Letter:
Investigation of the Possibility of High-Speed Motion of a Non-Pulley Musculoskeletal Robot
Tetsuya Morizono*
, Kotaro Furusawa*, and Hitoshi Kino**

*Fukuoka Institute of Technology
3-30-1 Wajiro-higashi, Higashi-ku, Fukuoka 811-0295, Japan
**Chukyo University
101-2 Yagoto Honmachi, Showa-ku, Nagoya, Aichi 466-8666, Japan
Robots with parallel-link structures are generally considered useful for achieving high-speed motion; however, they are typically large in size. Robot size can be reduced by using a serial-link structure. However, their moving parts, typically having a large mass or moment of inertia, are considered unsuitable for high-speed motion. High-speed motion performance can be improved by avoiding mounting actuators on the moving parts using some method to transmit the drive force or motion. In this letter, we propose a model in which a non-pulley musculoskeletal robot, previously studied by us, is modified to avoid mounting actuators on the movable parts. We demonstrate that the robot can be controlled to achieve the target posture using this modified model. We also discuss the feasibility of high-speed motion of a prototype robot using muscular forces computed for several motion patterns based on the minimum muscle-tension change model.
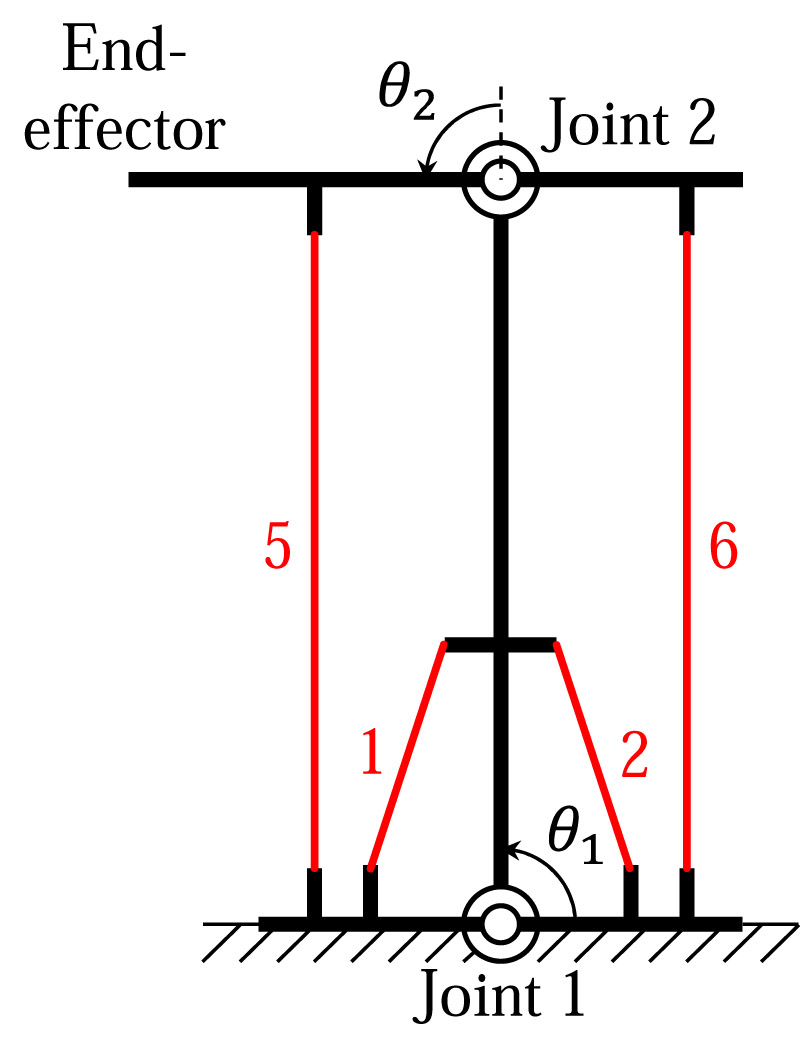
Two link robot model with four muscles
- [1] F. Pierrot, C. Reynaud, and A. Fournier, “DELTA: A simple and efficient parallel robot,” Robotica, Vol.8, pp. 105-109, 1990. https://doi.org/10.1017/S0263574700007669
- [2] E. P. Zehr and D. G. Sale, “Ballistic movement: Muscle activation and neuromuscular adaptation,” Can. J. Appl. Physiol., Vol.19, No.4, pp. 363-378, 1994. https://doi.org/10.1139/h94-030
- [3] G. Endo et al., “A Weight Compensation Mechanism with a Non-Circular Pulley and a Spring: Application to a Parallel Four-Bar Linkage Arm,” SICE J. Control, Measurement, and Syst. Integr., Vol.3, No.2, pp. 130-136, 2010. https://doi.org/10.9746/jcmsi.3.130
- [4] S. Ma et al., “Design and experiments for a coupled tendon-driven manipulator,” IEEE Control Syst. Mag., Vol.13, No.1, pp. 30-36, 1993. https://doi.org/10.1109/37.184790
- [5] Y. Shizume et al., “Enhancement of Control Stability Using Double Pulleys for Coupled Tendon-Driven Long-Reach Manipulator “Super Dragon”,” J. Robot. Mechatron., Vol.36, No.1, pp. 21-29, 2024. https://doi.org/10.20965/jrm.2024.p0021
- [6] H. Kino et al., “Numerical analysis of feedforward position control for non-pulley musculoskeletal system: A case study of muscular arrangement of a two-link planar system with six muscles,” Adv. Robot., Vol.27, No.16, pp. 1235-1248, 2013. https://doi.org/10.1080/01691864.2013.824133
- [7] M. Dornay et al., “Minimum Muscle-Tension Change Trajectories Predicted by Using a 17-Muscle Model of the Monkey’s Arm,” J. Mot. Behav., Vol.28, No.2, 1996. https://doi.org/10.1080/00222895.1996.9941736
- [8] H. Kino et al., “Sensorless Point-to-point Control for a Musculoskeletal Tendon-driven Manipulator: Analysis of a Two-DOF Planar System with Six Tendons,” Adv. Robot., Vol.31, No.16, pp. 851-864, 2017. https://doi.org/10.1080/01691864.2017.1372212
- [9] Y. Uno, M. Kawato, and R. Suzuki, “Formation and Control of Optimal Trajectory in Human Multijoint Arm Movement,” Biol. Cybern., Vol.61, No.2, pp. 89-101, 1989. https://doi.org/10.1007/BF00204593
- [10] F. Pierrot et al., “Optimal design of a 4-DOF parallel manipulator: From academia to industry,” IEEE T. Robot., Vol.25, No.2, pp. 213-224, 2009. https://doi.org/10.1109/TRO.2008.2011412
- [11] F. Xie and X.-J. Liu, “Design and development of a high-speed and high-rotation robot with four identical arms and a single platform,” J. Mech. Robot., Vol.7, No.4, Article No.041015, 2015. https://doi.org/10.1115/1.4029440
- [12] S. Briot, S. Caro, and C. Germain, “Design procedure for a fast and accurate parallel manipulator,” J. Mech. Robot., Vol.9, No.6, Article No.061012, 2017. https://doi.org/10.1115/1.4038009
This article is published under a Creative Commons Attribution-NoDerivatives 4.0 Internationa License.