Paper:
Development of Automated Display Shelf System for New Purchasing Experience by Dynamic Product Layout Changes
Masashi Seki*
, Kazuyoshi Wada*
, and Tetsuo Tomizawa**
*Graduate School of Systems Design, Department of Mechanical Systems Engineering, Tokyo Metropolitan University
6-6 Asahigaoka, Hino, Tokyo 191-0065, Japan
**Department of Mechanical Engineering, National Institute of Technology, Tokyo College
1220-2 Kunugida-machi, Hachioji, Tokyo 193-0997, Japan
This study proposes a micro-logistics node as a new infrastructure envisioned for future convenience stores. This system automates the management of products on shelves, reduces the workload on store clerks, and provides an entirely new shopping experience with optimal displays based on the time and customers visiting the store. Automated warehouse technology has recently advanced, and the storage and removal of items from warehouse racks have been successfully automated. However, when considering implementation in convenience stores, robotic systems must adapt to their unique conditions: operation in limited backyard space, handling a wide variety of products with different sizes and shapes, and minimization of dead space in product displays. To address these challenges, this study developed a robot system that travels on vertical and horizontal tracks installed behind display shelves, and places products stored in special trays at any coordinate on the shelves.
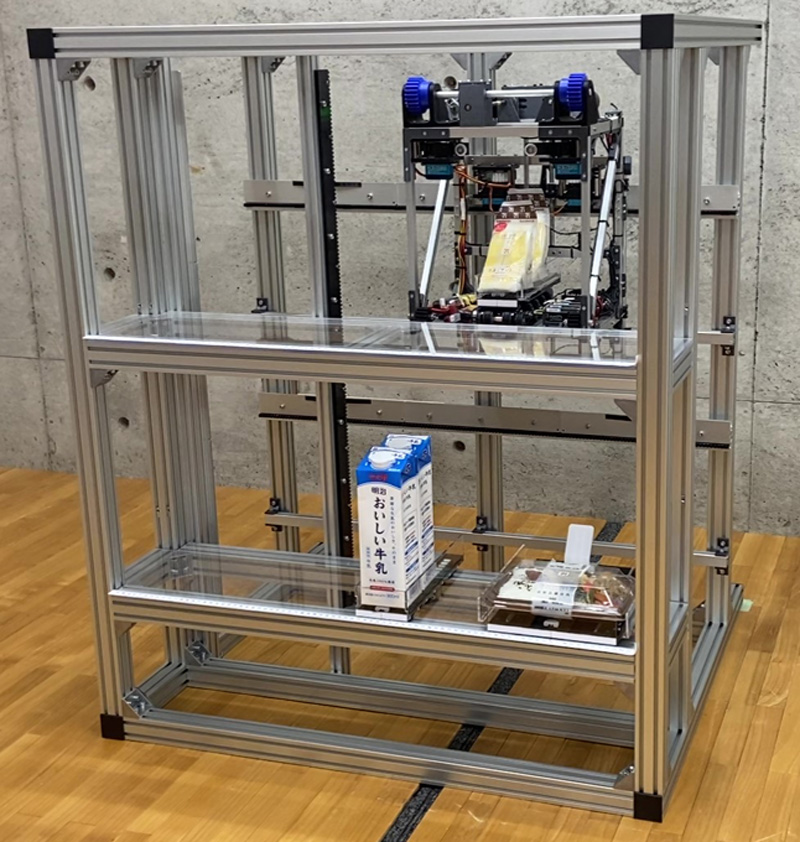
Automated display shelf for dynamic layouts
- [1] K. Miwa, “Study of Operation and Staff Scheduling in Retail Store,” J. Nagoya Gakuin University Social Sciences, Vol.51, No.4, pp. 143-158, 2015 (in Japanese).
- [2] Ministry of Economy, Trade and Industry, “Study Group on New Convenience Store—Third meeting: Survey report materials of user questionnaire and exit surveys,” 2022 (in Japanese).
- [3] R. Fukui, S. Kousaka, T. Sato, and M. Shimosaka, “Non-industrial stacker crane with compatibility/extensibility between manual operation and electrical driving,” IEEE/ASME Int. Conf. on Advanced Intelligent Mechatronics (AIM), pp. 383-390, 2012. https://doi.org/10.1109/AIM.2012.6265946
- [4] R. Fukui, T. Sunakawa, S. Kousaka, M. Watanabe, T. Sato, and M. Shimosaka, “TansuBot: A drawer-type storage system for supporting object search with contents’ photos and usage histories,” IEEE/RSJ Int. Conf. on Intelligent Robots and Systems, pp. 2703-2709, 2013. https://doi.org/10.1109/IROS.2013.6696738
- [5] J. Park, T. Nunogaki, and J. H. Lee, “The mechanical structure of mobile module for new self-configurable intelligent environment,” ROBOMECH J., Vol.2, Article No.14, 2015. https://doi.org/10.1186/s40648-015-0035-x
- [6] D. T. Tran, T. Satooka, and J. H. Lee, “Mobile module in reconfigurable intelligent space: Applications and a review of developed versions,” Int. J. of Advanced Computer Science and Applications, Vol.14, No.5, 2023. https://doi.org/10.14569/IJACSA.2023.01405116
- [7] R. Fukui, H. Morishita, T. Mori, and T. Sato, “HangBot: A ceiling mobile robot with robust locomotion under a large payload (Key mechanisms integration and performance experiments),” IEEE Int. Conf. on Robotics and Automation, pp. 4601-4607, 2011. https://doi.org/10.1007/978-3-642-28572-1_47
- [8] R. Fukui, Y. Yamada, K. Mitsudome, K. Sano, and S. I. Warisawa, “HanGrawler: Large-payload and high-speed ceiling mobile robot using crawler,” IEEE Trans. on Robotics, Vol.36, No.4, pp. 1053-1066, 2020. https://doi.org/10.1109/TRO.2020.2973100
- [9] R. Fukui, H. Morishita, T. Mori, and T. Sato, “Development of a home-use automated container storage/retrieval system,” IEEE/RSJ Int. Conf. on Intelligent Robots and Systems, pp. 2875-2882, 2008. https://doi.org/10.1109/IROS.2008.4650946
- [10] K. Yoshida, H. Toriyama, S. Warisawa, and R. Fukui, “Modularized robot machining system with scalability, portability and parallelism modular design for machine tool to proove concept and drilling experiment using a general purpose robot,” Trans. of the JSME, Vol.88, No.912, Article No.22-00107, 2022 (in Japanese). https://doi.org/10.1299/transjsme.22-00107
- [11] M. Vega-Heredia, R. E. Mohan, T. Y. Wen, J. Siti’Aisyah, A. Vengadesh, S. Ghanta, and S. Vinu, “Design and modelling of a modular window cleaning robot,” Automation in Construction, Vol.103, pp. 268-278, 2019. https://doi.org/10.1016/j.autcon.2019.01.025
- [12] V. H. Pham, H. C. Nguyen, N. D. Nguyen, B. N. Mach, and T. Q. Nguyen, “Design and simulation of a wall-climbing robot car using 3D printing technology and the vacuum method,” Advances in Mechanical Engineering, Vol.15, No.7, 2023. https://doi.org/10.1177/16878132231186277
- [13] P. Liang, X. Gao, Q. Zhang, R. Gao, M. Li, Y. Xu, and W. Zhu, “Design and stability analysis of a wall-climbing robot using propulsive force of propeller,” Symmetry, Vol.13, No.1, Article No.37, 2020. https://doi.org/10.3390/sym13010037
- [14] P. Liang, X. Gao, Q. Zhang, M. Li, R. Gao, and Y. Xu, “Analysis and experimental research on motion stability of wall-climbing robot with double propellers,” Advances in Mechanical Engineering, Vol.13, No.9, 2021. https://doi.org/10.1177/16878140211047726
- [15] R. Parween, T. Y. Wen, and M. R. Elara, “Design and development of a vertical propagation robot for inspection of flat and curved surfaces,” IEEE Access, Vol.9, pp. 26168-26176, 2020. https://doi.org/10.1109/ACCESS.2020.3039014
- [16] M. Zhang, J. Hardin, J. Cai, J. Brooks, and K. Green, “Self-organizing robot team (SORT): A multi-robot, wall climbing organizer-and-delivery system for living spaces,” Adaptive Environments Book Series, Springer, 2021.
- [17] D. Ge, Y. Tang, S. Ma, T. Matsuno, and C. Ren, “A pressing attachment approach for a wall-climbing robot utilizing passive suction cups,” Robotics, Vol.9, No.2, Article No.26, 2020. https://doi.org/10.3390/robotics9020026
- [18] N. Vangala, C. Varunav, J. Aravind, S. M. Yasin, and E. M. Raju, “Design and analysis of wall-climbing robot,” Proc. of the Second Int. Conf. on Emerging Trends in Engineering (ICETE2023), pp. 1077-1087, 2023. https://doi.org/10.2991/978-94-6463-252-1_108
- [19] A. Saito, K. Nagayama, Y. Homma, R. Aoyagi, K. Ito, T. Oomichi, S. Ashizawa, and F. Matsuno, “Multi-legged robot for 3-dimensional environments—Adaptive mechanism using flexible body and legs—,” Trans. of the Society of Instrument and Control Engineers, Vol.54, No.9, pp. 695-704, 2018 (in Japanese). https://doi.org/10.9746/sicetr.54.695
- [20] J. Wang, L. Huang, J. Yao, M. Liu, Y. Du, M. Zhao, Y. Shu, and D. Lu, “Weld seam tracking and detection robot based on artificial intelligence technology,” Sensors, Vol.23, No.15, Article No.6725, 2023. https://doi.org/10.3390/s23156725
- [21] W. Song, H. Jiang, T. Wang, D. Ji, and S. Zhu, “Design of permanent magnetic wheel-type adhesion-locomotion system for water-jetting wall-climbing robot,” Advances in Mechanical Engineering, Vol.10, No.7, 2018. https://doi.org/10.1177/1687814018787378
- [22] M. Zhang, X. Zhang, M. Li, J. Cao, and Z. Huang, “Optimization design and flexible detection method of a surface adaptation wall-climbing robot with multisensor integration for petrochemical tanks,” Sensors, Vol.20, No.22, Article No.6651, 2020. https://doi.org/10.3390/s20226651
- [23] R. Fukui, T. Mori, and T. Sato, “Measurement and control scheme for a container transfer robot in living space,” IEEE/ASME Int. Conf. on Advanced Intelligent Mechatronics, pp. 295-301, 2009. https://doi.org/10.1109/AIM.2009.5229997
- [24] N. Pedemonte, T. Rasheed, D. Marquez-Gamez, P. Long, É. Hocquard, F. Babin, C. Fouché, G. Caverot, A. Girin, and S. Caro, “FASTKIT: A mobile cable-driven parallel robot for logistics,” Advances in Robotics Research: From Lab to Market, pp. 141-163, 2020. https://doi.org/10.1007/978-3-030-22327-4_8
- [25] K. Iturralde, M. Feucht, D. Illner, R. Hu, W. Pan, T. Linner, T. Bock, I. Eskudero, M. Rodriguez, J. Gorrotxategi, J. B. Izard, J. Astudillo, J. Cavalcanti Santos, M. Gouttefarde, M. Fabritius, C. Martin, T. Henninge, S. M. Nornes, Y. Jacobsen, A. Pracucci, J. Cañada, J. D. Jimenez-Vicaria, R. Alonso, and L. Elia, “Cable-driven parallel robot for curtain wall module installation,” Automation in Construction, Vol.138, Article No.104235, 2022. https://doi.org/10.1016/j.autcon.2022.104235
- [26] S. Lessanibahri, P. Cardou, and S. Caro, “A cable-driven parallel robot with an embedded tilt-roll wrist,” J. of Mechanisms and Robotics, Vol.12, No.2, Article No.021107, 2020. https://doi.org/10.1115/1.4045937
- [27] M. Métillon, P. Cardou, K. Subrin, C. Charron, and S. Caro, “A cable-driven parallel robot with full-circle end-effector rotations,” J. of Mechanisms and Robotics, Vol.13, No.3, Article No.031017, 2021. https://doi.org/10.1115/1.4049631
- [28] H. Bui, H. A. Pierson, S. N. Pinkley, and K. M. Sullivan, “Toolpath planning for multi-gantry additive manufacturing,” IISE Trans., Vol.53, No.5, pp. 552-567, 2021. https://doi.org/10.1080/24725854.2020.1775915
- [29] S. Tezuka, K. Wada, A. Hori, N. Shinoki, T. Kariya, K. Ohi, T. Tomizawa, and T. Suzuki, “Development of a restroom cleaning system for convenience stores,” Advanced Robotics, Vol.36, No.23, pp. 1230-1240, 2022. https://doi.org/10.1080/01691864.2022.2130710
- [30] M. Seki, K. Wada, T. Teraguchi, and T. Tomizawa, “A robot hand with free-rotating grips for switching three different grasping modes,” Advanced Robotics, Vol.36, Nos.17-18, pp. 920-935, 2022. https://doi.org/10.1080/01691864.2022.2114298
- [31] T. Okayama, “Verification of the number of purchases related to the actual condition of food loss occurrence and suppression in convenience stores,” Taisho University J. of Human Environment, Vol.10, 2023 (in Japanese).
This article is published under a Creative Commons Attribution-NoDerivatives 4.0 Internationa License.