Paper:
Development of a Decommissioning Robot with a Simple Structure Capable of Traversing Steps Using Two Different Drive Systems
Riku Miura*, Seiya Tozaki*, Ibuki Mikado*, Toma Takei*, Shuichiro Ogake**, Kazuma Kobayashi*, Satoshi Mitsui*, Toshifumi Satake*, and Naoki Igo***

*National Institute of Technology, Asahikawa College
2-2-1-6 Shunkodai, Asahikawa, Hokkaido 071-8142, Japan
**Japan Advanced Institute of Science and Technology
1-1 Asahidai, Nomi, Ishikawa 923-1292, Japan
***Tokyo Information Design Professional University
2-7-1 Komatsugawa, Edogawa-ku, Tokyo 132-0034, Japan
In response to the imperative need for robotic involvement in the decommissioning of the Fukushima Daiichi Nuclear Power Plant, a proactive initiative was undertaken. This initiative led to the organization of the “7th Decommissioning Creative Robot Contest,” in which pivotal challenges related to nuclear plant decommissioning were addressed. Recognizing inaccessible areas within a decommissioned plant, the primary objective of this study was to develop a remotely operated robot capable of executing decontamination tasks in such environments. Two distinct locomotion systems were designed: mecanum wheels and crawlers. The mecanum wheels, characterized by their ability to execute approximately 100 mm vertical movements, facilitated the robot to surmount obstacles, particularly by negotiating 100 mm steps by engaging the tracks. Simultaneously, to address decontamination tasks at elevated locations, a threefold expandable ladder truck system was integrated, augmenting the operational range of the robot. Participation in the contest provided a platform for showcasing the developed technologies and validating their practicality. Despite encountering challenges during competition, such as damage to one locomotion system, the other locomotion system can be used to reach the destination. Experience serves as a crucial means of verifying technological advancements. Issues such as malfunctions in the range of motion control due to faulty limit switch contacts and unexpected loads on the tire elevation motors were noted, which hindered the achievement of the anticipated results. Despite these drawbacks, the adopted structural design demonstrates notable advantages, particularly in terms of maneuverability. The combination of mecanum wheels and crawlers along with a ladder truck system demonstrated adaptability to various scenarios. This adaptability holds significant promise for future nuclear power plant decontamination applications. While the competition may not have yielded the desired outcome, the lessons learned and the verified practicality of the developed technologies reinforce their potential utility in addressing the future challenges of nuclear plant decommissioning.
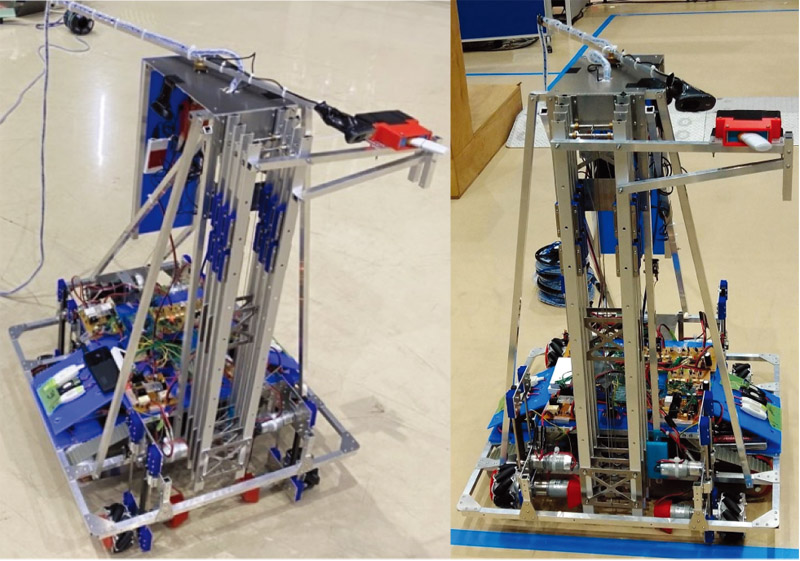
Decommissioning robot capable of traversing steps
- [1] S. Uchida, M. Naitoh, H. Suzuki, H. Okada, and S. Konishi, “Evaluation of Accumulated Fission Products in the Contaminated Water at the Fukushima Daiichi Nuclear Power Plant,” Nuclear Technology, Vol.188, Issue 3, pp. 252-265, 2014. https://doi.org/10.13182/NT13-152
- [2] S. Okada, K. Hirano, R. Kobayashi, and Y. Kometani, “Development and Application of Robotics for Decommissioning of Fukushima Daiichi Nuclear Power Plant,” Hitachi Rev., Vol.69, No.4, pp. 556-557, 2020.
- [3] T. Kotoku, “Robot Challenges for Nuclear Decommissioning of Fukushima Daiichi Power Station,” Proc. of the Int. Conf. on Advancing the Global Implementation of Decommissioning and Environmental Remediation Programmes, 4A(1), 2016.
- [4] K. Nagatani, S. Kiribayashi, Y. Okada, K. Otake, K. Yoshida, S. Tadokoro, and S. Kawatsuma, “Emergency Response to the Nuclear Accident at the Fukushima Daiichi Nuclear Power Plants Using Mobile Rescue Robots,” J. of Field Robotics, Vol.30, Issue 1, pp. 44-63, 2013. https://doi.org/10.1002/rob.21439
- [5] V. Michal, “Remote Operation and Robotics Technologies in Nuclear Decommissioning Projects,” Nuclear Decommissioning, Vol.1, pp. 346-374, 2012. https://doi.org/10.1533/9780857095336.2.346
- [6] T. Yoshida, K. Nagatani, S. Tadokoro, T. Nishimura, and E. Koyanagi, “Improvements to the Rescue Robot Quince Toward Future Indoor Surveillance Missions in the Fukushima Daiichi Nuclear Power Plant,” Proc. of the 8th Int. Conf. on Field and Service Robotics, pp. 19-32, 2014. https://doi.org/10.1007/978-3-642-40686-7_2
- [7] J. Ma, J. Luo, H. Pu, Y. Peng, S. Xie, and J. Gu, “Design, Simulation and Manufacturing of a Tracked Robot for Nuclear Accidents,” 2014 IEEE Int. Conf. on Robotics and Biomimetics (Robio 2014), pp. 1828-1833, 2014. https://doi.org/10.1109/ROBIO.2014.7090601
- [8] M. Totani, N. Sato, and Y. Morita, “Step Climbing Method for Crawler Type Rescue Robot Using Reinforcement Learning With Proximal Policy Optimization,” 2019 12th Int. Workshop on Robot Motion and Control (RoMoCo), pp. 154-159, 2019. https://doi.org/10.1109/RoMoCo.2019.8787360
- [9] H. Shin, C. H. Kim, Y. C. Seo, H. S. Eom, Y. Choi, and M. Kim, “Aerial Working Environment Monitoring Robot in High Radiation Area,” 2014 14th Int. Conf. on Control, Automation and Systems (ICCAS 2014), pp. 474-478, 2014. https://doi.org/10.1109/ICCAS.2014.6988048
- [10] H. Shin, S. H. Jung, Y. R. Choi, and C. Kim, “Development of a Shared Remote Control Robot for Aerial Work in Nuclear Power Plants,” Nuclear Engineering and Technology, Vol.50, Issue 4, pp. 613-618, 2018. https://doi.org/10.1016/j.net.2018.03.006
- [11] K. Fujita, K. Koike, and T. Koseki, “Motion and Vibration of the Lift Mechanism of a Ladder Truck,” Proc. of the 6th Int. Conf. on Motion and Vibration Control, pp. 508-513, 2002. https://doi.org/10.1299/jsmeintmovic.6.1.508
- [12] M. J. Bakari, K. M. Zied, and D. W. Seward, “Development of a Multi-Arm Mobile Robot for Nuclear Decommissioning Tasks,” Int. J. of Advanced Robotic Systems, Vol.4, Issue 4, 2007. https://doi.org/10.5772/5665
- [13] K. Kawabata, “Toward Technological Contributions to Remote Operations in the Decommissioning of the Fukushima Daiichi Nuclear Power Station,” The Japan Society of Applied Physics, Vol.59, No.5, Article No.050501, 2020. https://doi.org/10.35848/1347-4065/ab82ad
- [14] O. Roesch and H. Roth, “Remote Control of Mechatronic Systems Over Communication Networks,” IEEE Int. Conf. Mechatronics and Automation, pp. 1648-1653, 2005. https://doi.org/10.1109/ICMA.2005.1626802
- [15] S. Sato, T. Maegawa, K. Yoshimatsu, K. Sato, A. Nonaka, K. Takakura, and C. Konno, “Development of a Low Activation Concrete Shielding Wall by Multi-Layered Structure for a Fusion Reactor,” J. of Nuclear Materials, Vol.417, Issues 1-3, pp. 1131-1134, 2011. https://doi.org/10.1016/j.jnucmat.2010.12.302
This article is published under a Creative Commons Attribution-NoDerivatives 4.0 Internationa License.