Review:
Research and Development on Robotic Technologies for Infrastructure Maintenance
Keiji Nagatani* and Yozo Fujino**
*The University of Tokyo
7-3-1 Hongo, Bunkyo-ku, Tokyo 113-8656, Japan
**Yokohama National University
79-5 Tokiwadai, Hodogaya, Yokohama, Kanagawa 240-8501, Japan
Construction of infrastructures, such as bridges and tunnels, has increased significantly in Japan in the past 50 years. Most of the civil infrastructure is now aging rapidly. Basic infrastructure maintenance and management require proper repairing and reinforcement, for which periodic inspections are indispensable. Inspection of civil infrastructure, however, requires a large amount of workforce for traffic regulation and accessing difficult-to-reach locations. Occupational safety is also an important issue that cannot be ignored. Furthermore, technologies related to emergency responses after the occurrence of natural disasters are important, especially with the increasing number of natural disasters recently. Executing a safe and quick disaster response action is very challenging. To meet the above problems, “Infrastructure Maintenance, Renovation and Management” was established in the Cross-ministerial Strategic Innovation Promotion Program (SIP). Research and development programs for infrastructure management systems using new technologies had been conducted since 2014. In this paper, the research and development programs related to robotic technologies are described. Specifically, robotic technologies for bridge inspection, tunnel inspection, and disaster responses are introduced. In addition, the scheme of the SIP regional bases that facilitates the availability of the developed technologies to local governments is also introduced.
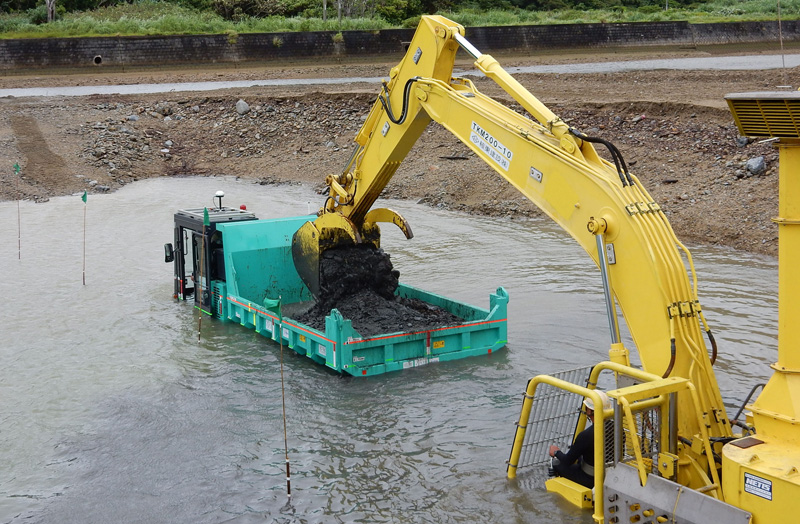
Heavy-duty amphibious crawler dumper
- [1] Y. Hada, M. Nakao, M. Yamada, H. Kobayashi, N. Sawasaki, K. Yokoji, and A. Yamashita, “Development of a Bridge Inspection Support System Using Two-Wheeled Multicopter and 3D Modeling Technology,” J. Disaster Res., Vol.12, No.3, pp. 593-606, 2017.
- [2] F. Tanaka, M. Tsuchida, and M. Onosato, “Associating 2D Sketch Information with 3D CAD Models for VR/AR Viewing During Bridge Maintenance Process,” Int. J. Automation Technol., Vol.13, No.4, pp. 482-489, 2019.
- [3] C. J. O. Salaan, Y. Okada, S. Mizutani, T. Ishii, K. Koura, K. Ohno, and S. Tadokoro, “Close visual bridge inspection using a UAV with a passive rotating spherical shell,” J. of Field Robotics, Vol.35, No.6, pp. 850-867, 2018.
- [4] Y. Okada, T. Ishii, K. Ohno, and S. Tadokoro, “Real-time restoration of aerial inspection images by recognizing and removing passive rotating shell of a UAV,” IEEE/RSJ Int. Conf. on Intelligent Robots and Systems (IROS), pp. 5006-5012, 2016.
- [5] K. Nonami, “State of the art and issue of drone technology and business frontier,” Johokanri, Vol.59, No.11, pp. 755-763, 2017 (in Japanese).
- [6] S. Nakamura, Y. Takahashi, D. Inoue, and T. Ueno, “The variable guide frame vehicle for tunnel inspection,” Proc. of 34th Int. Symp. on Automation and Robotics in Construction, pp. 671-674, 2017.
- [7] D. Inoue, T. Ueno, and S. Nakamura, “Experiment on Mobile Light-section Device for Automatic Crack Inspection of Actual-size Tunnel Lining Concrete,” Proc. of 34th Int. Symp. on Automation and Robotics in Construction, pp. 671-674, 2017.
- [8] J. Y. L. Kasahara, H. Fujii, A. Yamashita, and H. Asama, “Fuzzy Clustering of Spatially Relevant Acoustic Data for Defect Detection,” IEEE Robotics and Automation Letters, Vol.3, No.3, pp. 2616-2623. 2018.
- [9] M. Moteki, K. Fujino, T. Ohtsuki, and T. Hashimoto, “Research on visual point of operator in remote control of construction machinery,” 28th Int. Symp. on Automation and Robotics in Construction, pp. 532-537, 2011.
- [10] K. Chayama, A. Fujioka, K. Kawashima, H. Yamamoto, Y. Nitta, C. Ueki, and H. Asama, “Technology of Unmanned Construction System in Japan,” J. Robot. Mechatron., Vol.26, No.4, pp. 403-417, 2014.
- [11] S. Yuta, “Development of a remotely controlled semi-underwater heavy carrier robot for unmanned construction works,” J. Disaster Res., Vol.12, No.3, pp. 432-445, 2017.
- [12] H. Murakami, S. Suzuki, Y. Miura, M. Watanabe, F. Shibukawa, M. Maeda, R. Oohashi, Y. Kaneshima, H. Ueno, and Y. Hayase, “Development of Prototype machine for the Remotely controlled Shallow water Heavy Carrier Robot,” Proc. of the 2017 JSME Conf. on Robotics and Mechatronics, 1P1-D05, 2017 (in Japanese).
- [13] H. Matsuda, S. Nakamura, K. Yamaguchi, and K. Takahashi, “Regional Implementation Support of SIP Development Technology by “MICHIMORI”,” Concrete J., Vol.56, No.1, pp 88-93, 2018 (in Japanese).
This article is published under a Creative Commons Attribution-NoDerivatives 4.0 Internationa License.