Research Paper:
User Action Recognition Using a Fabric Pressure Distribution Sensor in an Electric Wheelchair for Soil Cultivation
Takahiro Matsuishi, Yasutake Takahashi
, and Satoki Tsuichihara

Graduate School of Engineering, University of Fukui
3-9-1 Bunkyo, Fukui, Fukui, , Japan
Advancements in robotics technology and information and communication technology have significantly affected agriculture, especially systems that aid workers. Soil cultivation often requires prolonged bending, which results in physical strain. A commercially available work wheelchair reduces back strain, but lacks power assistance and relies on leg movements. In a previous study, we developed an electric wheelchair with a fabric pressure-distribution sensor on the seat. This sensor, combined with a fuzzy controller, aids movement by measuring the center of pressure fluctuations and reducing leg strain. However, it does not recognize user’s actions, such as standing or sitting, and requires the wheelchair to stop. This study introduced a user-action recognition system using a wheelchair seat pressure sensor. This system accurately recognizes user actions through deep learning time-series data. We evaluated data augmentation and multi-user data to enhance the performance. The results show improved prediction accuracy for action recognition in the test scenarios.
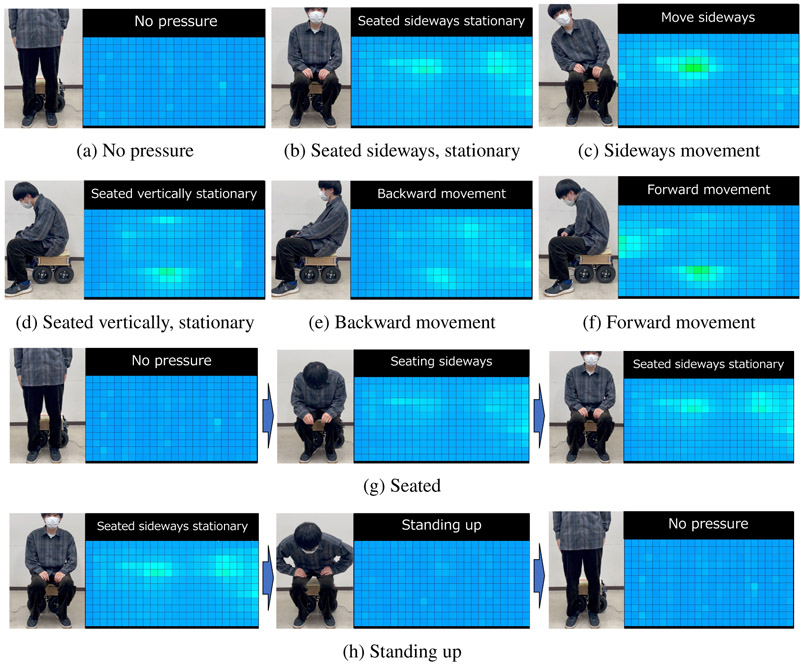
Action recognition for an electric wheelchair
- [1] M. Hachiya, “Overview of smart agricultural production technologies in Japan,” The 60th Japan Joint Automatic Control Conf., pp. 40-41, 2017 (in Japanese).
- [2] Ministry of Agriculture, Forestry and Fisheries, “Summary of results of the 2020 Census of Agriculture and Forestry (fixed values) (as of February 1, 2020),” Technical Report, 2021 (in Japanese). https://www.maff.go.jp/j/tokei/kekka_gaiyou/noucen/2020/index.html [Accessed November 4, 2022]
- [3] S. Hayashi et al., “Development of circulating-type movable bench system for strawberry cultivation,” Japan Agricultural Research Quarterly: JARQ, Vol.45, No.3, pp. 285-293, 2011. https://doi.org/10.6090/jarq.45.285
- [4] T. Tsuchiya et al., “Development of automatic harvester for weak vegetables and field tests,” Proc. of the 2014 JSME Conf. on Robotics and Mechatronics, Article No.1P2-W07, 2014 (in Japanese). https://doi.org/10.1299/jsmermd.2014._1P2-W07_1
- [5] N. S. Naik, V. V. Shete, and S. R. Danve, “Precision agriculture robot for seeding function,” 2016 Int. Conf. on Inventive Computation Technologies, 2016. https://doi.org/10.1109/INVENTIVE.2016.7824880
- [6] S. Parande, P. Ghodke, and N. Inamdar, “Agriculture Robot,” Int. J. of Advance Scientific Research and Engineering Trends, Vol.6, No.1, pp. 8-10, 2021.
- [7] H. Kobayashi, “Muscle suit,” J. of the Robotics Society of Japan, Vol.38, No.2, pp. 143-146, 2020 (in Japanese). https://doi.org/10.7210/jrsj.38.143
- [8] A. Nambu and M. Nakatsuka, “Application of assist suit to vegetable and fruit cultivation work,” J. of the Japanese Society of Agricultural Machinery and Food Engineers, Vol.80, No.4, pp. 204-209, 2018, (in Japanese). https://doi.org/10.11357/jsamfe.80.4_204
- [9] H. Fujimoto and K. Kishimoto, “Development report on the ‘HIMICO’ power assist suit for walking support,” IATSS Review, Vol.47, No.1, pp. 40-47, 2022 (in Japanese). https://doi.org/10.24572/iatssreview.47.1_40
- [10] E. Yagi, “Toward the realization of power-assistive suits,” 21st century WAKAYAMA, Vol.91, pp. 5-8, 2019 (in Japanese).
- [11] T. Nishi, “Current status and challenges of manipulation technology in smart farming,” J. of the Robotics Society of Japan, Vol.37, No.6, pp. 499-502, 2019 (in Japanese). https://doi.org/10.7210/jrsj.37.499
- [12] M. Nakano and K. Kishimoto, “Human movement tracking method of powered wear which is used in competition management,” Panasonic Technical J., Vol.65, No.2, pp. 50-52, 2019 (in Japanese).
- [13] T. Taketomi and Y. Sankai, “Walking assistance for cerebral palsy with robot suit HAL,” Trans. of Japanese Society for Medical and Biological Engineering, Vol.50, No.1, pp. 105-110, 2012 (in Japanese). https://doi.org/10.11239/jsmbe.50.105
- [14] T. Matsuishi, Y. Takahashi, and S. Tsuichihara, “Fuzzy control of electric wheelchair with intuitive user interface for soil cultivation,” J. of Japan Society for Fuzzy Theory and Intelligent Informatics, Vol.33, No.4, pp. 787-797, 2021. https://doi.org/10.3156/jsoft.33.4_787
- [15] S. Sundaram et al., “Learning the signatures of the human grasp using a scalable tactile glove,” Nature, Vol.569, No.7758, pp. 698-702, 2019. https://doi.org/10.1038/s41586-019-1234-z
- [16] J. Hori, H. Ohara, and S. Inayoshi, “Control of speed and direction of electric wheelchair using seat pressure mapping,” Biocybernetics and Biomedical Engineering, Vol.38, No.3, pp. 624-633, 2018. https://doi.org/10.1016/j.bbe.2018.04.007
- [17] Y. Enokibori and K. Mase, “A study of data augmentation to build high performance DNN for in-bed posture classification,” IPSJ SIG Technical Report, Vol.2017-ASD-9, No.11, 2017 (in Japanese).
- [18] W. Xu, M.-C. Huang, N. Amini, L. He, and M. Sarrafzadeh, “eCushion: A textile pressure sensor array design and calibration for sitting posture analysis,” IEEE Sensors J., Vol.13, No.10, pp. 3926-3934, 2013. https://doi.org/10.1109/JSEN.2013.2259589
- [19] J. Cheng, M. Sundholm, B. Zhou, M. Hirsch, and P. Lukowicz, “Smart-surface: Large scale textile pressure sensors arrays for activity recognition,” Pervasive and Mobile Computing, Vol.30, pp. 97-112, 2016. https://doi.org/10.1016/j.pmcj.2016.01.007
- [20] J. Cong, J. Jing, C. Chen, and Z. Dai, “Development of a PVDF sensor array for measurement of the dynamic pressure field of the blade tip in an axial flow compressor,” Sensors, Vol.19, No.6, Article No.1404, 2019. https://doi.org/10.3390/s19061404
- [21] K. Matsuno, Y. Takahashi, and S. Tsuichihara, “Development of a breathable and flexible pressure distribution sensor using conductive cloth,” Proc. of Symp. of Hokushinetsu Branch of Japan Society for Fuzzy Theory and Intelligent Informatics 2021, pp. 12-13, 2021 (in Japanese).
- [22] X. Glorot, A. Bordes, and Y. Bengio, “Deep sparse rectifier neural networks,” Proc. of the 14th Int. Conf. on Artificial Intelligence and Statistics, pp. 315-323, 2011.
- [23] N. Srivastava, G. Hinton, A. Krizhevsky, I. Sutskever, and R. Salakhutdinov, “Dropout: A simple way to prevent neural networks from overfitting,” J. of Machine Learning Research, Vol.15, No.56, pp. 1929-1958, 2014.
This article is published under a Creative Commons Attribution-NoDerivatives 4.0 Internationa License.