Paper:
Development of Automatic Chair Transport System - Chair Recognition and Approach Strategy –
Koshiro Miyauchi and Nobuaki Nakazawa
Department of Mechanical Science and Technology, Graduate School of Science and Technology, Gunma University
29-1 Hon-cho, Ota, Gunma 373-0057, Japan
In schools and other educational institutions, there are many instances that require the arrangement of chairs depending on the required purpose, such as a class or event. Some chairs are on casters; however, educational institutions typically use stacking or folding chairs. Although effective in terms of storage, these must be lifted by hand during transportation, increasing the burden on the workforce. While automation of baggage transport in warehouses has improved significantly, little attention has been paid to the automation of chair transport. Despite the demand and the fact that self-propelled chairs have already been developed, automatic transport of chairs without casters has never been reported. In this study, we constructed an automatic chair-transport system using an omnidirectional mobile robot and focused on a stacking chair that allowed the robot to position itself underneath. The developed system utilizes the image of the seat and frame pipe of the stacking chair to estimate the chair’s position and direction with respect to the robot. Once the robot has positioned itself under the chair, the chair is lifted and transported using a lifter device attached to the robot.
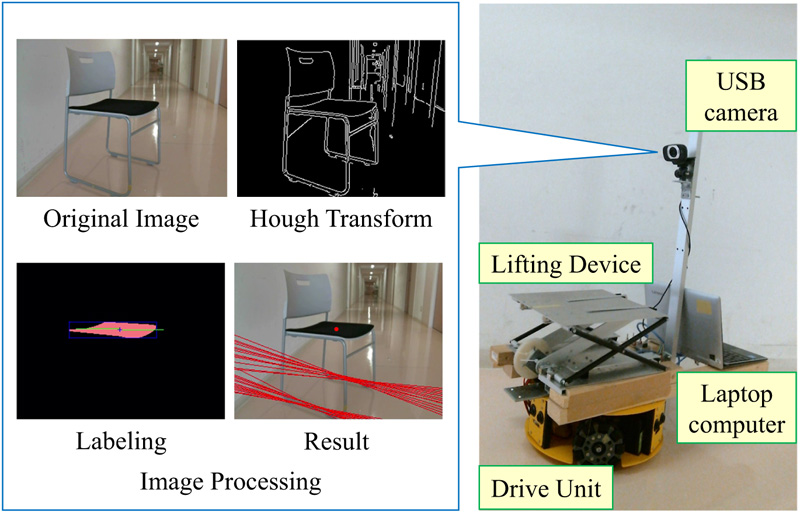
Robot configuration and chair detection
- [1] Logistics Policy Division, Ministry of Land, Infrastructure, Transport and Tourism, “About the current situation surrounding logistics,” 2018 (in Japanese).
- [2] T. Nishimura, A. Seo, K. Doi, and Y. Oshima, “Evaluation of Physical Stress Due to Handling Material White Ascending and Descending a Staircase,” J. of Japan Industrial Management Association, Vol.61, No.3, pp. 107-115, 2010 (in Japanese).
- [3] J. Balingit, H. Iwase, and M. Kitaoka, “Working Posture Classification using a Human Body Model in Manual Material Handling,” J. of Japan Industrial Management Association, Vol.55, No.2, pp. 77-88, 2004 (in Japanese).
- [4] A. Seo, Y. Kondo, and Y. Kusaka, “A Simple Software Supportive for Redesign of Working Conditions to Reduce Low Back Load,” J. Science of Labour, Vol.74, No.9, pp. 337-345, 1998 (in Japanese).
- [5] Industrial Health Division, Industrial Safety and Health Department, Labour Standards Bureau, Ministry of Health, Labour and Welfare, “Low back pain prevention measures guidelines in the workplace,” 2013 (in Japanese).
- [6] T. Higashi, K. Sekiyama, and T. Fukuda, “Autonomous Formation of Transportation Order under Dynamical Environment,” J. Robot. Mechatron., Vol.12, No.4, pp. 494-500, 2000.
- [7] S. Kato and K. W. Wong, “Intelligent Automated Guided Vehicle Controller with Reverse Strategy,” J. Adv. Comput. Intell. Intell. Inform., Vol.15, No.3, pp. 304-312, 2011.
- [8] N. Kimura, “Low back pain prevention measures guidelines in the workplace,” J. of the Robotics Society of Japan, Vol.35, No.9, pp. 652-655, 2017 (in Japanese).
- [9] T. Moriya, N. Kimura, K. Ara, and T. Watanabe, “Warehouse Automation towards Innovation in Logistics,” J. of the Robotics Society of Japan, Vol.37, No.8, pp. 699-702, 2019 (in Japanese).
- [10] S. Maki, K. Shirane, and R. Masaki, “A Map for Logistics Support Mobile Robot and Its Application,” J. of the Robotics Society of Japan, Vol.33, No.10, pp. 732-737, 2015 (in Japanese).
- [11] N. Kimura and J. Ota, “Unknown Object Detection Using Floor Height Map for Mobile Robots on Indoor Floor with Non-Horizontal Partial Areas,” J. of the Robotics Society of Japan, Vol.34, No.10, pp. 699-710, 2016 (in Japanese).
- [12] J. Seki, H. Aoyama, K. Ishikawa, S. Ishimura, T. Wadasako, Y. Adachi, Y. Satsumi, K. Yokota, K. Ozaki, and S. Yamamoto, “Development of the Indoor Mobile Robot Navigating by Vision and Magnetic Tags,” J. of the Robotics Society of Japan, Vol.27, No.8, pp. 833-841, 2009 (in Japanese).
- [13] M. Hashimoto, T. Tomiie, and F. Oba, “Dead Reckoning of a Modular Omnidirectional Vehicle by Fusing Redundant Odometry and Gyro Information,” Trans. of the Japan Society of Mechanical Engineers, Series C, Vol.66, No.645, pp. 1613-1620, 2000 (in Japanese).
- [14] Y. Hada and S. Yuta, “Positioning System for Indoor Vehicle Using Odometry, Ultrasonic Sensor and Environment Map (Ultrasonic Sensor Simulator for Landmark Identification),” Trans. of the Japan Society of Mechanical Engineers, Series C, Vol.68, No.672, pp. 2278-2285, 2002 (in Japanese).
- [15] T. Umetani, Y. Kondo, and T. Tokuda, “Rapid Development of a Mobile Robot for the Nakanoshima Challenge Using a Robot for Intelligent Environments,” J. Robot. Mechatron., Vol.32, No.6, pp. 1211-1218, 2020.
- [16] Y. Kume, Y. Hirata, and K. Kosuge, “Object Handling by Coordinated Multiple Mobile Manipulators Without Force/Torque Sensors,” J. Robot. Mechatron., Vol.20, No.3, pp. 394-402, 2008.
- [17] T. Takubo, H. Arai, K. Tanie, and T. Arai, “Human-Robot Cooperative Handling Using Variable Virtual Nonholonomic Constraint,” Int. J. Automation Technol., Vol.3, No.6, pp. 653-662, 2009.
- [18] K. Kosuge, R. Suda, N. Kazamura, M. Sato, and H. Kakuya, “Cooperative Transportation of Object by Mobile Robot Helper and Human,” Trans. of the Japan Society of Mechanical Engineers, Series C, Vol.69, No.685, pp. 2308-2314, 2003 (in Japanese).
- [19] J. Ota, T. Arai, K. Inoue, R. Chiba, T. Hirano, and Y. Maeda, “Material Transport System by Cooperation of Conveyor-Loaded AVGs,” Trans. of the Japan Society of Mechanical Engineers, Series C, Vol.67, No.658, pp. 209-215, 2001 (in Japanese).
- [20] H. Osumi, M. Kagatani, and Y. Aiyama, “Cooperative Control System for Three Industrial Robots (Singular Configurations of Passive Joint Mechanisms),” Trans. of the Japan Society of Mechanical Engineers, Series C, Vol.74, No.748, pp. 2985-2993, 2008 (in Japanese).
- [21] Y. Le, H. Kojima, and K. Matsuda, “Cooperative Obstacle-Avoidance Pushing Transportation of a Planar Object with One Leader and Two Follower Mobile Robots,” J. Robot. Mechatron., Vol.17, No.1, pp. 77-88, 2005.
- [22] Y. Hirata, K. Kosuge, T. Oosumi, H. Asama, H. Kaetsu, and K. Kawabata, “Coordinated Transportation of a Single Object by Omni-Directional Mobile Robots with Body Force Sensor,” J. Robot. Mechatron., Vol.12, No.3, pp. 242-248, 2000.
- [23] J. D. F. Heredia, S. Shirafuji, H. M. Sahloul, J. I. U. Rubrico, T. Ogata, T. Hara, and J. Ota, “Refining Two Robots Task Execution Through Tuning Behavior Trajectory and Balancing the Communication,” J. Robot. Mechatron., Vol.30, No.4, pp. 613-623, 2018.
- [24] M. Murooka, S. Noda, S. Nozawa, Y. Kakiuchi, K. Okada, and M. Inaba, “Achievement of Pivoting Large and Heavy Objects by Life-sized Humanoid Robot based on Online Estimation Control Method of Object State and Manipulation Force,” J. of the Robotics Society of Japan, Vol.32, No.7, pp. 595-602, 2014 (in Japanese).
- [25] M. Murooka, Y. Kojio, S. Nozawa, Y. Kakiuchi, K. Okada, and M. Inaba, “Whole-body Pushing Manipulation of Large and Heavy Objects by Life-sized Humanoid based on Contact Posture Planning and Online Footstep Modification,” J. of the Robotics Society of Japan, Vol.34, No.7, pp. 448-457, 2016 (in Japanese).
- [26] K. Harada, S. Kajita, H. Saito, M. Morisawa, F. Kanehiro, K. Fujiwara, K. Kaneko, and H. Hirukawa, “A Humanoid Robot Carrying a Heavy Object,” Proc. of the 2005 IEEE, Int. Conf. on Robotics and Automation, pp. 1724-1729, 2005.
- [27] M. Endo, K. Hirose, Y. Hirata, K. Kosuge, Y. Sugahara, K. Suzuki, H. Shinozuka, H. Arai, K. Akune, and T. Kanbayashi, “A Car Transportation System Using Multiple Robots iCART (1st Report, The Design and the Control Algorithm of Robot),” Trans. of the Japan Society of Mechanical Engineers, Series C, Vol.75, No.755, pp. 2028-2035, 2009 (in Japanese).
- [28] Y. Yoshimura, J. Ota, K. Inoue, T. Hirano, D. Kurabayashi, and T. Arai, “Iterative Transportation Planning of Multiple Objects by Cooperative Mobile Robots,” J. of the Robotics Society of Japan, Vol.16, No.4, pp. 499-507, 1998 (in Japanese).
This article is published under a Creative Commons Attribution-NoDerivatives 4.0 Internationa License.