Paper:
Effect of Microneedle Cross-Sectional Shape on Puncture Resistance – Investigation of Polygonal and Star-Shaped Cross Sections –
Seiji Aoyagi*, Kento Okuda**, Tomokazu Takahashi*, and Masato Suzuki*
*Kansai University
3-3-35 Yamate-cho, Suita, Osaka 564-8680, Japan
**Housing Technology, LIXIL Corporation
130 Asaji, Oyabe, Toyama 932-0122, Japan
The shape of the needle tip that is currently used in the medical field is a “lancet point,” which is a diagonally cut cylindrical pipe, further cut on both sides. The shape of the needle shank is typically cylindrical. In this paper, tip and shank shapes that differ from the standard shape are experimentally investigated for the purpose of reducing puncture resistance. Microneedles of various cross-sectional shapes, such as polygonal and star-like, were fabricated using stereo laser lithography. Before the needle penetrates the skin, sharp edges at the needle tip may be effective to generate a stress concentration on the skin, inducing a skin fracture. After the needle penetrates the skin, corners in the cross section of the needle shank may effectively reduce the frictional resistance because the contact area between the skin and needle is limited at the corners. A needle insertion experiment was conducted against an artificial skin made of polydimethylsiloxane. The puncture resistance decreased respectively for the circular needle, polygonal needle, and star-shaped needle. For the star-shaped needles, the maximum resistance decreased as the number of corners (N) decreased. For the polygonal needle, the maximum resistance increased as N increased from 3 to 5; however, there was no observable difference for N from 6 to 8. The experimental results show that a triangular star-shaped microneedle is the most effective in reducing the puncture resistance.
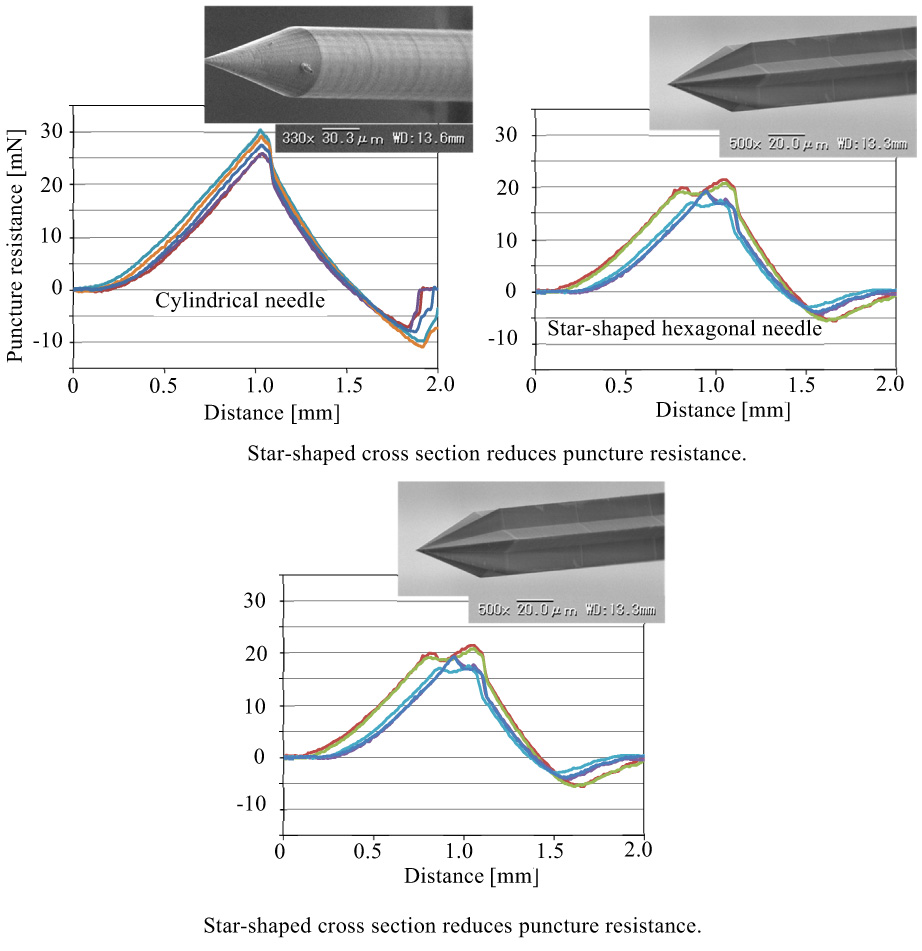
Star-shaped cross section reduces puncture resistance
- [1] Y. Wang, B. L. Tai, R. K. Chen, and A. J. Shih, “The Needle with Lancet Point: Geometry for Needle Tip Grinding and Tissue Insertion Force,” J. Manufacturing Sci. Eng., Vol.135, 041010, 2013.
- [2] Y. Urushibata, M. Suzuki, T. Takahashi, M. Ooishi, and S. Aoyagi, “Evaluation of resistance force of a needle made of plastic tube,” Proc. Spring Meeting of Japan Soc. Prec. Eng., pp. 599-600, 2014 (in Japanese).
- [3] “Surgical Needle Configuration with Star Shaped Cross-section,” U.S. Patent, No.5002565, 1991.
- [4] T. Inoue, K. Tsuchiya, M. Kimura, and K. Kajiwara, “Search of the optimum inner and outer shape for painless microneedle,” Proc. Fall Meeting of Japan Soc. Prec. Eng., pp. 205-206, 2009 (in Japanese).
- [5] H. Kimoto and K. Tsuchiya, “Fabrication of painless microneedle having polygonal cross-section based on sputtering method,” Proc. Spring Meeting of Japan Soc. Prec. Eng., pp. 319-320, 2016 (in Japanese).
- [6] R. S. Woodworth and, H. Schlosberg, “Experimental Psychology,” Rinehart and Winston, 1965.
- [7] S. Aoyagi, “Overview of Microneedles,” J. Japan Soc. Prec. Eng., Vol.82, No.12, pp. 999-1004, 2016.
- [8] N. Roxhed, T. C. Gasser, P. Griss, G. A. Holzapfel, and G. Stemme, “Penetration-Enhanced Ultrasharp Microneedles and Prediction on Skin Interaction for Efficient Transdermal Drug Delivery,” J. MEMS, Vol.16, No.6, pp. 1429-1440, 2007.
- [9] S. Henry, D. V. McAllister, M. G. Allen, and M. R. Prausnitz, “Micromachined Needles for the Transdermal Delivery of Drugs,” Proc. MEMS’98, pp. 494-498, 1998.
- [10] S. J. Moon and S. S. Lee, “Fabrication of Microneedle Array using Inclined LIGA Process,” Proc. Transducers’03, pp. 1546-1549, 2003.
- [11] H. Yagyu, S. Hayashi, and O. Tabata, “Fabrication of Plastic Micro Tip Array Using Laser Micromachining of Nanoparticles Dispersed Polymer and Micromolding,” IEEJ Trans. Sensors and Micromachines, Vol.126, No.1, pp. 7-13, 2006.
- [12] K. Imaeda, K. Bessho, and M. Shikida, “Sharp Tip-Separable Microneedle Device for Trans-Dermal Drug Delivery Systems,” Proc. Transducers 2015, pp. 1715-1718, 2015.
- [13] H. Izumi, M. Suzuki, S. Aoyagi, and T. Kanzaki, “Realistic imitation of mosquito’s proboscis, “Electrochemically etched sharp and jagged needles and their cooperative inserting motion,” Sensors and Actuators, Vol.A165, No.1, pp. 115-123, 2011.
- [14] S. Aoyagi, H. Izumi, and M. Fukuda, “Biodegradable Polymer Needle with Various Tip Angles and Consideration on Insertion Mechanism of Mosquito’s Proboscis,” Sensors and Actuators, Vol.A143, No.1, pp. 20-28, 2008.
- [15] M. Suzuki, T. Sawa, T. Takahashi, and S. Aoyagi, “Fabrication of Microneedle Mimicking Mosquito Proboscis Using Nanoscale 3D Laser Lithography System,” Int. J. Automation Technol., Vol.9, No.6, pp. 655-661, 2015.
- [16] M. Suzuki, T. Takahashi, and S. Aoyagi, “3D laser lithographic fabrication of hollow microneedle mimicking mosquitos and its characterization,” Int. J. Nanotechnology, Vol.15, No.1, pp. 157-173, 2018.
- [17] T. Tanaka, T. Takahashi, M. Suzuki, and S. Aoyagi, “Development of Minimally Invasive Microneedle Made of Tungsten – Sharpening Through Electrochemical Etching and Hole Processing for Drawing up Liquid Using Excimer Laser –,” J. Robot. Mechatron., Vol.25, No.4, pp. 755-761, 2013.
- [18] Y. Hara, M. Yamada, C. Tatsukawa, T. Takahashi, M. Suzuki, and S. Aoyagi, “Fabrication of stainless microneedle with laser cut sharp tip and its characterization of penetration and blood sampling performance,” Int. J. Automation Technol., Vol.10, No.6, pp. 950-957, 2016.
- [19] Y. Hara, M. Yamada, C. Tatsukawa, T. Takahashi, M. Suzuki, and S. Aoyagi, “Laser fabrication of jagged shaped stainless microneedle imitating mosquito’s maxilla,” Int. J. Automation Technol., Vol.10, No.6, pp. 958-964, 2016.
- [20] N. D. M. Begg and A H. Slocum, “Audible frequency vibration of puncture-access medical devices,” Medical Eng. Physics, Vol.36, No.3, pp. 371-377, 2014.
- [21] M. Ogura, Y. Terada, M. Suzuki, T. Takahashi, and S. Aoyagi, “Development of puncture jig for preventing from buckling imitating labium of mosquito,” Proc. Symp. Micro-Nano Sci. and Tech., pp. 233-234, 2013 (in Japanese).
- [22] P. G. Agache, C. Monneur, J. L. Leveque, and J. D. Rigal, “Mechanical properties and Young’s modulus of human skin in vivo,” Archives of Dermatological Research, Vol.269, No.3, pp. 221-232, 1980.
- [23] F. M. Hendriks, D. Broken, J. T. V. Eemeren, C. W. Oomens, F. P. Baaijens, and J. B. Horsten, “A numerical-experimental method to characterize the non-linear mechanical behaviour of human skin,” Skin Research and Technology, Vol.9. No.3, pp. 274-283, 2003.
- [24] J. F. Manschot and J. M. Brakkee, “The measurement and modelling of the mechanical properties of human skin in vivo – II. The model,” J. Biomechanics, Vol.19, No.7, pp. 517-521, 1986.
- [25] S. A. Ranamukhaarachchi, S. Lehnert, S. L. Ranamukhaarachchi, L. Sprenger, T. Shneider, I. Mansoor, K. Rai, U. O. Häfeli, and B. Stoeber, “A micromechanical comparison of human and porcine skin before and after preservation by freezing for medical device development,” Scientific Reports, Vol.6, 32074, 2016.
- [26] J. C. J. Wei, G. A. Edwards, D. J. Martin, H. Huang, M. L. Crichton, and M. A. F. Kendall, “Allometric scaling of skin thickness, elasticity, viscoelasticity to mass for micro-medical device translation: from mice, rats, rabbits, pigs to humans,” Scientific Reports, Vol.7, 15885, 2017.
- [27] T. Asakura and H. Seino, “Basic Study on a Micro-tapered needle (TN-3305) Used for Insulin Pre-filled Products,” Jpn. J. Pharm. Health Care Sci., Vol.30, No.6, pp. 368-376, 2004.
- [28] H. Saito, S. Kondo, A. Funakubo, and K. Mitsubayashi, “Measurement of Puncture Force during the Needle Puncture to Stretched Elastic Rubbers,” Proc. Japanese Society for Medical and Biological Eng., OR27-1, 2004 (in Japanese).
- [29] P. A. Stupar and A. Pisano, “Silicon, Parylene, and Silicon/Parylene Micro-Needles for Strength and Toughness,” Tech. Digest Transducers’01, pp. 1386-1389, 2001.
- [30] R. Nishino, T. Takahashi, M. Suzuki, S. Aoyagi, R. Hosomi, K. Fukunaga, D. Uta, T. Takazawa, and T. Fujii, “Reproduction of two layered animal skin using keratin film and its characterization,” Proc. of Fall Meeting of Japan Soc. Prec. Eng., pp. 188-189, 2019 (in Japanese).
- [31] T. Fujii, S. Takayama, and Y. Ito, “A novel purification procedure for keratin-associated proteins and keratin from human hair,” J. of Biological Macromolecules, Vol.13, No.3, pp. 92-106, 2013.
- [32] H. Izumi, T. Yajima, S. Aoyagi, N. Tagawa, Y. Arai, M. Hirata, and S. Yorifuji, “Combined Harpoonlike Jagged Microneedles Imitating Mosquito’s Proboscis and Its Insertion Experiment with Vibration,” Trans. Electrical and Electronic Eng., Vol.3, pp. 425-431, 2008.
This article is published under a Creative Commons Attribution-NoDerivatives 4.0 Internationa License.