata, and S. Hirose, “A passive weight compensation mechanism with a non-circular pulley and a spring,” 2010 IEEE Int. Conf. on Robotics and Automation, pp. 3843-3848, 2010. https://doi.org/10.1109/ROBOT.2010.5509797
- [12] D. Shin, X. Yeh, and O. Khatib, “Variable radius pulley design methodology for pneumatic artificial muscle-based antagonistic actuation systems,” 2011 IEEE/RSJ Int. Conf. on Intelligent Robotics and Systems, pp. 1830-1835, 2011. https://doi.org/10.1109/IROS.2011.6095180
- [13] D. Shin, X. Yeh, and O. Khatib, “Circular pulley versus variable radius pulley: Optimal design methodologies and dynamic characteristics analysis,” IEEE Tras. on Robotics, Vol.29, Issue 3, pp. 766-774, 2013. https://doi.org/10.1109/TRO.2013.2242374
- [14] R. Tanaka, T. Abe, and H. Tomori, “Application of noncircular pulleys to straight-fiber-type pneumatic artificial muscle manipulator,” J. Robot. Mechatron., Vol.35, No.3, pp. 622-632, 2023. https://doi.org/10.20965/jrm.2023.p0622
- [15] T. Nakamura and H. Shinohara, “Position and force control based on mathematical models of pneumatic artificial muscles reinforced by straight glass fibers,” Proc. 2007 IEEE Int. Conf. on Robotics and Automation, pp. 4361-4366, 2007. https://doi.org/10.1109/ROBOT.2007.364151
This article is published under a Creative Commons Attribution-NoDerivatives 4.0 Internationa License.