Paper:
Development of a Real-Time Force and Temperature Sensing System with MEMS-LSI Integrated Tactile Sensors for Next-Generation Robots
Masanori Muroyama*, Hideki Hirano*, Chenzhong Shao*, and Shuji Tanaka*,**
*Microsystem Integration Center, Tohoku University
6-6-1 Aoba, Aramaki, Aoba-ku, Sendai 980-8579, Japan
**Department of Robotics, Graduate School of Engineering, Tohoku University
6-6-1 Aoba, Aramaki, Aoba-ku, Sendai 980-8579, Japan
This study proposes a sensing system that can sense force and temperature at the same time. The system consists of MEMS-LSI integrated tactile sensor devices called sensor nodes, a field-programmable gate array (FPGA) based relay node, and a host PC. For real-time temperature and force data acquisition, a time-sharing force and temperature task processing mechanism was implemented with a dedicated computer architecture in the FPGA configuration and the host program. This study firstly reports the temperature dependency analysis of a capacitive sensor readout circuit in the sensor node by circuit-level simulation. With a fabricated sensor node, sensor output data were measured and analyzed with varying temperatures and applied force. Based on the measured data, linear multiple regression equations for temperature compensation of sensed force data were developed. In the temperature range of 24.8°C–60°C, the average/maximum force errors when considering the temperature effect were −0.98%/65% without the compensation, and 0.072%/17% with the compensation, respectively. One cycle time of temperature and force sensing for one sensor node was 113 ms on average. The experimental results showed that real-time temperature and force sensing and temperature compensation for accurate force sensing could be achieved successfully. The study also demonstrated the system with hot-coffee cup and finger touch examples.
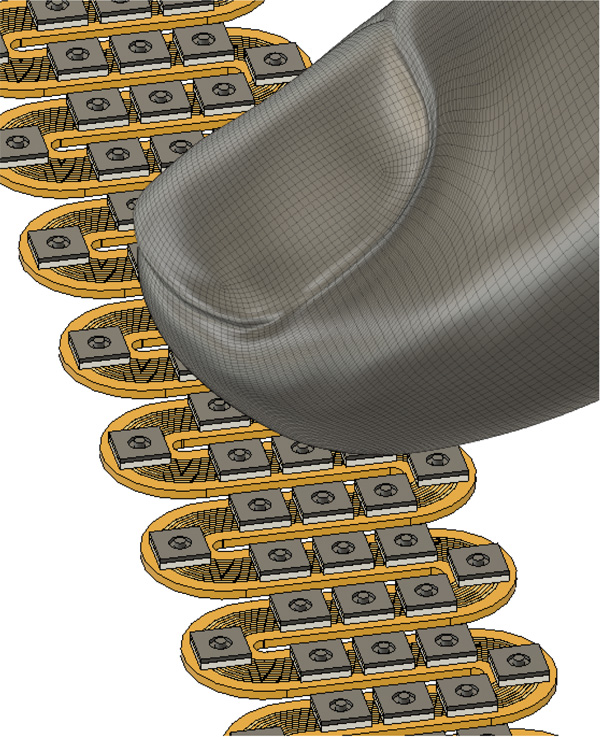
Real-time force and temperature sensing
- [1] B. D. Argall and A. G. Billard, “A Survey of Tactile Human-Robot Interactions,” Robotics and Autonomous Systems, Vol.58, No.10, pp. 1159-1176, 2010.
- [2] R. S. Dahiya, G. Metta, M. Valle, and G. Sandini, “Tactile Sensing – From Humans to Humanoids,” IEEE Trans. on Robotics, Vol.26, No.1, pp. 87-96, 2010.
- [3] H. Yousef, M. Boukallel, and K. Althoefer, “Tactile sensing for dexterous in-hand manipulation in robotics – A review,” Sensors and Actuators A, Vol.167, pp. 171-187, 2011.
- [4] D. Silvera-Tawil, D. Rye, and M. Velonaki, “Artificial Skin and Tactile Sensing for Socially Interactive Robots: a Review,” Robot. Auton. Syt., Vol.63, pp. 230-243, 2015.
- [5] G. Liang, Y. Wang, D. Mei, K. Xi, and Z. Chen, “Flexible Capacitive Tactile Sensor Array with Truncated Pyramids as Dielectric Layer for Three-Axis Force Measurement,” Microelectromech. Syst., Vol.24, pp. 1510-1519, 2015.
- [6] G. Canavese, S. Stassi, C. Fallauto, S. Corbellini, V. Cauda, V. Camarchia, M. Pirola, and C. F. Pirri, “Piezoresistive Flexible Composite for Robotic Tactile Applications,” Sensors and Actuators A, Vol.208, pp. 1-9, 2014.
- [7] M. Muroyama, M. Makihata, S. Tanaka, T. Kojima, T. Nakayama, U. Yamaguchi, H. Yamada, Y. Nonomura, H. Funabashi, Y. Hata, and M. Esashi, “Tactile Sensor Network System with CMOS-MEMS Integration for Social Robot Applications,” Proc. of Smart Systems Integration 2014, pp. 181-188, 2014.
- [8] S. Asano, M. Muroyama, T. Bartley, T. Kojima, T. Nakayama, U. Yamaguchi, H. Yamada, Y. Nonomura, Y. Hata, H. Funabashi, and S. Tanaka, “Surface-Mountable Capacitive Tactile Sensors with Flipped CMOS-Diaphragm on a Flexible and Strechable Bus Line,” Sensors and Actuators A, Vol.240, pp. 167-176, 2016.
- [9] Y. Hata, Y. Nonomura, Y. Omura, T. Nakayama, M. Fujiyoshi, H. Funabashi, T. Akashi, M. Muroyama, and S. Tanaka, “Quad-Seesaw-Electrode Type 3-Axis Tactile Sensor with Low Nonlinearities and Low Cross-Axis Sensitivities,” Sensors and Actuators A, Vol.266, pp. 24-35, 2017.
- [10] Y. Hata, Y. Suzuki, M. Muroyama, T. Nakayama, Y. Nonomura, R. Chand, H. Hirano, Y. Omura, M. Fujiyoshi, and S. Tanaka, “Integrated 3-Axis Tactile Sensor Using Quad-Seesaw-Electrode Structure on Platform LSI with Through Silicon Vias,” Sensors and Actuators A, Vol.273, pp. 30-41, 2018.
- [11] S. Asano, M. Muroyama, T. Nakayama, Y. Hata, Y. Nonomura, and S. Tanaka, “3-Axis Fully-Integrated Capacitive Tactile Sensor with Flip-Bonded CMOS on LTCC Interposer,” Sensors, Vol.17, Issue 11, No.2451, pp. 1-14, 2017.
- [12] M. Makihata, M. Muroyama, S. Tanaka, T. Nakayama, Y. Nonomura, and M. Esashi, “Design and Fabrication Technology of Low Profile Tactile Sensor with Digital Interface for Whole Body Robot Skin,” Sensors, Vol.18, Issue 7, No.2374, pp. 1-14, 2018.
- [13] H. Takao, M. Yawata, K. Sawada, and K. Ishida, “A multifunctional integrated silicon tactile image with arrays of strain and temperature sensors on single crystal silicon diaphragm,” Sensors and Actuators A, Vol.20, pp. 119-127, 2011.
- [14] R. Araki, T. Abe, H. Noma, and M. Sohgawa, “Miniaturization and High-Density Arrangement of Microcantilevers in Proximity and Tactile Sensor for Dexterous Gripping Control,” Micromachines, Vol.9, No.6, p. 301, 2018.
- [15] K. Watatani, K. Terao, F. Shimokawa, and H. Takao, “Planar-type MEMS tactile sensor integrating micro-macro detection function of fingertip to evaluate surface touch sensation,” Japanese J. of Applied Physics, Vol.58, pp. 097002-1-097002-9, 2019.
- [16] Y. Ohmura, Y. Kuniyoshi, and A. Nagakubo, “Conformable and Scalable Tactile Sensor Skin for Curved Surfaces,” Proc. of 2006 IEEE Int. Conf. on Robotics and Automation, pp. 1348-1353, 2006.
- [17] A. Schmitz, P. Maiolino, M. Maggiali, L. Natale, G. Cannata, and G. Metta, “Methods and Technologies for the Implementation of Large-Scale Robot Tactile Sensors,” IEEE Trans. on Robotics, Vol.27, No.3, pp. 389-400, 2011.
- [18] E. Kandel, J. Schwartz, T. Jessell, S. Siegelbaum, and A. J. Hudspeth, “Principles of Neural Science, Fifth Edition,” McGraw-Hill Professional, 2012.
- [19] T. Bartley, S. Tanaka, Y. Nonomura, T. Nakayama, and M. Muroyama, “Delay Window Blind Oversampling Clock and Data Recovery Algorithm with Wide Tracking Range,” Proc. of ISCAS 2015, pp. 1598-1601, 2015.
- [20] T. Bartley, S. Tanaka, Y. Nonomura, T. Nakayama, Y. Hata, and M. Muroyama, “Sensor Network Serial Communication System with High Tolerance to Timing and Topology Variations,” Proc. of IEEE Sensors 2015, pp. 362-365, 2015.
- [21] M. Muroyama, T. Nakayama, Y. Hata, Y. Nonomura, T. Bartley, and S. Tanaka, “A CMOS-LSI for a Sensor Network Platform of Social Robot Applications,” Proc. of Smart Systems Integration 2016, pp. 320-327, 2016.
- [22] M. Muroyama, T. Nakayama, Y. Hata, and S. Tanaka, “Multi-Sensor Platform LSI Enabling Different Sensors to Be Event-Driven and Connected to Common Differential Bus Line,” Proc. of Transducers 2017, pp. 1156-1159, 2017.
- [23] Y.-J. Huang, T.-H. Tzeng, T.-W. Lin, C.-W. Huang, P.-W. Yen, P.-H. Kuo, C.-T. Lin, and S.-S. Lu, “A Self-Powered CMOS Reconfigurable Multi-Sensor SoC for Biomedical Applications,” IEEE J. of Solid-State Circuits, Vol.49, No.4, pp. 851-866, 2014.
- [24] R. J. Baker, “CMOS Circuit Design, Layout, and Simulation, Revised Second Edition,” Wiley – IEEE Press, 2007.
This article is published under a Creative Commons Attribution-NoDerivatives 4.0 Internationa License.