Research Paper:
Remaining Useful Life Prediction for Tools Based on Monitoring Data and Stochastic Degradation Model
Baokang Zhang*
, Ning Li**
, Jiahui Huang**, Takahiro Arakawa**,, Kentaro Ishii**, and Ryuichi Yashima**
*College of Information Engineering, Zhejiang University of Technology
No.18 Chaowang Road, Hangzhou, Zhejiang 310014, China
**Sustainable Engineering, Tokyo University of Technology
1404-1 Katakuramachi, Hachioji, Tokyo 192-0982, Japan
Corresponding author
This study proposes a graph convolutional network (GCN)-based data–model interactive remaining useful life (RUL) prediction method for tools. First, a composite health indicator (CHI) is built by aggregating information from neighboring nodes through the GCN. Second, a stochastic degradation model is established to capture the time-varying evolutionary trend. Specifically, the drift coefficient is treated as a random variable to represent its variability among different individuals of the same type of tool, and the model parameters are estimated using intermediate evolutionary process data. Then, a data–model interactive mechanism is proposed by forming closed-loop optimization between the CHI construction and the stochastic degradation model to enhance the RUL prediction accuracy. Finally, experiments are conducted on the PHM2010 dataset to verify the effectiveness and superiority of the proposed method.
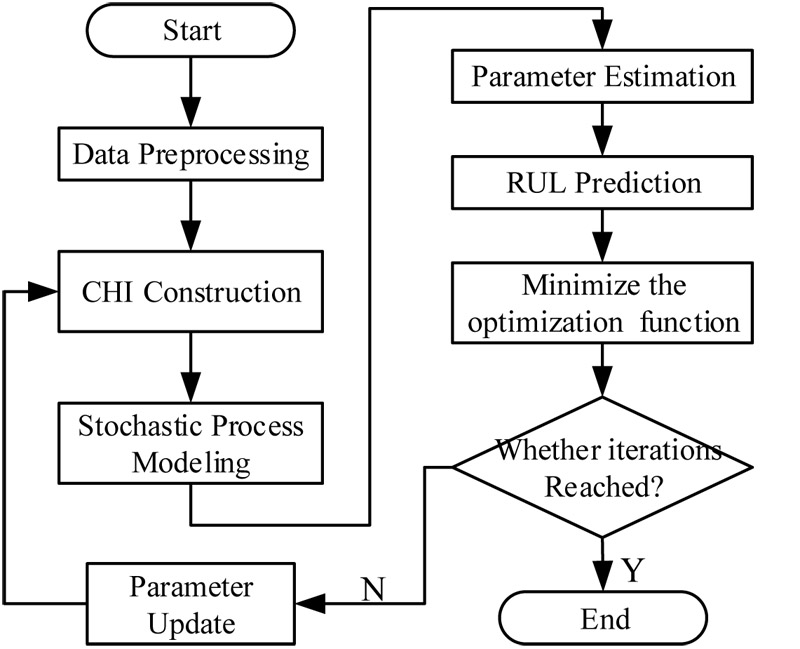
RUL prediction based on data-model interactive
- [1] Q. Wu, S. J. Dong, W.-A Zhang et al., “Online modeling of the CNC engraving system with dead-zone input nonlinearity,” IEEE Trans. on Industrial Electronics, Vol.69, No.1, pp. 774-782, 2022. https://doi.org/10.1109/TIE.2020.3044819
- [2] Z. Meng, B. Xu, L. X. Cao et al., “A novel convolution network based on temporal attention fusion mechanism for remaining useful life prediction of rolling bearings,” IEEE Sensors J., Vol.23, No.4, pp. 3990-3999, 2023.
- [3] Y. Zhang, L. Fang, Z. Qi, and H. Deng, “A Review of Remaining Useful Life Prediction Approaches for Mechanical Equipment,” IEEE Sensors J., Vol.23, No.24, pp. 29991-30006, 2023. https://doi.org/10.1109/JSEN.2023.3326487
- [4] Z. Zhou, B. Yao, Y. Tan et al., “Analysis and Thoughts on Application of Optical Fibre Sensing in Manufacturing,” J. of Mechanical Engineering, Vol.58, No.8, pp. 3-26, 2022. https://doi.org/10.3901/JME.2022.08.003
- [5] Y. G. Lei, “Intelligent Fault Diagnosis and Remaining Useful Life Prediction of Rotating Machinery,” Butterworth-Heinemann, 2016.
- [6] J. Liang, H. Liu, and N.-C. Xiao, “A hybrid approach based on deep neural network and double exponential model for remaining useful life prediction,” Expert Systems with Applications, Vol.249, Article No.123563, 2024. https://doi.org/10.1016/j.eswa.2024.123563
- [7] G. Yu, W. Xia, Z. Song et al., “Wear-life analysis of deep groove ball bearings based on Archard wear theory,” J. of Mechanical Science and Technology, Vol.32, pp. 3329-3336, 2018. https://doi.org/10.1007/s12206-018-0635-5
- [8] C. H. Oppenheimer and K. A. Loparo, “Physically based diagnosis and prognosis of cracked rotor shafts,” Component and Systems Diagnostics, Prognostics, and Health Management II. SPIE, Vol.4733, pp. 122-132, 2002. https://doi.org/10.1117/12.475502
- [9] Y. Lei, N. Li, S. Gontarz et al., “A model-based method for remaining useful life prediction of machinery,” IEEE Trans. on Reliability, Vol.65, No.3, pp. 1314-1326, 2016. https://doi.org/10.1109/TR.2016.2570568
- [10] X. Liu, L. Liu, D. Liu, L. Wang, Q. Guo, and X. Peng, “A Hybrid Method of Remaining Useful Life Prediction for Aircraft Auxiliary Power Unit,’’ IEEE Sensors J., Vol.20, No.14, pp. 7848-7858, 2020. https://doi.org/10.1109/JSEN.2020.2979797
- [11] X. Wang, P. Ye, S. Liu, Y. Zhu, Y. Deng, Y. Yuan, and H. Ni, “Research Progress of Battery Life Prediction Methods Based on Physical Model,” Energies, Vol.16, No.9, Article No.3858, 2023. https://doi.org/10.3390/en16093858
- [12] D. Huang, W.-A. Zhang et al., “Wavelet packet decomposition-based multiscale CNN for fault diagnosis of wind turbine gearbox,” IEEE Trans. on Cybernetics, Vol.53, No.1, pp. 443-453, 2023. https://doi.org/10.1109/TCYB.2021.3123667
- [13] Z. Du, L. Zuo, J. Li et al., “Data-driven estimation of remaining useful lifetime and state of charge for lithium-ion battery,” IEEE Trans. on Transportation Electrification, Vol.8, No.1, pp. 356-367, 2021. https://doi.org/10.1109/TTE.2021.3109636
- [14] H. Guo, B. C. Ren, X. G. Yan et al., “Research on dynamic prediction of tool life based on deep convolutional neural network,” Control and Decision, Vol.37, No.08, pp. 2119-2126, 2022. http://doi.org/10.13195/j.kzyjc.2020.1530
- [15] T. H. Shen, K. Ding, J. Li et al., “A graph-structured joint timing data-driven method for equipment remaining service life prediction,” J. of Mechanical Engineering, Vol.59, No.12, pp. 183-194, 2023.
- [16] M. Kiamari, B. Krishnamachari, and B. Krishnamachari, “GKAN: Graph Kolmogorov-Arnold Networks,” arXiv:2406.06470, 2024. https://doi.org/10.48550/arXiv.2406.06470
- [17] H. Li, Z. Zhang, T. Li et al., “A review on physics-informed data-driven remaining useful life prediction: Challenges and opportunities,” Mechanical Systems and Signal Processing, Vol.209, Article No.111120, 2024. https://doi.org/10.1016/j.ymssp.2024.111120
- [18] Y. G. Lei and B. Yang, “Big data-driven intelligent operation and maintenance theory and application of mechanical equipment,” Electronic Industry Press, 2022.
- [19] K. X. Peng, Y. T. Pi, R. H. Jiao, and P. Tang, “Health index construction and remaining life prediction of aero-engines,” Control Theory and Applications, Vol.37, No.4, pp. 713-720, 2020.
- [20] C.-H. Hu, H. Pei, X.-S. Si et al., “A prognostic model based on DBN and diffusion process for degrading bearing,” IEEE Trans. on Industrial Electronics, Vol.67, No.10, pp. 8767-8777, 2019. https://doi.org/10.1109/TIE.2019.2947839
- [21] T. M. Li, X. S. Si, X. Liu et al., “Remaining life prediction technique for stochastic degraded equipment under big data with number-mode linkage,” J. of Automation, Vol.48, No.09, pp. 2119-2141, 2022.
- [22] Q. Zhang, J. Chang, G. Meng et al., “Learning graph structure via graph convolutional networks,” Pattern Recognition, Vol.95, pp. 308-318, 2019. https://doi.org/10.1016/j.patcog.2019.06.012
- [23] Z. Zhang, X. Si, C. Hu, and Y. Lei, “Degradation data analysis and remaining useful life estimation: A review on Wiener-process-based methods,” European J. of Operational Research, Vol.271, No.3, pp. 775-796, 2018. https://doi.org/10.1016/j.ejor.2018.02.033
- [24] W. Li and H. Li, “FPGA Implementation Method of Arbitrary Base Logarithm Transformation Based on System Generator,” Shipboard Electronic Countermeasures, Vol.45, No.06, pp. 85-89, 2022 (in Chinese).
- [25] C. Li, “Research on Electromagnetic Transient Simulation Method Based on Multi-Frequency Band Time Scale Transformation,” Doctoral dissertation, North China Electric Power University, 2020.
- [26] T. Li, H. Pei, Z. Pang, X. Si, and J. Zheng, “A sequential Bayesian updated Wiener process model for remaining useful life prediction,” IEEE Access, Vol.8, pp. 5471-5480, 2019. https://doi.org/10.1109/ACCESS.2019.2962502
- [27] Y. Zhu, “Research on Monitoring Technology of Cutter Wear State for Wheel Loader Based on Machine Learning,” Doctoral dissertation, Guizhou University, 2022.
This article is published under a Creative Commons Attribution-NoDerivatives 4.0 Internationa License.