Paper:
Development of Microneedle Puncture Device that Prevents Buckling of Needle by Delivery Operation
Masato Suzuki, Fuuta Motooka, Tomokazu Takahashi, and Seiji Aoyagi
Department of Mechanical Engineering, Kansai University
3-3-35 Yamate-cho, Suita, Osaka 564-8680, Japan
Herein, using the micromachining technology, we propose a microneedle delivery mechanism that is similar to the lead delivery mechanism for a mechanical pencil. This mechanism involves three parts: a needle grasping part, a needle advancing part, and a needle retainer. This mechanism advances the needle by repeating the following steps: 1) fix the needle in the grasping part; 2) simultaneously advance the grasping part and the needle using the advancing part; 3) release the needle from the grasping part; 4) retreat the grasping and the advancing parts to their initial positions. This operation advances the needle very slowly, thereby allowing the needle to puncture the skin without buckling, even if the needle has a narrow diameter. Each component of the puncture device was cut from a plastic plate using a femtosecond laser. We evaluated the performance of the device for a stainless steel needle of φ100 μm, and were successful in delivering the needle at approximately 100 μm/cycle under a no-load condition. We also succeeded in puncturing the same needle into a hydrogel (Young’s modulus of ∼0.08 MPa) using this device.
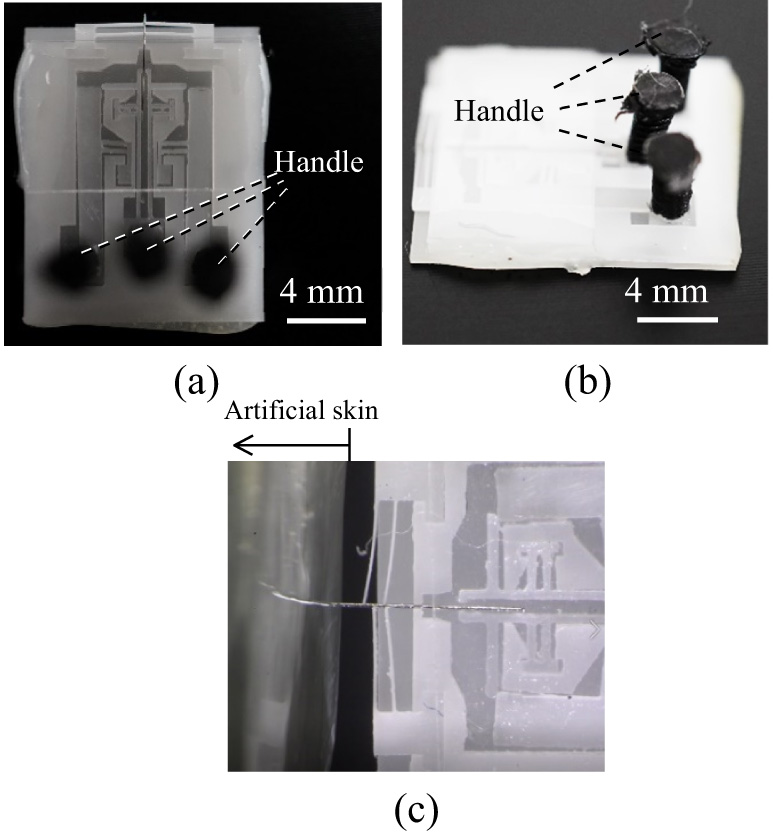
Microneedle puncture device that prevents buckling of the needle
- [1] S. P. Davis, B. J. Landis, Z. H. Adams, M. G. Allen, and M. R. Prausnitz, “Insertion of Microneedles into Skin: Measurement and Prediction of Insertion Force and Needle Fracture Force,” J. Biomechanics, Vol.37, No.8, pp. 1155-1163, 2004.
- [2] S.-O. Choi and Y.-G. Kim, “Intracellular Protein Delivery and Gene Transfection by Electroporation Using a Microneedle Electrode Array,” Small, Vol.8, No.7, pp. 1081-1091, 2012.
- [3] K. Oka, S. Aoyagi, Y. Araia, Y. Isono, G. Hashiguchi, and H. Fujitad, “Fabrication of a micro needle for a trace blood test,” Sensors and Actuators A: Physical, Vols.97-98, pp. 478-485, 2002.
- [4] K. Tsuchiya, K. Isobata, M. Sato, Y. Uetsuji, E. Nakamachi, K. Kajiwara, and M. Kimura, “Design of painless microneedle for blood extraction system,” Proc. of SPIE – BioMEMS and Nanotechnology III, Vol.6799, 67990Q, 2007.
- [5] M. Suzuki, T. Sawa, T. Takahashi, and S. Aoyagi, “Fabrication of Microneedle Mimicking Mosquito Proboscis Using Nanoscale 3D Laser Lithography System,” Int. J. Automation Technol., Vol.9, No.6, pp. 655-661, 2015.
- [6] S. Aoyagi, H. Izumi, and M. Fukuda, “Biodegradable polymer needle with various tip angles and consideration on insertion mechanism of mosquito’s proboscis,” Sensors and Actuators A: Physical, Vol.143, Issue 1, pp. 20-28, 2008.
- [7] S. Aoyagi et al., “Development of a micro lancet needle made of biodegradable polymer for low-invasive medical treatment,” Proc. of the 13th Int. Conf. on Solid-State Sensors, Actuators and Microsystems, 2005. Digest of Technical Papers. Transducers’05, Vol.2, pp. 1195-1198, 2005.
- [8] T. Tanaka, T. Takahashi, M. Suzuki, and S. Aoyagi, “Development of Minimally Invasive Microneedle Made of Tungsten – Sharpening Through Electrochemical Etching and Hole Processing for Drawing up Liquid Using Excimer Laser –,” J. Robot. Mechatron., Vol.25, No.4, pp. 755-761, 2013.
- [9] M. Shikida, T. Hasada, and K. Sato, “Fabrication of a hollow needle structure by dicing, wet etching and metal deposition,” J. of Micromechanics and Microengineering, Vol.16, No.10, pp. 2230-2239, 2006.
- [10] “Push Type Mechanical Pencil,” U.S. Patent 3892495, 1975.
- [11] T. Tsuruta, T. Takahashi, M. Suzuki, and S. Aoyagi, “Proposal of a guide tool for avoiding buckling of microneedle inspired by acupuncture technique,” The Collection of Lectures by the Japan Society of Precision Engineering, Autumn Competition, pp. 109-110, 2014 (in Japanese).
- [12] M. Suzuki, M. Tosaka, T. Takahashi, and S. Aoyagi, “Development of a fine needle puncture device that mimics the function of the lower lip of mosquitoes – Verification of Buckling Prevention Function –,” The Collection of Lectures by the Japan Society of Precision Engineering 2019 Spring Competition, pp. 359-360, 2019 (in Japanese).
- [13] O. Milleta, P. Bernardonib, S. Régnierb, P. Bidaudb, E. Tsitsirisc, D. Collardd, and L. Buchaillota, “Electrostatic actuated micro gripper using an amplification mechanism,” Sensors and Actuators A: Physical, Vol.114, Issues 2-3, pp. 371-378, 2004.
- [14] O. Fuchiwaki, A. Ito, D. Misaki, and H. Aoyama, “Multi-axial micromanipulation organized by versatile micro robots and micro tweezers,” Proc. of 2008 IEEE Int. Conf. on Robotics and Automation, pp. 893-898, 2018.
- [15] J. C. Brege, C. K. Yoon, R. Xiao, H. R. Kwag, M. O. Wang, J. P. Fisher, T. D. Nguyen, and D. H. Gracias, “Self-Folding Thermo-Magnetically Responsive Soft Microgrippers,” ACS Applied Materials and Interfaces, Vol.7, No.5, pp. 3398-3405, 2015.
- [16] D. V. Dao, P. H. Pham, and S. Sugiyama, “Multimodule Micro Transportation System Based on Electrostatic Comb-Drive Actuator and Ratchet Mechanism,” J. of Microelectromechanism Systems, Vol.20, No.1, pp. 140-149, 2011.
- [17] K. S. J. Piester, R. S. Fearing, and R. T. Howe, “A planar Air Levitated Electrostatic Actuator Systems,” IEEE Proc. on Micro Electro Mechanical Systems, pp. 67-71, 1990.
- [18] R. Yokokawa, S. Takeuchi, T. Kon, M. Nishiura, R. Ohkura, M. Edamatsu, K. Sutoh, and H. Fujita, “Hybrid Nanotransport System by Biomolecular Linear Motors,” J. of Microelectromechanism Systems, Vol.13, No.4, pp. 612-619, 2004.
- [19] Y. Urushiata, M. Suzuki, T. Takahashi, M. Oishi, and S. Aoyagi, “Evaluation of resistance force of a needle made of plastic tube,” The Collection of Lectures by the Japan Society of Precision Engineering 2014 Spring Competition, pp. 599-600, 2014 (in Japanese).
- [20] X. Liang and S. A. Boppart, “Biomechanical Properties of In Vivo Human Skin From Dynamic Optical Coherence Elastography,” IEEE Trans. Biomed. Eng., Vol.57, No.4, pp. 953-959, 2010.
- [21] H. Zahouani, C. Pailler-Mattei, B. Sohm, R. Vargiolu, V. Cenizo, and R. DebretSkin, “Characterization of the mechanical properties of a dermalequivalent compared with human skin in vivo by indentation and static friction tests,” J. Skin Research and Technology, Vol.15, No.1, pp. 68-76, 2009.
- [22] S. Yamamoto et al., “Evaluation of puncture resistance force of microneedle by nonlinear FEM analysis and experimental validation,” J. of Biomechanical Science and Engineering, Vol.14, No.4, 19-00238, 2019.
This article is published under a Creative Commons Attribution-NoDerivatives 4.0 Internationa License.