Research Paper:
Research on Active Disturbance Rejection Algorithm for Loading Control of 3-DOF Parallel Robot
Yu Liu
, Yumeng Chen, Yu Gong, and Guoxin Zhao

College of Information Engineering, Beijing Institute of Petrochemical Technology
No.19 Qingyuan North Road, Daxing District, Beijing 102617, China
Corresponding author
A three-dimensional (3D) loading device based on a pneumatic 3-universal-prismatic-universal (UPU) parallel manipulator (three chains with UPU joint each) is designed to apply time-varying multi-dimensional loads to a target. First, according to the principle of vector superposition and Newton–Raphson method, the inverse and forward kinematics of the loading device are analyzed. Second, based on the screw theory, the static mapping between the dynamic platform and actuations is derived. Third, a second-order mathematical model is established for pneumatic 3-UPU parallel mechanism based on proportional flow valve and a metal seal pneumatic cylinder. A referential inaccurate model is provided for the control algorithm during modeling. Fourth, based on active disturbance rejection control (ADRC) technique, a 3D loading control algorithm is proposed and dynamic loading control is realized. Experimental results show that the ADRC algorithm has good robustness against disturbances, the steady-state control accuracy is less than 2 N, and the mean square error in dynamic tracking (sinusoidal tracking at 0.2 Hz) is less than 10.5 N.
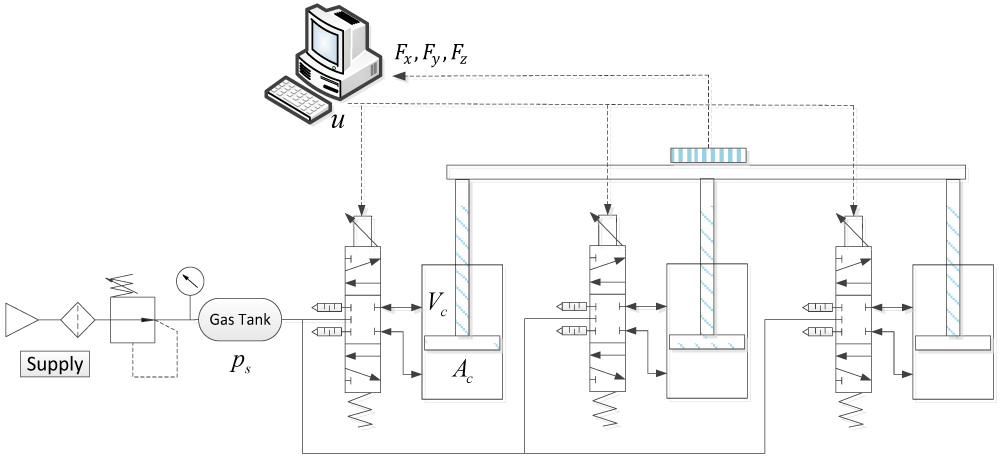
Loading control system of 3-UPU robot
- [1] Z. Yang et al., “Progress in the research of reliability technology of machine tools,” J. of Mechanical Engineering, Vol.49, No.20, pp. 130-139, 2013 (in Chinese).
- [2] V. E. Gough and S. G. Whitehall, “Universal tyre test machine,” Proc. of the 9th Int. Congress FISITA, pp. 117-137, 1962.
- [3] D. Wang, R. Fan, and W. Chen, “Stiffness analysis of a hexaglide parallel loading mechanism,” Mechanism and Machine Theory, Vol.70, pp. 454-473, 2013. https://doi.org/10.1016/j.mechmachtheory.2013.08.015
- [4] L.-W. Tsai, “Kinematics of a three-DOF platform with three extensible limbs,” J. Lenarčič and V. Parenti-Castelli (Eds.), “Recent Advances in Robot Kinematics,” pp. 401-410, Springer, 1996. https://doi.org/10.1007/978-94-009-1718-7_40
- [5] G. Bhutani and T. A. Dwarakanath, “Novel design solution to high precision 3 axes translational parallel mechanism,” Mechanism and Machine Theory, Vol.75, pp. 118-130, 2014. https://doi.org/10.1016/j.mechmachtheory.2013.11.010
- [6] R. B. A. Shyam and A. Ghosal, “Path planning of a 3-UPU wrist manipulator for sun tracking in central receiver tower systems,” Mechanism and Machine Theory, Vol.119, pp. 130-141, 2018. https://doi.org/10.1016/j.mechmachtheory.2017.08.019
- [7] Q. Wei et al., “Nonlinear compound control of pneumatic servo loading system,” J. of Mechanical Engineering, Vol.53, No.14, pp. 217-224, 2017 (in Chinese).
- [8] R. Li et al., “A sliding mode variable structure control approach for a pneumatic force servo system,” 2006 6th World Congress on Intelligent Control and Automation, pp. 8173-8177, 2006. https://doi.org/10.1109/WCICA.2006.1713567
- [9] C. Sheng and T. Zhao, “Control strategy of fast pneumatic force servo system,” Control Theory & Applications, Vol.27, No.11, pp. 1551-1556, 2010 (in Chinese).
- [10] D. Meng et al., “Adaptive robust output force tracking control of pneumatic cylinder while maximizing/minimizing its stiffness,” J. of Central South University, Vol.20, No.6, pp. 1510-1518, 2013.
- [11] J. Q. Han, “Automatic Disturbance Rejection Control Technology,” National Defense Industry Press, 2008 (in Chinese).
- [12] Z. Wu et al., “Active disturbance rejection control design for high-order integral systems,” ISA Trans., Vol.125, pp. 560-570, 2022. https://doi.org/10.1016/j.isatra.2021.06.038
- [13] X. Wu et al., “Attitude stabilization control of autonomous underwater vehicle based on decoupling algorithm and PSO-ADRC,” Frontiers in Bioengineering and Biotechnology, Vol.10, Article No.843020, 2022. https://doi.org/10.3389/fbioe.2022.843020
- [14] B. Xiang, Q. Guo, and W. Wong, “Active disturbance rejection control of test sample in electrostatic suspension system,” Mechanical Systems and Signal Processing, Vol.148, Article No.107187, 2021. https://doi.org/10.1016/j.ymssp.2020.107187
- [15] X. Zhou, C. Wang, and Y. Ma, “Vector speed regulation of an asynchronous motor based on improved first-order linear active disturbance rejection technology,” Energies, Vol.13, No.9, Article No.2168, 2020. https://doi.org/10.3390/en13092168
- [16] Z. S. Wu, “Pneumatic Transmission and Control,” Harbin Institute of Technology Press, 1995 (in Chinese).
- [17] Y. Liu et al., “Pressure control of pneumatic gravity compensation system,” J. of Mechanical Engineering, Vol.54, No.16, pp. 212-219, 2018 (in Chinese).
- [18] S. Balajiwale, H. Arya, and A. Joshi, “Study of performance of ADRC for longitudinal control of MAV,” IFAC-PapersOnLine, Vol.49, No.1, pp. 585-590, 2016. https://doi.org/10.1016/j.ifacol.2016.03.118
This article is published under a Creative Commons Attribution-NoDerivatives 4.0 Internationa License.