Paper:
Development of a Self-Weight Gripper Suitable for Flexible and Heavy Bagged Objects
Takahide Kitamura*
, Takeru Shirasawa**, Natsuki Yamanobe*
, Toshio Ueshiba*
, Atsushi Ushirone**, and Yukiyasu Domae*,

*National Institute of Advanced Industrial Science and Technology
AIST Tokyo Waterfront (Second Annex), 2-4-7 Aomi, Koto-ku, Tokyo 135-0064, Japan
Corresponding author
**Toyota Motor Corporation
1 Toyota-cho, Toyota, Aichi 471-8571, Japan
A social issue owing to the aging of society in recent years is the daily removal of garbage by the elderly. This study proposes a gripper that can grip large, flexible, and heavy objects such as garbage bags as well as small and light objects such as plastic bottles, with the aim of automating the garbage-collection process. The proposed gripper consists of an opening/closing mechanism with a rhombic link structure and a contact area that makes contact with the object to be gripped. This mechanism is characterized by its power-saving effect as it converts the weight of the waste into gripping force through the rhombic structure. Therefore, minimizing power consumption is important for automating garbage collection with battery-driven mobile manipulators. This study describes the principle of operation of the rhombic link structure of the proposed gripper and compares it with conventional motor-torque gripping. Furthermore, by incorporating a flexible structure in the form of the gripping contact area, we verified that the proposed gripper is capable of gripping and operating a total of six types of garbage depending on the size (large or small), content (bottles or cans), and material of the garbage bags. The results show that the proposed gripper uses 60% less electricity than a parallel open/close type gripper and improves the success rate of gripping large garbage bags by 20% owing to the flexible structure of the contact area.
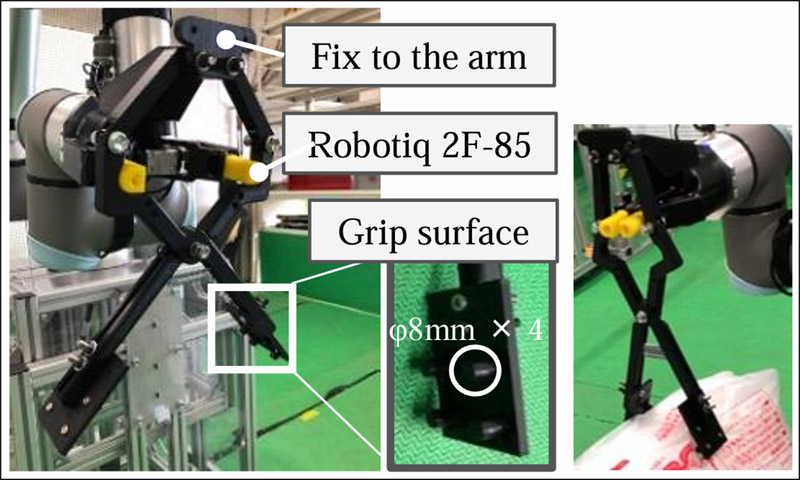
Self-weighted robotic forceps gripper for waste
- [1] M. Shishehgar, D. Kerr, and J. Blake, “The effectiveness of various robotic technologies in assisting older adults,” Health Informatics J., Vol.25, Issue 3, pp. 892-918, 2019. https://doi.org/10.1177/1460458217729729
- [2] A. Henschel, G. Laban, and E. S. Cross, “What makes a robot social? A review of social robots from science fiction to a home or hospital near you,” Curr. Robot. Rep., Vol.2, No.1, pp. 9-19, 2021. https://doi.org/10.1007/s43154-020-00035-0
- [3] E. Kojima, R. Tajima, M. Ju, M. Sato, H. Matsukami, and Y. Jimbo, “Mutual and public support system for the disposal of garbage for elderly people: Psychological factors affecting willingness to use the system,” J. of the Japan Society of Material Cycles and Waste Management, Vol.26, pp. 117-127, 2015 (in Japanese). https://doi.org/10.3985/jjsmcwm.26.117
- [4] K. Mochiduki and K. Nonaka, “Weight survey of each designated garbage bags (2014),” Annual Report of Fukuoka City Institute of Health and Environment, No.45, pp. 127-135, 2020 (in Japanese).
- [5] S. Song, D.-M. Drotlef, D. Son, A. Koivikko, and M. Sitti, “Adaptive self-sealing suction-based soft robotic gripper,” Advanced Science, Vol.8, Issue 17, Article No.2100641, 2021. https://doi.org/10.1002/advs.202100641
- [6] R. Shah, Y. Jiang, H. Karnan et al., “Solving service robot tasks: UT Austin Villa@Home 2019 team report,” arXiv preprint, arXiv:1909.06529, 2019. https://doi.org/10.48550/arXiv.1909.06529
- [7] J. Liu, P. Balatti, K. Ellis et al., “Garbage collection and sorting with a mobile manipulator using deep learning and whole-body control,” 2020 IEEE-RAS 20th Int. Conf. on Humanoid Robots, pp. 408-414, 2020. https://doi.org/10.1109/HUMANOIDS47582.2021.9555800
- [8] B. S. Zapata-Impata, V. Shah, H. Singh et al., “AutOTranS: An autonomous open world transportation system,” arXiv preprint, arXiv:1810.03400, 2018. https://doi.org/10.48550/arXiv.1810.03400
- [9] D. Bonello, M. A. Saliba, and K. P. Camilleri, “An exploratory study on the automated sorting of commingled recyclable domestic waste,” Procedia Manufacturing, Vol.11, pp. 686-694, 2017. https://doi.org/10.1016/j.promfg.2017.07.168
- [10] B. Engelen, J. R. Peeters, and K. Kellens, “Sorting of packaging waste: A framework to link gripper technologies and waste classes,” Procedia CIRP, Vol.122, pp. 725-730, 2024. https://doi.org/10.1016/j.procir.2024.01.101
- [11] D. Morrison, A. W. Tow, M. McTaggart et al., “Cartman: The low-cost Cartesian manipulator that won the amazon robotics challenge,” 2018 IEEE Int. Conf. on Robotics and Automation (ICRA), pp. 7757-7764, 2018. https://doi.org/10.1109/ICRA.2018.8463191
- [12] V. P. Dinakaran, M. P. Balasubramaniyan, Q. H. Le et al., “A novel multi objective constraints based industrial gripper design with optimized stiffness for object grasping,” Robotics and Autonomous Systems, Vol.160, Article No.104303, 2023. https://doi.org/10.1016/j.robot.2022.104303
- [13] M. Fujita, Y. Domae, A. Noda et al., “What are the important technologies for bin picking? Technology analysis of robots in competitions based on a set of performance metrics,” Advanced Robotics, Vol.34, Issues 7-8, pp. 560-574, 2020. https://doi.org/10.1080/01691864.2019.1698463
- [14] N. Correll, K. E. Bekris, D. Berenson et al., “Analysis and observations from the first Amazon picking challenge,” IEEE Trans. on Automation Science and Engineering, Vol.15, Issue 1, pp. 172-188, 2018. https://doi.org/10.1109/TASE.2016.2600527
- [15] L. Villani and J. D. Schutte, “Force Control,” Springer Handbook of Robotics. Springer, Cham, pp. 195-220, 2016. https://doi.org/10.1007/978-3-540-30301-5_8
- [16] N. Yamanobe, “Research trends of force control in robotic manipulation,” J. of the Society of Instrument and Control Engineers, Vol.56, No.10, pp. 741-746, 2017. https://doi.org/10.11499/sicejl.56.741
- [17] A. Kobayashi, J. Kinugawa, S. Arai et al., “Design and development of compactly folding parallel open-close gripper with wide stroke,” 2019 IEEE/RSJ Int. Conf. on Intelligent Robots and Systems (IROS), pp. 2408-2414, 2019. https://doi.org/10.1109/IROS40897.2019.8967838
- [18] H. Kawasaki, T. Komatsu, K. Uchiyama et al., “Dexterous anthropomorphic robot hand with distributed tactile sensor: Gifu hand II,” 1999 IEEE Int. Conf. on Systems, Man, and Cybernetics (SMC’99), Vol.2, pp. 782-787, 1999. https://doi.org/10.1109/ICSMC.1999.825361
- [19] U. Kim, D. Jung, H. Jeong et al., “Integrated linkage-driven dexterous anthropomorphic robotic hand,” Nat. Commun., Vol.12, No.7177, 2021. https://doi.org/10.1038/s41467-021-27261-0
- [20] J. Amend, N. Cheng, S. Fakhouri et al., “Soft robotics commercialization: Jamming grippers from research to product,” Soft Robotics, Vol.3, No.4, pp. 213-222, 2016. https://doi.org/10.1089/soro.2016.0021
- [21] G. D. Howard, J. Brett, J. O’Connor et al., “One-shot 3D-printed multimaterial soft robotic jamming grippers,” Soft Robotics, Vol.9, No.3, pp. 497-508, 2022. https://doi.org/10.1089/soro.2020.0154
- [22] O. Pfaff, S. Simeonov, I. Cirovic, and P. Stano, “Application of finray effect approach for production process automation,” Ann. DAAAM & Proc. of the 22nd Int. DAAAM Symp., Vol.22, No.1, pp. 1247-1248, 2011. https://doi.org/10.2507/22nd.daaam.proceedings.608
- [23] W. Crooks, S. Rozen-Levy, B. Trimmer et al., “Passive gripper inspired by Manduca sexta and the Fin Ray® Effect,” Int. J. of Advanced Robotic Systems, Vol.14, No.4, 2017. https://doi.org/10.1177/1729881417721155
- [24] W. Crooks, G. Vukasin, M. O’Sullivan et al., “Fin Ray® Effect inspired soft robotic gripper: From the robosoft grand challenge toward optimization,” Frontiers Robotics and AI, Vol.3, Article No.70, 2016. https://doi.org/10.3389/frobt.2016.00070
- [25] E. Almanzor, N. R. Anvo, T. G. Thuruthel et al., “Autonomous detection and sorting of litter using deep learning and soft robotic grippers,” Frontiers Robotics and AI, Vol.9, Article No.1064853, 2022. https://doi.org/10.3389/frobt.2022.1064853
- [26] T. Kitamura, K. Matsushita, and N. Nakatani, “Analysis of contact force and shape change on grasping a square object using an actual fin ray soft gripper,” Sensors, Vol.23, Issue 24, Article No.9827, 2023. https://doi.org/10.3390/s23249827
- [27] T. Kitamura, K. Matsushita, N. Nakatani et al., “Development and investigation of a grasping analysis system with two-axis force sensors at each of the 16 points on the object surface for a hardware-based finray-type soft gripper,” Sensors, Vol.24, Issue 15, Article No.4896, 2024. https://doi.org/10.3390/s24154896
This article is published under a Creative Commons Attribution-NoDerivatives 4.0 Internationa License.