Review:
New Robotics Pioneered by Fluid Power
Koichi Suzumori
Tokyo Institute of Technology
2-12-1 Ookayama, Meguro-ku, Tokyo 152-8552, Japan
The history of robotics began with fluid power around 1960, at which time, all robots were driven by pneumatic or hydraulic actuators. Subsequently, in the mid-1980s, electromagnetic motors replaced the mainstay of robot actuators, while fluid-powered robots almost completely disappeared. However, in recent years, by utilizing the unique features of flexibility and lightness of pneumatics and the high power and robustness of hydraulics, several robots with unique characteristics, which cannot be realized with conventional electrical motors, are being developed. The author has developed various types of new fluid power actuators, including pneumatic and hydraulic types, to realize novel robots with unique features. This paper reviews the author’s previous works on fluid power actuators and robots driven by them. Furthermore, it presents prospective robots that can be realized using fluid power.
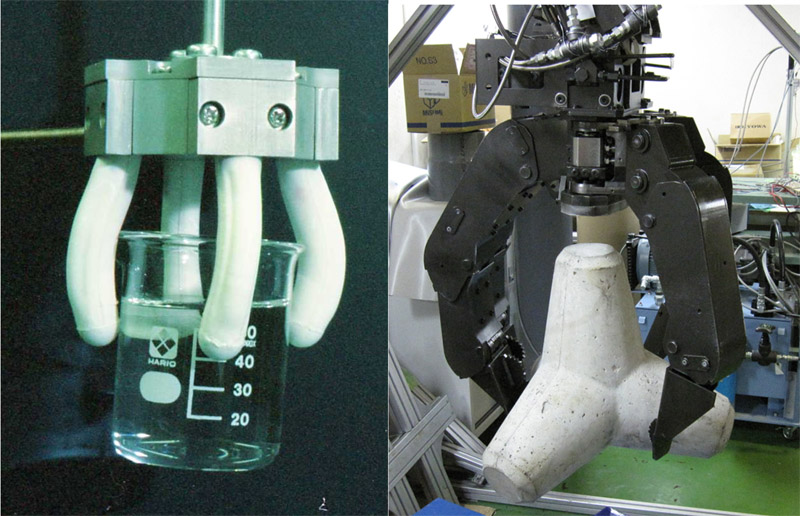
Fluid power realizing new robots: pneumatic soft hand (left) and hydraulic power hand (right)
- [1] K. Suzumori, “New Pneumatic Actuators Producing Breakthrough in Mechatronics,” Proc. JFPS Int. Symp. on Fluid Power, Issue 7-1, pp. 197-202, 2008.
- [2] D. Sasaki, T. Noritsugu, and M. Takaiwa, “Development of Active Support Splint driven by Pneumatic Soft Actuator (ASSIST),” IEEE Int. Conf. on Robotics and Automation (ICRA), 2005.
- [3] K. Takemura, S. Yokota, and K. Edamura, “Development and control of a micro artificial muscle cell using electro-conjugate fluid,” Sensors and Actuators A: Physical, Vol.133, Issue 2, pp. 493-499, 2007.
- [4] M. Raibert et al., “BigDog, the Rough-Terrain Quadruped Robot,” Proc. 17th World Congress IFAC, pp. 10822-10825, 2008.
- [5] K. Chayama et al., “Technology of Unmanned Construction System in Japan,” J. Robot. Mechatron., Vol.26, No.4, pp. 403-417, 2014.
- [6] H. Kobayashi et al., “Realization of all motion for the upper limb by a muscle suit,” IEEE Int. Workshop on Robot and Human Interactive Communication, 2004.
- [7] K. Uzuka, I. Enomoto, and K. Suzumori, “Comparative Assessment of Several Nutation Motor Types,” IEEE/ASME Tran. on Mechatronics, Vol.14, No.1, pp. 82-92, 2009.
- [8] A. A. M. Faudzi, K. Suzumori, and S. Wakimoto, “Development of an Intelligent Chair Tool System Applying New Intelligent Pneumatic Actuators,” Advanced Robotics, Vol.24, No.10, pp. 1503-1528, 2010.
- [9] T. Kubo, Y. Kobayashi, A. A. M. Faudzi, and K. Suzumori, “Development of Active 80-faced Polyhedron for Haptic Physical Human-Machine Interface,” IEEE/RSJ Int. Conf. on Intelligent Robots and Systems (IROS), pp. 1259-1264, 2009.
- [10] A. Pail et al., “Automatenfinger,” Bundersrepublik Deutschland Patentschrift, 2426086, 1974.
- [11] K. Suzumori, S. Iikura, and H. Tanaka, “Applying a Flexible Microactuator to Robotic Mechanisms,” IEEE Control Systems, Vol.12, No.1, pp. 21-27, 1992.
- [12] K. Suzumori, T. Maeda, H. Watanabe, and T. Hisada, “Fiberless Flexible Microactuator Designed by Finite-Element Method,” IEEE/ASME Trans. on Mechatronics, Vol.2, No.4, pp. 281-286, 1997.
- [13] K. Suzumori, A. Koga, and R. Haneda, “Microfabrication of Integrated FMAs using Stereo Lithography,” IEEE Workshop Micro Electro Mechanical Systems, pp. 136-141, 1994.
- [14] K. Suzumori and S. Asaad, “A Novel Pneumatic Rubber Actuator for Mobile Robot Bases,” Proc. IEEE/RSJ Int. Conf. Intelligent Robots and Systems (IROS), pp. 1001-1006, 1996.
- [15] K. Suzumori, T. Hama, and T. Kanda, “New Pneumatic Rubber Actuators to Assist Colonoscope Insertion,” IEEE Int. Conf. on Robotics and Automation (ICRA), pp. 1824-1829, 2006.
- [16] H. F. Schulte, “The Characteristics of the McKibben Artificial Muscle,” The Application of External Power in Prosthetics and Orthotics, pp. 94-115, 1961.
- [17] S. Kurumaya et al., “Active Textile Braided in Three Strands with Thin McKibben Muscle,” Soft Robotics, Vol.6, No.2, pp. 250-262, 2019.
- [18] S. Koizumi et al., “Recurrent Braiding of Thin McKibben Muscles to Overcome Their Limitation of Contraction,” Soft Robotics, Vol.7, No.2, pp. 251-258, 2019.
- [19] T. Hiramitsu et al., “Experimental Evaluation of Textile Mechanisms Made of Artificial Muscles,” IEEE Int. Conf. on Soft Robotics (RoboSoft), 2019.
- [20] T. Abe et al., “Fabrication of ‘18 Weave’ Muscles and their Application to Soft Power Support Suit for Upper Limbs Using Thin McKibben Muscle,” IEEE Robotics and Automation Letters (RA-L), 2019.
- [21] S. Koizumi et al., “Soft Robotic Gloves with Thin McKibben Muscles for Hand Assist and Rehabilitation,” IEEE/SICE Int. Symp. on System Integration, pp. 93-98, 2020.
- [22] S. Kurumaya, K. Suzumori, H. Nabae, and S. Wakimoto, “Musculoskeletal lower-limb robot driven by multifilament muscles,” Robomech J., Vol.3, p. 18, 2016.
- [23] A. A. M. Faudzi et al., “Index Finger of a Human-like Robotic Hand using Thin Soft Muscles,” IEEE Robotics and Automation Letters (RA-L), Vol.3, No.1, pp. 92-99, 2017.
- [24] M. Takeichi, K. Suzumori, G. Endo, and H. Nabae, “Development of a 20-M-Long Giacometti Arm with Balloon Body Based on Kinematic Model with Air Resistance,” IEEE/RSJ Int. Conf. on Intelligent Robots and Systems (IROS), pp. 2710-2716, 2017.
- [25] Y. Nishioka et al., “Multiplex pneumatic control method for multi-drive system,” Sensors and Actuators A: Physical, Vol.164, No.1-2, pp. 88-94, 2010.
- [26] D. Hirooka et al., “Design and evaluation of orifice arrangement for particle-excitation flow control valve,” Sensors and Actuators A: Physical, Vol.A171, No.2, pp. 283-291, 2011.
- [27] H. Matsuoka et al., “Development of a gas/liquid phase change actuator for high temperatures,” ROBOMECH J., Vol.3, p. 1, 2016.
- [28] V. Cacucciolo et al., “Electrically-Driven Soft Fluidic Actuators Combining Stretchable Pumps With Thin McKibben Muscles,” Frontiers in Robotics and AI, Vol.6, Article 146, 2020.
- [29] A. Wada et al., “Energy regenerative hose-free pneumatic actuator,” Sensors and Actuators A: Physical, Vol.249, pp. 1-7, 2016.
- [30] T. Kitamori et al., “Untethered Three-Arm Pneumatic Robot using Hose-free Pneumatic Actuator,” IEEE/RSJ Int. Conf. on Intelligent Robots and Systems (IROS), pp. 543-548, 2016.
- [31] K. Suzumori, “Soft robots as an E-kagen artifact,” IEEE Int. Conf. on Soft Robotics (RoboSoft), 2018.
- [32] M. Mori et al., “Field test for verifying the capability of two high-powered hydraulic small robots for rescue operations,” IEEE/RSJ Int. Conf. on Intelligent Robots and Systems (IROS), pp. 3492-3497, 2006.
- [33] S. Tadokoro, “Overview of the ImPACT Tough Robotics Challenge and Strategy for Disruptive Innovation in Safety and Security,” Disaster Robotics, Springer, pp. 3-22, 2019.
- [34] H. Nabae et al., “Super-low friction and lightweight hydraulic cylinder using multi-directional forging magnesium alloy and its application to robotic leg,” Advanced Robotics, Vol.32, pp. 524-534, 2018.
- [35] K. Suzumori et al., “New Hydraulic Components for Tough Robots, Disaster Robotics,” Springer, pp. 401-451, 2019.
- [36] T. Ukida et al., “Fabrication and Evaluation of Hydraulic Particle Excitation Valve Vibrated Perpendicularly to Direction of Flow Path,” JFPS Int. J. of Fluid Power System, Vol.11, No.2, pp. 9-17, 2018.
- [37] H. Yoshinada, “Dual-Arm Construction Robot with Remote-Control Function,” Disaster Robotics, Springer, pp. 195-264, 2019.
- [38] M. Hemmi et al., “Development of Hydraulic Tough Motors with High Power Density and their Application to a 7-axis Robotic Arm,” IEEE/SICE Int. Symp. on System Integration, pp. 264-269, 2019.
- [39] M. Mori et al., “Very High Force Hydraulic McKibben Artificial Muscle with a p-Phenylene-2, 6-benzobisoxazole Cord Sleeve,” Advanced Robotics, Vol.24, Nos.1-2, pp. 233-254, 2010.
- [40] K. Suzumori et al., “Long bending rubber mechanism combined contracting and extending fluidic actuators,” IEEE/RSJ Int. Conf. on Intelligent Robots and Systems (IROS), pp. 4454-4459, 2013.
- [41] R. Morita et al., “A proposal of a new rotational-compliant joint with oil-hydraulic McKibben artificial muscles,” Advanced Robotics, Vol.32, pp. 511-523, 2018.
- [42] M. Mori et al., “Development of Power Robot Hand with Shape Adaptability Using Hydraulic McKibben Muscles,” IEEE Int. Conf. on Robotics and Automation (ICRA), pp. 1162-1168, 2010.
- [43] R. Chandler, “Playback,” 1958.
This article is published under a Creative Commons Attribution-NoDerivatives 4.0 Internationa License.