Paper:
Inspection Test of a Tunnel with an Inspection Vehicle for Tunnel Lining Concrete
Satoru Nakamura*, Atsushi Yamashita**, Fumihiro Inoue***, Daisuke Inoue*, Yusuke Takahashi*, Nobukazu Kamimura*, and Takao Ueno*
*Institute of Technology, Tokyu Construction Co., Ltd.
3062-1 Tana, Chuo-ku, Sagamihara, Kanagawa 252-0244, Japan
**The University of Tokyo
7-3-1 Hongo, Bunkyo-ku, Tokyo 113-8656, Japan
***Shonan Institute of Technology
1-1-25 Tsujidonishikaigan, Fujisawa-shi, Kanagawa 251-8511, Japan
Users of bridges and tunnels are generally concerned about the aging of these structures. Periodic inspections are necessary to keep old bridges and tunnels healthy. Inspection engineers must approach the inspection points as close as possible by mobile elevating of the work platform for close visual inspection of lining concrete. The inspection of a road tunnel particularly requires traffic regulation. Furthermore, it takes much time to perform visual inspection and hammering test for the vast area. Moreover, the inspection results have variations by inspectors. We propose an “Inspection Vehicle” for inspection of tunnel lining concrete by a new technology for infrastructure maintenance. This study reports the finding on element technology of an inspection vehicle and applies a tunnel inspection test.
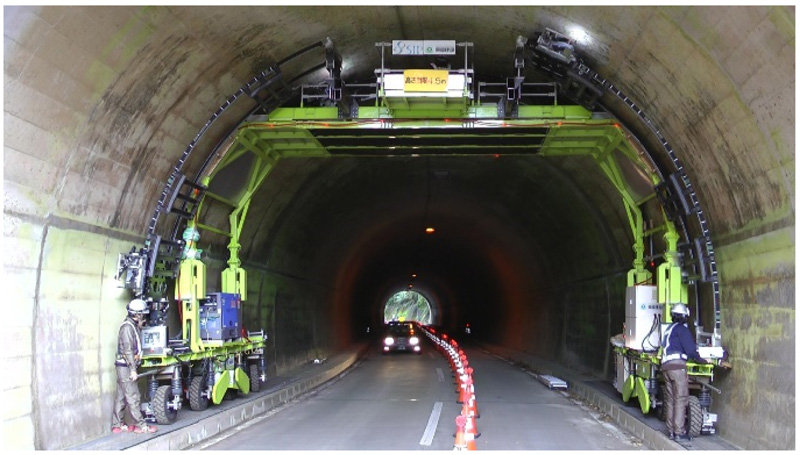
Inspection test of a tunnel with an inspection system
- [1] K. Ishikawa, J. Takiguchi, Y. Amano, T. Hashizume, and T. Fujishima, “Tunnel Cross-Section Measurement System Using a Mobile Mapping System,” J. Robot. Mechatron., Vol.21, No.2, pp. 193-199, 2009.
- [2] K. Endou, T. Ikenoya, and R. Kurazume, “Development of 3D Scanning System Using Automatic Guiding Total Station,” J. Robot. Mechatron., Vol.24, No.6, pp. 992-999, 2012.
- [3] T. Mizutani, N. Nakamura, T. Yamaguchi, M. Tarumi, Y. Ando, and I. Hara, “Bridge Slab Damage Detection by Signal Processing of UHF-Band Ground Penetrating Radar Data,” J. Disaster Res., Vol.12, No.3, pp. 415-421, 2017.
- [4] Y. Hada, M. Nakao, M. Yamada, H. Kobayashi, N. Sawasaki, K. Yokoji, S. Kanai, F. Tanaka, H. Date, S. Pathak, A. Yamashita, M. Yamada, and T. Sugawara, “Development of a Bridge Inspection Support System Using Two-Wheeled Multicopter and 3D Modeling Technology,” J. Disaster Res., Vol.12, No.3, pp. 593-605, 2017.
- [5] T. Murakami, N. Saito, Y. Komachi, K. Okamura, T. Michikawa, M. Sakashita, S. Kogure, K. Kase, S. Wada, and K. Midorikawa, “High Spatial Resolution Survey Using Frequency-Shifted Feedback Laser for Transport Infrastructure Maintenance,” J. Disaster Res., Vol.12, No.3, pp. 546-556, 2017.
- [6] S. Nakamura, Y. Takahashi, D. Inoue, and T. Ueno, “The Variable Guide Frame Vehicle for Tunnel Inspection,” 34th Int. Symp. on Automation and Robotics in Construction (ISARC2017), B-3-1(54), 2017.
- [7] F. Inoue, “A Study on Adaptive Arch Structure Applying Variable Geometry Truss (Mechanism of Movable Arch Roof with External Panel),” J. Robot. Mechatron., Vol.21, No.2, pp. 172-178, 2009.
- [8] F. Inoue, S. Kwon, T. Uchiyama, S. Nakamura, and Y. Yanagihara, “Shape Control of Variable Guide Frame for Tunnel Wall Inspection,” 34th Int. Symp. on Automation and Robotics in Construction (ISARC2017), B-4-5(185), 2017.
- [9] G. S. Chirikjian, “Kinematic synthesis of mechanisms and robotic manipulators with binary actuators,” J. Mech. Des., Vol.117, No.4, pp. 573-580, 1995.
- [10] D. Inoue, T. Ueno, and S. Nakamura, “Robotic Inspection Tests of Tunnel Lining Concrete with Crack Light-section Device on Variable Guide Frame,” 35th Int. Symp. on Automation and Robotics in Construction (ISARC2018), pp. 524-529, 2018.
- [11] J. Im, H. Fujii, A. Yamashita, and H. Asama, “Multi-Modal Diagnostic Method for Detection of Concrete Crack Direction Using Light-Section Method and Hammering Test,” 2017 14th Int. Conf. on Ubiquitous Robots and Ambient Intelligence (URAI) , pp. 922-927, 2017.
- [12] H. Fujii, A. Yamashita, and H. Asama. “Improvement of Environmental Adaptivity of Defect Detector for Hammering Test Using Boosting Algorithm,” IEEE/RSJ Int. Conf. on Intelligent Robots and System, ThFT14, 2015.
- [13] J. Kasahara, H. Fujii, A. Yamashita, and H. Asama, “Unsupervised learning approach to automation of hammering test using topological information,” ROBOMECH J., Vol.4, No.13, pp. 1-10, 2017.
- [14] Y. Takahashi, S. Maehara, Y. Ogawa, and T. Satoh, “Concrete Inspection Systems Using Hammering Robot Imitating Sounds of Workers,” 35th Int. Symp. on Automation and Robotics in Construction (ISARC2018), pp. 206-210, 2018.
This article is published under a Creative Commons Attribution-NoDerivatives 4.0 Internationa License.