Development Report:
Development of Hanger-Rope Inspection Robot for Suspension Bridges
Hidekazu Kajiwara, Naohiko Hanajima, Kentarou Kurashige, and Yoshinori Fujihira
Muroran Institute of Technology
27-1 Mizumoto-cho, Muroran, Hokkaido 050-8585, Japan
This paper describes the development of a hanger-rope inspection robot for suspension bridges. The inspection robot inspects the hanger rope by going up and down the rope installed vertically downward from the main cable of a suspension bridge. The going-up-and-down mechanism of the robot consists of a drive roller driven by a motor and a non-excitation electromagnetic brake, and the robot can safely descend after climbing the rope at high speed. The developed robot is small in size and light in weight, and an inspection worker can easily install the robot on the rope. In addition, the robot can be wirelessly controlled with ease from the controller. First, this paper describes the hanger-rope inspection strategy of the suspension bridge. Then, the developed prototype 2 robot is introduced. Next, the result of the hanger-rope inspection in an actual suspension bridge and the problems are clearly revealed by experiment. Finally, the newly developed prototype 3 robot is introduced, and the result of the going-up-and-down experiment is described.
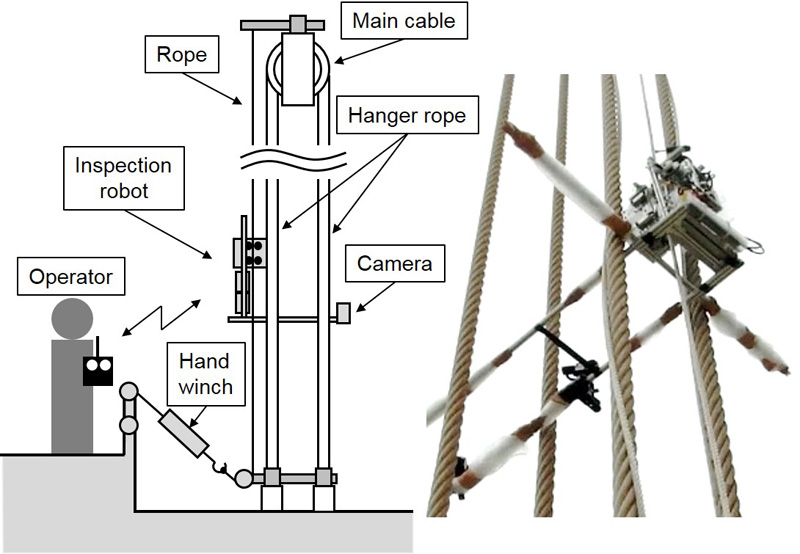
Hanger-rope inspection using prototype 2 robot
- [1] K. Kawamura, T. Hasegawa, and M. Shiozaki, “Basic Study of an Inspection Record System for Cable-Stayed Bridge Cable Inspection Robot,” Proc. Jpn. Soc. Civ. Eng. F3, Vol.72, No.2, pp. I_83-I_92, 2016 (in Japanese).
- [2] F. Xu, X. Wang, and L. Wang, “Cable Inspection Robot for Cable-Stayed Bridges: Design, Analysis, and Application,” J. of Field Robotics, Vol.28, Issue 3, pp. 441-459, 2011.
- [3] X. Li , C. Gao, Y. Guo, F. He, and Y. Shao, “Cable surface damage detection in cable-stayed bridges using optical techniques and image mosaicking,” Optics and Laser Technology, Vol.110, pp. 36-43, 2019.
- [4] K. H. Cho, Y. H. Jin, H. M. Kim, H. Moon, J. C. Koo, and H. R. Choi, “Caterpillar-based Cable Climbing Robot for Inspection of Suspension Bridge Hanger Rope,” IEEE Int. Conf. on Automation Science and Engineering, pp. 1059-1062, 2013.
- [5] N. Imajo, Y. Takada, and M. Kashinoki, “Development and Evaluation of Compact Robot Imitating a Hermit Crab for Inspecting the Outer Surface of Pipes,” J. of Robotics, Vol.2015, pp. 1-7, 2015.
- [6] A. Baghani, M. Nili, and A. A. Harati, “Kinematics Modeling of a Wheel-Based Pole Climbing Robot (UT-PCR),” Proc. of the 2005 IEEE Int. Conf. on Robotics and Automation, pp. 2099-2104, 2005.
- [7] H. Tsukagoshi, K. Fuchigami, E. Watari, and A. Kitagawa, “Deformable Anchor Ball for Thrown Referring to Octopus Suckers,” J. Robot. Mechatron., Vol.26, No.4, pp. 477-485, 2014.
- [8] T. Egami, A. Nagashima, and K. Umemoto, “Lift Stabilization Control for an Experimental Space Elevator Climber for a Rope-type Tether using a CMG Unit,” J. of the Robotics Society of Japan, Vol.35, No.1, pp. 47-54, 2017 (in Japanese).
- [9] M. Sarieva, L. Yao, K. Sugawara, and T. Egami, “Synchronous Position Control of Robotics System for Infrastructure Inspection Moving on Rope Tether,” J. Robot. Mechatron., Vol.31, No.2, pp. 317-328, 2019.
This article is published under a Creative Commons Attribution-NoDerivatives 4.0 Internationa License.