Paper:
Development of High Dynamic Range Six-Axis Force Sensor with Simple Structure
Takamasa Kawahara and Toshiaki Tsuji

Department of Electrical Engineering, Electronics, and Applied Physics, Saitama University
255 Shimo-Ohkubo, Sakura-ku, Saitama 338-8570, Japan
We propose a six-axis force sensor with a simple structure that can measure small forces while affording a high load capacity. For a robot to perform complex motions in an unknown environment, the force sensor used must exhibit a high resolution and high load rating. Various studies have been conducted to simultaneously satisfy these two requirements. However, the high processing cost due to the complicated sensor structure is problematic. Therefore, we develop a column-type high dynamic range (HDR) six-axis force sensor using two types of strain gauges. The sensor was composed of a drawn pipe to solve structural problems that arise during manufacturing. By attaching strain gauges to the surface of the drawn pipe, the forces and torques in the six axes can be measured. HDR measurement was realizable using a semiconductor strain gauge for small loads and a metallic foil strain gauge for large loads. Based on the simulation results, the rated loads of the sensor were 1400 N in the Fx and Fy directions, 9000 N in the Fz direction, and 120 Nm in the Mx, My, and Mz directions. The performance of the fabricated force sensor was evaluated. The maximum nonlinearity errors of the semiconductor strain gauge and the metallic foil strain gauges were 1.21% and 1.81%, respectively. In addition, when comparing the S/N ratios, the minimum measurable values were 0.035 N and 0.13 N for Fy and Fz, respectively.
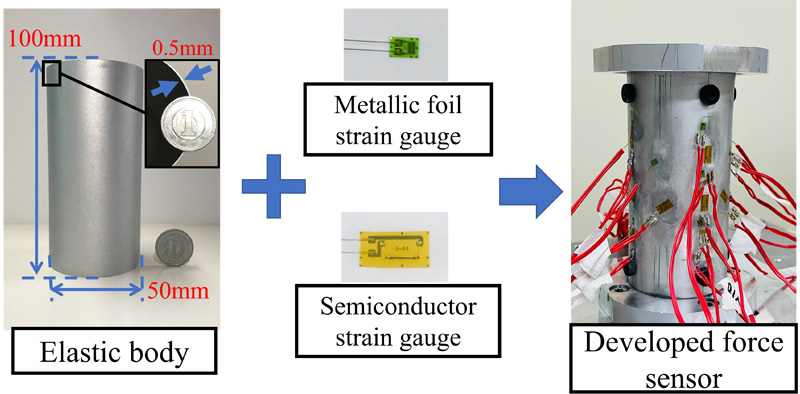
Column-type HDR six-axis force sensor
- [1] W. Schwalb et al., “A force-sensing surgical tool with a proximally located force/torque sensor,” Int. J. Med. Robot. Comput. Assist. Surg., Vol.13, No.3, 2017. https://doi.org/10.1002/rcs.1737
- [2] C.-Y. Lin et al., “Real-Time Robot Pose Correction on Curved Surface Employing 6-Axis Force/Torque Sensor,” IEEE Access, Vol.10, pp. 90149-90162, 2022. https://doi.org/10.1109/ACCESS.2022.3201233
- [3] M. Oikawa et al., “Reinforcement Learning for Robotic Assembly Using Non-Diagonal Stiffness Matrix,” IEEE Robot. Autom. Lett. (RAL), Vol.6, No.2, pp. 2737-2744, 2021. https://doi.org/10.1109/LRA.2021.3060389
- [4] T. Tsumugiwa et al., “Development of mechanical-impedance-varying mechanism in admittance control,” J. Robot. Mechatron., Vol.30, No.6, pp. 863-872, 2018.
- [5] S. Weng et al., “Design of an overload protection device for six-axis force/torque sensors,” IEEE Int. Conf. on Real-time Computing and Robot. (RCAR), pp. 239-242, 2016. https://doi.org/10.1109/RCAR.2016.7784032
- [6] L. Fu et al., “A Polyetheretherketone Six-Axis Force/Torque Sensor,” IEEE Access, Vol.7, pp. 105391-105401, 2019. https://doi.org/10.1109/ACCESS.2019.2932387
- [7] J. Yao et al., “A heavy load miniature six-component force sensing mechanism with hybrid branches,” Measurement, Vol.157, Article No.107623, 2020. https://doi.org/10.1016/j.measurement.2020.107623
- [8] D.-H. Lee et al., “A Capacitive-Type Novel Six-Axis Force/Torque Sensor for Robotic Applications,” IEEE Sensors J., Vol.16, No.8, pp. 2290-2299, 2016. https://doi.org/10.1109/JSEN.2015.2504267
- [9] S. Somlor et al., “Development of a capacitive-type 6-axis force-torque sensor,” IEEE SENSORS, pp. 1-3, 2017. https://doi.org/10.1109/ICSENS.2017.8234153
- [10] S. Aoyagi et al., “Multiaxis capacitive force sensor and its measurement principle using neural networks,” J. Robot. Mechatron., Vol.18, No.4, pp. 442-449, 2006.
- [11] G. Palli et al., “Development of an optoelectronic 6-axis force/torque sensor for robotic applications,” Sensors and Actuators A: Physical, Vol.220, pp. 333-346, 2014. https://doi.org/10.1016/j.sna.2014.09.023
- [12] Y. Sun et al., “Design and optimization of a novel six-axis force/torque sensor for space robot,” Measurement, Vol.65, pp. 135-148, 2015. https://doi.org/10.1016/j.measurement.2015.01.005
- [13] F. Arai et al., “Improvement of the measurement range and temperature characteristics of a load sensor using a quartz crystal resonator with all crystal layer components,” Sensors, Vol.17, No.5, 2017. https://doi.org/10.3390/s17051067
- [14] łabelokumura D. Okumura et al., “High Dynamic Range Sensing by a Multistage Six-Axis Force Sensor with Stopper Mechanism,” IEEE Int. Conf. Robot. Autom. (ICRA), pp. 4065-4070, 2018. https://doi.org/10.1109/ICRA.2018.8460571
- [15] R. Tamura et al., “High Dynamic Range 6-Axis Force Sensor Employing a Semiconductor-Metallic Foil Strain Gauge Combination,” IEEE Robot. Autom. Lett. (RAL), Vol.6, No.4, pp. 6243-6249, 2021. https://doi.org/10.1109/LRA.2021.3093008
- [16] łabelentou J. H. Kim et al., “Design and analysis of a column type multi-component force/moment sensor,” Measurement, Vol.33, No.3 pp. 213-219, 2003. https://doi.org/10.1016/S0263-2241(02)00044-1
- [17] I. Payo et al., “Six-Axis Column-Type Force and Moment Sensor for Robotic Applications,” IEEE Sensors J., Vol.18, No.17, pp. 6996-7004, 2018. https://doi.org/10.1109/JSEN.2018.2853561
- [18] D. Okumura et al., “Miniaturization of multistage high dynamic range six-axis force sensor composed of resin material,” Proc. Int. Conf. Robot. Autom. (ICRA), pp. 4297-4302, 2019.
- [19] B. W. Byrne et al., “Investigating 6 degree-of-freedom loading on shallow foundations,” Proc. Int. Symposium of Frontiers in Offshore Geotechnics (ISFOG), pp. 477-482, 2005.
- [20] M. Siddhpura et al., “A review of chatter vibration research in turning,” Int. J. of Machine Tools and Manufacture, Vol.61, pp. 27-47, 2012. https://doi.org/10.1016/j.ijmachtools.2012.05.007
- [21] M. Y. Cao et al., “Six-Axis Force/Torque Sensors for Robotics Applications: A Review,” IEEE Sensors J., Vol.21, No.24, pp. 27238-27251, 2021. https://doi.org/10.1109/JSEN.2021.3123638
This article is published under a Creative Commons Attribution-NoDerivatives 4.0 Internationa License.