Paper:
A Basic Framework of Virtual Reality Simulator for Advancing Disaster Response Work Using Teleoperated Work Machines
Mitsuhiro Kamezaki*, Junjie Yang**, Hiroyasu Iwata***,
and Shigeki Sugano**
*Research Institute for Science and Engineering (RISE), Waseda University, 17 Kikui-cho, Shinjuku-ku, Tokyo 162-0044, Japan
**Department of Modern Mechanical Engineering, School of Creative Science and Engineering, Waseda University, 3-4-1 Okubo, Shinjuku-ku, Tokyo 169-8555, Japan
***Department of Modern Mechanical Engineering, School of Creative Science and Engineering, Waseda University, Green Computing System R&D Center, 27 Waseda-machi, Shinjuku-ku, Tokyo 162-0042, Japan
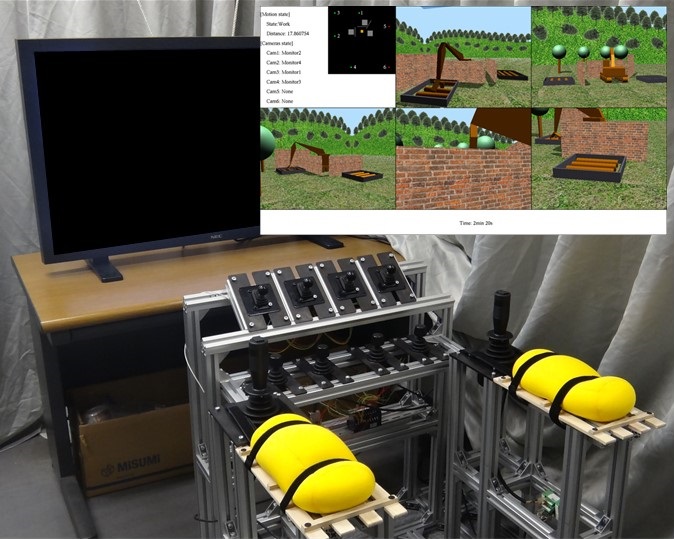
- [1] S. Tadokoro, “Special project on development of advanced robots for disaster response (DDT project),” Proc. IEEEWorkshop on Advanced Robotics and its Social Impacts, pp. 66-72, 2005.
- [2] A. Ishii, “Operation system of a double-front work machine for simultaneous operation,” Proc. Int. Symp. Automation and Robotics in Const., pp. 539-542, 2006.
- [3] M. Guarnieri, P. Debenest, T. Inoh, E. Fukushima, and S. Hirose, “Helios VII: a new vehicle for disaster response-mechanical design and basic experiments,” Advanced Robotics, Vol.19, No.8, pp. 901-927, 2005.
- [4] C. M. Humphrey and J. A. Adams, “Robotic tasks for chemical, biological, radiological, nuclear and explosive incident response,” Advanced Robotics, Vol.23, No.9, pp. 1217-1232, 2009.
- [5] S. Nishigaki, K. Saibara, S. Kitahara, H. Iwasaki, K. Yamada, and H. Satoh, “ICT-based work management to support unmanned construction for post-disaster restoration,” Proc. Int. Symp. Automation and Robotics in Const., pp. 508-513, 2011.
- [6] K. Yokoi, K. Nakashima, M. Kobayashi, H. Mihune, H. Hasunuma, Y. Yanagihara, T. Ueno, T. Gokyuu, and K. Endou, “A tele-operated humanoid robot drives a backhoe in the open air,” Proc. IEEE/RSJ Int. Conf. Intelligent Robots and Systems, pp. 1117-1122, 2003.
- [7] Y. Hiramatsu, T. Aono, and M. Nishio, “Disaster restoration work for the eruption of Mt Usuzan using an unmanned construction system,” Advanced Robotics, Vol.16, No.6, pp. 505-508, 2002.
- [8] Y. Ban, “Unmanned construction system: present status and challenges,” Proc. Int. Symp. Automation and Robotics in Const., pp. 241-246, 2002.
- [9] T. Xinxing, Z. Dingxuan, H. Yamada, and N. Tao, “Haptic interaction in tele-operation control system of construction robot based on virtual reality,” Proc. Int. Conf. Mechatronics and Automation, pp. 78-83, 2009.
- [10] K. Nagatani, S. Kiribayashi, Y. Okada, K. Otake, Y. Kazuya, S. Tadokoro, T. Nishimura, T. Yoshida, E. Koyanagi, M. Fukushima, and S. Kawatsuma, “Gamma-ray irradiation test of electric components of rescue mobile robot Quince,” Proc. IEEE Int. Symp. Safety, Security, and Rescue Robotics, pp. 56-60, 2011.
- [11] T. Hirabayashi, “Examination of information presentation method for teleoperation excavator,” J. Robotics and Mechatronics, Vol.24, No.6, pp. 967-976, 2012.
- [12] M. Jinki, S. Youngwan, P. Shinsuk, and K. Jinwook, “Development of immersive augmented reality interface for construction robotic system,” Proc. Int. Conf. Control, Automation and Systems, pp. 1192-1197, 2007.
- [13] N. Fujiwara, T. Onda, H. Masuda, and K. Chayama, “Virtual property lines drawing on the monitor for observation of unmanned dam construction site,” Proc. IEEE/ACMInt. Symp. Augmented Reality, pp. 101-104, 2000.
- [14] S. Kitahara and Y. Takashi, “Deployment of construction robots applying the information technology and network system,” Proc. Int. Symp. Automation and Robotics in Const., pp. 19-23, 2006.
- [15] H.-J. Park, S. Lee, S.-K. Kang, M.-S. Kang, M.-S. Song, and C. Han, “Experimental study on hydraulic signal compensation for the application of a haptic interface to a tele-operated excavator,” Proc. Int. Symp. Automation and Robotics in Const., pp. 298-303, 2011.
- [16] D. B. Kaber, Y. Lee, M. Clamann, and Y. S. Lee, “Investigating human performance in a virtual reality haptic simulator as influenced by fidelity and system latency,” IEEE Trans. Systems, Man and Cybernetics, Part A: Systems and Humans, Vol.42, No.6, pp. 1562-1566, 2012.
- [17] K. W. Oh, D. Kim, N. H. Kim, and D. Hong, “The virtual environment for force-feedback experiment of excavator using a novel designed haptic device,” Proc. Int. Symp. Automation and Robotics in Const., pp. 51-56, 2011.
- [18] S. Haque and S. Srinivasan, “A meta-analysis of the training effectiveness of virtual reality surgical simulators,” IEEE Trans. Information Technology in Biomedicine, Vol.10, No.1, pp. 51-58, 2006.
- [19] C. Basdogan, M. Sedef, M. Harders, and S. Wesarg, “VR-based simulators for training in minimally invasive surgery,” IEEE Computer Graphics and Applications, Vol.27, No.2, pp. 54-66, 2007.
- [20] S. Nagiri, Y. Amano, K. Fukui, and S. Doi, “The study of driving support system for individual driver,” Proc. IEEE Int. Conf. Systems, Man and Cybernetics, pp. 563-568, 2002.
- [21] S. Strassburger, T. Schulze, M. Lemessi, and G. D. Rehn, “Temporally parallel coupling of discrete simulation systems with virtual reality systems,” Proc. Conf. Winter Simulation, pp. 1949-1957, 2005.
- [22]
Supporting Online Materials:[a] Japanese Industrial Standards Committee (JISC),
https://www.jisc.go.jp/eng/ [Accessed January 15, 2014]
This article is published under a Creative Commons Attribution-NoDerivatives 4.0 Internationa License.