Paper:
Development of Pneumatic Artificial Rubber Muscle Using Segmented Shape-Memory Polymer Sheets
Kazuto Takashima*, Yuta Okamura*, Daiki Iwamoto*, Toshiro Noritsugu**, and Toshiharu Mukai***
*Graduate School of Life Science and Systems Engineering, Kyushu Institute of Technology
2-4 Hibikino, Wakamatsu-ku, Kitakyushu 808-0196, Japan
**Mimasaka University
50 Kitazonocho, Tsuyama 708-8511, Japan
***Department of Information Engineering, Faculty of Information Engineering, Meijo University
1-501 Shiogamaguchi, Tenpaku-ku, Nagoya 468-8502, Japan
We have developed a pneumatic artificial rubber muscle using two shape-memory polymer (SMP) sheets. We attached the SMP sheets to a linear pneumatic artificial rubber muscle. Utilizing the large difference in the elastic modulus below and above the glass transition temperature, the shape fixity and shape recovery of SMPs, the bending direction and the initial shape can be changed. In this study, in order to increase the bending motion range, we developed a segmented SMP sheet with embedded electrical heating wires, and evaluated its mechanical properties using bending and tensile tests. Moreover, we attached such sheets to an artificial muscle and evaluated the bending motion. Bending tests showed that segmenting the SMP sheets greatly reduced their bending stiffness. In tensile tests at temperatures below the glass transition temperature, it was found that the artificial muscle with the attached sheet withstood high elongating loads without failure. Attachment of such segmented SMP sheets to an artificial muscle resulted in an increased bending angle. Through isotonic and isometric tests, we showed that the prototype actuator could bend in two directions.
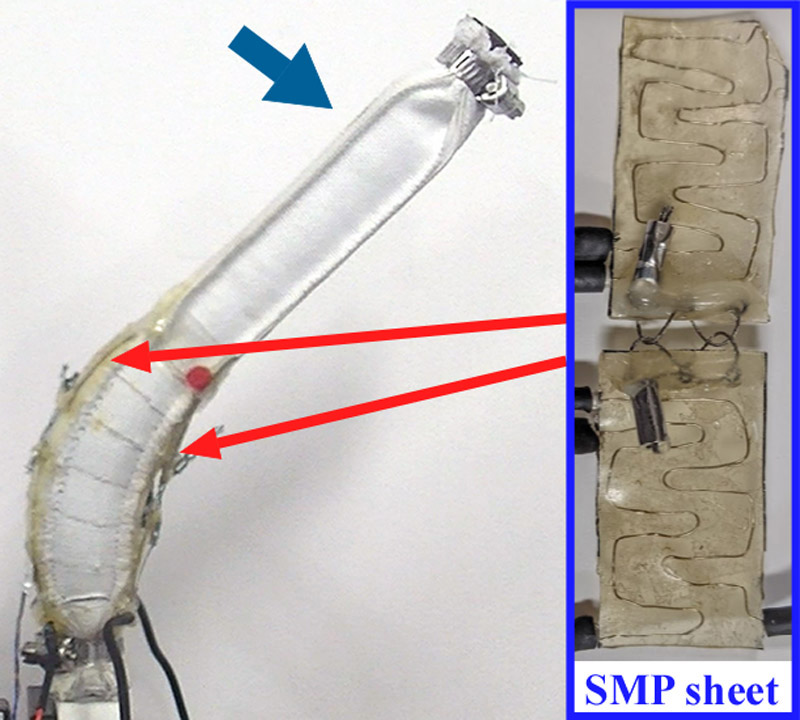
Pneumatic actuator using segmented SMP sheets
- [1] J. Leng, X. Lan, Y. Liu, and S. Du, “Shape-memory polymers and their composites: Stimulus methods and applications,” Prog. Mater. Sci., Vol.56, pp. 1077-1135, 2011. https://doi.org/10.1016/j.pmatsci.2011.03.001
- [2] J. Shintake, V. Cacucciolo, D. Floreano, and H. Shea, “Soft robotic grippers,” Adv. Mater., Vol.30, Article No.1707035, 2018. https://doi.org/10.1002/adma.201707035
- [3] T. Liao, M. S. Kalairaj, C. J. Cai, Z. T. H. Tse, and H. Ren, “Fully-printable soft actuator with variable stiffness by phase transition and hydraulic regulations,” Actuators, Vol.10, Article No.269, 2021. https://doi.org/10.3390/ACT10100269
- [4] S. Yahara, S. Wakimoto, T. Kanda, and K. Matsushita, “McKibben artificial muscle realizing variable contraction characteristics using helical shape-memory polymer fibers,” Sensors and Actuators: A Physical, Vol.295, pp. 637-642, 2019. https://doi.org/10.1016/j.sna.2019.06.012
- [5] Y. An and H. Okuzaki, “Novel electro-active shape memory polymers for soft actuators,” Jpn. J. Appl. Phys., Vol.59, Article No.061002, 2020. https://doi.org/10.35848/1347-4065/ab8e08
- [6] K. Takashima, T. Noritsugu, J. Rossiter, S. Guo, and T. Mukai, “Curved type pneumatic artificial rubber muscle using shape-memory polymer,” J. Robot. Mechatron., Vol.24, No.3, pp. 472-479, 2012. https://doi.org/10.20965/jrm.2012.p0472
- [7] K. Takashima, K. Sugitani, N. Morimoto, S. Sakaguchi, T. Noritsugu, and T. Mukai, “Pneumatic artificial rubber muscle using shape-memory polymer sheet with embedded electrical heating wire,” Smart Mater. Struct., Vol.23, No.12, Article No.125005, 2014. https://doi.org/10.1088/0964-1726/23/12/125005
- [8] K. Takashima, D. Iwamoto, S. Oshiro, T. Noritsugu, and T. Mukai, “Characteristics of pneumatic artificial rubber muscle using two shape-memory polymer sheets,” J. Robot. Mechatron., Vol.33, No.3, pp. 653-664, 2021. https://doi.org/10.20965/jrm.2021.p0653
- [9] K. Takashima, J. Kobuchi, N. Kamamichi, K. Takagi, and T. Mukai, “Characterization of variable-sensitivity force sensor using stiffness change of shape-memory polymer based on temperature,” ROBOMECH J., Vol.8, Article No.24, 2021. https://doi.org/10.1186/S40648-021-00210-8
- [10] K. Takashima, T. Imazawa, and H. Cho, “Variable-stiffness and deformable link using shape-memory material and jamming transition phenomenon,” J. Robot. Mechatron., Vol.34, No.2, pp. 466-477, 2022. https://doi.org/10.20965/jrm.2022.p0466
- [11] K. Takashima, J. Rossiter, and T. Mukai, “McKibben artificial muscle using shape-memory polymer,” Sensors & Actuators: A Physical, Vol.164, pp. 116-124, 2010. https://doi.org/10.1016/j.sna.2010.09.010
- [12] H. Meng, H. Mohamadian, M. Stubblefield, D. Jerro, S. Ibekwe, S.-S. Pang, and G. Li, “Various shape memory effects of stimuli-responsive shape memory polymers,” Smart Mater. Struct., Vol.22, No.9, Article No.093001, 2013. https://doi.org/10.1088/0964-1726/22/9/093001
- [13] Q. Ge, C. K. Dunn, H. J. Qi, and M. L. Dunn, “Active origami by 4D printing,” Smart Mater. Struct., Vol.23, No.9, Article No.094007, 2014. https://doi.org/10.1088/0964-1726/23/9/094007
- [14] Y. Wang, J. Wang, and X. Peng, “Refinement of a 3D finite strain viscoelastic constitutive model for thermally induced shape memory polymers,” Polym. Test., Vol.96, Article No.107139, 2021. https://doi.org/10.1016/j.polymertesting.2021.107139
- [15] K. Takashima, R. Miyazaki, and T. Mukai, “Surface shape changeable tactile sensor using shape-memory polymer,” Proc. of the SICE Annual Conf. 2021, pp. 1166-1171, 2021.
- [16] T. Higuchi, K. Suzumori, and S. Tadokoro (Eds.), “Next-generation actuators leading breakthroughs,” Springer, 2010.
- [17] Y. Kadowaki, T. Noritsugu, M. Takaiwa, D. Sasaki, and M. Kato, “Development of soft power-assist glove and control based on human intent,” J. Robot. Mechatron., Vol.23, No.2, pp. 281-291, 2011. https://doi.org/10.20965/jrm.2011.p0281
This article is published under a Creative Commons Attribution-NoDerivatives 4.0 Internationa License.