Paper:
Development of Mobility Type Upper Limb Power Assist System —Mechanism and Design of Power Assist Device—
Hiroyuki Inoue* and Hiroshi Shimura**
*Department of Integrated Science and Technology, National Institute of Technology, Tsuyama College
624-1 Numa, Tsuyama, Okayama 708-8509, Japan
**Ricoh Company, Ltd.
2-7-1 Izumi, Ebina, Kanagawa 243-0460, Japan
In fruit cultivation, viticulture requires the longest working hours in extended arm postures, much of which is carried out in standing postures to accumulate fatigue on arms, shoulders, and legs: a tough working environment. In this study, we propose a power assist system to assist its users in their extended arm work while they move in vineyards. The proposed system largely consists of a mobile robot, a power assist device for work, and a control system. The mobile robot is structured with a tracked vehicle for rough terrain arranged on its left and right sides so that the users can sit between the two vehicles and be assisted by the power assist device for work installed on it. The power assist device for work with a single linear actuator utilizing a linkage mechanism has the function to retain users’ hand attitude angles while assisting the flexion and extension movements of their shoulder, elbow, and carpometacarpal joints. Then, we verify by simulations the effects that the arrangement and lengths of links will have on the carpometacarpal joints’ trajectories as well as on the hand attitude angles. Finally, in order to check the effectiveness of the proposed power assist device for work, we conducted the evaluation experiments for assumed grape-harvesting work and gibberellin treatments. As a result, we proved its work assisting effects from the muscle activity states as well as its applicability to other kinds of work by altering its linkage structure and hand support part.
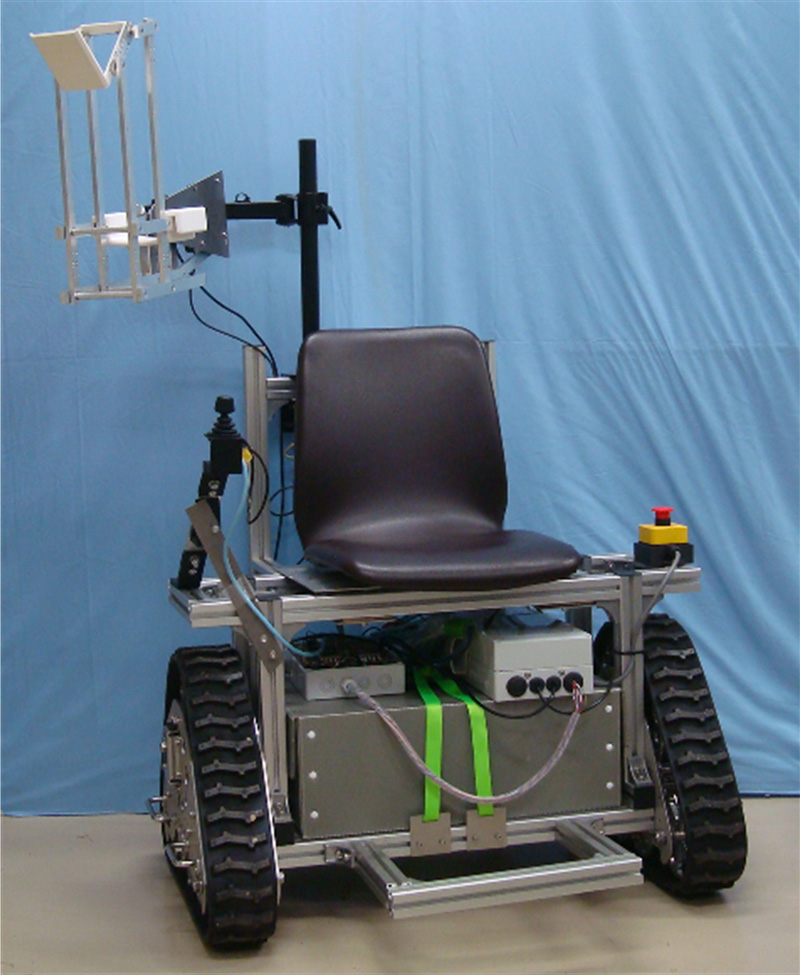
Mobility type upper limb power assist system
- [1] M. Ishii, K. Yamamoto, and K. Hyodo, “Stand-Alone Wearable Power Assist Suit –Development and Availability–,” J. Robot. Mechatron., Vol.17, No.5, pp. 575-583, 2005. https://doi.org/10.20965/jrm.2005.p0575
- [2] H. Kobayashi, T. Aida, and T. Hashimoto, “Muscle Suit Development and Factory Application,” Int. J. Automation Technol., Vol.3, No.6, pp. 709-715, 2009. https://doi.org/10.20965/ijat.2009.p0709
- [3] H. Kobayashi, T. Shiiba, and Y. Ishida, “Realization of All 7 Motions for the Upper Limb by a Muscle Suit,” J. Robot. Mechatron., Vol.16, No.5, pp. 504-512, 2004. https://doi.org/10.20965/jrm.2004.p0504
- [4] K. Kiguchi, R. Esaki, and T. Fukuda, “Development of a Wearable Exoskeleton for Daily Forearm Motion Assist,” Advanced Robotics, Vol.19, No.7, pp. 751-771, 2005. https://doi.org/10.1163/1568553054455086
- [5] J. C. Perry, J. Rosen, and S. Burns, “Upper-Limb Powered Exoskeleton Design,” IEEE/ASME Trans. on Mechatronics, Vol.12, No.4, pp. 408-417, 2007. https://doi.org/10.1109/TMECH.2007.901934
- [6] E. Yagi, D. Harada, and M. Kobayashi, “Development of an Upper Limb Power Assist System Using Pneumatic Actuators for Farming Lift-Up Motion,” J. of System Design and Dynamics, Vol.3, No.5, pp. 781-791, 2009. https://doi.org/10.1299/jsdd.3.781
- [7] E. Yagi, D. Harada, and M. Kobayashi, “Upper-Limb Power-Assist Control for Agriculture Load Lifting,” Int. J. Automation Technol., Vol.3, No.6, pp. 716-722, 2009. https://doi.org/10.20965/ijat.2009.p0716
- [8] K. Miyawaki, “Link Type Arm Support Equipment,” J. Robot. Mechatron., Vol.27, No.1, pp. 110-111, 2015. https://doi.org/10.20965/jrm.2015.p0110
- [9] T. Kosaki and S. Li, “A Water-Hydraulic Upper-Limb Assistive Exoskeleton System with Displacement Estimation,” J. Robot. Mechatron., Vol.32, No.1, pp. 149-156, 2020. https://doi.org/10.20965/jrm.2020.p0149
- [10] K. Sano, E. Yagi, and M. Sato, “Development of a Wearable Assist Suit for Walking and Lifting-Up Motion Using Electric Motors,” J. Robot. Mechatron., Vol.25, No.6, pp. 923-930, 2013. https://doi.org/10.20965/jrm.2013.p0923
- [11] K. Nomura, T. Yonezawa, H. Takemura, and H. Mizoguchi, “Development of Six-DOF Human Ankle Motion Control Device Using Stewart Platform Structure for Fall Prevention,” J. Robot. Mechatron., Vol.28, No.5, pp. 654-663, 2016. https://doi.org/10.20965/jrm.2016.p0654
- [12] Y. Naruoka, N. Hiramitsu, and Y. Mitsuya, “A Study of Power-Assist Technology to Reduce Body Burden During Loading and Unloading Operations by Support of Knee Joint Motion,” J. Robot. Mechatron., Vol.28, No.6, pp. 949-957, 2016. https://doi.org/10.20965/jrm.2016.p0949
- [13] M. Kashima, H. Arakawa, S. Kimura, R. Nishihama, K. Yokoyama, I. Kikutani, and T. Nakamura, “Development of Assist Suit for Squat Lifting Support Considering Gait and Quantitative Evaluation by Three-Dimensional Motion Analysis,” J. Robot. Mechatron., Vol.32, No.1, pp. 209-219, 2020. https://doi.org/10.20965/jrm.2020.p0209
- [14] S. Kimura, R. Suzuki, K. Machida, R. Nishihama, M. Okui, and T. Nakamura, “Proposal of Motion Judgment Algorithm Based on Joint Angle of Variable Elastic Assist Suit with High Back Drivability,” J. Robot. Mechatron., Vol.32, No.5, pp. 863-875, 2020. https://doi.org/10.20965/jrm.2020.p0863
- [15] K. Uchiyama, T. Ito, and H. Tomori, “Development of Endoskeleton Type Knee Joint Assist Orthosis Using McKibben Type Artificial Muscle,” J. Robot. Mechatron., Vol.34, No.2, pp. 390-401, 2022. https://doi.org/10.20965/jrm.2022.p0390
- [16] H. Inoue and T. Noritsugu, “Development of Upper-Limb Power Assist Machine Using Linkage Mechanism – Drive Mechanism and its Applications –,” J. Robot. Mechatron., Vol.30, No.2, pp. 214-222, 2018. https://doi.org/10.20965/jrm.2018.p0214
- [17] T. Keller and J. Arvidsson, “A Model for Prediction of Vertical Stress Distribution near the Soil Surface Below Rubber-Tracked Undercarriage Systems Fitted on Agricultural Vehicles,” Soil and Tillage Research, Vol.155, pp. 116-123, 2016. https://doi.org/10.1016/j.still.2015.07.014
- [18] H. Shimura and A. Kawaguchi, “Tracked Vehicle for Rough Terrain,” Proc. of the 2017 JSME Conf. on Robotics and Mechatronics, Session ID 1P2-C12, 2017 (in Japanese). https://doi.org/10.1299/jsmermd.2017.1P2-C12
- [19] H. Shimura, H. Okamoto, T. Kitahara, and R. Yamashina, “Report on the Load Carrying Robot Using the Tracked Vehicle,” Proc. of the 2021 JSME Conf. on Robotics and Mechatronics, Session ID 2P1-J07, 2021 (in Japanese). https://doi.org/10.1299/jsmermd.2021.2P1-J07
This article is published under a Creative Commons Attribution-NoDerivatives 4.0 Internationa License.