Paper:
Development of an Intersection Module for a Modularized Rail Structure – Implementation of Compliant Mechanisms for a Replacing Task of Movable Parts –
Rui Fukui*, Gen Kanayama*, Yuta Kato**, Ryo Takahashi***, and Shin’ichi Warisawa*
*Department of Human and Engineered Environmental Studies, Graduate School of Frontier Sciences, The University of Tokyo
5-1-5 Kashiwa-no-ha, Kashiwa-shi, Chiba 277-8563, Japan
**Central Japan Railway Company
JR Central Towers, 1-1-4 Meieki, Nakamura-ku, Nagoya, Aichi 450-6101, Japan
***Sony Corporation
1-7-1 Konan, Minato-ku, Tokyo 108-0075, Japan
For decommissioning of the Fukushima Daiichi Nuclear Power Station, we are developing an “automated construction system for a modularized rail structure.” The intersection module developed in this study produces structure branches and changes robot attitudes. To maintain module functions, assuming the anticipated malfunctions caused by high-radiation environments, remotely controlled robots are used to replace malfunctioning parts of the module. To facilitate maintenance tasks, small positioning errors must be accommodated. This compliant function can be realized by the maintenance robot or the module. To elucidate effective combinations of the compliant mechanisms, experiments are conducted using prototypes. Experimental results confirm that the compliant mechanism of the robot contributes more efficiently than that of the module. This study is expected to be applied to practical distributed robotic systems because it is necessary to replace malfunction parts as simply as possible if they are replaced by remotely controlled robots.
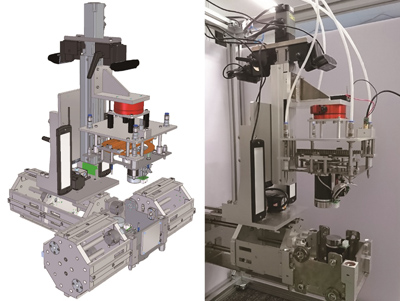
Intersection module for a modularized rail structure and its movable part replacing robot
- [1] K. Chayama, A. Fujioka, K. Kawashima, H. Yamamoto, Y. Nitta, C. Ueki, A. Yamashita, and H. Asama, “Technology of Unmanned Construction System in Japan,” J. Robot. Mechatron., Vol.26, No.4, pp. 16-20, 2014.
- [2] M. Kamezaki, J. Yang, H. Iwata, and S. Sugano, “A Basic Framework of Virtual Reality Simulator for Advancing Disaster Responce Work Using Teleoperated Work Machines,” J. Robot. Mechatron., Vol.26, No.4, pp. 486-495, 2014.
- [3] New Energy and Industrial Technology Development Organization (NEDO), “The Challenges and Proposals for the Years to Come,” 2014 White Paper on Robotization of Industry, Business and Our Life, pp. 249-296, 2014 (in Japanese).
- [4] T. Bock, “Construction Robotics,” J. Robot. Mechatron., Vol.28, No.2, pp. 116-122, 2016.
- [5] R. Fukui, Y. Kato, R. Takahashi, W. Wan, and M. Nakao, “Automated Construction System of Robot Locomotion and Operation Platform for Hazardous Environments – Basic System Design and Feasibility Study of Module Transferring and Connecting Motions,” J. of Field Robotics, Vol.33, No.6, pp. 751-764, 2016.
- [6] R. Fukui, K. Kawae, Y. Kato, and M. Nakao, “Rail Structure Supporting Mechanism Using Foamable Resin for Pillar Expansion, Anchoring, and Fixation,” J. Robot. Mechatron., Vol.28, No.2, pp. 129-137, 2016.
- [7] R. Fukui, Y. kato, G. Kanayama, R. Takahashi, and M. Nakao, “Construction Planning for a Modularized Rail Structure – Type Selection of Rail Structure Modules and Dispatch Planning of Constructor Robots –,” Proc. of the 13th Int. Symp. on Distributed Autonomous Robotic Systems (DARS 2016), London, United Kingdom, pp. 605-617, 2017.
- [8] T. Fukuda, S. Nakagawa, Y. Kawauchi, and S. Buss, “Structure Decision Method for Self Organising Robots Based on Cell Structure-CEBOT,” Proc. of the 1989 IEEE Int. Conf. on Robotics and Automation (ICRA 1989), Scottsdale, AZ, USA, pp. 695-700, 1989.
- [9] F. Mondada, G. C. Pettinaro, A. Guignard, I. W. Kwee, D. Floreano, J.-L. Deneubourg, S. Nolfi, L. M. Gambardella, and M. Dorigo, “Swarm-Bot: A New Distributed Robotic Concept,” Autonomous Robots, Vol.17, No.2, pp. 193-221, 2016.
- [10] J. Neubert and H. Lipson, “Soldercubes: a self-soldering self-reconfiguring modular robot system,” Autonomous Robots, Vol.40, No.1, pp. 139-158, 2016.
- [11] C. Parrott, T. Dodd, and R. Groß, “HiGen: A high-speed genderless mechanical connection mechanism with single-sided disconnect for self-reconfigurable modular robots,” Proc. of the 2014 IEEE/RSJ Int. Conf. on Intelligent Robots and Systems (IROS 2014), Chicago, IL, USA, pp. 3926-3932, 2014.
- [12] A. M. Mehta and D. Rus, “An End-to-End System for Designing Mechanical Structures for Print-and-fold Robots,” Proc. of the 2014 IEEE Int. Conf. on Robotics and Automation (ICRA 2014), Hong Kong, China, pp. 1460-1465, 2014.
- [13] S.-K. Yun and D. Rus, “Optimal self assembly of modular manipulators with active and passive modules,” Autonomous Robots, Vol.32, No.2, pp. 183-207, 2011.
- [14] W. Lee, M. Hirai, and S. Hirose, “Gunryu III: reconfigurable magnetic wall-climbing robot for decommissioning of nuclear reactor,” Advanced Robotics, Vol.27, No.14, pp. 1099-1111, 2013.
- [15] S. Murata, E. Yoshida, H. Kurokawa, K. Tomita, and S. Kokaji, “Self-Repairing Mechanical Systems,” Autonomous Robots, Vol.10, No.1, pp. 7-21, 2001.
- [16] K. Stoy, D. Brandt, and D. J. Christensen, “Self-Reconfigurable Robots: An Introduction,” The MIT Press, 2010.
- [17] K. Obara, S. Kakudate, T. Yagi, M. Norio, and K. Shibanuma, “Continuous Running Test of Radiation Resistance Motor Driving Equipment under High Gamma Ray Irradiation,” JAEA-Technology 2006-023, 2006 (in Japanese).
- [18] H. Qiao, B. S. Dalay, and R. M. Parkin, “Robotic Peg-Hole Insertion Operations using a Six-Component Force Sensor,” Proc. of the Institution of Mechanical Engineers, Part C: J. of Mechanical Engineering Science, Vol.207, No.5, pp. 289-306, 1993.
- [19] F. C. Abu-Dakka, B. Nemec, J. A. Jørgensen, T. R. Savarimuthu, N. Krüger, and A. Ude, “Adaptation of manipulation skills in physical contact with the environment to reference force profiles,” Autonomous Robots, Vol.39, No.2, pp. 199-217, 2015.
- [20] L. Righetti, M. Kalakrishnan, P. Pastor, J. Binney, J. Kelly, R. C. Voorhies, G. S. Sukhatme, and S. Schaal, “An autonomous manipulation system based on force control and optimization,” Autonomous Robots, Vol.36, No.1, pp. 11-30, 2014.
- [21] C. Claeys and E. Simoen, “Radiation Effects in Advanced Semiconductor Materials and Devices,” Springer-Verlag, 2002.
- [22] D. E. Whitney, “Quasi-Static Assembly of Compliantly Supported Rigid Parts,” ASME J. of Dynamic Systems, Measurement, and Control, Vol.104, No.1, pp. 65-77, 1982.
- [23] N. Kinoshita and T. Arai, “The Analysis of Insertion Process by the Elastic Assembly Machine,” J. of the Japan Society of Precision Engineering, Vol.44, No.3, pp. 346-351, 1978 (in Japanese).
- [24] T. Yamaguchi, M. Higuchi, A. Yano, and K. Fujita, “Peg-in-Hole by Using a Fixture with Passive Compliance Function (1st Report, Construction of Peg-in-Hole Task Model by Using a Fixture with Passive RCC Function under Quasi-Static Analysis),” Trans. of the Japan Society of Mechanical Engineers, Vol.68, No.674, pp. 275-281, 2002 (in Japanese).
This article is published under a Creative Commons Attribution-NoDerivatives 4.0 Internationa License.