Paper:
Automatic Transplanting Equipment for Chain Pot Seedlings in Shaft Tillage Cultivation
Junya Tatsuno*, Kiyoshi Tajima**, and Masayoshi Kato***
*Faculty of Engineering, Kindai University
1 Takaya Umenobe, Higashi-Hiroshima, Hiroshima 739-2116, Japan
**Faculty of Regional Environment Science, Tokyo University of Agriculture
1-1-1 Sakuragaoka, Setagaya, Tokyo 156-8502, Japan
***Faculty of Agriculture, Tokyo University of Agriculture
1737 Funako, Atsugi, Kanagawa 243-0034, Japan
The study aims to develop automatic transplanting equipment for chain pot seedlings. We intend to practice the shaft tillage cultivation using an autonomous farming robot. We had developed an autonomous working vehicle and automatic transplanting equipment for plug seedlings used in shaft tillage cultivation. To reinforce the robot system’s versatility, we developed transplanting equipment for the chain pot seedlings. We experimentally investigated the transplanting performance. Approximately 84% of the seedlings were automatically transplanted using the developed equipment. Since the equipment was performed well in the failure samples, we assumed that the cause of such failures was attributed to seedling quality. In addition, we measured the power consumption of the equipment used to build an electrical power supply system. Consequently, we calculated the power requirements for each process. Compared with the plug seedling equipment developed in the previous study, the chain pot seedlings’ power requirement was lower because the conveying actions of seedlings were different. In the next stage of our research, to construct a fully automatic system, we will consider the seedling raising method in which seedlings can become uniformly high-quality and investigate the plant establishment performance using the developed equipment.
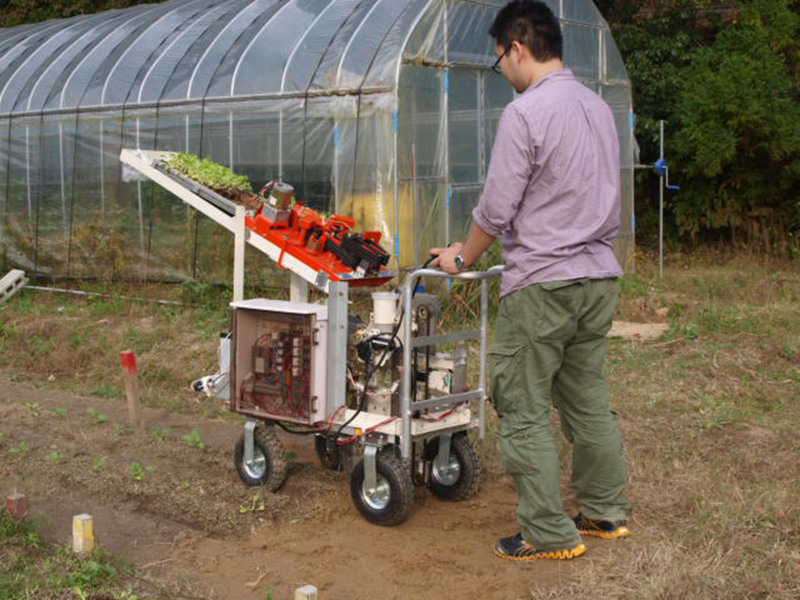
Developed transplanting equipment for chain pot seedlings during the performance test
- [1] A. Mizushima, N. Noguchi, K. Ishii, H. Terao, O. Yukumoto, and S. Yamamoto, “Automatic Guidance Algorism Based on Sensor Fusion of Geomagnetic Direction Sensor and Gyroscope – Sensor fusion composed of Kalman filter,” J. of the Japanese Society of Agricultural Machinery, Vo.63, Issue 4, pp. 96-102, 2001 (in Japanese).
- [2] M. Kise, Q. Zhang, and N. Noguchi, “An Obstacle Identification Algorithm for a Laser Range Finder Based Obstacle Detector,” Trans. of the ASAE, Vol.48, Issue 3, pp. 1269-1278, 2005.
- [3] E. J. Van Henten, B. A. J. Van Tuijl, J. Hemming, J. G. Kornet, J. Bontsema, and E. A. Van Os, “Field Test of an Autonomous Cucumber Picking Robot,” Biosystems Eng., Vol.86, Issue 3, pp. 305-313, 2003.
- [4] S. Bachche and K. Oka, “Design, Modeling and Performance Testing of End-Effector for Sweet Pepper Harvesting Robot Hand,” J. Robot. Mechatron., Vol.25, No.4, pp. 705-717, 2012.
- [5] T. Yoshida, T. Fukao, and T. Hasegawa, “Fast Detection of Tomato Peduncle Using Point Cloud with a Harvesting Robot,” J. Robot. Mechatron., Vol.30, No.2, pp. 180-186, 2018.
- [6] T. Fujinaga, S. Yasukawa, and K. Ishii, “Tomato Growth State Map for the Automation of Monitoring and Harvesting,” J. Robot. Mechatron., Vol.32, No.6, pp. 1279-1291, 2020.
- [7] R. C. Harrell, P. D. Adsit, T. A. Pool, and R. Hoffman, “The Florida robotic grove-lab,” Trans. of the ASAE, Vol.33, Issue 2, pp. 391-399, 1990.
- [8] J. Baeten, K. Donne, S. Boedrij, W. Beckers, and E. Claesen, “Autonomous Fruit Picking Machine: A Robotic Apple Harvester,” Proc. of the 6th Int. Conf. on Field and Service Robotics (FSR), pp. 531-540, 2008.
- [9] H. A. M. Williams, M. H. Jones, M. Nejati, M. J. Seabright, J. Bell, N. D. Penhall, J. J. Barnett, M. D. Duke, A. J. Scarfe, H. S. Ahn, J. Lim, and B. A. MacDonald, “Robotic kiwifruit harvesting using machine vision, convolutional neural networks, and robotic arms,” Biosystems Eng., Vol.181, pp. 140-156, 2019.
- [10] K. Tajima, K. Tamaki, J. Tatsuno, M. Kato, and T. Inagaki, “A study on the shaft tillage cultivation system for an agricultural Robot,” Eng’96 Int. Conf. on Agricultural Engineering, 96-A-101, 1996.
- [11] K. Tajima, M. Kato, and J. Tatsuno, “Development of Planting Tool for the Bed with Cover Crop,” Japanese J. of Farm Work Research, Vol.35, No.4, pp. 223-228, 2000 (in Japanese).
- [12] K. Tajima, M. Kato, J. Tatsuno, and K. Tamaki, “Effect of Dressing Application Method on the Growth of Chinese Cabbage Under the Shaft Tillage Cultivation with Cut Weed Living Mulch,” Japanese J. of Farm Work Research, Vol.38, No.1, pp. 17-24, 2003 (in Japanese).
- [13] K. Tajima, J. Tatsuno, M. Kato, Y. Sasaki, H. Kawashima, T. Ishii, Y. Miyauchi, E. Kinoshita, and K. Tamaki, “Development of Automatic Attachment for Shaft Tillage Cultivation and Transplanting,” Japanese J. of Farm Work Research, Vol.43, No.3, pp. 135-142, 2008 (in Japanese).
- [14] J. Tatsuno, K. Tajima, M. Kato, T. Ishii, and K. Tamaki, “Positioning of an Autonomous Farm Vehicle for Conducting Shaft Tillage Cultivation,” J. of the Japanese Society of Agricultural Machinery, Vol.71, No.2, pp. 45-63, 2009 (in Japanese).
- [15] J. Tatsuno, K. Inagaki, and K. Tajima, “Development of a Legged Robot for Shaft Tillage Cultivation – Proposal of Basic Concept –,” Proc. of the 4th IFAC Int. Workshop on Bio-Robotics, Information Technology, and Intelligent Control for Bioproduction Systems (Bio-Robotics IV), 203, 2009.
This article is published under a Creative Commons Attribution-NoDerivatives 4.0 Internationa License.