Paper:
An Optimal Design Methodology for the Trajectory of Hydraulic Excavators Based on Genetic Algorithm
Takamichi Yuasa, Masato Ishikawa, and Satoshi Ogawa
Osaka University
2-1 Yamadaoka, Suita, Osaka 565-0871, Japan
Hydraulic excavators are one type of construction equipment used in various construction sites worldwide, and their usage and scale are diverse. Generally, the work efficiency of a hydraulic excavator largely depends on human operation skills. If we can comprehend the experienced operation skills and utilize them for manual control assist, semi-automatic or automatic remote control, it would improve its work efficiency and suppress personnel costs, reduce the operator’s workload, and improve his/her safety. In this study, we propose a methodology to design efficient machine trajectories based on mathematical models and numerical optimization, focusing on ground-level excavation as a dominant task. First, we express its excavation trajectory using four parameters and assume the models for the amount of excavated soil and the reaction force based on our previous experiments. Next, we combine these models with a geometrical model for the hydraulic excavating machine. We then assign the amount of soil to a performance index preferably to be maximized and the amount of work to a cost index preferably to be minimized, both in the form of functions of the trajectory parameters, resulting in an optimization problem that trades them off. In particular, we formulate (1) a multi-objective optimization problem maximizing a weighted linear combination of the amount of soil and the amount of work as an objective function, and (2) a single-objective optimization problem maximizing the amount of soil under a given upper bound on the amount of work, so that we can solve these optimization problems using the genetic algorithm (GA). Finally, we conclude this paper by suggesting our notice on design methodology and discussing how we should provide the optimization method as mentioned above to the users who operate hydraulic excavators.
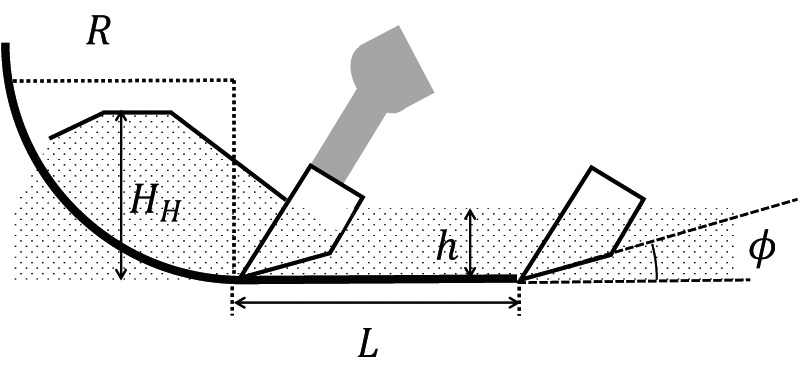
Mathematical approach to trajectory design for hydraulic excavators
- [1] R. Sekizuka, M. Ito, S. Saiki, Y. Yamazaki, and Y. Kurita, “System to evaluate the skill of operating hydraulic excavators using a remote controlled excavator and virtual reality,” Frontiers in Robotics and AI, Vol.6, 2020.
- [2] Y. Sakaida, D. Chugo, K. Kawabata, and H. Asama, “Analysis of skillful hydraulic excavator operation: skill analysis based on simulation,” Proc. of JSME Conf. on Robotics and Mechatronics (ROBOMECH2007), 1P1-M07, 2007 (in Japanese).
- [3] Y. Sakaida, D. Chugo, H. Yamamoto, K. Kawabata, and H. Asama, “Analysis of Skillful Hydraulic Excavator Operation: Correlation of Excavating Direction and Bucket’s posture,” Proc. of JSME Conf. on Robotics and Mechatronics (ROBOMECH2008), 2P1-B19, 2008.
- [4] T. Yoshida, T. Koizumi, N. Tsujiuchi, K. Chen, and Y. Nakamoto, “Investigation of efficiency improvement in digging operation for hydraulic excavators,” J. of System Design and Dynamics, Vol.7, No.1, pp. 66-78, 2013.
- [5] T. Yoshida, T. Koizumi, N. Tsujiuchi, Z. Jiang, and Y. Nakamoto, “Digging trajectory optimization by soil models and dynamics models of excavator,” SAE Int. J. of Commercial Vehicles, Vol.6, No.2, pp. 429-440, 2013.
- [6] T. Yoshida, T. Koizumi, N. Tsujiuchi, Z. Jiang, and Y. Nakamoto, “Dynamic analysis of an excavator during digging operation,” SAE Int. J. of Commercial Vehicles, Vol.6, No.2, pp. 419-428, 2013.
- [7] K. Katsushima, H. Suzuki, G. Ishigami, and S. Ozaki, “High precision simulation of construction robot focused on interaction between soil and machines – micro approach based on discrete element method –,” Proc. of JSME Conf. on Robotics and Mechatronics (ROBOMECH2017), 2A1-Q07, 2017 (in Japanese).
- [8] K. Katsushima, H. Suzuki, G. Ishigami, and S. Ozaki, “Extension of soil excavation model in disaster response simulator using discrete element method,” Proc. of JSME Conf. on Robotics and Mechatronics (ROBOMECH2018), 2A1-L02, 2018 (in Japanese).
- [9] H. Osumi, Y. Kawashima, T. Tsuda, Y. Sano, and C. Wu, “Optimization of excavation position considering energy in backhoe,” Proc. of JSME Conf. on Robotics and Mechatronics (ROBOMECH2018), 2A2-A06, 2018 (in Japanese).
- [10] R. Yoneyama, T. Omura, G. Sakayori, S. Ozaki, and G. Ishigami, “Towards high-fidelity simulator of construction machine based on accurate machine-soil interaction mechanics – RFT-based bucket dynamics modeling and experimental validation –,” Proc. of JSME Conf. on Robotics and Mechatronics (ROBOMECH2017), 2A1-Q08, 2017 (in Japanese).
- [11] K. Tsuchiya and G. Ishgami, “Vision-based measurement of spatio-temporal deformation of excavated soil for the estimation of bucket resistive force,” J. of Terramechanics, Vol.90, pp. 11-21, 2020.
- [12] M. Kozui, T. Yamamoto, M. Akiyama, K. Koiwai, and Y. Yamazaki, “Application of a MIMO-PID controller for a hydraulic excavator considering the velocity of CoM,” J. Robot. Mechatron., Vol.32, No.3, pp. 643-651, 2020.
- [13] Y. Oshima, T. Kinoshita, K. Koiwai, T. Yamamoto, T. Nanjo, Y. Yamazaki, and Y. Fujimoto, “Data-driven torque controller for a hydraulic excavator,” J. Robot. Mechatron., Vol.28, No.5, pp. 752-758, 2016.
- [14] M. Ishikawa, K. Nagura, and S. Ogawa, “On data-based modeling of scooping process by hydraulic excavator,” Proc. of JSME Conf. on Robotics and Mechatronics (ROBOMECH2018), 2A2-A03, 2018 (in Japanese).
- [15] K. Izawa, M. Ishikawa, T. Yuasa, and S. Ogawa, “Modeling of scooping process by hydraulic excavator using physics simulation software,” SICE Kansai Section/ISCIE Symp. for Young Researchers, D1-1, 2019 (in Japanese).
- [16] “PC200-11/PC210-11 Catalog,” Komatsu Ltd., 2017.
- [17] R. Naka, M. Ishikawa, and S. Ogawa, “Development of automatic digging system for modeling digging process of hydraulic excavator,” Proc. of JSME Conf. on Robotics and Mechatronics (ROBOMECH2020), 2P1-A02, 2020 (in Japanese).
This article is published under a Creative Commons Attribution-NoDerivatives 4.0 Internationa License.