Paper:
Analysis and Optimization for Balancing Mechanism of High-Speed & Heavy-Load Manipulators
Yongfei Xiao, Shuhui Bi, Xuelin Wang,
Xiangdong Li, and Xinjian Fan
Shandong Provincial Key Laboratory of Robot and Manufacturing Automation Technology, Institute of Automation, Shandong Academy of Science, No.19, Keyuan Road, Jinan, Shandong 250014, China
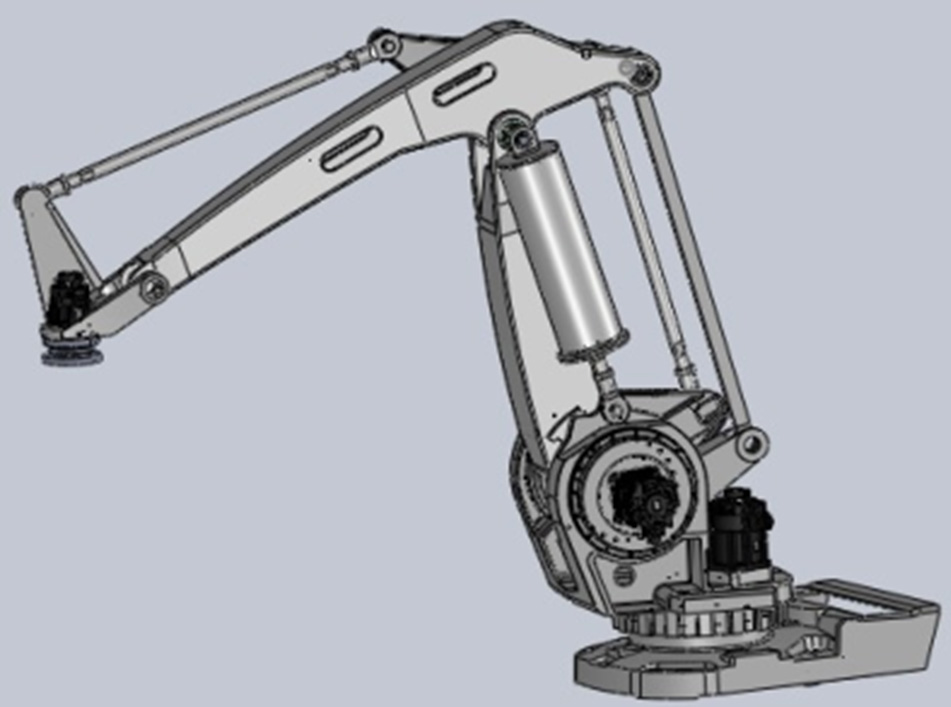
- [1] Y.-B. Lu, C.-H. Zhao, L. Zhang, and J.-L. Liu, “The analysis and optimization for the balancing cylinder of industrial robot,” Develop & Innovation of Machinery & Electrical Products. China, Vol.24, pp. 19-20, 2011.
- [2] W. Yangnian and G. Clement, “Design of reactionless 3-DOF and 6-DOF parallel manipulators using parallelepiped mechanisms,” IEEE Trans. of Robotics, Vol.21, pp. 821-833, 2005.
- [3] H. Shen, “Optimization on the lower arm equilibrator of an arcwelding robot,” Modular Machine Tool & Automatic Manufacturing Technique, Vol.9, pp. 79-80, 2004.
- [4] X. Tang, W. Li, T. Zhang, and G. Tuo, “Effect of parallel four-bar mechanism on spotwelding robot,” J. of China Agricultural University, Vol.4, pp. 37-40, 2004.
- [5] J. L. Herder, “Design of spring force compensation systems,” Mechanism Mach. Theory, Vol.33, No.1, pp. 151-161, 1998.
- [6] A. Lecours and C. Gosselin, “Reactionless two-degree-of-freedom planar parallel mechanism with variable payload,” ASME J. Mechanisms Robot., Vol.2, No.4, pp. 041010-1–041010-7, 2010.
- [7] M. Arsenault and C. M. Gosselin, “Static balancing of tensegrity mechanisms,” ASME J. Mech. Design, Vol.129, No.3, pp. 295-300, 2007.
- [8] I. Simionescu and L. Ciupitu, “The static balancing of the industrial robot arms – Part II: Continuous balancing,” Mech. Mach. Theory, Vol.35, No.9, pp. 1299-1311, 2000.
- [9] C. M. Gosselin, F. Vollmer, G. Cote, and W. Yangnian, “Synthesis and design of reactionless three-degree-of-freedom parallel mechanisms,” IEEE Trans. of Robtics and Automation, Vol.20, pp. 191-199, 2004.
- [10] W. K. Chung and K. S. Cho, “On the dynamic characteristics of a balance PUMA-760 robot,” IEEE Trans. of Industrial Electronics, Vol.35, pp. 222-230, 1988.
- [11] Z.Wenhong, T. Lamarche, and P. Barnard, “Modular Robot Manipulators with Preloadable Modules,” ICMA 2007, Harbin, pp. 7-12, 2007.
- [12] L. Yanbo and K. E. Bekris, “Balancing state-space coverage in planning with dynamics,” 2010 IEEE Int. Conf. on Robotics and Automation, Alaska, pp. 3246-3253, 2010.
- [13] B. Liping, “Simulation analysis of robot dynamics based on ADAMS,” Mechanical and Electrical Engineering Magazine, Vol.24, pp. 75-77, 2007.
This article is published under a Creative Commons Attribution-NoDerivatives 4.0 Internationa License.