Paper:
Multifunctional Shelf and Magnetic Marker for Stock and Disposal Tasks in Convenience Stores
Tomohito Takubo, Takeshi Nakamura, Riko Sugiyama, and Atsushi Ueno
Osaka Metropolitan University
3-3-138 Sugimoto, Sumiyoshi-ku, Osaka 558-8585, Japan
Product management using a multifunctional shelf, and manipulation using an electromagnet hand and a magnetic marker, are proposed for stock and disposal tasks. The multifunctional shelf manages the type, position, and number of products on the shelf, and plans display and disposal operations. The shelf provides directions to a mobile manipulator for moving products on the shelf according to the display and disposal plan. The proposed multifunctional shelf has a camera on each level that helps the mobile manipulator recognize the product. By optimizing the movement of products, the display and disposal work can be performed much more efficiently. To quickly grasp the product, a new manipulation strategy using a magnetic marker and an electromagnet hand is proposed. The electromagnet hand has two electromagnets and can quickly grasp and release the magnet marker by changing the S/N pole pair. Experiments using the proposed multifunctional shelf and electromagnet hand were conducted to demonstrate the effectiveness of the proposed system.
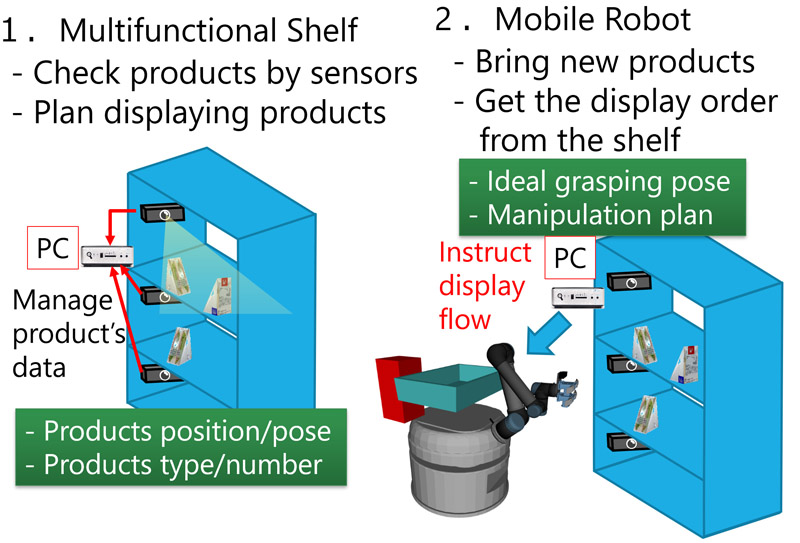
Cooperative task execution using multifunctional shelf and mobile manipulator
- [1] K. Wada, M. Niitsuma, S. Nakamura, and K. Ohara, “Workshop on Future Convenience Store Challenge,” Int. Symposium on System Integration 2021 (SII2021), WS01, 2021.
- [2] T. Wakayama, G. A. Garcia Ricardez, L. E. Hafi, and J. Takamatsu, “6D-Pose Estimation for Manipulation in Retail Robotics using the Inference-embedded OAK-D Camera,” 2022 IEEE/SICE Int. Symposium on System Integration (SII), WeBT3.1, 2022.
- [3] P. M. Uriguen Eljuri, G. A. Garcia Ricardez, N. Koganti, J. Takamatsu, and T. Ogasawara, “Combining a Monte Carlo Tree Search and a Feasibility Database to Plan and Execute Rearranging Tasks,” IEEE Access, Vol.9, pp. 21721-21734, 2021.
- [4] Y. Labbe, S. Zagoruyko, I. Kalevatykh, I. Laptev, J. Carpentier, M. Aubry, and J. Sivic, “Monte-Carlo Tree Search for Efficient Visually Guided Rearrangement Planning,” IEEE Robotics and Automation Letters, Vol.5, Issue 2, pp. 3715-3722, 2020.
- [5] A. Krontiris and K. E. Bekris, “Efficiently Solving General Rearrangement Tasks: A Fast Extension Primitive for an Incremental Sampling-based Planner,” IEEE Int. Conf. on Robotics and Automation (ICRA), pp. 3924-3931, 2016.
- [6] R. Wang, K. Gao, D. Nakhimovich, J. Yu, and K. E. Bekris, “Uniform Object Rearrangement: From Complete Monotone Primitives to Efficient Non-Monotone Informed Search,” IEEE Int. Conf. on Robotics and Automation (ICRA 2021), 2021.
- [7] R. Sakai, S. Katsumata et al., “A Mobile Dual-Arm Manipulation Robot System for Stocking and Disposing of Items in a Convenience Store by Using Universal Vacuum Grippers for Grasping Items,” Advanced Robotics, Vol.34, Issue 3-4, pp. 219-234, 2020.
- [8] J. Tanaka, D. Yamamoto, H. Ogawa et al., “Portable compact suction pad unit for parallel grippers,” Advanced Robotics, Vol.34, Issue 3-4, pp. 202-218, 2020.
- [9] J. Shintake, V. Cacucciolo, D. Floreano et al., “Soft robotic grippers,” Advanced Materials, Vol.30, Issue 29, 2018.
- [10] J. Tanaka, A. Sugahara, and H. Ogawa, “Four-Fingered Robot Hand with Mechanism to Change the Direction of Movement,” J. Robot. Mechatron., Vol.30, No.4, pp. 624-637, 2018.
- [11] J. Tanaka, “Three-Fingered Robot Hand with Gripping Force Generating Mechanism Using Small Gas Springs,” J. Robot. Mechatron., Vol.31, No.1, pp. 118-134, 2019.
- [12] S. Hasegawa, K. Wada, K. Okada, and M. Inaba, “A Three-Fingered Hand with a Suction Gripping System for Warehouse Automation,” J. Robot. Mechatron., Vol.31, No.2, pp. 289-304, 2019.
- [13] T. Ario and I. Mizuuchi, “Planning the Shortest Carrying Trajectory Including Path and Attitude Change Considering Gripping Constraints,” J. Robot. Mechatron., Vol.34, No.3, pp. 607-614, 2022.
- [14] K. Fujita and T. Tasaki, “Improving the Success Rate of Pose Estimation of Objects by Image Translation for Product Display,” The 33rd 2022 Int. Symposium on Micro-NanoMechatronics and Human Science (MHS2022), TP2-2-3, 2022.
- [15] G. Álvarez-Narciandi, A. Motroni, M. R. Pino, A. Buffi, and P. Nepa, “A UHF-RFID gate control system based on a Convolutional Neural Network,” 2019 IEEE Int. Conf. on RFID Technology and Applications (RFID-TA), pp. 353-356, 2019.
- [16] E. Miyake, T. Takubo, and A. Ueno, “3D Pose Estimation for the Object with Knowing Color Symbol by Using Correspondence Grouping Algorithm,” 2020 IEEE/SICE Int. Symposium on System Integration (SII2020), TuTB.1, 2020.
This article is published under a Creative Commons Attribution-NoDerivatives 4.0 Internationa License.