Paper:
Development of 3-USR Type Spatial 6-DOF Parallel Mechanism with Large Workspace—Proposal of 3-USR Mechanism and Design of Spherical 5-Link Mechanism to Replace Active Universal Pairs (U)—
Hayato Ishihara, Takumu Kikuchi, Masaru Higuchi
, Yuichi Nakazato
, and Kensuke Takita
Nippon Institute of Technology
4-1 Gakuendai, Miyashiro-machi, Minamisaitama-gun, Saitama 345-8501, Japan
In this paper, we present a 3-USR-type 6-degree-of-freedom (6-DOF) parallel mechanism characterized by an expansive workspace. This mechanism consists of three coupling chains, each comprising a universal pair (U), a spherical pair (S), and a rotational pair (R), in sequence from the stationary base. To achieve a large workspace, the three stationary universal pairs are designated as active pairs, with their rotational axes intersecting at a single point, thereby creating a hemispherical workspace akin to that of a serial mechanism. To implement the active universal pair within a parallel mechanism, we replaced the spherical 5-link mechanism, which originally featured two stationary active rotational pairs, with stationary active universal pairs, and conducted an inverse kinematics analysis. Subsequently, we assessed the expansive workspace of the spherical 5-link mechanism, a key factor influencing the working area of the 3-USR-type 6-DOF parallel mechanism, by examining its motion transmissibility. Based on this evaluation, we designed two compact mechanisms that provide a large workspace and allow for the configuration of all three rotational axes to intersect at a single point. We experimentally investigated the relationship between motion transmissibility and rigidity for these two types of spherical 5-link mechanisms, demonstrating that motion transmissibility can serve as an indicator of rigidity. Finally, a prototype of the 3-USR mechanism was fabricated.
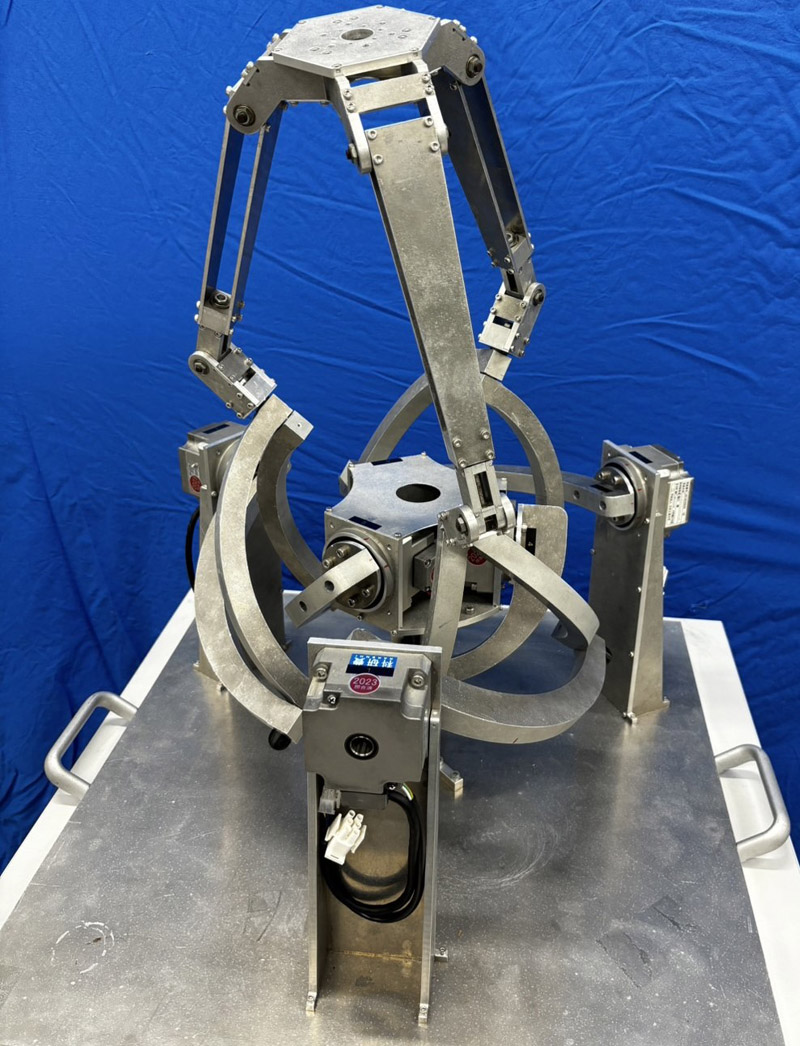
Prototype of 3-USR type spatial 6-DOF parallel mechanism
- [1] J. Arata, “Haptics application of parallel mechanisms,” J. of the Robotics Society of Japan, Vol.30, No.2, pp. 144-147, 2012 (in Japanese).
- [2] J. Arata, H. Kondo, and H. Fujimoto, “Development of a force presenter ‘DELTA-4’ using a parallel link mechanism,” J. of the Robotics Society of Japan, Vol.27, No.8, pp. 917-925, 2009 (in Japanese).
- [3] T. Harada, “Proposal of 2-arm 6-DOF parallel robot with kinematic redundancy and driving redundancy,” Proc. of JSME Annual Conf. on Robotics and Mechatronics (ROBOMEC), 2A2-B02, 2015 (in Japanese). https://doi.org/10.1299/jsmermd.2015._2A2-B02_1
- [4] H. Qin, A. Song, Y. Liu, G. Jiang, and B. Zhou, “Design and calibration of a new 6 DOF haptic device,” Sensors, Vol.15, No.12, pp. 31293-31313, 2015. https://doi.org/10.3390/s151229857
- [5] M. Vulliez, S. Zeghloul, and O. Khatib, “Design strategy and issues of the Delthaptic, a new 6-DOF parallel haptic device,” Mechanism and Machine Theory, Vol.128, pp. 395-411, 2018. https://doi.org/10.1016/j.mechmachtheory.2018.06.015
- [6] D. Chablat and P. Wenger, “A six degree-of-freedom haptic device based on the orthoglide and hybrid agile eye,” Proc. of ASME Int. Design Engineering Technical Conf., pp. 795-802, 2008. https://doi.org/10.1115/DETC2006-99065
- [7] M. Uchiyama, Y. Tsumaki, and W. Yoon, “Design of a compact 6-DOF haptic device to use parallel mechanisms,” Robotics Research, pp. 145-162, 2007. https://doi.org/10.1007/978-3-540-48113-3_14
- [8] Y. Takeda and H. Funahashi, “Development of a 6-DOF spatial parallel manipulator with excellent motion transfer: First report, extraction of mechanism constant region based on Monte Carlo method,” Trans. of the Japan Society of Mechanical Engineers, Series C, Vol.61, No.589, pp. 3781-3788, 1995 (in Japanese).
- [9] Y. Takeda, X. Xiao, K. Hirose, Y. Yoshida, and K. Ichiryu, “Kinematic analysis and design of 3-RPSR parallel mechanism with triple revolute joints on the base,” Int. J. Automation Technol., Vol.4, No.4, pp. 346-354, 2010. https://doi.org/10.20965/ijat.2010.p0346
- [10] X. Liang and Y. Takeda, “Transmission index of a class of parallel manipulators with 3-RS(SR) primary structures based on pressure angle and equivalent mechanism with 2-SS chains replacing RS chain,” Mech. Mach. Theory., Vol.139, pp. 359-378, 2019. https://doi.org/10.1016/j.mechmachtheory.2019.04.018
- [11] D. Stewart, “A platform with six degrees of freedom,” Proc. of the Institution of Mechanical Engineers, Vol.180, Issue 1, pp. 371-386, 1965. https://doi.org/10.1243/PIME_PROC_1965_180_029_02
- [12] S.-U. Lee and S. Kim, “Analysis and optimal design of a new 6 DOF parallel type haptic device,” Proc. of 2006 IEEE/RSJ Int. Conf. on Intelligent Robots and Systems, pp. 460-465, 2006. https://doi.org/10.1109/IROS.2006.282255
- [13] F. Gosselin, J.-P. Martins, C. Bidard, C. Andriot, and J. Brisset, “Design of a new parallel haptic device for desktop applications,” Proc. of First Joint Eurohaptics Conf. and Symp. on Haptic Interfaces for Virtual Environment and Teleoperator Systems. World Haptics Conf., pp. 189-194, 2005. https://doi.org/10.1109/WHC.2005.33
- [14] J. Yoon and J. Ryu, “Design, fabrication, and evaluation of a new haptic device using a parallel mechanism,” IEEE/ASME Trans. on Mechatronics, Vol.6, Issue 3, pp. 221-233, 2001. https://doi.org/10.1109/3516.951360
- [15] C. M. Gosselin and É. S. Pierre, “Development and experimentation of a fast 3-DOF camera-orienting device,” Int. J. of Robotic Research, Vol.16, Issue 5, pp. 619-630, 1997. https://doi.org/10.1177/027836499701600503
- [16] Y. Takeda, H. Funahashi, and Y. Sasaki, “Development of a 3-DOF spherical parallel mechanism with excellent working area and motion transfer,” Trans. of the JSME, Vol.579, No.94, pp. 404-410, 1994 (in Japanese).
- [17] H. Fukumaru, T. Takagi, and A. Hayashi, “Development of a multi-degree-of-freedom joint actuator with 3-DOF spherical mechanism,” Proc. of the 2019 Japan Society for Precision Engineering Fall Meeting, 2019 (in Japanese).
- [18] S. Huda and Y. Takeda, “Kinematic analysis and synthesis of a 3-URU pure rotational parallel mechanism with respect to singularity and workspace,” J. of Advanced Mechanical Design, Systems, and Manufacturing, Vol.1, Issue 1, pp. 81-92, 2007. https://doi.org/10.1299/jamdsm.1.81
- [19] K. Ueda, H. Yamada, H. Ishida, and S. Hirose, “Design of large motion range and heavy duty 2-DOF spherical parallel wrist mechanism,” J. Robot. Mechatron., Vol.25, No.2, pp. 294-305, 2013. https://doi.org/10.20965/jrm.2013.p0294
- [20] G. Wu, S. Caro, and J. Wang, “Design and transmission analysis of an asymmetrical spherical parallel manipulator,” Mechanism and Machine Theory, Vol.94, pp. 119-131, 2015. https://doi.org/10.1016/j.mechmachtheory.2015.07.012
- [21] X. Kong, “Forward displacement analysis and singularity analysis of a special 2-DOF 5R spherical parallel manipulator,” J. of Mechanisms and Robotics, Vol.3, No.2, Article No.024501, 2011. https://doi.org/10.1115/1.4003445
- [22] G. Palmieri, “On the positioning error of a 2-DOF spherical parallel wrist with flexible links and joints – An FEM approach,” Mech. Sci., Vol.6, Issue 1, pp. 9-14, 2015. https://doi.org/10.5194/ms-6-9-2015
- [23] Y. Takeda et al., “Development of a spherical in-parallel actuated mechanism with three degrees of freedom with large working space and high motion transmissibility: Evaluation of motion transmissibility and analysis of working space,” JSME Int. J. Series C, Vol.39, Issue 3, pp. 541-548, 1996. https://doi.org/10.1299/jsmec1993.39.541
- [24] T. Maeno, S. Yamamura, and M. Higuchi, “Design of 3-USR parallel mechanism with wide working area: Relationship between motion transferability of active universal joint and working area,” Proc. of JSME Conf. on Robotics and Mechatronics, 2P1-J11, 2022 (in Japanese).
This article is published under a Creative Commons Attribution-NoDerivatives 4.0 Internationa License.