Paper:
Development of a Spray-Coated Tactile Sensor – Prototype and Modeling of 2D Sensor on Cylindrical Surface –
Kouki Sato*, Luis Canete**, and Takayuki Takahashi*
*Fukushima University
1 Kanayagawa, Fukushima-shi, Fukushima 960-1296, Japan
**University of San Carlos
Nasipit Talamban, Cebu City, Cebu 6000, Philippines
The objective of this study is to extend the application of the spray-coated tactile sensor, ScoTacS, which is being developed by the authors and can be constructed simply by “coating” with a spray gun, from one dimension to two dimensions, and further to configure it into various shapes such as a ring. This sensor is constructed by coating three layers-conductive, piezoelectric, and resistive films-in sequence. It is based on a unique principle by which the contact position is detected from the delay time, i.e., the time difference between the arrivals of peaks in the output signals. As the delay time varies with the contact position, it can be used to estimate the contact position. In this paper, after analyzing the characteristics of one-dimensional sensors, such as linear and ring sensors, we present the equivalent circuit models and experimental results of a two-dimensional sensor fully coated on a cylinder.
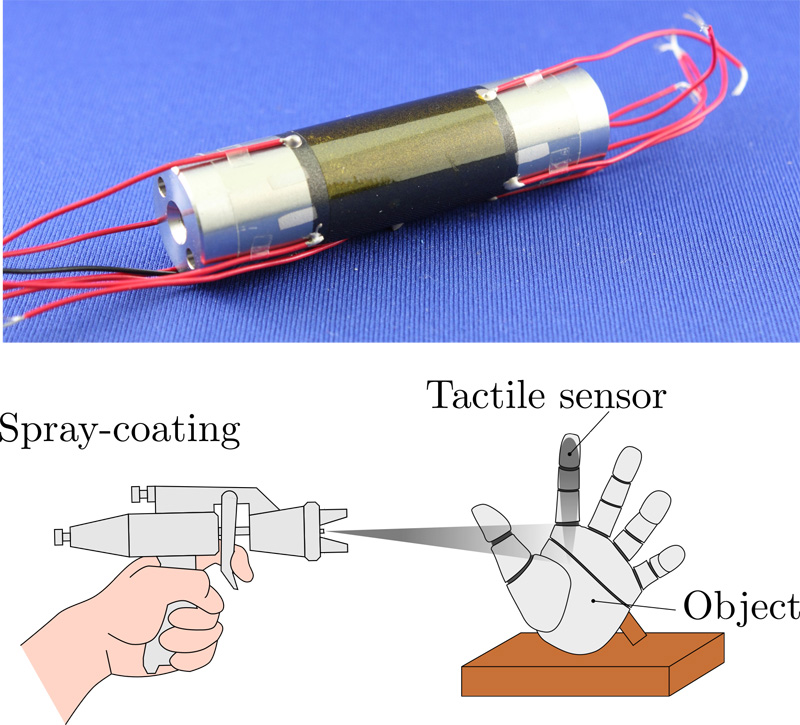
Spray-coated tactile sensor, ScoTacS
- [1] K. Sato, L. Canete, and T. Takahashi, “Development of a spray-coated tactile sensor – Study for extension to 2D sensor –,” The Robotics and Mechatronics Conf. 2018 in Kitakyushu, Japan, 1P1-M15, 2018 (in Japanese).
- [2] T. Takahashi, R. Kitajima, Y. Umino, A. Kanazawa, and T. Kuwata, “Position detection system,” Japan patent 6448084, December 14, 2018.
- [3] R. Kitajima, L. Canete, and T. Takahashi, “Development of a spray-coated tactile sensor – Improvement of the sensor model –,” The Robotics and Mechatronics Conf. 2017 in Fukushima, Japan, 1P1-N01, 2017 (in Japanese).
- [4] R. Kitajima, L. Canete, and T. Takahashi, “Development of a spray-coated tactile sensor – Inverstigation of feasibility of the sensor coated to the cylindrical curved surface –,” The Robotics and Mechatronics Conf. 2017 in Fukushima, Japan, 1A1-N01, 2017 (in Japanese).
- [5] K. Takashima, S. Horie, T. Mukai, K. Ishida, and K. Matsushige, “Piezoelectric Properties of Vinylidene Fluoride Oligomer for Use in Tactile Sensor,” J. of the Robotics Society of Japan, Vol.26, Issue 6, pp. 711-717, 2008 (in Japanese).
- [6] J. Dargah, “A piezoelectric tactile sensor with three sensing elements for robotic, endoscopic and prosthetic applications,” Sensors and Actuators A: Physical, Vol.80, Issue 1, pp. 23-30, 2000.
- [7] T. Shiraoka, S. Guo, K. Hashimoto, and T. Mukai, “Development of a Polymer-Based Flexible Sensor Sheet Using Electric Capacitance (A New Structure Achieving Both High Precision and High Resolution),” Trans. of the Japan Society of Mechanical Engineers Series C, Vol.79, Issue 798, pp. 304-313, 2013 (in Japanese).
- [8] Z. Zou, C. Zhu, Y. Li, X. Lei, W. Zhang, and J. Xiao, “Rehealable, fully recyclable, and malleable electronic skin enabled by dynamic covalent thermoset nanocomposite,” Science Advances, Vol.4, 2018.
- [9] L. E. Osborn, A. Dragomir, J. L. Betthauser, C. L. Hunt, H. H. Nguyen, R. R. Kaliki, and N. V. Thakor, “Prosthesis with neuromorphic multilayered e-dermis perceives touch and pain,” Science Robotics, Vol.3, 2018.
- [10] S. Lee, A. Reuveny, J. Reeder, S. Lee, H. Jin, Q. Liu, T. Yokota, T. Sekitani, T. Isoyama, Y. Abe, Z. Suo, and T. Someya, “A transparent bending-insensitive pressure sensor,” Nature Nanotechnology, Vol.11, pp. 472-478, 2016.
- [11] T. Sagisaka, Y. Ohmura, A. Nagakubo, Y. Kuniyoshi, and K. Ozaki, “High-density Conformable Tactile Sensing Glove,” J. of the Robotics Society of Japan, Vol.30, Issue 7, pp. 711-717, 2012 (in Japanese).
- [12] H. Shinoda, “Artificial Skin for Soft Machines,” J. of the Robotics Society of Japan, Vol.19, Issue 7, pp. 814-817, 2001 (in Japanese).
- [13] Y. Wang, K. Xi, D. Mei, G. Liang, and Z. Chen, “A Flexible Tactile Sensor Array Based on Pressure Conductive Rubber for Contact Force Measurement and Slip Detection,” J. Robot. Mechatron., Vol.28, No.3, pp. 378-385, 2016.
- [14] M. Shimojo and M. Ishikawa, “Thin and Flexible Position Sensor,” J. Robot. Mechatron., Vol.2, No.1, pp. 38-41, 1990.
- [15] M. Shimojo, T. Araki, A. Ming, and M. Ishikawa, “A High-Speed Mesh of Tactile Sensors Fitting Arbitrary Surfaces,” IEEE Sensors J., Vol.10, No.4, pp. 822-830, 2010.
- [16] J. Oh, J. Yang, J. Kim, H. Park, S. Kwon, S. Lee, J. Sim, H. Oh, J. Kim, and S. Park, “Pressure Insensitive Strain Sensor with Facile Solution-Based Process for Tactile Sensing Applications,” ACS Nano 2018, Vol.12, Issue 8, pp. 7546-7553, 2018.
- [17] Y. Zhang, G. Laput, and C. Harrison, “Electrick:Low-Cost Touch Sensing Using Electric Field Tomography,” The 2017 CHI Conf. on Human Factors in Computing Systems (CHI’17), pp. 1-14, 2017.
- [18] S. Sato, J. Kobori, T. Harada, M. Saeki, and T. Wakimoto, “Step Response Time Error of RC Distributed Line by Approximating Discrete Elements,” IEEJ Trans. on Fundamentals and Materials, Vol.118, Issue 11, pp. 1311-1317, 1998 (in Japanese).
This article is published under a Creative Commons Attribution-NoDerivatives 4.0 Internationa License.