Paper:
Design and Modeling of Soft Pneumatic Helical Actuator with High Contraction Ratio
Peizheng Yuan, Ginjiro Kawano, and Hideyuki Tsukagoshi
Tokyo Institute of Technology
2-12-1 Ookayama, Meguro-ku, Tokyo 152-8552, Japan
Soft contraction actuators are becoming important elements particularly for human-friendly robotic applications. However, it is challenging to achieve both a large operating distance while generating practical force. Hence, we present a new soft contraction actuator capable of realizing a high ratio contraction by pneumatic power. It can be easily fabricated using soft materials, including rubber tubes, one-way extensible cloth, and inextensible wire. Its initial shape is tubular but it can curve and coil to a helix shape owing to its different extensibilities on two sides when pressurized. A maximum contraction ratio of 78% and a 23 N contraction force can be achieved with an 11.6 mm initial outer diameter tube under 0.3 MPa. The effect of the tilt angle of a one-way extensible cloth on the helical shape is investigated, and a mathematical model illustrating the relationship between the contraction ratio and force is derived. Our experimental results suggest that this helical actuator has a much higher contraction ratio than a McKibben actuator under the same conditions. Finally, we discuss the potential application of the proposed actuator to a wearable device, i.e., for assisting the dorsiflexion of an ankle joint requiring a wide range of motion.
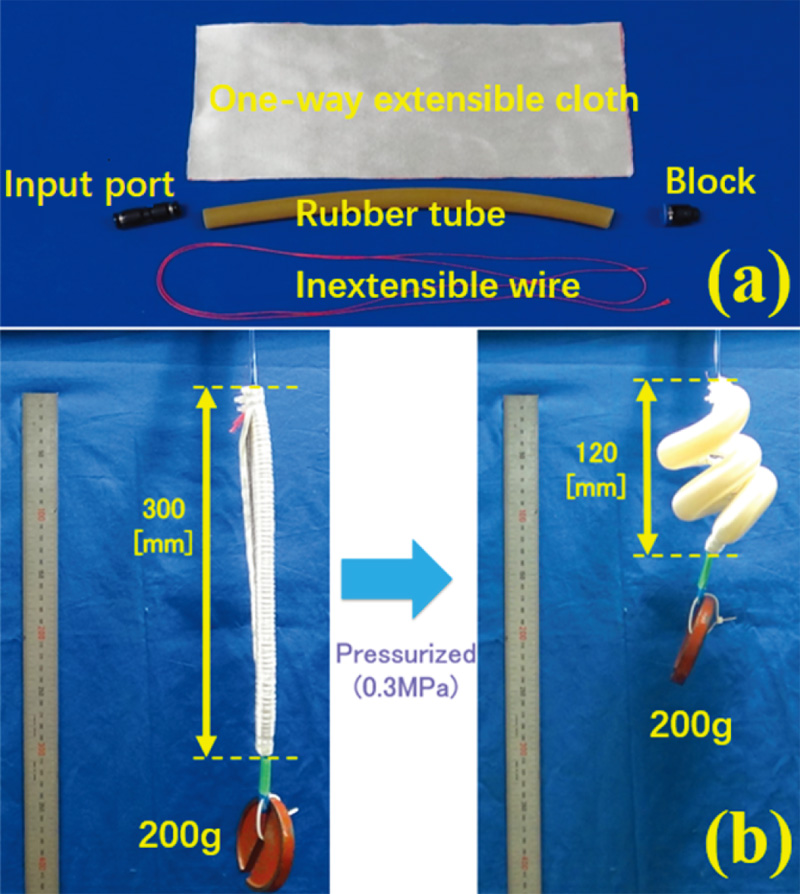
Helical actuator with high contraction ratio made of simple materials
- [1] C. Laschi, B. Mazzolai, and M. Cianchetti, “Soft robotics: Technologies and systems pushing the boundaries of robot abilities,” Science Robotics, Vol.1, No.1, eaah3690, 2016.
- [2] D. Rus and M. T. Tolley, “Design fabrication and control of soft robots,” Nature, Vol.521, pp. 467-475, 2015.
- [3] T. Noritsugu, M. Takaiwa, and D. Sasaki, “Development of power assist wear using pneumatic rubber artificial muscles,” J. Robot. Mechatron., Vol.21, No.5, pp. 607-613, 2009.
- [4] C. Thakur, K. Ogawa, and Y. Kurita, “Active passive nature of assistive wearable gait augment suit for enhanced mobility,” J. Robot. Mechatron., Vol.30, No.5, pp. 717-728, 2018.
- [5] T. Kosaki and S. Li, “A Water-Hydraulic Upper-Limb Assistive Exoskeleton System with Displacement Estimation,” J. Robot. Mechatron., Vol.32, No.1, pp. 149-156, 2020.
- [6] L. N. Awad et al., “A soft robotic exosuit improves walking in patients after stroke,” Sci. Transl. Med., Vol.9, No.400, eaai9084, 2017.
- [7] P. Polygerinos et al., “Soft robotic glove for hand rehabilitation and task specific training,” 2015 IEEE Int. Conf. on Robotics and Automation (ICRA), pp. 2913-2919, 2015.
- [8] H. Al-Fahaam, S. Davis, and S. Nefti-Meziani, “Wrist rehabilitation exoskeleton robot based on pneumatic soft actuators,” 2016 Int. Conf. for Students on Applied Engineering (ICSAE), pp. 491-496, 2016.
- [9] T. Kawamura, H. Kawahara, and M. Nakazawa, “Control of Vertebrate Backbone System by Using Artificial Rubber Muscles,” J. Robot. Mechatron., Vol.7, No.6, pp. 483-487, 1995.
- [10] S. Krishna, T. Nagarajan, and A. M. A. Rani, “Review of current development of pneumatic artificial muscle,” J. of Applied Sciences, Vol.11, No.10, pp. 1749-1755, 2011.
- [11] B. Tondu and P. Lopez, “Modeling and control of McKibben artificial muscle robot actuators,” IEEE Control Systems Magazine, Vol.20, No.2, pp. 15-38, 2000.
- [12] N. S. Usevitch, A. M. Okamura, and E. W. Hawkes, “APAM: antagonistic pneumatic artificial muscle,” 2018 IEEE Int. Conf. on Robotics and Automation (ICRA), pp. 1539-1546, 2018.
- [13] W. Felt, M. A. Robertson, and J. Paik, “Modeling vacuum bellows soft pneumatic actuators with optimal mechanical performance,” 2018 IEEE Int. Conf. on Soft Robotics (RoboSoft), pp. 534-540, 2018.
- [14] E. R. Perez-Guagnelli, S. Nejus, J. Yu et al., “Axially and radially expandable modular helical soft actuator for robotic implantables,” IEEE Int. Conf. on Robotics and Automation (ICRA), pp. 4297-4304, 2018.
- [15] L. H. Blumenschein et al., “A tip-extending soft robot enables reconfigurable and deployable antennas,” IEEE Robotics and Automation Letters, Vol.3, No.2, pp. 949-956, 2018.
- [16] L. H. Blumenschein et al., “Helical actuation on a soft inflated robot body,” 2018 IEEE Int. Conf. on Soft Robotics (RoboSoft), pp. 245-252, 2018.
- [17] R. Geer and S. Li, “Examining the coiling motion of soft actuators reinforced with tilted helix fibers,” American Society of Mechanical Engineers (ASME) 2018 Conf. on Smart Materials, Adaptive Structures and Intelligent Systems, Paper No.SMASIS2018-8038, 2018.
- [18] P. Yuan, G. Kawano, and H. Tsukagoshi, “Soft Pneumatic Helical Actuator with High Contraction Ratio,” 2019 IEEE/RSJ Int. Conf. on Intelligent Robots and Systems (IROS), pp. 8300-8305, 2019.
- [19] F. Connolly et al., “Mechanical programming of soft actuators by varying fiber angle,” Soft Robotics, Vol.2, No.1, pp. 26-32, 2015.
- [20] R. Mutlu, G. Alici, and W. Li, “Three-dimensional kinematic modeling of helix-forming lamina-emergent soft smart actuators based on electroactive polymers,” IEEE Trans. on Systems, Man, and Cybernetics: Systems, Vol.47, No.9, pp. 2562-2573, 2017.
- [21] K. Han, N. H. Kim, and D. Shin, “A novel soft pneumatic artificial muscle with high-contraction ratio,” Soft Robotics, Vol.5, No.5, pp. 554-566, 2018.
- [22] R. N. Stauffer, E. Y. Chao, and R. C. Brewster, “Force and motion analysis of the normal, diseased, and prosthetic ankle joint,” Clinical Orthopaedics and Related Research, Vol.127, pp. 189-196, 1977.
This article is published under a Creative Commons Attribution-NoDerivatives 4.0 Internationa License.