Development Report:
Development of Multi-Articulated Tracked Vehicle with a Sensorless Salvaging Bucket for Decommissioning
Junji Hirasawa, Shun Isobe, Yusuke Kuramochi, Mitsuhiro Nishino, and Yoshihisa Nihei
National Institute of Technology, Ibaraki College
866 Nakane, Hitachinaka-shi, Ibaraki 312-0011, Japan
In this paper, we describe a prototypical crawler vehicle developed for “Hairo Sozo Robocon,” i.e., the 4th creative robot contest for decommissioning conducted in 2019. The rules of this robot contest required a high turning ability on a flat floor and high mobility through the inner space of a pipe. In addition, the robot needed to salvage objects from a floor placed 3.2 meters underneath itself. We developed a multi-articulated tracked vehicle to provide high mobility in both contexts. The vehicle was equipped with a sensorless salvaging bucket inspired by a traditional sampler sounding weight.
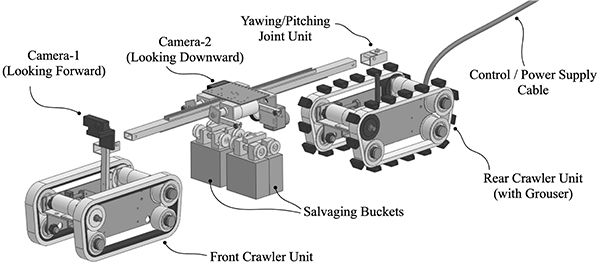
Outline of developed test vehicle “Debris Hunter I”
- [1] H. Kondo, K. Sato, and N. Sugiyama, “Practical Analysis of Turning Resistance of the Tracked Vehicle,” J. of the Japanese Society Agricultural Machinery, Vol.50, No.2, pp. 19-25, 1988 (in Japanese).
- [2] N. Ito, K. Kito, and J. Bai, “Evaluation of Turnability for Tracked Vehicle (Part 1) – Comparison Between Spin and Pivot Turn Systems –,” J. of the Japanese Society Agricultural Machinery, Vol.56, No.6, pp. 11-16, 1994 (in Japanese).
- [3] Desrial and N. Ito, “Theoretical Model for the Estimation of Turning Motion Resistance for the Tracked Vehicle,” J. of the Japanese Society Agricultural Machinery, Vol.61, No.6, pp. 169-178, 1999.
- [4] J. Hirasawa and T. Kimura, “Development of stair-climbing mechanism with passive crawlers (analysis of limitation for crawler rotation angle and test vehicle performance),” Trans. of the JSME, Vol.82, No.834, doi: 10.1299/transjsme.15-00357, 2016 (in Japanese).
- [5] J. Hirasawa, “Improvement of the Mobility on the Step-Field for a Stair Climbable Mobile Robot with Passive Crawlers,” J. Robot. Mechatron., Vol.32, No.4, pp. 780-788, 2020.
- [6] A. M. Bertetto and M. Ruggiu, “Low Cost Pipe-Crawling Pneumatic Robot,” J. Robot. Mechatron., Vol.14, No.4, pp. 400-407, 2002.
- [7] S. Wakimoto, K. Suzumori, M. Takata, and J. Nakajima, “In-Pipe Inspection Micro Robot Adaptable to Changes in Pipe Diameter,” J. Robot. Mechatron., Vol.15, No.6, pp. 609-615, 2003.
- [8] T. Yanagida, K. Adachi, and T. Nakamura, “Development of Bellows-Type Artificial Rubber Muscle and Application to Peristaltic Crawling Endoscopic Robot,” J. Robot. Mechatron., Vol.25, No.4, pp. 748-754, 2013.
- [9] T. Nishimura, A. Kakogawa, and S. Ma, “Improvement of a Screw Drive In-Pipe Robot with Pathway Selection Mechanism to Pass Through T-Branches,” J. Robot. Mechatron., Vol.25, No.2, pp. 340-346, 2013.
- [10] J. Yamakawa, K. Watanabe, T. Inagaki, M. Kitano, and H. Jozaki, “Turning Characteristics of Articulated Tracked Vehicles,” Trans. of the JSME, Vol.66, No.642, pp. 579-585, 2000 (in Japanese).
- [11] T. Yoshida, “Introduction of Quince,” J. of the Japan Society of Mechanical Engineers, Vol.117, No.1151, pp. 672-673, 2014 (in Japanese).
- [12] S. Kawatsuma, K. Nakai, Y. Suzuki, and T. Kase, “Irradiation Test of Semiconductors Components on the Shelf for Nuclear Robots Based on Fukushima Accidents,” QST Takasaki Annual Report 2015, p. 81, 2016.
This article is published under a Creative Commons Attribution-NoDerivatives 4.0 Internationa License.