Paper:
Micro Flow Control Valve with Stable Condition Using Particle-Excitation
Daisuke Hirooka, Naomichi Furushiro, and Tomomi Yamaguchi
Deportment of Mechanical Engineering, Kansai University
3-3-35 Yamate-cho, Suita-shi, Osaka 564-8680, Japan
This paper proposes a drive principle that aims to improve the control characteristics of a particle-excitation flow control valve capable of continuous air flow control. Aiming at application to a small servo valve, the authors have developed a particle-excitation flow control valve that controls flow rate by separating particles, which act as a valve element, from an orifice that is opened by the oscillation of a piezoelectric element. This paper proposes a method of more finely adjusting the motion of the particles. This method makes it possible to adjust to what degree each orifice opens, thereby refining the control of the flow rate and improving the responsiveness of the valve. Here, the authors produce a prototype, evaluate its characteristics, and confirm its effectiveness.
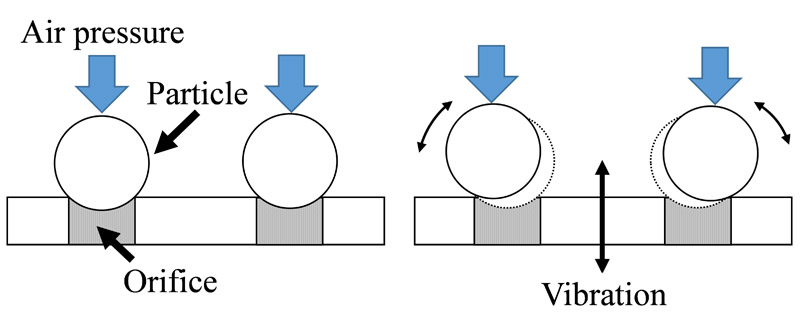
Basic working principle of micro flow control valve using particle-excitation
- [1] K. Suzumori, “Soft Robotics seen from Actuator Technology,” J. of the Robotics Society of Japan, Vol.37, No.1, pp. 26-29, 2019 (in Japanese).
- [2] S. Kurumaya, H. Nabae, G. Endo, and K. Suzumori, “Design of Thin McKibben Muscle and Multifilament Structure,” Sensors and Actuators A: Physical, Vol.261, pp. 66-74, 2017.
- [3] Z. Wang, Y. Makiyama, and S. Hirai, “A Soft Needle Gripper Capable of Grasping and Piercing for Handling Food Materials,” J. Robot. Mechatron., Vol.33, No.4, pp. 935-943, doi: 10.20965/jrm.2021.p0935, 2021.
- [4] J. Tanaka and N. Matsuhira, “Disposable Robotic Finger Driven Pneumatically by Flat Tubes and a Hollow Link Mechanism,” J. Robot. Mechatron., Vol.32, No.5, pp. 958-976, doi: 10.20965/jrm.2020.p0958, 2020.
- [5] Z. Wu, X. Li, and Z. Guo, “A Novel Pneumatic Soft Gripper with a Jointed Endoskeleton Structure,” Chinese J. of Mechanical Engineering, Vol.32, Article No.78, 2019.
- [6] A. Kojima, M. Okui, and T. Nakamura, “Development of Soft Pneumatic Actuators Using High-Strain Elastic Materials with Stress Anisotropy of Short Fibers,” Proc. of the 1st Int. Electronic Conf. on Actuator Technology: Materials, Devices and Applications, Article No.41, 2020.
- [7] S. Jien, S. Hirai, and K. Honda, “Miniaturization Design of Piezoelectric Vibration-Driven Pneumatic Unconstrained Valves,” J. Robot. Mechatron., Vol.22, No.1, pp. 91-99, doi: 10.20965/jrm.2010.p0091, 2010.
- [8] T. Akagi, S. Dohta, and S. Katayama, “Development of Small-sized Flexible Control Valve Using Vibration Motor,” Proc. of the 7th JFPS Int. Symp. on Fluid Power 2008, pp. 725-730, 2008.
- [9] Y. Miyaki and H. Tsukagoshi, “Soft simple compact valve inducing self-excited vibration aimed for mobile robots unnecessary for electricity,” 2018 IEEE/ASME Int. Conf. on Advanced Intelligent Mechatronics (AIM), pp. 670-675, 2018.
- [10] T. Takayama and Y. Sumi, “Self-excited air flow passage changing device for periodic pressurization of soft robot,” Robomech J., Vol.8, Article No.20, 2021.
- [11] T. Kobayashi, T. Akagi, S. Dohta, T. Shinohara, and S. Shimooka, “Development of Small-sized Servo Valve using Gate Mechanism and Diaphragm,” JFPS Int. J. of Fluid Power System, Vol.14, No.1, pp. 1-9, 2021.
- [12] T. Kanno, T. Hasegawa, T. Miyazaki, N. Yamamoto, D. Haraguchi, and K. Kawashima, “Development of a Poppet-Type Pneumatic Servo Valve,” Applied Science, Vol.8, Article No.2094, 2018.
- [13] Y. Ishida and K. Tadano, “Development of a Pinch-type Pneumatic Servo Valve,” Trans. of the Japan Fluid Power System Society, Vol.48, No.1, pp. 1-7, 2017 (in Japanese).
- [14] D. Hirooka, K. Suzumori, and T. Kanda, “Flow control valve for pneumatic actuators using particle excitation by PZT vibrator,” Sensors and Actuators A: Physical, Vol.155, pp. 285-289, 2009.
- [15] D. Hirooka, K. Suzumori, and T. Kanda, “Design and Evaluation of Orifice Arrangement for Particle-Excitation Flow Control Valve,” Sensors and Actuators A: Physical, Vol.171, No.2, pp. 283-291, 2011.
- [16] D. Hirooka, T. Yamaguchi, N. Furushiro, K. Suzumori, and T. Kanda, “Development of Novel Particle Excitation Flow Control Valve for Stable Flow Characteristics,” Int. J. Automation Technol., Vol.10, No.4, pp. 540-548, doi: 10.20965/ijat.2016.p0540, 2016.
- [17] D. Hirooka, T. Yamaguchi, N. Furushiro, K. Suzumori, and T. Kanda, “Particle-Excitation Flow-Control Valve using Piezo Vibration-Improvement for a high flow rate and Research on Controllability-,” Trans. on Sensors and Micromachines, Vol.137, No.1, pp. 32-37, 2017.
- [18] D. Hirooka, T. Yamaguchi, N. Furushiro, K. Suzumori, and T. Kanda, “Optimization of orifice position in particle-excitation valve for proportional flow control,” Robomech J., Vol.4, Article No.25, 2017.
- [19] Y. Miyake, T. Yamaguchi, N. Furushiro, and D. Hirooka, “The Method of Improving Flow Characteristics for Air Flow Control Valve Using Particle Excitation by PZT Transducer,” Proc. of Int. Workshop on Piezoelectric Materials and Applications in Actuators (IWPMA2018), p. 117, 2018.
This article is published under a Creative Commons Attribution-NoDerivatives 4.0 Internationa License.