Paper:
An Investigation Towards an Efficient Algorithm for the Automation of Stocking and Disposal Tasks in a Convenience Store Using a Robotic Arm System
Fahmi Aziz Sasono
and Kazuyoshi Wada

Graduate School of Systems Design, Tokyo Metropolitan University
6-6 Asahigaoka, Hino, Tokyo 191-0065, Japan
Robotic systems have been introduced to convenience stores to fulfill several menial tasks. One of those tasks is stocking, disposing, and arranging the product in the item rack. The general approach is to use a robotic arm to do pick-and-place tasks with the product. However, to solve this task, an appropriate algorithm is needed. In this study, we propose building an efficient algorithm for automating stocking, disposal, and arranging tasks with a robotic arm. In order to build it, a set of cost functions can be derived from the goal of stocking, disposal, and arranging processes in convenience stores. The derived cost function can then be used as a basis for creating a new algorithm that can drive the logical decisions of the system. A method to find temporary spaces within the item rack is also implemented in this algorithm. To find the most efficient form for the developed algorithm, several algorithms based on the cost function are built and tested on a simulated system of convenience store conditions. From the experiment, it is shown that, with the cost function created, using the greedy search algorithm performs the best compared to the other methods.
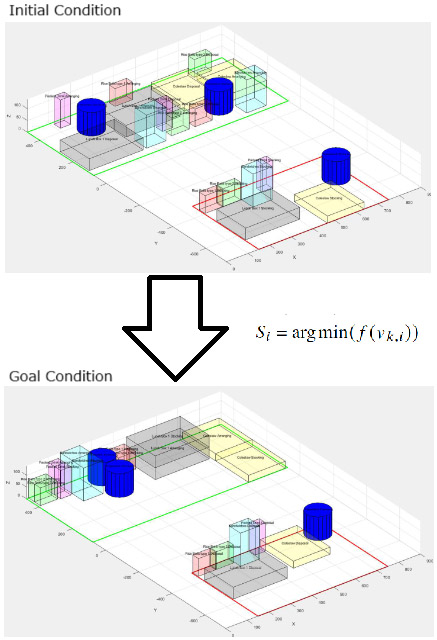
Algorithm to solve stock and disposal task
- [1] C. R. Garrett, R. Chitnis, R. Holladay, B. Kim, T. Silver, L. P. Kaelbling, and T. Lozano-Pérez, “Integrated task and motion planning,” Annual Review of Control, Robotics, and Autonomous Systems, Vol.4, pp. 265-293, 2021. https://doi.org/10.1146/annurev-control-091420-084139
- [2] M. Costanzo, G. De Maria, G. Lettera, and C. Natale, “Can robots refill a supermarket shelf?: Motion planning and grasp control,” IEEE Robotics & Automation Magazine, Vol.28, No.2, pp. 61-73, 2021. https://doi.org/10.1109/MRA.2021.3064754
- [3] T. Takubo, T. Nakamura, R. Sugiyama, and A. Ueno, “Multifunctional shelf and magnetic marker for stock and disposal tasks in convenience stores,” J. Robot. Mechatron., Vol.35, No.1, pp. 18-29, 2023. https://doi.org/10.20965/jrm.2023.p0018
- [4] S. H. Cheong, B. Y. Cho, J. Lee, C. Kim, and C. Nam, “Where to relocate?: Object rearrangement inside cluttered and confined environments for robotic manipulation,” 2020 IEEE Int. Conf. on Robotics and Automation (ICRA), pp. 7791-7797, 2020. https://doi.org/10.1109/ICRA40945.2020.9197485
- [5] H. Zhang, P. Long, D. Zhou, Z. Qian, Z. Wang, W. Wan, D. Manocha, C. Park, T. Hu, C. Cao et al., “Dorapicker: An autonomous picking system for general objects,” 2016 IEEE Int. Conf. on Automation Science and Engineering (CASE), pp. 721-726, 2016. https://doi.org/10.1109/COASE.2016.7743473
- [6] P.-C. Huang and A. K. Mok, “A case study of cyber-physical system design: Autonomous pick-and-place robot,” 2018 IEEE 24th Int. Conf. on Embedded and Real-Time Computing Systems and Applications (RTCSA), pp. 22-31, 2018. https://doi.org/10.1109/RTCSA.2018.00012
- [7] M. D. Shanthi and T. Hermans, “Pick and place planning is better than pick planning then place planning,” IEEE Robotics and Automation Letters, Vol.9, No.3, pp. 2790-2797, 2024. https://doi.org/10.1109/LRA.2024.3360892
- [8] K. Fujita and T. Tasaki, “Pynet: Poseclass and yaw angle output network for object pose estimation,” J. Robot. Mechatron., Vol.35, No.1, pp. 8-17, 2023. https://doi.org/10.20965/jrm.2023.p0008
- [9] K. Komoda, A. Sugahara, H. Nakamoto, A. Ogawa, and Y. Hatanaka, “Mobile picking-robot having wide reach area for shelves,” 2019 IEEE/SICE Int. Symp. on System Integration (SII), pp. 210-215, 2019. https://doi.org/10.1109/SII.2019.8700409
- [10] M. Seki, K. Wada, Y. Kitajima, M. Hashimoto, and T. Tomizawa, “Development of xyz stage-type display robot system for stock and disposal tasks in convenience stores,” Advanced Robotics, Vol.36, No.23, pp. 1252-1272, 2022. https://doi.org/10.1080/01691864.2022.2134736
- [11] G. Garcia Ricardez, S. Okada, N. Koganti, A. Yasuda, P. U. Eljuri, T. Sano, P.-C. Yang, L. El Hafi, M. Yamamoto, J. Takamatsu et al., “Restock and straightening system for retail automation using compliant and mobile manipulation,” Advanced Robotics, Vol.34, Nos.3-4, pp. 235-249, 2020. https://doi.org/10.1080/01691864.2019.1698460
- [12] R. Sakai, S. Katsumata, T. Miki, T. Yano, W. Wei, Y. Okadome, N. Chihara, N. Kimura, Y. Nakai, I. Matsuo, and T. Shimizu, “A mobile dual-arm manipulation robot system for stocking and disposing of items in a convenience store by using universal vacuum grippers for grasping items,” Advanced Robotics, Vol.34, Nos.3-4, pp. 219-234, 2020. https://doi.org/10.1080/01691864.2019.1705909
- [13] R. Tomikawa, Y. Ibuki, K. Kobayashi, K. Matsumoto, H. Suito, Y. Takemura, M. Suzuki, T. Tasaki, and K. Ohara, “Development of display and disposal work system for convenience stores using dual-arm robot,” Advanced Robotics, Vol.36, No.23, pp. 1273-1290, 2022. https://doi.org/10.1080/01691864.2022.2136503
- [14] M. Katayama, S. Tokuda, M. Yamakita, and H. Oyama, “Fast ltl-based flexible planning for dual-arm manipulation,” 2020 IEEE/RSJ Int. Conf. on Intelligent Robots and Systems (IROS), pp. 6605-6612, 2020. https://doi.org/10.1109/IROS45743.2020.9341352
- [15] P. M. U. Eljuri, G. A. G. Ricardez, N. Koganti, J. Takamatsu, and T. Ogasawara, “Rearranging tasks in daily-life environments using a monte carlo tree search and a feasibility database,” 2021 IEEE/SICE Int. Symp. on System Integration (SII), pp. 330-335, 2021. https://doi.org/10.1109/IEEECONF49454.2021.9382688
- [16] P. M. U. Eljuri, L. El Hafi, G. A. Garcia Ricardez, A. Taniguchi, and T. Taniguchi, “Neural network-based motion feasibility checker to validate instructions in rearrangement tasks before execution by robots,” 2022 IEEE/SICE Int. Symp. on System Integration (SII), pp. 1058-1063, 2022. https://doi.org/10.1109/SII52469.2022.9708602
- [17] C.-Y. Su, H.-C. Wang, C.-H. Ko, and K.-Y. Young, “Development of an autonomous robot replenishment system for convenience stores,” Electronics, Vol.12, No.8, Article No.1940, 2023. https://doi.org/10.3390/electronics12081940
- [18] H. Premachandra, H. Herath, M. Suriyage, K. Thathsarana, Y. Amarasinghe, R. Gopura, and S. Nanayakkara, “Genetic algorithm based pick and place sequence optimization for a color and size sorting delta robot,” 2020 6th Int. Conf. on Control, Automation and Robotics (ICCAR), pp. 209-213, 2020. https://doi.org/10.1109/ICCAR49639.2020.9108045
- [19] C. Nam, J. Lee, S. H. Cheong, B. Y. Cho, and C. Kim, “Fast and resilient manipulation planning for target retrieval in clutter,” 2020 IEEE Int. Conf. on Robotics and Automation (ICRA), pp. 3777-3783, 2020. https://doi.org/10.1109/ICRA40945.2020.9196652
- [20] D. Saxena and M. Likhachev, “Manipulation among movable objects for pick-and-place tasks in 3d workspaces,” IROS 2023 Workshop on Leveraging Models for Contact-Rich Manipulation, 2023.
- [21] J. Ahn, C. Kim, and C. Nam, “Coordination of two robotic manipulators for object retrieval in clutter,” 2022 Int. Conf. on Robotics and Automation (ICRA), pp. 1039-1045, 2022. https://doi.org/10.1109/ICRA46639.2022.9811978
- [22] A. Vince, “A framework for the greedy algorithm,” Discrete Applied Mathematics, Vol.121, Nos.1-3, pp. 247-260, 2002. https://doi.org/10.1016/S0166-218X(01)00362-6
- [23] C. Wilt, J. Thayer, and W. Ruml, “A comparison of greedy search algorithms,” Proc. of the Int. Symp. on Combinatorial Search, Vol.1, No.1, pp. 129-136, 2010. https://doi.org/10.1609/socs.v1i1.18182
- [24] A. Candra, M. A. Budiman, and K. Hartanto, “Dijkstra’s and a-star in finding the shortest path: a tutorial,” 2020 Int. Conf. on Data Science, Artificial Intelligence, and Business Analytics (DATABIA), pp. 28-32, 2020. https://doi.org/10.1109/DATABIA50434.2020.9190342
- [25] M. Heusner, T. Keller, and M. Helmert, “Understanding the search behaviour of greedy best-first search,” Proc. of the Int. Symp. on Combinatorial Search, Vol.8, No.1, pp. 47-55, 2017. https://doi.org/10.1609/socs.v8i1.18425
- [26] D. E. Golberg, “Genetic Algorithms in Search, Optimization, and Machine Learning,” Addion Wesley, 1989.
- [27] W. Hui, “Comparison of several intelligent algorithms for solving tsp problem in industrial engineering,” Systems Engineering Procedia, Vol.4, pp. 226-235, 2012. https://doi.org/10.1016/j.sepro.2011.11.070
- [28] S. Katoch, S. S. Chauhan, and V. Kumar, “A review on genetic algorithm: past, present, and future,” Multimedia Tools and Applications, Vol.80, pp. 8091-8126, 2021. https://doi.org/10.1007/s11042-020-10139-6
- [29] K. Wada, “New robot technology challenge for convenience store,” 2017 IEEE/SICE Int. Symp. on System Integration (SII), pp. 1086-1091, 2017. https://doi.org/10.1109/SII.2017.8279367
This article is published under a Creative Commons Attribution-NoDerivatives 4.0 Internationa License.