Paper:
Effect for a Paddy Weeding Robot in Wet Rice Culture
Hitoshi Sori*, Hiroyuki Inoue*, Hiroyuki Hatta**, and Yasuhiro Ando**
*National Institute of Technology, Tsuyama College
624-1 Numa, Tsuyama-city, Okayama 708-8509, Japan
**IKOMA Robotech Corporation
634-28 Toshima, Tsuyama-city, Okayama 708-0016, Japan
In recent years, wet rice farming that does not use chemical herbicides has come in demand owing to the diversified consumer needs, preference for pesticide-free produce, and need to reduce the environmental load. In this paper, we propose a “weeding robot” that can navigate autonomously while weeding a paddy field. The weeding robot removes the weeds by churning up the soil and inhibits the growth of the weeds by blocking-off sunlight. It has two wheels, whose rotational speed is controlled by pulse width modulation (PWM) signals. Moreover, it has capacitive touch sensors to detect the rice plants and an azimuth sensor used when turning. To demonstrate its effect in wet rice culture, we conduct a navigation experiment using the proposed weeding robot in two types of paddy field: conventional and sparse planting. The experiment results demonstrate that the proposed weeding robot is effective in its herbicidal effect, promoting the rice seedling growth and increasing the crop yield.
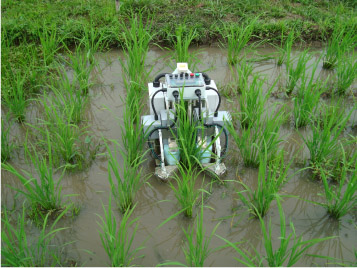
Movement of the weeding robot
- [1] J. Sato, “Farming Robots,” J. Robot. Mechatron., Vol.9, No.4, pp. 287-292, 1997.
- [2] K. Imou, “Automatization and Robotization of Agricultural Machinery,” J. of the Robotics Society of Japan, Vol.35, No.5, pp. 376-378, 2017.
- [3] W. Nakagawa, “Robots of Agricultural Implement and Machinery. Current State, Problem, and View in the Future,” J. of the Robotics Society of Japan, Vol.35, No.5, pp. 387-389, 2017.
- [4] N. Noguchi, J. F. Reid, Q. Zhang, L.Tian, and A. C. Hansen, “Vision Intelligence for Mobile Agro-Robotic System,” J. Robot. Mechatron., Vol.11, No.3, pp. 193-199, 1999.
- [5] K. Tamaki, “The research project of agricultural robot for land utilization mainly in paddy fields,” Farming mechanization, Vol.3104, pp. 14-17, 2010 (in Japanese).
- [6] T. Mitsui, T. Kobayashi, T. Kagiya, A. Inaba, and S. Ooba, “Verification of a Weeding Robot “AIGAMO-ROBOT” for Paddy Fields,” J. Robot. Mechatron., Vol.20, No.2, pp. 228-232, 2008.
- [7] Y. Nishida, “A Study for an Image Processing System that Judges a Line of Rice Plants on the Weeding Robot “TAMBA”,” Memoirs of Fukui University of Technology, Vol.46, pp. 18-23, 2016 (in Japanese).
- [8] K. Yasuda, F. Takakai, Y. Kaneta, and A. Imai, “Running Freely on the Rice Plan Hills,” Farming mechanization, Vol.3180, pp. 16-20, 2016 (in Japanese).
- [9] H. Hatta, Y. Ando, K. Iizuka, H. Inoue, and H. Sori, “Development of Weeding Robot for Paddy Field,” Mechanical Engineering Congress, S151013, 2013 (in Japanese).
- [10] S, Akihira, H. Inoue, H. Sori, H. Hatta, and Y. Ando, “Weeding Robot Control for Rice Plant Line Following,” Proc. of the 2015 JSME Conf. on Robotics and Mechatronics, 2P1-B09, 2015 (in Japanese).
- [11] K, Namba, H. Inoue, H. Sori, H. Hatta, and Y. Ando, “Rice Plant Line Detection Using Capacitive Touch Sensor for Weeding Robot,” Proc. of the 2015 JSME Conf. on Robotics and Mechatronics, 2P1-B10, 2015 (in Japanese).
This article is published under a Creative Commons Attribution-NoDerivatives 4.0 Internationa License.