Development Report:
Design and Manufacture of a New Debris Retrieval Robot
Yohei Kobayashi, Ryotaro Kayawake, Keito Sagane, Kazuaki Murai, and Yasuo Utsumi
National Institute of Technology, Maizuru College
234 Shiroya, Maizuru, Kyoto 625-8511, Japan
This is a report on the No.2 debris retrieval robot that has been developed. While unit 1 was a machine built to demonstrate basic ideas, such as the arm mechanism, the robot that was designed and manufactured this time was developed with an emphasis on its structure and the functions that can be used at the decommissioning site. Only the ideas of a crawler that can run through a thin pipe and a telescopic arm mechanism to access debris were carried over from unit 1; all other parts for debris retrieval robot No.2 were redesigned. The crawler was made from metal with significantly increased rigidity to improve the running performance of the robot. In addition, to improve maneuverability, an omnidirectional camera unit was installed. As the view of this camera is not limited to the direction of travel of the robot, it makes it possible for the operator to have a better grasp of situations that the robot may encounter. The debris collection mechanism was changed to a more reliable mechanism that is not affected by the shape of the debris. The arm expansion and contraction mechanisms were also changed to a more reliable structure.
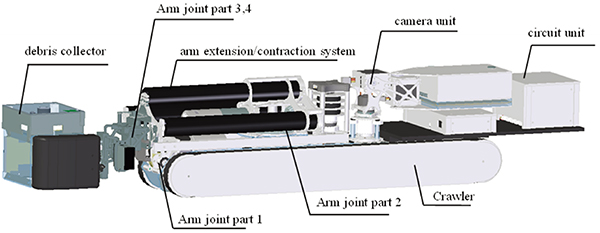
Designed debris retrieval robot
- [1] O. Seki, “Current Status of D&R for Fuel Debris Retrieval to Proceed with Decommissioning of the Fukushima Daiichi NPS – Outline of D&R Conducted by International Research Institute for Nuclear Decommissioning (IRID) –,” Decommissioning Technical Report, J. of the RANDEC, pp. 29-45, 2017 (in Japanese).
- [2] S. Suzuki, “Human Resource Development Through the Creative Robot Contest for Decommissioning,” J. of the Robotics Society of Japan, Vol.36, No.7, pp. 483-486, 2018 (in Japanese).
- [3] T. Doi and S. Suzuki, “Summary of the third HIRO creative RoboCon and characteristics of the robots participating in that – Application of high mobility mechanism with passive wheels unit –,” Proc. of JSME Annual Conf. on Robotics and Mechatronics (Robomec), 2P2-M07, 2019.
- [4] S. Kino, E. Takada, S. Suzuki, Y. Ohta, and T. Suzuki, “Education for human resource development in the nuclear field in National Institute of Technology,” J. of the Atomic Energy Society of Japan, Vol.57, No.9, pp. 612-615, 2015 (in Japanese).
- [5] H. Asama, “Remote technology for decommissioning of Fukushima Daiichi Nuclear Power Station,” J. of the Atomic Energy Society of Japan, Vol.62, No.3, pp. 125-126, 2020.
- [6] S. Onitsuka, “Present status of Fukushima Daiichi Nuclear power plant decommissioning,” J. of the Atomic Energy Society of Japan, Vol.62, No.3, pp. 121-124, 2020 (in Japanese).
- [7] S. Sato, T. Song, and Y. Aiyama, “Development of Tele-Operated Underfloor Mobile Manipulator,” J. Robot. Mechatron., Vol.33, No.6, pp. 1398-1407, 2021.
- [8] K. Suzuki and K. Kawabata, “Development of a Robot Simulator for Decommissioning Tasks Utilizing Remotely Operated Robots,” J. Robot. Mechatron., Vol.32, No.6, pp. 1292-1300, 2020.
- [9] R. Fukui, G. Kanayama, Y. Kato, R. Takahashi, and S. Warisawa, “Development of an Intersection Module for a Modularized Rail Structure – Implementation of Compliant Mechanisms for a Replacing Task of Movable Parts –,” J. Robot. Mechatron., Vol.30, No.3, pp. 467-476, 2018.
- [10] R. Fukui, K. Kawae, Y. Kato, and M. Nakao, “Rail Structure Supporting Mechanism Using Foamable Resin for Pillar Expansion, Anchoring, and Fixation,” J. Robot. Mechatron., Vol.28, No.2, pp. 129-137, 2016.
This article is published under a Creative Commons Attribution-NoDerivatives 4.0 Internationa License.