Paper:
A Control System for a Tool Use Robot: Drawing a Circle by Educing Functions of a Compass
Kyo Kutsuzawa, Sho Sakaino, and Toshiaki Tsuji
Saitama University
255 Shimo-Ohkubo, Sakura-ku, Saitama 338-8570, Japan
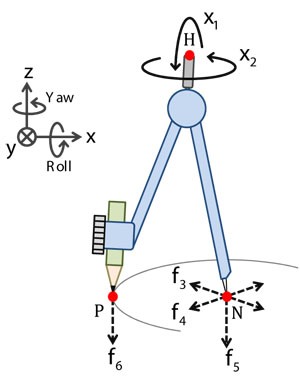
Axes in the compass coordinate system
- [1] B. B. Beck, “Animal Tool Behavior,” Garland STPM Pub., 1980.
- [2] J. J. Gibson, “The Ecological Approach to Visual Perception,” Houghton Mifflin, Boston, 1979.
- [3] A. Stoytchev, “Behavior-Grounded Representation of Tool Affordances,” Proc. IEEE Int. Conf. Robot. Autom., pp. 3060-3065, 2005.
- [4] R. Jain and T. Inamura, “Learning of Tool Affordances for Autonomous Tool Manipulation,” IEEE/SICE Int. Symp. on System Integration, pp. 814-819, 2011.
- [5] T. Mar, V. Tikhanoff, G. Metta, and L. Natale, “Self-Supervised Learning of Grasp Dependent Tool Affordances on the iCub Humanoid Robot,” Proc. IEEE Int. Conf. Robot. Autom., pp. 3200-3206, 2015.
- [6] C. Nabeshima, Y. Kuniyoshi, and M. Lungarella, “Towards a Model for Tool-Body Assimilation and Adaptive Tool-Use,” IEEE Int. Conf. on Develop. and Learning, pp. 288-293, 2007.
- [7] C. Nabeshima, “A Computational Model of Flexible Tool-Use Based on Body Schema Adaptation and Functionality Learning,” Ph.D. dissertation, The University of Tokyo, 2009 (in Japanese).
- [8] P. Kormushev, S. Calinon, and D. G. Caldwell, “Robot Motor Skill Coordination with EM-Based Reinforcement Learning,” Proc. IEEE/RSJ Int. Conf. Intell. Robots Syst., pp. 3232-3237, 2010.
- [9] P. Kormushev, S. Calinon, and D. G. Caldwell, “Imitation Learning of Positional and Force Skills Demonstrated via Kinesthetic Teaching and Haptic Input,” Advanced Robotics, Vol.25, No.5, pp. 581-603, 2011.
- [10] M. Takeuchi, J. Shimodaira, Y. Amaoka, S. Hamatani, H. Hirai, and F. Miyazaki, “Reconstruction of Human Skills by Using PCA and Transferring Them to a Robot,” J. of Robotics and Mechatronics, Vol.26, No.1, pp. 51-58, 2014.
- [11] Y. Watanabe, K. Nagahama, K. Yamazaki, K. Okada, and M. Inaba, “Cooking Behavior with Handling General Cooking Tools Based on a System Integration for a Life-Sized Humanoid Robot,” Paladyn, J. of Behavioral Robotics, Vol.4, No.2, pp. 63-72, 2013.
- [12] F. Osawa, H. Seki, and Y. Kamiya, “Clothes Folding Task by Tool-Using Robot,” J. of Robotics and Mechatronics, Vol.18, No.5, pp. 618-625, 2006.
- [13] J. K. Salisbury Jr., “Interpretation of Contact Geometries from Force Measurements,” Proc. IEEE Int. Conf. Robot. Autom., Vol.1, pp. 240-247, 1984.
- [14] N. Mimura and Y. Funahashi, “Parameter Identification of Contact Conditions by Active Force Sensing,” Proc. IEEE Int. Conf. Robot. Autom., Vol.3, pp. 2645-2650, 1994.
- [15] K. Kutsuzawa, S. Sakaino, and T. Tsuji, “Estimation of Individual Contact Force when Two Contact Points Exist During Robotic Tool Use,” Proc. JSME Int. Conf. on Advanced Mechatronics, pp. 46-47, 2015.
- [16] M. H. Raibert and J. J. Craig, “Hybrid Position/Force Control of Manipulators,” Trans. ASME, J. Dyn. Syst. Meas. Control, Vol.103, No.2, pp. 126-133, 1981.
- [17] O. Khatib, “A Unified Approach for Motion and Force Control of Robot Manipulators: The Operational Space Formulation,” IEEE J. Robot. Autom., Vol.3, No.1, pp. 43-53, 1987.
- [18] R. Featherstone, S. Sonck, and O. Khatib, “A General Contact Model for Dynamically-Decoupled Force/Motion Control,” Experimental Robotics V, Springer, pp. 128-139, 1998.
- [19] J. Park and O. Khatib, “Robot Multiple Contact Control,” Robotica, Vol.26, No.5, pp. 667-677, 2008.
- [20] T. Tsuji, H. Nishi, and K. Ohnishi, “A Controller Design Method of Decentralized Control System,” IEEJ Trans. Ind. Appl., Vol.126-D, No.5, pp. 630-638, 2006.
- [21] T. Tsuji, K. Ohnishi, and A. uSabanovi‘c, “A Controller Design Method Based on Functionality,” IEEE Trans. Ind. Electron., Vol.54, No.6, pp. 3335-3343, 2007.
- [22] N. Mimura and Y. Funahashi, “Parameter Identification of a Grasp by a Planar Two-Fingered Robot Hand,” J. of Robotics and Mechatronics, Vol.5, No.1, pp. 12-18, 1993.
This article is published under a Creative Commons Attribution-NoDerivatives 4.0 Internationa License.