Paper:
Experimental Evaluation of Highly Accurate 3D Measurement Using Stereo Camera and Line Laser
Shunya Nonaka*, Sarthak Pathak**
, and Kazunori Umeda**

*Precision Engineering Course, Graduate School of Science and Engineering, Chuo University
1-13-27 Kasuga, Bunkyo-ku, Tokyo 112-8551, Japan
**Department of Precision Mechanics, Faculty of Science and Engineering, Chuo University
1-13-27 Kasuga, Bunkyo-ku, Tokyo 112-8551, Japan
This paper proposes a method to improve the accuracy of 3D measurement of a stereo camera by marking a measured object using a line laser. Stereo cameras are commonly used for 3D measurement, but the accuracy of 3D measurement is affected by the amount of texture. Therefore, a new measurement system combining a stereo camera and a line laser is developed. The accuracy of 3D measurement with a stereo camera is improved by using a line laser to mark arbitrary points on the measured object and measuring the marked points, regardless of the amount of texture on the measured object. Because the laser is only used to mark points on the measurement target, calibration is not required with the stereo camera. Experimental evaluation showed that our proposed method can obtain millimeters.
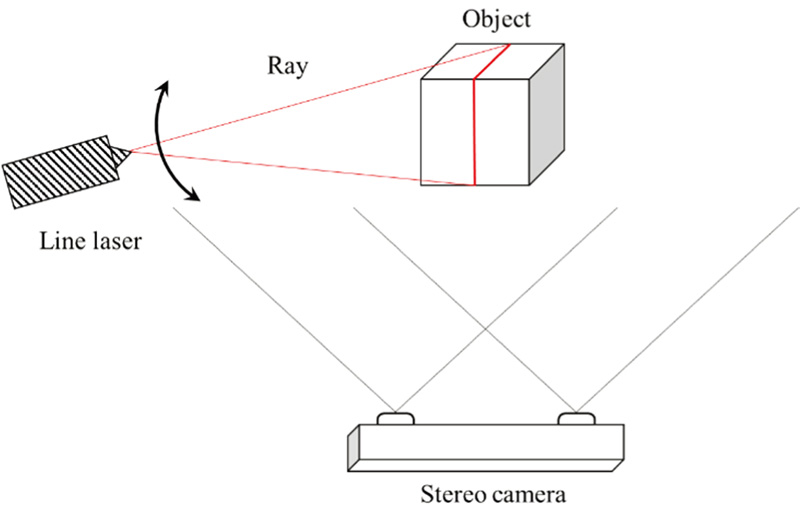
3D measurement by stereo camera and line laser
- [1] E. Heo, M. Kwon, and B. Kim, “Large free form measurement using slit beam,” 2008 Int. Conf. on Control, Automation and Systems, Seoul, South Korea, pp. 1224-1227, 2008. https://doi.org/10.1109/ICCAS.2008.4694335
- [2] S. Ding, X. Zhang, H. Chen, and J. Wang, “Large scale object’s measurement method research based on multi-view reconstruction,” 2017 2nd Int. Conf. on Image, Vision and Computing (ICIVC), Chengdu, pp. 555-558, 2017. https://doi.org/10.1109/ICIVC.2017.7984617
- [3] Z. Liu, J. Huang, S. Bu, J. Han, X. Tang, and X. Li, “Template Deformation-Based 3-D Reconstruction of Full Human Body Scans From Low-Cost Depth Cameras,” IEEE Trans. on Cybernetics, Vol.47, No.3, pp. 695-708, 2017. https://doi.org/10.1109/TCYB.2016.2524406
- [4] S. Gao, C. F. Cheung, and D. Li, “Autostereoscopic Measurement System for Rapid 3D Inspection of Wire Bonding,” 2021 Int. Conf. of Optical Imaging and Measurement (ICOIM), Xi’an, China, pp. 145-148, 2021. https://doi.org/10.1109/ICOIM52180.2021.9524422
- [5] M. Kawata, H. Higuchi, S. Pathak, A. Yamashita, and H. Asama, “Scale Optimization of Structure from Motion for Structured Light-based All-round 3D Measurement,” 2021 IEEE Int. Conf. on Systems, Man, and Cybernetics (SMC), Melbourne, Australia, pp. 442-449, 2021. https://doi.org/10.1109/SMC52423.2021.9658793
- [6] M. Yao and B. Xu, “A Dense Stereovision System for 3D Body Imaging,” IEEE Access, Vol.7, pp. 170907-170918, 2019. https://doi.org/10.1109/ACCESS.2019.2955915
- [7] D. Hong, H. Lee, M. Kim, and H. Cho, “A 3D inspection system for PCB board by fusing moiré technique and stereo vision algorithm,” SICE Annual Conf. 2007, Takamatsu, pp. 2473-2479, 2007. https://doi.org/10.1109/SICE.2007.4421405
- [8] A. Harjoko, R. M. Hujja, and L. Awaludin, “Low-cost 3D surface reconstruction using Stereo camera for small object,” 2017 Int. Conf. on Signals and Systems (ICSigSys), Bali, Indonesia, pp. 285-289, 2017. https://doi.org/10.1109/ICSIGSYS.2017.7967057
- [9] H. Aoki, T. Shiga, A. Suzuki, and K. Takeuchi, “Non-contact Heartbeat Measurement by Hybrid Method of Passive Stereo and Active Stereo,” 2019 IEEE 1st Global Conf. on Life Sciences and Technologies (LifeTech), Osaka, Japan, pp. 115-116, 2019. https://doi.org/10.1109/LifeTech.2019.8883983
- [10] A. Okubo, A. Nishikawa, and F. Miyazaki, “Selective reconstruction of a 3-D scene with an active stereo vision system,” Proc. of Int. Conf. on Robotics and Automation, Albuquerque, NM, USA, Vol.1, pp. 751-758, 1997. https://doi.org/10.1109/ROBOT.1997.620125
- [11] Y. Shirai, “Recognition of polyhedrons with a range finder,” Pattern Recognit., pp. 243-244, 1972. https://doi.org/10.1016/0031-3203(72)90003-9
- [12] H. Sasama, “Evaluation of Slit Light System for Objects with Metallic Reflection and Application to Iron Wheels,” J. Robot. Mechatron., Vol.10, No.5, pp. 455-461, 1998. https://doi.org/10.20965/jrm.1998.p0455
- [13] O. Ozeki, K. Kogure, H. Onouchi, H. Higuchi, and S. Yamamoto, “Visual Inspection System for Welded Beads of Automotive Panel,” J. Robot. Mechatron., Vol.5, No.2, pp. 112-116, 1993. https://doi.org/10.20965/jrm.1993.p0112
- [14] H. Kijima and H. Oku, “Structured Light Field by Two Projectors Placed in Parallel for High-Speed and Precise 3D Feedback,” J. Robot. Mechatron., Vol.34, No.5, pp. 1096-1110, 2022. https://doi.org/10.20965/jrm.2022.p1096
- [15] J. Chen, Q. Gu, T. Aoyama, T. Takaki, and I. Ishii, “Blink-Spot Projection Method for Fast Three-Dimensional Shape Measurement,” J. Robot. Mechatron., Vol.27, No.4, pp. 430-443, 2015. https://doi.org/10.20965/jrm.2015.p0430
- [16] R. Sato, K. Kato, and K. Harada, “Development of the hole position inspection system of pressed car parts by using laser 3-d measurement,” The 19th Korea-Japan Joint Workshop on Frontiers of Computer Vision, Incheon, South Korea, pp. 317-322, 2013. https://doi.org/10.1109/FCV.2013.6485513
- [17] L. Zhao, H. Xu, J. Li, and Q. Cai, “Binocular Stereo Vision Measuring System Based on Structured Light Extraction Algorithm,” 2012 Int. Conf. on Industrial Control and Electronics Engineering, Xi’an, China, pp. 644-647, 2012. https://doi.org/10.1109/ICICEE.2012.174
- [18] M. Yoshimura, Y. Ji, and K. Umeda, “Stereo Measurement of Cross-Sectional Shape of Weld Beads by Marking,” 2020 ICPE 18th Int. Conf. on Precision Engineering, D-4-5, 2020.
- [19] T. Fukuda, Y. Ji, and K. Umeda, “Accurate Range Image Generation Using Sensor Fusion of TOF and Stereo-based Measurement,” Proc. 12th France-Japan and 10th Europe-Asia Congress on Mechatronics, 2018. https://doi.org/10.1109/MECATRONICS.2018.8495739
- [20] R. B. Rusu and S. Cousins, “3D is here: Point Cloud Library (PCL),” IEEE Int. Conf. on Robotics and Automation (ICRA), 2011. https://doi.org/10.1109/ICRA.2011.5980567
- [21] R. Schnabel, R. Wahl, and R. Klein, “Efficient RANSAC for Point-Cloud Shape Detection,” Computer Graphics Forum, Vol.26, No.2, pp. 214-226, 2007. https://doi.org/10.1111/j.1467-8659.2007.01016.x
This article is published under a Creative Commons Attribution-NoDerivatives 4.0 Internationa License.