Paper:
Monitoring and Analysis of Auto Body Precision Based on Big Data
Yixin Yang*,**,, Jianjun Gao**, and Konghui Guo*
*College of Mechanical and Transportation Engineering, Hunan University
Lushan Road, Yuelu District, Changsha, Hunan 410082, China
**BAIC Motor Co., Ltd. Zhuzhou Branch
Liyu Industrial Park, Tianyuan District, Zhuzhou, Hunan 412007, China
Corresponding author
In this paper, a Hadoop-based big data system for auto body precision is established. The system unifies the elements that affect auto body precision into a big data platform, which is more efficient than traditional management methods. Using big data analysis, we devised algorithms to improve the efficiency and accuracy of body precision monitoring. Furthermore, we developed techniques to analyze complex dimension deviation problems using a correlation analysis method, principal component analysis (PCA), and improved PCA method. We further established failure modes and devised monitoring and diagnosis models based on time series analysis.
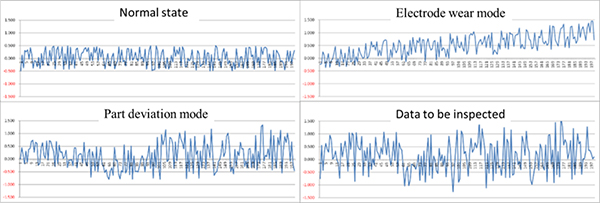
Auto body precision analysis based on big data
- [1] D.-H. Tang, “From American Automobile 2mm Program to China Automobile Manufacturing Quality Program,” Development & Innovation of Machinery & Electrical Products, Vol.2006, No.1, pp. 26-28, 2006 (in Chinese).
- [2] Z. Lin, “Quality control technology of automobile body manufacturing,” China Machine Press, 2005.
- [3] H. Xie, C. Jiang, and Z. Zhang, “Interval description of dimensional tolerance and uncertainty optimization,” The 3rd Conf. on Computational Mechanics (CCM 2014), 2014.
- [4] D. Yang, “Research on real-time monitoring and fault diagnosis system and its key technologies in BIW welding process,” Master Thesis, Hefei Polytechnic University, 2014.
- [5] X. Chen and J. Huang, “Application of RPS in Precision Design Body,” Automotive Technology, Vol.2006, No.8, pp. 18-21+42, 2006 (in Chinese).
- [6] Y. Tao, H. Shi, B. Song, and S. Tan, “A Novel Dynamic Weight Principal Component Analysis Method and Hierarchical Monitoring Strategy for Process Fault Detection and Diagnosis,” IEEE Trans. on Industrial Electronics, Vol.67, No.9, pp. 7994-8004, 2020.
- [7] T. Sibillano, A. Ancona, V. Berardi, and P. M. Lugarà, “Correlation analysis in laser welding plasma,” Optics Communications, Vol.251, Issues 1-3, pp. 139-148, 2005.
- [8] S. Yi, Z. He, X.-Y. Jing, Y. Li, Y.-M. Cheung, and F. Nie, “Adaptive Weighted Sparse Principal Component Analysis for Robust Unsupervised Feature Selection,” IEEE Trans. on Neural Networks and Learning Systems, Vol.31, No.6, pp. 2153-2163, 2020.
- [9] H. Caussinus and A. Ruiz-Gazen, “Principal Component Analysis, Generalized,” S. Kotz, C. B. Read, N. Balakrishnan, B. Vidakovic, and N. L. Johnson (Eds.), “Encyclopedia of Statistical Sciences,” Vol.10, John Wiley & Sons, Inc., 2005.
- [10] Z. Sun, J. Zhao, and L. Li, “Comparison between PCA and KPCA methods in comprehensive evaluation of robotic kinematic dexterity,” High Technology Letters, Vol.20, No.2, pp. 154-160, 2014.
- [11] S. Yang, “Research on BIW size deviation based on wavelet modulus maximum and principal component analysis,” Master Thesis, Chongqing Jiaotong University, 2014.
- [12] Y. Yang, S. Shen, Y. Liu, Z. Li, and S. Jin, “Diagnosis of body online detecting dimensional deviation based on pattern recognition,” Machinery Design & Manufacture, Vol.2012, No.1, pp. 188-190, 2012 (in Chinese).
- [13] K. Geng, J. He, K. Wang, and Y. Chen, “Gear Fault Diagnosis Based on Pattern Recognition of Acoustic Emission Signals,” Machine Tool & Hydraulics, Vol.47, No.16, pp. 192-196+208, 2019 (in Chinese).
This article is published under a Creative Commons Attribution-NoDerivatives 4.0 Internationa License.