Development Report:
Development of Condition Monitoring System for Electric Resistance Spot Welding Used to Manufacture Railway Car Bodies
Masashi Oikawa*, Kentaro Atsumi*, Yosuke Otsuka*, and Naoki Kawada**
*Japan Transport Engineering Company
3-1 Okawa, Kanazawa-ku, Yokohama, Kanagawa 236-0043, Japan
**Saitama Institute of Technology
1690 Fusaiji, Fukaya, Saitama 369-0293, Japan
Stainless steel railway car bodies are assembled by joining the outer plates and the pillar materials using resistance spot welding. In recent years, more and more car bodies are being assembled using laser welding in addition to the resistance spot welding. For this laser welding system, we developed a condition monitoring system considering the processes before and after laser welding as a single system, and obtained and put into practical use an appropriate condition that suppresses spatter generation during laser welding. On the other hand, in resistance spot welding, the current, weld time, electrode load, and electrode tip shape are the main factors that determine the welding quality. Therefore, the configuration of the equipment is less complicated than that of laser welding system, and the condition monitoring is easier than that of the laser welding. In this study, by transferring the concept of the condition monitoring system developed for laser welding to resistance spot welding, we achieved a reduction of more than 60% in terms of electricity consumption and improved the appearance of the car body by optimizing the indentation shape. In addition to this technical achievement, we also present in this paper a case study showing the opportunity for innovation by restructuring the technological paradigm of the resistance spot welding in the production of stainless steel car body shells.
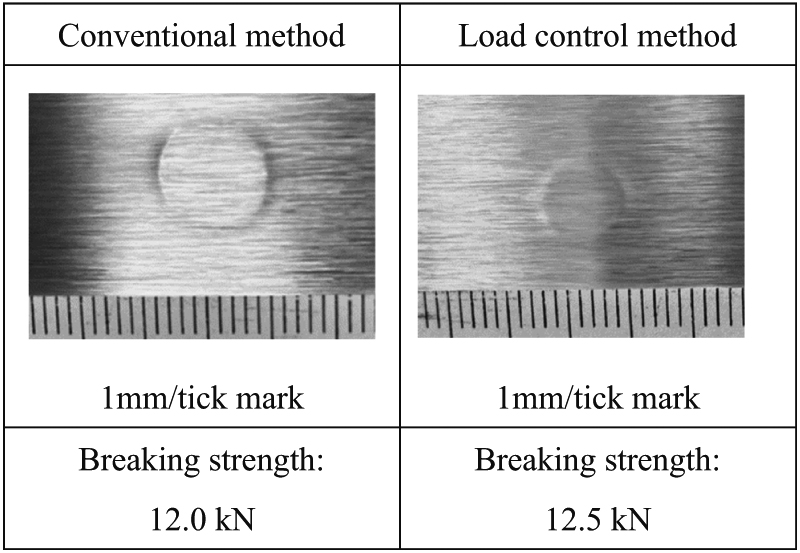
Comparison of appearance of weld zone
- [1] H. Uchida, “Car Body Shell Structure and Latest Technology of Railway Vehicle – Stainless Steel Car, Aluminum Alloy Car –,” J. of the Japan Society of Mechanical Engineers, Vol.35, No.1003, pp. 394-395, 2002 (in Japanese).
- [2] M. Oikawa and H. Kumehara, “Development of Laser Spot Welded Stainless Steel Double Skin Panels for Civil Transports – 1st Report, Manufacturing Technology for Laser Spot Welded Stainless Steel Double Skin Panels and Static Mechanical Properties,” J. of the Japan Society for Precision Engineering, Vol.72, No.12, pp. 1515-1519, 2006 (in Japanese).
- [3] M. Oikawa, Y. Yoshida, N. Suzuki, and H. Kumehara, “Development of Laser Spot Welded Stainless Steel Double Skin Panels for Civil Transports – 2nd Report, Study of Equivalent Rigidity Model of Stainless Steel Double Skin Panel,” J. of the Japan Society for Precision Engineering, Vol.74, No.12, pp. 1287-1291, 2008 (in Japanese).
- [4] N. Kawada, M. Oikawa, and H. Kumehara, “Development of Monitoring System for Laser Welding System of Thin Stainless Steel Sheets by Waveform Analysis,” Proc. of ICALEO 2007, 1506, 2007.
- [5] Y. Otsuka, M. Oikawa, T. Sobagaki, K. Oogawara, and O. Kimura, “History of Technology in Stainless Steel Car Body – From Technology Introduction of Resistance Spot Welding to Development of the World’s First Laser Welding Car Body –,” J-TREC Technical Review, Vol.6, pp. 22-31, 2017 (in Japanese).
- [6] N. Kawada, M. Oikawa, and H. Kumehara, “Development of Monitoring System for Laser Welding System of Stainless Steel Sheets, 1st,” Proc. of 2006 Autumn Meeting of the Japan Society for Precision Engineering, pp. 615- 616, 2006 (in Japanese).
- [7] S. Shiraishi, N. Kawada, M. Oikawa, and H. Kumehara, “Development of Monitoring System for Laser Welding System of Stainless Steel Sheets, 3rd,” Proc. of 2007 Autumn Meeting of the Japan Society for Precision Engineering, pp. 975- 976, 2007 (in Japanese).
- [8] J. Herwan, S. Kano, R. Oleg, H. Sawada, and M. Watanabe, “Comparing Vibration Sensor Positions in CNC Turning for a Feasible Application in Smart Manufacturing System,” Int. J. Automation Technol., Vol.12, No.3, pp. 282-289, 2018.
- [9] J. Sun, G. S. Hong, M. Rahman, and Y. S. Wong, “Identification of feature set for effective tool condition monitoring by acoustic emission sensing,” Int. J. of Production Research, Vol.42, Issue 5, pp. 901-918, 2004.
- [10] X. Li, “Real-time tool wear condition monitoring in turning,” Int. J. of Production Research, Vol.39, Issue 5, pp. 981-992, 2001.
- [11] A. Hayashi, R. Sato, and K. Shirase, “Measurement and Evaluation of Electric Power Consumption of Feed Drive Systems in NC Machine Tool,” J. of the Japan Society for Precision Engineering, Vol.79, No.10, pp. 930-936, 2013 (in Japanese).
- [12] W. H. Wang, G. S. Hong, Y. S. Wong, and K. P. Zhu, “Sensor fusion for online tool condition monitoring in milling,” Int. J. of Production Research, Vol.45, Issue 21, pp. 5095-5116, 2007.
- [13] H. Saglam and A. Unuvar, “Tool condition monitoring in milling based on cutting forces by a neural network,” Int. J. of Production Research, Vol.41, Issue 7, pp. 1519-1532, 2003.
- [14] JIS Z 3140, 2017 (in Japanese).
- [15] JRIS (Japan Association of Rolling Stock Industries Standard), W0161, 2006 (in Japanese).
- [16] T. Hirashima, “Development of Stainless Steel Car Body Structure using Laser Welding and Technology at Kawasaki Heavy Industries – Special feature: Research on Railway Car Body Structure –,” Rolling Stock and Technology, Vol.14, No.7, pp. 11-17, 2008 (in Japanese).
- [17] K. Shima, “Power Increasing of Fiber Lasers,” Function and Materials, Vol.39, No.4, pp. 25-32, 2019 (in Japanese).
This article is published under a Creative Commons Attribution-NoDerivatives 4.0 Internationa License.