Paper:
Development of Pneumatically Driven Hand Capable of Grasping Flexible Objects
Kotaro Nishikawa*, Kentaro Hirata**, and Masahiro Takaiwa***
*Department of Integrated Science and Technology, National Institute of Technology, Tsuyama College
624-1 Numa, Tsuyama, Okayama 708-8509, Japan
**Graduate School of Natural Science and Technology, Okayama University
3-1-1 Tsushima-naka, Kita-ku, Okayama 700-8530, Japan
***Graduate School of Technology, Industrial and Social Sciences, Tokushima University
2-1 Minamijyousanjima-cho, Tokushima 770-8506, Japan
Industrial robots equipped with various grippers have been introduced in production sites and most of them are electrically driven. Because of the electric actuator’s characteristics, they have no back drivability, making it difficult for them to grasp flexible objects. In this study, therefore, we propose a pneumatically driven robot hand capable of grasping flexible objects by effectively employing the compressibility and back drivability of air.
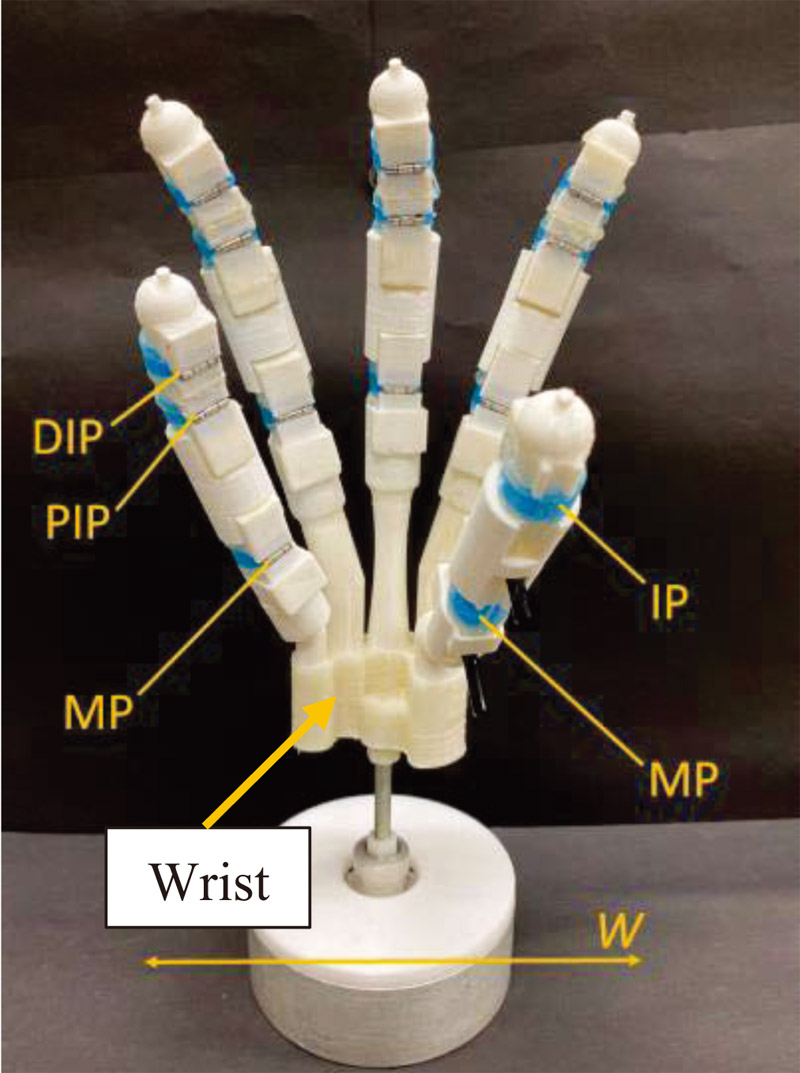
Pneumatic robot hand
- [1] K. Tadakuma, “Principle and Embodiment of Embracing Gripper Mechanisms,” J. of the Robotics Society of Japan, Vol.35, No.1, pp. 36-39, 2017 (in Japanese).
- [2] S. Hasegawa, K. Wada, K. Okada, and M. Inaba, “A Three-Fingered Hand with a Suction Gripping System for Warehouse Automation,” J. Robot. Mechatron., Vol.31, No.2, pp. 289-304, 2019.
- [3] S. Bachche and K. Oka, “Design, Modeling and Performance Testing of End-Effector for Sweet Pepper Harvesting Robot Hand,” J. Robot. Mechatron., Vol.25, No.4, pp. 705-717, 2013.
- [4] N. Kondo and M. Monta, “Fruit Harvesting Robotics,” J. Robot. Mechatron., Vol.11, No.4, pp. 321-325, 1999.
- [5] N. Irie and N. Taguchi, “Asparagus Harvesting Robot,” J. Robot. Mechatron., Vol.26, No.2, pp. 267-268, 2014.
- [6] H. Kawasaki and T. Mouri, “Humanoid Robot Hand its Applied Research,” J. Robot. Mechatron., Vol.31, No.1, pp. 16-26, 2019.
- [7] J. Ueda, M. Kondo, and T. Ogasawara, “The Multifingered NAIST Hand System for Robot In-Hand Manipulation,” J. of Mechanism and Machine Theory, Vol.45, No.2, pp. 224-238, 2010.
- [8] T. Tsuji, T. Shibanoki, G. Nakamura, and A. Furui, “Development of Myoelectric Robotic/Prosthetic Hands with Cybernetic Control at the Biological Systems Engineering Laboratory, Hiroshima University,” J. Robot. Mechatron., Vol.31, No.1, pp. 27-34, 2019.
- [9] J. Tanaka, “Three-Fingered Robot Hand with Gripping Force Generating Mechanism Using Small Gas Springs – Mechanical Design and Basic Experiments –,” J. Robot. Mechatron., Vol.31, No.1, pp. 118-134, 2019.
- [10] H. Kawasaki and T. Mouri, “Myoelectric Prosthetic Hand with High Grasping Force,” J. Robot. Mechatron., Vol.26, No.1, p. 100, 2014.
- [11] S. Shimono, T. Tamamoto, A. Ito, and K. Koganezawa, “Multi-Joint-Gripper with Stiffness Adjustor,” Trans. of the Society of Instrument and Control Engineering, Vol.49, No.1, pp. 11-17, 2013 (in Japanese).
- [12] A. Ke, J. Huang, and J. He, “An Underactuated Prosthetic Hand with Coupled Metacarpophalangeal Joints,” J. Adv. Comput. Intell. Intell. Inform., Vol.22, No.5, pp. 674-682, 2018.
- [13] M. Ohga, M. Takeda, A. Matsuba, A. Koide, and T. Tsuji, “Development of A Five-Finger Prosthetic Hand Using Ultrasonic Motors Controlled by Two EMG Signals,” J. Robot. Mechatron., Vol.14, No.6, pp. 565-572, 2002.
- [14] T. Nishida, “Soft Grippers for Industrial Robots,” J. of the Robotics Society of Japan, Vol.37, No.1, pp. 42-45, 2019 (in Japanese).
- [15] T. Watanabe, “Manipulation with Soft Robotic Hands,” J. of the Robotics Society of Japan, Vol.37, No.1, pp. 30-33, 2019 (in Japanese).
- [16] T. Takahashi, S. Kikuchi, M. Suzuki, and S. Aoyagi, “Development of Vacuum Gripper Imitating Octopus Sucker,” J. of the Japan Society for Precision Engineering, Vol.79, No.10, pp. 970-971, 2013 (in Japanese).
- [17] T. Takahashi, S. Kikuchi, M. Suzuki, and S. Aoyagi, “Octopus-Bioinspired Vacuum Gripper with Micro Bumps,” J. of the Robotics Society of Japan, Vol.35, No.1, pp. 62-69, 2017 (in Japanese).
- [18] K. Nishikawa, M. Shakutsui, K. Hirata, and M. Takaiwa, “Development of Pneumatic Bellows Myoelectric Hand with Tactile Feedback,” Trans. of the Institute of Electrical Engineers of Japan C, Vol.137, No.1, pp. 127-135, 2017 (in Japanese).
- [19] J. Nagase and N. Saga, “Development of a Tendon Driven Robot Hand Using a Pneumatic Balloon,” Trans. of Industry of the Society of Instrument and Control Engineering, Vol.9, No.11, pp. 76-83, 2010 (in Japanese).
- [20] K. Nishikawa, K. Hirata, and M. Takaiwa, “Development of Self-Powered Pneumatic Prosthetic Hand with Tactile Feedback,” Trans. of the Japan Fluid Power System Society, Vol.49, No.2, pp. 56-63, 2018 (in Japanese).
- [21] S. Hirai, “Robot Hand for Food Handling,” J. of the Society of Instrument and Control Engineering, Vol.56, No.10, pp. 787-791, 2017 (in Japanese).
This article is published under a Creative Commons Attribution-NoDerivatives 4.0 Internationa License.