Development Report:
Design and Practice of a Model-Based Development Education in Hydraulic Systems
Mikiya Sako*, Shin Wakitani*, Masatoshi Kozui*, Toru Yamamoto*, Koji Yamashita**, Kazushige Koiwai**, and Yoichiro Yamazaki**
*Graduate School of Engineering, Hiroshima University
1-4-1 Kagamiyama, Higashi-hiroshima, Hiroshima 739-8527, Japan
**KOBELCO Construction Machinery Co., Ltd.
2-1 Itsukaichikou 2-chome, Saeki-ku, Hiroshima 731-5161, Japan
This paper proposes educational simulation environment for the model-based development (MBD) of hydraulic systems. In recent years, customer requirements for different products have become more diversified and increasingly complicated. Thus, companies must respond to such demands promptly. Many companies are beginning to adopt an MBD as a solution to this problem because such an approach can reduce the development time and cost. However, most engineers in such companies lack experience with an MBD. Therefore, establishing a training environment that can allow them to learn the MBD process experientially within a short timeframe is an effective approach. Moreover, because hydraulic systems are mainly used in construction machines, this study focuses on educational materials for hydraulic systems through an MBD educational program jointly developed between Hiroshima University and Kobelco Construction Machinery Co., Ltd.
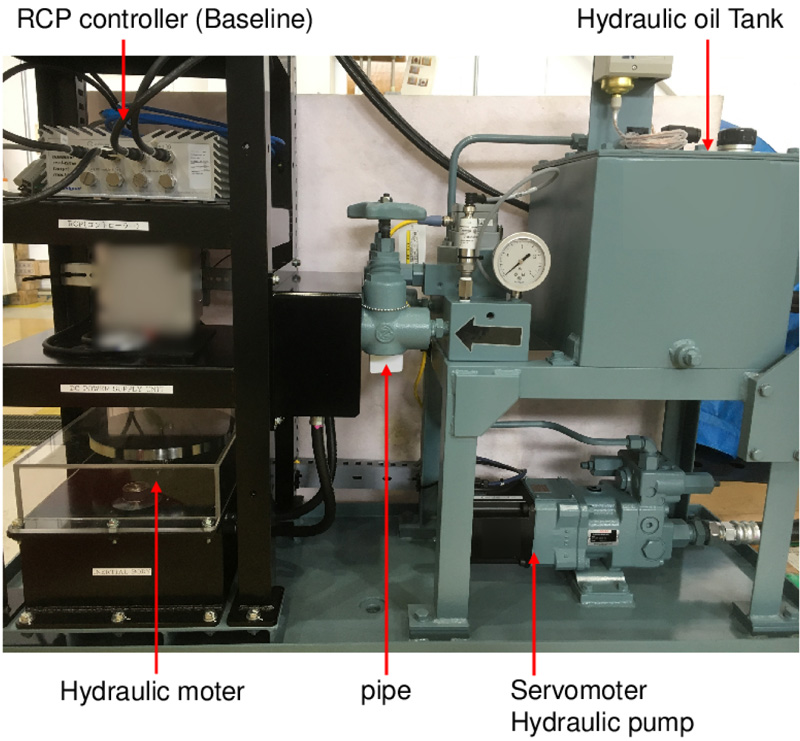
Hydraulic motor control system for MBD education
- [1] A. Ohata and K. R. Butts, “Improving Model-based Design for Automotive Control Systems Development,” Proc. 17th IFAC World Congress 2008, Vol.41, No.2, pp. 1062-1065, 2008.
- [2] H. Ogata and T. Katayama, “Skill standards for model based development engineers in the automotive industry,” IFAC Proc. Volumes, Vol.42, No.24, pp. 240-244, 2009.
- [3] S. Wakitani and T. Yamamoto, “Design of an Educational Hardware in the Loop Simulator for Model-Based Development Education,” J. Robot. Mechatron., Vol.31, No.3, pp. 376-382, 2019.
- [4] A. Ohata, H. Ito, S. Gopalswamy, and K. Furuta, “Plant Modeling Environment Based on Conservation Laws and Projection Method for Automotive Control Systems,” SICE J. of Control, Measurement, and System Integration, Vol.1, Issue 3, pp. 227-234, 2008.
- [5] T. Nagano, M. Harakawa, M. Iwase, J. Ishikawa, and H. Koizumi, “Model Based Development Method for Servo Control System of Industrial Machine,” Trans. of the Japan Society for Simulation Technology, Vol.10, No.3, pp. 77-87, 2018.
- [6] T. Ishigooka, H. Saissi, T. Piper, S. Winter, and N. Suri, “Safety Verification Utilizing Model-based Development for Safety Critical Cyber-Physical Systems,” J. of Information Processing, Vol.25, pp. 797-810, 2017.
- [7] M. Shimoura, K. Tsujimoto, and Y. Morita, “Applying Model-Based Development (MBD) to Rocket Electronic Control Systems,” J. of IHI Techonologies, Vol.54, No.1, pp. 34-40, 2014.
- [8] S. Yoshida, H. Ito, T. Morikawa, J. Kako, and Y. Kuroda, “Development of High Level Modeling Method for Rapid Modeling Process – Application for Combustion Modeling in Engine Cylinder –,” Trans. of the Society of Automotive Engineers of Japan, Vol.46, No.1, pp. 103-108, 2015.
- [9] Y. Akimoto, E. Sato-Shimokawara, Y. Fujimoto, and T. Yamaguchi, “Model-Based Development with User Model as Practical Process of HCD for Developing Robots,” J. Robot. Mechatron., Vol.28, No.4, pp. 579-590, 2016.
- [10] T.-H. Lim, H.-C. Cho, H.-S. Lee, and S.-Y. Yang, “Development of Hardware In the Loop System (HILS) for Hydraulic Excavator,” Proc. of 22nd Int. Symp. on Automation and Robotics in Construction (ISARC 2005), 2005.
- [11] M. Watanabe and K. Sakai, “Development of Nonlinear Tractor Model using in Constructing Tractor Driving Simulator,” American Society of Agricultural and Biological Engineers (ASABE), Vol.1700374, pp. 1-6, 2017
- [12] S. Wakitani and T. Yamamoto, “Practice of Model-based Development for Automotive Engineers,” Proc. of 2017 IEEE Frontiers in Education Conf. (FIE), pp. 1-4, 2017.
- [13] R. Iserman, J. Schaffnit, and S. Sinsel, “Hardware-in-the-loop simulation for the design and testing of engine-control systems,” Control Engineering Practice, Vol.7, No.5, pp. 643-653, 1999.
- [14] Y. Senta, M. Hashima, and Y. Sato, “HIL Simulation System: An Embedded-Software Development Environment for Mechanical Systems,” J. of the Society of Instrument and Control Engineers, Vol.41, No.2, pp. 151-154, 2002.
- [15] M. Bacic, “On hardware-in-the-loop simulation,” Proc. of the 44th IEEE Conf. on Decision and Control, pp. 3194-3198, 2005.
- [16] A. Sala and J. Bondia, “Teaching experience with hardware-in-the-loop simulation,” IFAC Proc. Volumes, Vol.39, No.6, pp. 123-128, 2006.
- [17] G. Gambino, G. Siano, G. Palmieri, W. Mauro, G. Vanoli, F. Criscuolo, D. Del Cogliano, F. de Rossi, and L. Glielmo, “A low-cost HIL platform for testing professional refrigerators controllers,” IFAC Proc. Volumes, Vol.47, No.3, pp. 3104-3109, 2014.
This article is published under a Creative Commons Attribution-NoDerivatives 4.0 Internationa License.