Paper:
Characterization of Catheter-Type Tactile Sensor Using Polyvinylidene Fluoride (PVDF) Film
Kazuto Takashima*,**
, Souichiro Nagano*, Masahiro Watanabe*, and Kenji Ishida***

*Graduate School of Life Science and Systems Engineering, Kyushu Institute of Technology
2-4 Hibikino, Wakamatsu-ku, Kitakyushu, Fukuoka 808-0196, Japan
**Collaborative Research Center for Green Materials on Environmental Technology, Kyushu Institute of Technology
2-4 Hibikino, Wakamatsu-ku, Kitakyushu, Fukuoka 808-0196, Japan
***Department of Applied Quantum Physics and Nuclear Engineering, Faculty of Engineering, Kyushu University
744 Motooka, Nishi-ku, Fukuoka, Fukuoka 819-0395, Japan
To enable quantitative palpation in vivo, we previously developed a catheter-type tactile sensor with an outer diameter of 2 mm composed of a polyvinylidene fluoride (PVDF) film for minimally invasive surgery. However, our previous studies did not evaluate the effect of the PVDF film shape on the sensor output. In this study, we fabricated three types of prototype sensors with different PVDF film shapes and sizes using a simple cutting method. One of the films had the same shape as that used in one of our previous studies. We also prepared two types of PVDF film with a wide base and a narrow tip because we assumed that the deformation of the sensor gradually decreases from the root to the tip, similar to the first mode of the natural frequency. We evaluated the frequency response of the proposed sensors by vibrating the sensor tip and compared the results with the theoretical values. It was confirmed that the sensor output increased with PVDF film size. Although this tendency was observed for both the measured and theoretical values, the measured values were smaller than the theoretical values. Moreover, the effect of film size was larger than that of film shape. Improvements in the sensor structure and the theoretical equation and better evaluation methods are required in order to optimize the film shape and size.
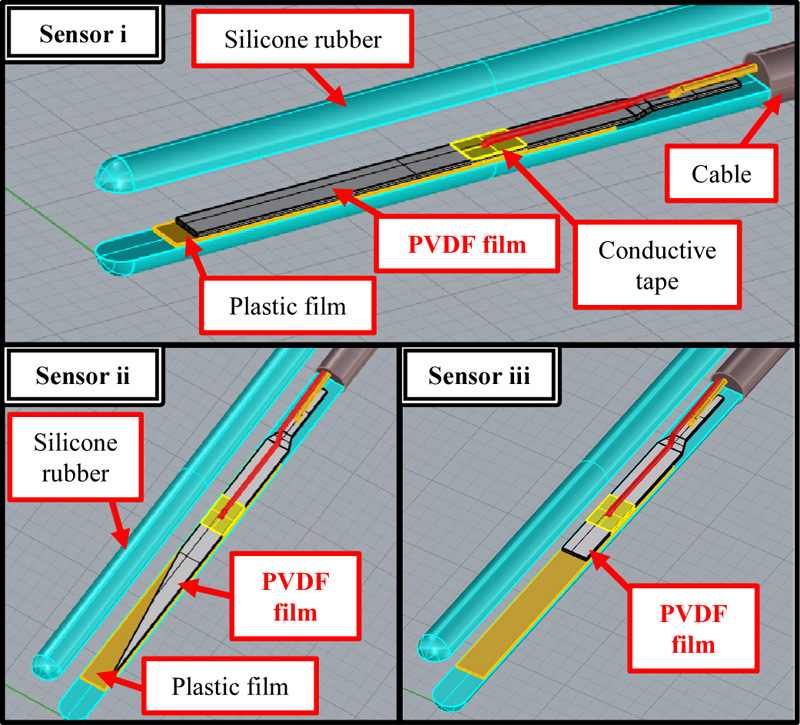
Prototype catheter-type tactile sensors
- [1] W. Othman et al., “Tactile sensing for minimally invasive surgery: Conventional methods and potential emerging tactile technologies,” Front. Robot. AI, Vol.8, Article No.705662, 2022. https://doi.org/10.3389/frobt.2021.705662
- [2] E. Sho et al., “Arterial enlargement in response to high flow requires early expression of matrix metalloproteinases to degrade extracellular matrix,” Exp. Mol. Pathol., Vol.73, No.2, pp. 142-153, 2002. https://doi.org/10.1006/exmp.2002.2457
- [3] K. Kitamura, H. Hasegawa, and H. Kanai, “Accurate estimation of carotid luminal surface roughness using ultrasonic radio-frequency echo,” Jpn. J. Appl. Phys., Vol.51, No.7S, Article No.07GF08, 2012. https://doi.org/10.1143/JJAP.51.07GF08
- [4] M. E. H. Eltaib and J. R. Hewit, “Tactile sensing technology for minimal access surgery—A review,” Mechatronics, Vol.13, No.10, pp. 1163-1177, 2003. https://doi.org/10.1016/S0957-4158(03)00048-5
- [5] B. Ren et al., “The critical technologies of vascular interventional robotic catheterization: A review,” IEEE Sens. J., Vol.23, No.24, pp. 30051-30069, 2023. https://doi.org/10.1109/JSEN.2023.3320356
- [6] M. Tanimoto et al., “Micro force sensor for intravascular neurosurgery and in vivo experiment,” Proc. of the 11th Annual Int. Workshop on Micro Electro Mechanical Systems (MEMS-98), pp. 504-509, 1998. https://doi.org/10.1109/MEMSYS.1998.659809
- [7] H. Takizawa, H. Tosaka, R. Ohta, S. Kaneko, and Y. Ueda, “Development of a microfine active bending catheter equipped with MIF tactile sensors,” Technical Digest. IEEE Int. MEMS 99 Conf., pp. 412-417, 1999. https://doi.org/10.1109/MEMSYS.1999.746864
- [8] Y. Haga, T. Mineta, and M. Esashi, “Active catheter, active guide wire and related sensor systems,” Proc. of the 5th Biannual World Automation Congress, pp. 291-296, 2002. https://doi.org/10.1109/WAC.2002.1049455
- [9] P. Polygerinos et al., “Novel miniature MRI-compatible fiber-optic force sensor for cardiac catheterization procedures,” 2010 IEEE Int. Conf. on Robotics and Automation, pp. 2598-2603, 2010. https://doi.org/10.1109/ROBOT.2010.5509416
- [10] T. Sekitani, U. Zschieschang, H. Klauk, and T. Someya, “Flexible organic transistors and circuits with extreme bending stability,” Nat. Mater., Vol.9, No.12, pp. 1015-1022, 2010. https://doi.org/10.1038/nmat2896
- [11] K. Takashima et al., “Measurement of the piezoelectric properties of vinylidene fluoride oligomer using pneumatic pressure for tactile sensors,” J. Solid Mech. Mater. Eng., Vol.6, No.10, pp. 975-988, 2012. https://doi.org/10.1299/jmmp.6.975
- [12] K. Takashima et al., “Development of catheter-type tactile sensor composed of polyvinylidene fluoride (PVDF) film,” ROBOMECH J., Vol.6, Article No.19, 2019. https://doi.org/10.1186/s40648-019-0147-9
- [13] K. Takashima, M. Watanabe, K. Inoue, S. Horie, and K. Ishida, “Fabrication and evaluation of catheter-type tactile sensor composed of two polyvinylidene fluoride films,” 2022 61st Annual Conf. of the Society of Instrument and Control Engineers (SICE), pp. 1165-1170, 2022. https://doi.org/10.23919/SICE56594.2022.9905774
- [14] T. Hayashi, N. Uchida, K. Nagayasu, H. Takahashi, and H. Nakamura, “Monitoring of structural vibration by using distributed PVDF film sensors,” Trans. Jpn. Soc. Mech. Eng., Ser. C, Vol.67, No.660, pp. 2565-2571, 2001 (in Japanese). https://doi.org/10.1299/kikaic.67.2565
- [15] N. Tanaka, Y. Kikushima, and M. Kuroda, “Design procedure of one-dimensional distributed parameter smart sensors,” Trans. Jpn. Soc. Mech. Eng., Ser. C, Vol.61, No.590, pp. 3923-3930, 1995 (in Japanese). https://doi.org/10.1299/kikaic.61.3923
- [16] R. Kikuuwe, K. Nakamura, and M. Yamamoto, “Finger-mounted tactile sensor for evaluating surfaces,” J. Robot. Mechatron., Vol.24, No.3, pp. 430-440, 2012. https://doi.org/10.20965/jrm.2012.p0430
- [17] I. Fujimoto, Y. Yamada, T. Maeno, T. Morizono, and Y. Umetani, “Identification of incipient slip phenomena based on the circuit output signals of PVDF film strips embedded in artificial finger ridges,” Trans. Soc. Instrum. Control Eng., Vol.40, No.6, pp. 648-655, 2004. https://doi.org/10.9746/sicetr1965.40.648
- [18] W. X. Feng, H. R. Wang, S. X. Guo, K. J. Wang, and X. F. Ye, “Design and experiments of a catheter side wall tactile sensor for minimum invasive surgery,” 2007 Int. Conf. on Mechatronics and Automation, pp. 1073-1078, 2007. https://doi.org/10.1109/ICMA.2007.4303697
- [19] Z. Chen, K.-Y. Kwon, and X. Tan, “Integrated IPMC/PVDF sensory actuator and its validation in feedback control,” Sens. Actuators A: Phys., Vol.144, No.2, pp. 231-241, 2008. https://doi.org/10.1016/j.sna.2008.01.023
- [20] M. Tanaka, “Sensor system for measuring human touch sensation,” J. Robot. Soc. Jpn., Vol.26, No.3, pp. 230-233, 2008 (in Japanese). https://doi.org/10.7210/jrsj.26.230
- [21] T. Okuyama, M. Sone, Y. Tanahashi, and M. Tanaka, “Palpation sensor using two PVDF films,” ICMIT 2009: Mechatronics and Information Technology (Proc. of SPIE, Vol.7500), Article No.75000J, 2010. https://doi.org/10.1117/12.858316
- [22] Z. Yi, Y. Zhang, and J. Peters, “Bioinspired tactile sensor for surface roughness discrimination,” Sens. Actuators A: Phys., Vol.255, pp. 46-53, 2017. https://doi.org/10.1016/j.sna.2016.12.021
- [23] X. L. Sun, J. P. Yan, Y. F. Li, and H. Liu, “Multi-frequency ultrasound transducers for medical applications: A survey,” Int. J. Intell. Robot. Appl., Vol.2, No.3, pp. 296-312, 2018. https://doi.org/10.1007/s41315-018-0057-7
- [24] K. Tsukagoshi, T. Hashimoto, and T. Koike, “Simultaneous measurement of swallowing sound and mechanomyogram of submental muscle with PVDF film,” 2018 40th Annual Int. Conf. of the IEEE Engineering in Medicine and Biology Society (EMIC), pp. 3310-3313, 2018. https://doi.org/10.1109/EMBC.2018.8512959
- [25] K. Takashima, S. Horie, T. Mukai, K. Ishida, and K. Matsushige, “Piezoelectric properties of vinylidene fluoride oligomer for use in medical tactile sensor applications,” Sens. Actuators A: Phys., Vol.144, No.1, pp. 90-96, 2008. https://doi.org/10.1016/j.sna.2008.01.015
- [26] Y. Yamamoto, K. Kure, T. Iwai, T. Kanda, and K. Suzumori, “Flexible displacement sensor using piezoelectric polymer for intelligent FMA,” 2007 IEEE/RSJ Int. Conf. on Intelligent Robots and Systems, pp. 765-770, 2007. https://doi.org/10.1109/IROS.2007.4399268
- [27] Y. Nagayama et al., “Multipoint detection of structural deformation of pulsating 3D heart model using flexible organic piezoelectric-sensor array,” Jpn. J. Appl. Phys., Vol.61, No.SE, Article No.SE1014, 2022. https://doi.org/10.35848/1347-4065/ac5a04
- [28] N. Durand et al., “Vinylidene fluoride telomers for piezoelectric devices,” Polym. J., Vol.43, No.2, pp. 171-179, 2011. https://doi.org/10.1038/pj.2010.102
- [29] S. Horii and T. Nakamura, “An in-pipe mobile robot for use as an industrial endoscope based on an earthworm’s peristaltic crawling,” J. Robot. Mechatron., Vol.24, No.6, pp. 1054-1062, 2012. https://doi.org/10.20965/jrm.2012.p1054
This article is published under a Creative Commons Attribution-NoDerivatives 4.0 Internationa License.