Paper:
Concept and Prototype of Soft Actuator for Liquid Nitrogen Temperature Environments
Daisuke Yamaguchi*, Tatsuya Hanaki**, Yuji Ishino**, Masayuki Hara**, Masaya Takasaki**, and Takeshi Mizuno**
*Okayama University
1-1-1 Tsushima-naka, Kita-ku, Okayama 700-8530, Japan
**Saitama University
255 Shimo-Okubo, Sakura-ku, Saitama 338-8570, Japan
A prototype of a soft actuator for extreme environments was fabricated, and driven in a cryogenic temperature environment. Previous soft actuators cannot be used for robots in extreme environments because resin, the main fabrication material, exhibits weak environmental characteristics. Therefore, this study proposes the application of polyimide (PI) films to soft actuators. PI is characterized by excellent environmental resistance. However, the welding of PI is difficult because of its high resistance. In this study, a welding method was developed for PI films. This method does not require pretreatment, or the use of adhesives or additives to reduce resistance. Hence, an actuator that utilizes all the characteristics of PI was realized. The actuator was characterized in a cryogenic environment, which is one of the extreme environments, and was successfully driven at a liquid nitrogen temperature of 78 K. This proposed technology is not limited to cryogenic environments and is expected to provide extreme environmental resistance to existing soft robots.
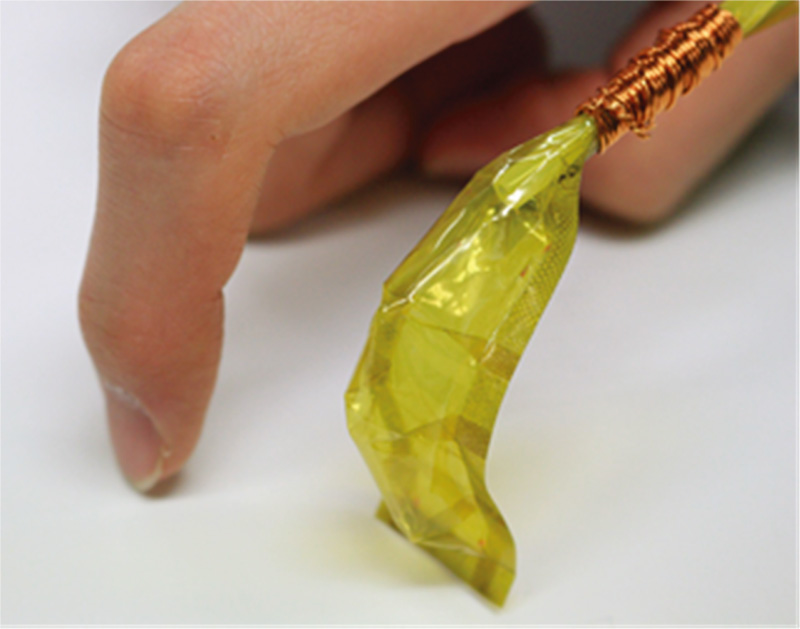
Soft actuator for extreme environments
- [1] J. F. Mohn, H. S. Bowman, and R. K. Cunningham, “A method for the preservation of human blood group erythrocyte antigens in liquid nitrogen for a test cell panel,” Vox Sang., Vol.19, No.5-6, pp. 508-521, doi: 10.1111/j.1423-0410.1970.tb01783.x., 1970.
- [2] A. Bielanski, S. Nadin-Davis, T. Sapp, and C. Lutze-Wallace, “Viral contamination of embryos cryopreserved in liquid nitrogen,” Cryobiology, Vol.40, No.2, pp. 110-116, doi: 10.1006/cryo.1999.2227, 2000.
- [3] A. Saki and S. Yoshida, “Survival of plant tissue at super-low temperature VI. Effects of cooling and rewarming rates on survival,” Plan Physiol., Vol.42, No.12, pp. 1695-1701, doi: 10.1104/pp.42.12.1695, 1967.
- [4] D. Yamaguchi, T. Kanda, and K. Suzumori, “An ultrasonic motor for cryogenic temperature using bolt-clamped Langevin-type transducer,” Sens. Actuators A: Phys., Vol.184, pp. 134-140, doi: 10.1016/j.sna.2012.06.024, 2012.
- [5] Y. Fujiyoshi, T. Mizusaki, K. Morikawa, H. Yamagishi, Y. Aoki, H. Kihara, and Y. Harada, “Development of a superfluid helium stage for high-resolution electron microscopy,” Ultramicroscopy, Vol.38, No.3-4, pp. 241-251, doi: 10.1016/0304-3991(91)90159-4, 1991.
- [6] R. Shively, “Submerged cryogenic motor materials development,” IEEE Electr. Insul. Mag., Vol.19, No.3, pp. 7-11, doi: 10.1109/MEI.2003.1203016, 2003.
- [7] D. Sasaki, T. Noritsugu, and M. Takaiwa, “Development of high contractile pneumatic artificial rubber muscle for power assist device,” J. Robot. Mechatron., Vol.24, No.1, pp. 150-157, doi: 10.1299/jsmemdt.2008.8.123, 2012.
- [8] K. Suzumori, S. Iikura, and H. Tanaka, “Development of flexible microactuator and its applications to robotic mechanisms,” Proc. of the 1991 IEEE Int. Conf. on Robotics and Automation, pp. 1622-1627, doi: 10.1109/ROBOT.1991.131850, 1991.
- [9] J. Walker, T. Zidek, C. Harbel, S. Yoon, F. S. Strickland, S. Kumar, and M. Shin, “Soft robotics: a review of recent developments of pneumatic soft actuators,” Actuators, Vol.9, No.1, pp. 3, doi: 10.3390/act9010003, 2020.
- [10] T. Sato, N. Saito, T. Ogasawara, and T. Sato, “Development of rubberless artificial muscle and fundamental characteristics,” Proc. of IECON, pp. 2124-2129, doi: 10.1109/IECON.2011.6119636, 2011.
- [11] Y. Nishioka, M. Uesu, and S. Kawamura, “Experimental production of a pneumatic soft and lightweight gripper utilizing pleated plastic-films actuators,” Proc. of the 12 Int. Conf. on Fluid Control, Measurements, and Visualization, OS4-01-4, doi: 10.1080/01691864.2017.1345323, 2013.
- [12] B. Wang, A. McDaid, A. Biglari-Abbari, T. Giffney, and K. Aw, “A bimorph pneumatic bending actuator by control of fiber braiding angle,” Sens. Actuators A: Phys., Vol.257, pp. 173-184, doi: 10.1016/j.sna.2017.02.003, 2007.
- [13] M. Okada and Y. Nakamura, “Design of active/passive hybrid compliance in the frequency domain-shaping dynamic compliance of humanoid shoulder mechanism,” Proc. of IEEE Int. Conf. on Robotics and Automation, pp. 2250-2257, doi: 10.1109/ROBOT.2000.846362, 2000.
- [14] S. Wakimoto, J. Misumi, and K. Suzumori, “New concept and fundamental experiments of a smart pneumatic artificial muscle with a conductive fiber,” Senc. Actuators A: Phys., Vol.250, pp. 48-54, doi: 10.1016/j.sna.2016.08.004, 2016.
- [15] D. Sasaki, T. Noritsugu, and M. Takaiwa, “Development of pneumatic soft robot hand for human friendly robot,” J. Robot. Mechatron., Vol.15, No.2, pp. 164-171, 2003.
- [16] J. W. Paquette, K. J. Kim, and D. Kim, “Low temperature characteristics of ionic polymer-metal composite actuators,” Sens. Actuators A: Phys., Vol.118, No.1, pp. 135-143, doi: 10.1016/j.sna.2004.08.006, 2005.
- [17] Q. Xu, M. Pang, L. Zhu, Y. Zhang, and S. Feng, “Mechanical properties of silicone rubber composed of diverse vinyl content silicone gums blending,” Mater. Des., Vol.31, No.9, pp. 4083-4087, doi: 10.1016/j.matdes.2010.04.052, 2010.
- [18] M. Kadono, “Silicone rubber,” J. SRIJ, Vol.46, No.4, pp. 295-313, 1973 (in Japanese).
This article is published under a Creative Commons Attribution-NoDerivatives 4.0 Internationa License.