Paper:
Development of Semi-Crouching Assistive Device Using Pneumatic Artificial Muscle
Naoki Saito*, Daisuke Furukawa**, Toshiyuki Satoh**, and Norihiko Saga***
*Department of Intelligent Mechatronics, Akita Prefectural University
84-4 Ebinokuchi, Tsuchiya, Yurihonjo, Akita 015-0055, Japan
**Department of Intelligent Mechatronics, Akita Prefectural University
84-4 Ebinokuchi, Tsuchiya, Yurihonjo, Akita 015-0055, Japan
***Department of Human System Engineering, Kwansei Gakuin University
2-1 Gakuen, Sanda, Hyogo 669-1337, Japan
This paper describes a semi-crouching assistive device using pneumatic artificial muscles. The goal of this device is to reduce the load on the lower back when performing work in the semi-crouching position. The load on the lower back is reduced by decreasing the compressive pressure on the lumbar disk of the lower back. This compressive pressure increases as the contraction force of the erector spine increases. Therefore, it is important to reduce the muscle activity of the erector spine. Based on the analytical result of a worker’s position model, the proposed device adopts a scheme to push the chest of the user as an appropriate assistive method. Additionally, the analytical result shows that a reduction in weight of the device is also important for decreasing the load on the lower back. Based on these results, we prototyped a lightweight semi-crouching assistive device that can generate sufficient assistive force via a pneumatic artificial muscle, which has high power to weight ratio. This device was experimentally evaluated via electromyogram of the erector spine when the user maintains a semi-crouching position. The experimental results confirmed the usefulness of this device.
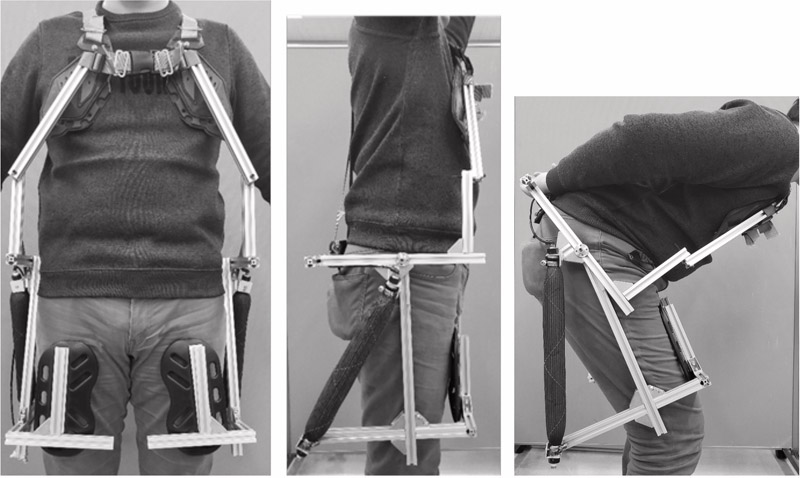
Proposed semi-crouching assistive device (SCADev)
- [1] Y. Sankai, “Leading Edge of Cybernics: Robot Suit HAL,” Proc. SICE-ICASE Int. Joint Conf. 2006, pp. 1-2, 2006.
- [2] S. Toyama and J. Yonetake, “Development of the Ultrasonic Motor-Powered Assisted Suit System,” J. Soc. of Biomech., Vol.34, No.4, pp. 184-188, 2006.
- [3] Y. T. Liao, T. Ishioka, K. Mishima, C. Kanda, K. Kodama, and E. Tanaka, “Development and Evaluation of a Close-Fitting Assistive Suit for Back and Arm Muscle – e.z.UP® –,” J. Robot. Mechatron., Vol.32, No.1, pp. 157-172, 2020.
- [4] M. Kashima, H. Arakawa, S. Kimura, R. Nishihama, K. Yokoyama, I. Kikutani, and T. Nakamura, “Development of Assist Suit for Squat Lifting Support Considering Gait and Quantitative Evaluation by Three-Dimensional Motion Analysis,” J. Robot. Mechatron., Vol.32, No.1, pp. 209-219, 2020.
- [5] Y. Imamura, T. Tanaka, Y. Suzuki, K. Takizawa, and M. Yamanaka, “Analysis of Trunk Stabilization Effect by Passive Power-Assist Device,” J. Robot. Mechatron., Vol.26, No.6, pp. 791-798, 2014.
- [6] H. Kobayashi, T. Aida, and T. Hashimoto, “Muscle Suit Development and Factory Application,” Int. J. Automation Technol., Vol.3, No.6, pp. 709-715, 2009.
- [7] X. Li, T. Noritsugu, M. Takaiwa, and D. Sasaki, “Design of Wearable Power Assist Wear for Low Back Support Using Pneumatic Actuators,” Int. J. Automation Technol., Vol.7, No.2, pp. 228-236, 2013.
- [8] H. Inose, S. Mohri, Y. Yamada, T. Nakamura, K. Yokoyama, and I. Kikutani, “Development of a Lightweight Power-assist Suit Using Pneumatic Artificial Muscles and Balloon-amplification Mechanism,” Proc. The 14th Int. Conf. on Control, Automation, Robotics and Vision (ICARCV 2016), P0191, 2016.
- [9] C. Ishii, H. Yamamoto, and D. Takigawa, “Development of a New Type of Lightweight Power Assist Suit for Transfer Work,” Proc. 2015 Asia-Pacific Conf. on Computer Aided System Engineering (APCASE), pp. 208-213, 2015.
- [10] Y. Imamura, T. Tanaka, Y. Suzuki, K. Takizawa, and M. Yamanaka, “Motion-Based-Design of Elastic Material for Passive Assistive Device Using Musculoskeletal Model,” J. Robot. Mechatron., Vol.23, No.6, pp. 978-990, 2011.
- [11] K. Naruse, S. Kawai, H. Yokoi, and Y. Kakazu, “Design if Wearable Power-Assist Device for Lower Back Support,” J. Robot. Mechatron., Vol.16, No.5, pp. 489-496, 2004.
- [12] T. Matsumatu, S. Fukuyama, and T. Sato, “Model for Analysis of Weight Lifting Motion Considering the Abdominal Pressure Increased by Valsalva Maneuver,” Trans. JSME, C, Vol.72, No.724, pp. 169-176, 2006.
- [13] D. B. Chaffin, “A computerized biomechanical model development of and use in studying gross body actions,” J. Biomechanics, Vol.2, pp. 429-441, 1969.
- [14] N. Saito and T. Satoh, “Structure of Rubberless Artificial Muscle and Evaluation of a Lifetime,” Proc. the 42th Ann. Conf. of the IEEE Ind. Elec. Soc. (IECON2016), pp. 648-653, 2016.
- [15] N. Saito, T. Sato, T. Ogasawara, R. Takahashi, and T. Sato, “Mechanical equilibrium model of rubberless artificial muscle and application to position control of antagonistic drive system,” Industrial Robot: An Int. J., Vol.40, Issue 4, pp. 347-354, 2013.
- [16] T. Hisada, S. Kudo, and T. Satta, “Investigation of attachment sites of surface electromyograph electrodes for intrinsic back muscle,” Rigaluryoho Kagaku, Vol.29, No.2, pp. 259-263, 2014 (in Japanese).
This article is published under a Creative Commons Attribution-NoDerivatives 4.0 Internationa License.