Paper:
TasKi: Overhead Work Assistance Device with Passive Gravity Compensation Mechanism
Yasuyuki Yamada*, Hirokazu Arakawa**, Taro Watanabe**, Shunya Fukuyama**, Rie Nishihama**, Isao Kikutani***, and Taro Nakamura**
*Faculty of Engineering and Design, Hosei University
2-33 Ichigayatamachi, Shinjuku-ku, Tokyo 162-0843, Japan
**Chuo University
1-13-27 Kasuga, Bunkyo-ku, Tokyo 112-8551, Japan
***Nabtesco Corporation
JA Kyosai Bldg., 2-7-9 Hirakawacho, Chiyoda-ku, Tokyo 102-0093, Japan
During overhead work, workers need to keep raising weights of approximately 2 to 4 kg with the muscular strength of their upper limbs, and the burden of this work is high. Therefore, we developed an assistive device, named TasKi, using a self-weighted compensation mechanism to reduce the burden on upper limbs during overhead work. It can compensate for upper limb weight using the force of a spring in various postures of the upper limbs, without a battery. In this study, to provide effective assistance to many users, we clarified the crucial assistance and parameter adjustment range of settings corresponding to physical differences. First, the assistive force value of TasKi to reduce the work burden of each user was confirmed via a subjective evaluation experiment and myoelectric potential measurements. Next, we conducted a test survey of TasKi users and investigated the relationship between physique and the wearing feeling. According to the survey, 80% of the subjects provided favorable opinions on the assistive method used by TasKi. Finally, we had subjects of various physiques wear the device and investigated the relationship between physique and the wearing feeling with respect to shoulder joint movements. It was observed that the subjects with greater shoulder widths experienced difficulties when moving in the direction of internal-external rotation because of the small size of TasKi. The influence on the ease of motion and perception of size was less in the direction of flexion-extension and adduction-abduction motions.
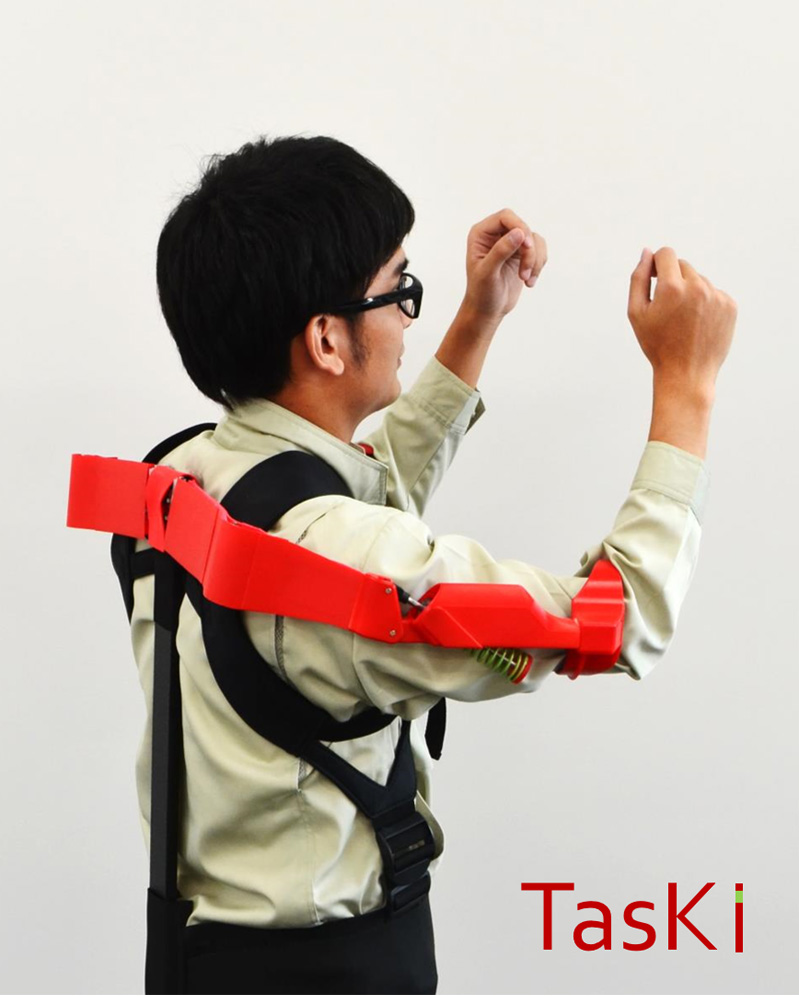
Overhead work assist by gravity compensation mechanism
- [1] T. Abe, S. Koizumi, H. Nabae, G. Endo, and K. Suzumori, “Muscle textile to implement soft suit to shift balancing posture of the body,” 2018 IEEE Int. Conf. on Soft Robotics (RoboSoft), pp. 572-578, doi: 10.1109/ROBOSOFT.2018.8405387, 2018.
- [2] Y. Yamada and T. Nakamura, “TasKi: Under-Trellis Work Assistance Device by Using Weight Compensation Mechanism,” Proc. of JSME Annual Conf. on Robotics and Mechatronics (Robomec), 1A1-B02, Fukushima, Japan, 2017.
- [3] S. Hirose and R. Chu, “Development of a Lightweight Torque Limiting M-Drive Actuator for Hyper-Redundant Manipulator Float Arm,” Proc. of the 1999 IEEE Int. Conf. on Robotics and Automation (ICRA), Vol.4, pp. 2831-2836, Detroit, USA, 1999.
- [4] J. L. Herder, “Conception of balanced spring Mechanisms,” ASME Design Engineering Technical Conf., 1998.
- [5] N. Ulrich et al., “Passive mechanical gravity compensation for robot manipulators,” Proc. of the IEEE Int. Conf. on Robotics and Automation (ICRA), pp. 1536-1541, Sacramento, USA, April 9-11, 1991.
- [6] Y. Yamada and T. Morita, “Mechanical gravity canceller with oscillating block slider crank mechanism,” Trans. of the Japan Society of Mechanical Engineers, Part C, Vol.76, No.767, pp. 1797-1803, 2010 (in Japanese).
- [7] Y. Yamada and T. Morita, “Design of constructing virtual gravity for link mechanisms,” J. of Mechanical Systems for Transportation and Logistics, Vol.5, No.1, pp. 30-42, 2012.
- [8] L. A. van der Heide, G. J. Gelderblom, and L. P. de Witte, “Dynamic arm supports: Overview and categorization of dynamic arm supports for people with decreased arm function,” IEEE Int. Conf. on Rehabilitation Robotics (ICORR), pp. 1-6, doi: 10.1109/ICORR.2013.6650491, 2013.
- [9] D. Koo, P. H. Chang, M. K. Sohn, and J. Shin, “Shoulder mechanism design of an exoskeleton robot for stroke patient rehabilitation,” 2011 IEEE Int. Conf. on Rehabilitation Robotics, pp. 1-6, Zurich, Switzerland, June 29 to July 1, 2011.
This article is published under a Creative Commons Attribution-NoDerivatives 4.0 Internationa License.