Paper:
Two-Joint Robotic Unit Fabricated by the Robot Packaging Method
Hiroki Nishiyama and Mizuho Shibata

Kindai University
1 Takaya Umenobe, Higashi-Hiroshima, Hiroshima 739-2116, Japan
A two-joint robotic unit was developed to perform various tasks using a single unit. The unit is covered with a flexible plastic film and an insulating fluid, which makes it waterproof. A flexible film may limit the range of motion of a robotic unit. The robot packaging method, which is a method of packaging the internal components of a robot using the vacuum packaging technique, is used for plastic film covering. The effects of the film and the insulating fluid were experimentally clarified. Robot fingers, fish-like robots, and crawling robots were considered as application examples of the proposed robotic unit. These examples demonstrate that the robotic unit can work in contact with objects and in water.
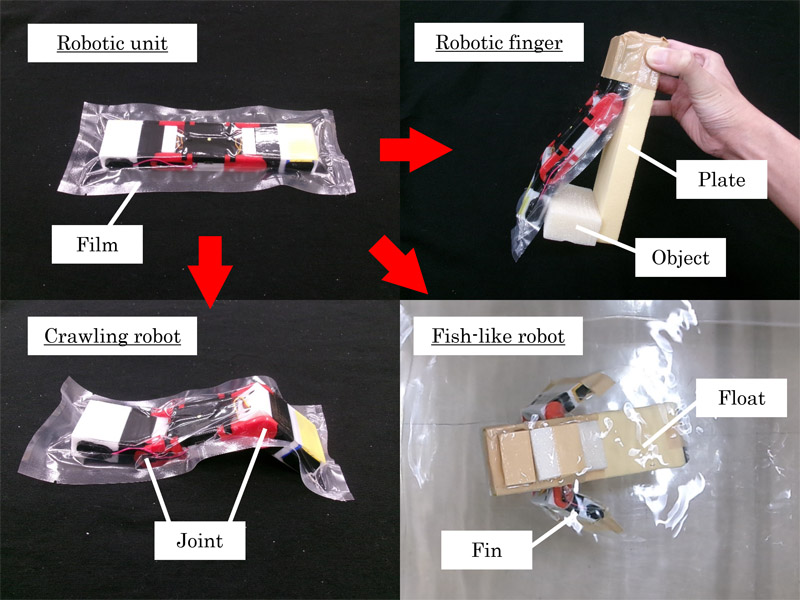
Two-joint robotic unit fabricated by the robot packaging method
- [1] M. Shibata and N. Sakagami, “Fabrication of a fish-like underwater robot with flexible plastic film body,” Advanced Robotics, Vol.29, No.1, pp. 103-113, 2015. https://doi.org/10.1080/01691864.2014.944213
- [2] M. Shibata, “Chapter 11: Fish-like robot encapsulated by a plastic film,” G. Weng (Ed.), “Recent Advances in Robotic Systems,” pp. 235-251, InTechOpen, 2016. https://doi.org/10.5772/63506
- [3] A. Pamecha, I. Ebert-Uphoff, and G. S. Chirikjian, “Useful metrics for modular robot motion planning,” IEEE Trans. on Robotics and Automation, Vol.13, No.4, pp. 531-545, 1997. https://doi.org/10.1109/70.611311
- [4] M. Yim et al., “Modular self-reconfigurable robot systems [grand challenges of robotics],” IEEE Robotics & Automation Magazine, Vol.14, No.1, pp. 43-52, 2007. https://doi.org/10.1109/MRA.2007.339623
- [5] M. Yim, D. G. Duff, and K. D. Roufas, “PolyBot: A modular reconfigurable robot,” 2000 IEEE Int. Conf. on Robotics and Automation (ICRA), Vol.1, pp. 514-520, 2000. https://doi.org/10.1109/ROBOT.2000.844106
- [6] M. Yim, Y. Zhang, and D. Duff, “Modular robots,” IEEE Spectrum, Vol.39, No.2, pp. 30-34, 2002. https://doi.org/10.1109/6.981854
- [7] S. Murata et al., “M-TRAN: Self-reconfigurable modular robotic system,” IEEE/ASME Trans. on Mechatronics, Vol.7, No.4, pp. 431-441, 2002. https://doi.org/10.1109/TMECH.2002.806220
- [8] A. Kamimura et al., “Automatic locomotion design and experiments for a modular robotic system,” IEEE/ASME Trans. on Mechatronics, Vol.10, No.3, pp. 314-325, 2005. https://doi.org/10.1109/TMECH.2005.848299
- [9] W.-M. Shen, B. Salemi, and P. Will, “Hormone-inspired adaptive communication and distributed control for CONRO self-reconfigurable robots,” IEEE Trans. on Robotics and Automation, Vol.18, No.5, pp. 700-712, 2002. https://doi.org/10.1109/TRA.2002.804502
- [10] M. Shimizu, T. Kato, M. Lungarella, and A. Ishiguro, “Adaptive modular robots through heterogeneous inter-module connections,” J. Robot. Mechatron., Vol.20, No.3, pp. 386-393, 2008. https://doi.org/10.20965/jrm.2008.p0386
- [11] S. Odem and O. Medina, “A self-reconfiguration algorithm for sliding triangular modular robots,” IEEE Robotics and Automation Letters, Vol.9, No.3, pp. 2216-2223, 2024. https://doi.org/10.1109/LRA.2024.3355756
- [12] J. W. Romanishin, K. Gilpin, and D. Rus, “M-blocks: Momentum-driven, magnetic modular robots,” 2013 IEEE/RSJ Int. Conf. on Intelligent Robots and Systems, pp. 4288-4295, 2013. https://doi.org/10.1109/IROS.2013.6696971
- [13] C. S. S. Reddy, S. Patlolla, A. Agrawal, and K. R. Anupama, “SQ-BOT—A modular robot prototype for self-reconfiguring structures,” 2016 Int. Conf. on Robotics: Current Trends and Future Challenges (RCTFC), 2016. https://doi.org/10.1109/RCTFC.2016.7893408
- [14] Y. Morooka and I. Mizuuchi, “Gravity compensation modular robot: Proposal and prototyping,” J. Robot. Mechatron., Vol.31, No.5, pp. 697-706, 2019. https://doi.org/10.20965/jrm.2019.p0697
- [15] S. Yu, Y. Nakata, Y. Nakamura, and H. Ishiguro, “Inter-module physical interactions: A force-transmissive modular structure for whole-body robot motion,” J. Robot. Mechatron., Vol.33, No.5, pp. 1190-1203, 2021. https://doi.org/10.20965/jrm.2021.p1190
- [16] J. Chen, T. Chen, and Z. Deng, “Design method of modular units for articulated in-pipe robot inspecting system,” 2011 2nd Int. Conf. on Digital Manufacturing & Automation, pp. 389-392, 2011. https://doi.org/10.1109/ICDMA.2011.102
- [17] C. Wright et al., “Design and architecture of the unified modular snake robot,” 2012 IEEE Int. Conf. on Robotics and Automation, pp. 4347-4354, 2012. https://doi.org/10.1109/ICRA.2012.6225255
- [18] B. S. Homberg, R. K. Katzschmann, M. R. Dogar, and D. Rus, “Haptic identification of objects using a modular soft robotic gripper,” 2015 IEEE/RSJ Int. Conf. on Intelligent Robots and Systems, pp. 1698-1705, 2015. https://doi.org/10.1109/IROS.2015.7353596
- [19] H. Huang et al., “MCSG: A morphology configurable soft gripper with self-adaption modular composite finger,” IEEE Trans. on Industrial Electronics, Vol.71, No.1, pp. 708-717, 2024. https://doi.org/10.1109/TIE.2023.3243294
- [20] M. Hutter et al., “ANYmal—A highly mobile and dynamic quadrupedal robot,” 2016 IEEE/RSJ Int. Conf. on Intelligent Robots and Systems, pp. 38-44, 2016. https://doi.org/10.1109/IROS.2016.7758092
- [21] Y. H. Lee et al., “Development of a quadruped robot system with torque-controllable modular actuator unit,” IEEE Trans. on Industrial Electronics, Vol.68, No.8, pp. 7263-7273, 2021. https://doi.org/10.1109/TIE.2020.3007084
- [22] J. C. Romão, M. Tavakoli, C. Viegas, P. Neto, and A. T. de Almeida, “InchwormClimber: A light-weight biped climbing robot with a switchable magnet adhesion unit,” 2015 IEEE/RSJ Int. Conf. on Intelligent Robots and Systems, pp. 3320-3325, 2015. https://doi.org/10.1109/IROS.2015.7353839
- [23] H. Lu et al., “Controllable mobile adhesion integration unit for flexible magnetic adhesion robot,” 49th Annual Conf. of the IEEE Industrial Electronics Society (IECON 2023), 2023. https://doi.org/10.1109/IECON51785.2023.10312363
- [24] H. Qian et al., “Leveraging the efficiency of multi-task robot manipulation via task-evoked planner and reinforcement learning,” 2024 IEEE Int. Conf. on Robotics and Automation (ICRA), pp. 9220-9226, 2024. https://doi.org/10.1109/ICRA57147.2024.10611076
- [25] J. Baca, M. Ferre, A. Campos, J. Fernandez, and R. Aracil, “On the analysis of a multi-task modular robot system for field robotics,” 2010 IEEE Electronics, Robotics and Automotive Mechanics Conf., pp. 475-480, 2010. https://doi.org/10.1109/CERMA.2010.60
- [26] M. G. B. Atia, A. Mohammad, A. Gameros, D. Axinte, and I. Wright, “Reconfigurable soft robots by building blocks,” Advanced Science, Vol.9, No.33, Article No.2203217, 2022. https://doi.org/10.1002/advs.202203217
- [27] T. Anzai, Y. Kojio, T. Makabe, K. Okada, and M. Inaba, “Design and development of a flying humanoid robot platform with bi-copter flight unit,” 2020 IEEE-RAS 20th Int. Conf. on Humanoid Robots (Humanoids), pp. 69-75, 2021. https://doi.org/10.1109/HUMANOIDS47582.2021.9555801
- [28] M. Rude, K. Hirahara, and S. Yuta, “Collisions need not be dangerous for elliptical and flexible vehicles,” 1997 IEEE Int. Conf. on Intelligent Processing Systems, Vol.2, pp. 1277-1281, 1997. https://doi.org/10.1109/ICIPS.1997.669203
- [29] B. Cho et al., “Design of a compact embedded hydraulic power unit for bipedal robots,” IEEE Robotics and Automation Letters, Vol.6, No.2, pp. 3631-3638, 2021. https://doi.org/10.1109/LRA.2021.3061390
- [30] C. J. Salaan et al., “Development and experimental validation of aerial vehicle with passive rotating shell on each rotor,” IEEE Robotics and Automation Letters, Vol.4, No.3, pp. 2568-2575, 2019. https://doi.org/10.1109/LRA.2019.2894903
- [31] L. G. Librado, C. Y. Cahig, C. A. G. Banglos, J. C. Pao, and C. J. O. Salaan, “Meshing and insulation strategies for shelled UAVs in proximal inspection of distribution utility lines,” IEEE Robotics and Automation Letters, Vol.7, No.2, pp. 5278-5285, 2022. https://doi.org/10.1109/LRA.2022.3155227
- [32] B. A. N. Campos and J. M. S. T. Motta, “Online measuring of robot positions using inertial measurement units, sensor fusion and artificial intelligence,” IEEE Access, Vol.9, pp. 5678-5689, 2021. https://doi.org/10.1109/ACCESS.2020.3048877
- [33] H. Nishiyama and M. Shibata, “Development of robot unit packaged with a flexible plastic film,” Proc. of 2023 JSME Annual Conf. on Robotics and Mechatronics, Article No.1A1-C11, 2023 (in Japanese). https://doi.org/10.1299/jsmermd.2023.1A1-C11
- [34] R. Ahvenainen (Ed.), “Novel Food Packaging Techniques,” Woodhead Publishing, 2003.
- [35] S. Imai, H. Mizoguchi, and E. Inagakii, “Proposition of new control method of eel-like swimming robot for swimming in narrow water ways,” 2008 10th Int. Conf. on Control, Automation, Robotics and Vision, pp. 681-684, 2008. https://doi.org/10.1109/ICARCV.2008.4795599
- [36] M. Shibata and N. Sakagami, “A robot fish encapsulated by an electromagnetic wave-transmitting plastic film,” 41st Annual Conf. of the IEEE Industrial Electronics Society (IECON 2015), pp. 2729-2734, 2015. https://doi.org/10.1109/IECON.2015.7392514
- [37] M. Shibata and N. Sakagami, “Development of pressure measurement equipment fabricated by robot packaging method,” 2021 IEEE/SICE Int. Symp. on System Integration (SII), pp. 263-269, 2021.
This article is published under a Creative Commons Attribution-NoDerivatives 4.0 Internationa License.